
10694
.pdf
УДК 502
С.А. Лубкова
Расчет количества выбросов химических веществ, образующихся при компримировании хлора
Всовременных условиях негативные факторы техногенного, природного и террористического характера представляют собой одну из наиболее реальных угроз для обеспечения стабильного социальноэкономического развития страны, повышения качества жизни населения, укрепления национальной безопасности и международного престижа России.
Среди различных видов техногенной опасности для людей и окружающей среды химическая опасность занимает особое место. Современные темпы развития химической промышленности сопровождаются увеличением масштабов производства. Так, сегодня строятся новые заводы, расширяются уже имеющиеся производства, растут требования к количеству производимого продукта. Увеличение производства в области химии влечет за собой возрастание риска возникновения аварий на этих производствах. В связи с этим необходимы как новые исследования в области промышленной безопасности, так обобщение и углубление уже имеющихся разработок и методов.
Взаконодательстве Российской Федерации под промышленной безопасностью понимается состояние защищенности жизненно важных интересов личности и общества от аварий на опасных производственных объектах [1]. Отсюда следует, что наряду с исследованиями по предупреждению и предотвращению аварий необходимы разработки и методики, позволяющие локализовать уже возникшие аварии и минимизировать их последствия. Подобные исследования находят свое применение в разрабатываемых предприятиями декларациях промышленной безопасности, планах ликвидации аварийных ситуаций (ПЛАСах), инструкциях и прочей документации.
Однако большая часть предприятий и оборудования на предприятиях досталась нам от советских времен, а соответственно срок безаварийной его эксплуатации прошел. Кроме того, само оборудование может быть не герметично, и в местах соединения может давать утечки.
Рассмотрим одну из ситуаций, связанных с утечками на производстве, а именно рассчитаем величину утечки вредных веществ, поступающих через неплотности фланцевых соединений. Расчет производим по методике, изложенной в [2].
Величина утечки определяется по формуле:
G lkm 10p5 ,
где G – величина утечки, г/ч; k – коэффициент, учитывающий материал прокладки: для нашего случая k=5 – для резины; l – длина фланцевого соединения, м; m – коэффициент негерметичности, принимаемый, исходя из определяемой продолжительности работы фланцевого соединения: для нашего случая m=0,005 – для трубопроводов и оборудования, подвергаемых повторному испытанию; p – избыточное давление внутренней среды, р=101325Па.
Рассчитаем величину утечек оборудования, находящегося на улице и более подвергающегося внешнему воздействию. Вредное вещество – хлор. Оборудование входит в линию производственного процесса охлаждения, осушки и компримирования хлора, поэтому для каждого трубопровода будем считать собственную величину утечки, а для каждого оборудования суммарную величину утечки от всех прилегающих трубопроводов. Расчеты сведем в табл. 1.
|
|
|
|
Таблица 1 |
|
Расчет количества хлора, поступающего через неплотности |
|||||
|
фланцевых соединений |
|
|
||
|
Номер |
Длина |
Количество |
Суммарное |
|
Название |
хлора с |
|
|||
трубопровода/ |
трубопровода/ |
количество хлора, |
|
||
оборудования |
трубопровода/ |
|
|||
участка |
участка, м |
г/ч |
|
||
|
участка, г/ч |
|
|||
|
|
|
|
|
|
|
1 |
0,8 |
0,02 |
|
|
|
2 |
5,6 |
0.14 |
|
|
Колонна |
3 |
9,2 |
0.23 |
0.535 |
|
сушки хлора |
4 |
2,0 |
0.05 |
|
|
|
|
||||
|
5 |
3,0 |
0.075 |
|
|
|
6 |
0,8 |
0.02 |
|
|
|
1 |
3.0 |
0.075 |
|
|
Холодильник |
2 |
1.6 |
0.04 |
0.245 |
|
|
3 |
5.2 |
0.13 |
|
|
Фильтр |
1 |
2,0 |
0.05 |
0.09 |
|
2 |
1.6 |
0.04 |
|
||
|
|
|
|||
Бак напорный |
1 |
22.8 |
0.57 |
0.62 |
|
2 |
2 |
0.05 |
|
||
|
|
|
|||
|
1 |
1.2 |
0.03 |
|
|
|
2 |
0.4 |
0.01 |
|
|
Насос |
3 |
1.6 |
0.04 |
0.265 |
|
4 |
2.8 |
0.07 |
|
||
|
|
|
|||
|
5 |
1.6 |
0.04 |
|
|
|
6 |
3.0 |
0.072 |
|
|
Бак |
1 |
3.2 |
0.08 |
0.12 |
|
2 |
1.6 |
0.04 |
|
||
|
|
|
|||
Бак напорный |
1 |
0.8 |
0.02 |
0.0775 |
|
2 |
1.5 |
0.0375 |
|
||
|
|
|
|||
Колонна |
1 |
2 |
0.05 |
|
|
2 |
1.5 |
0.0375 |
0.2 |
|
|
отпарная |
|
||||
3 |
1.5 |
0.0375 |
|
|
|
|
|
|
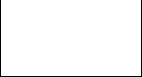
|
4 |
3.0 |
0.075 |
|
|
Колонна |
1 |
3.0 |
0.075 |
0.15 |
|
абгазная |
2 |
3.0 |
0.075 |
||
|
Σ=2.3025
Таким образом, получилось, что за один час с оборудования, находящегося на улице, от одного корпуса в атмосферный воздух поступает 2.3025г/ч.
Производство на данном участке непрерывное. За 8-часовую смену в воздухе оказывается: . За сутки в воздухе оказывается:
.
За год в атмосферном воздухе оказывается около 20 кг хлора. Может показаться мало. Но данное количество хлора выделяется с участка площадью 360 м2. Площадь же большинства химических заводов во много раз превышает данную площадь.
Кроме этого, большинство химических заводов принадлежат к 1 классу опасности и санитарно-защитная зона (СЗЗ) вокруг них должна составлять 1000м и более [3]. Однако, мало где соблюдается данные размеры СЗЗ. Поэтому расчет утечек через неплотности фланцевых соединений должен проводиться на любом химическом предприятии. А его результаты должны учитываться при корректировании СЗЗ. Оба процесса необходимо производить в современных условиях эксплуатации химических производств во избежание аварийных и чрезвычайных ситуаций.
Литература
1.Федеральный закон от 21 июля 1997 г. № 116-ФЗ «О промышленной безопасности опасных производственных объектов», принят Государственной Думой 20 июня 1997 года.
2.Тищенко, Н.Ф. Охрана атмосферного воздуха. Расчет содержания вредных веществ и их распределение в воздухе. Справочник, изд./ Н.Ф. Тищенко. – М.: Химии, 1991. – 368 с.
3.СанПиН 2.2.1/2.1.1.1200-03 «Санитарно-защитные зоны и санитарная классификация предприятий, сооружений и иных объектов». – М., 2007.
УДК 69.057.5:502.3
А.А. Мартин
Новейшие тенденции в разработке антиадгезионных составов для опалубок, связанные с экологическими требованиями
квыпускаемой продукции
Внастоящее время строительство зданий и сооружений из монолитного и сборного железобетона и бетона является одним из ведущих направлений строительной отрасли. До 2008 года объемы выпуска продукций из бетона и железобетона росли, но в результате
кризиса 2008 года объем выпускаемой продукции товарного бетона и сборных железобетонных деталей и конструкций упали с 28,8 млн. м3 и 28,8 млн. м3 в год соответственно до 20,0 млн. м3 и 17,5 млн. м3 – в 2009
году, а за первые 5 месяцев 2010 года объемы выпуска составили соответственно лишь 6,76 млн. м3 и 5,26 млн. м3 [4]. Пусть объемы производства изделий из бетона на время снизились, но вопрос совершенствования технологии и материально-сырьевой базы сохранил свою актуальность. С технологической стороны одними из наиболее важных и трудоемких технологических процессов являются опалубочные работы. Они составляют от 40 … 55% от общей трудоемкости работ по возведению монолитной конструкции, а стоимость колеблется в пределах 30 … 45% соответственно. При этом в опалубочные работы входят: сборка опалубки в крупнопанельные щиты, обработка смазками, установка в проектное положение, распалубка, последующий ремонт [2].
Одним из важнейших компонентов опалубочных работ является использование антиадгезионных составов, направленных на снижение сил сцепления между бетоном и поверхностью палубы. Устранение сцепления бетона с опалубкой влияет на снижение затрат и трудоемкости работ по демонтированию конструкций опалубки, последующего ее ремонта и доводку лицевой поверхности бетона.
Современный рынок антиадгезионных смазок разнообразен, но однозначно то, что нет состава, который идеально бы удовлетворял всем требованиям, которые к нему предъявляются. С момента развития смазочных составов главной решаемой задачей было снижение или полное устранение сцепления бетона с опалубкой. В результате проведенных исследований было выявлено, что основой лучше всего будут служить минеральные, а затем и синтетические масла, благодаря своим барьерным способностям и проявляемым инертным свойствам при контактировании с бетоном. Исходя из этого, несложно понять, что разработка практически всех существующих разделительных составов велась на основе предложенных масел, а совершенствование – сводилось к улучшению состава на базе этих масел.
Внастоящее время, в связи с ухудшением экологической обстановки, стало выдвигаться требование, вставшее наравне с условием устранения сил сцепления – это экологичность применяемых составов, т. е. совершенствованию подлежит не только технологический аспект, но и материально-сырьевая база. Данные исследования получили название «Зеленые технологии». Однако вновь совершенствованию подверглись лишь главные составляющие смазок – масла. В результате исследований были получены составы, которые являются биоразлагаемыми, что значительно снижает вредное воздействие на экосистему. Примером такой смазки является смазка «ЭПРОМ-Б (ЭКС)» фирмы «РЕПРОМ» [8].
Одним из главных условий, для исключения при проектировании смазок, на основе синтетических и минеральных масел, является то, что они образуются из нефти, которая является невозобновляемым источником сырья. В связи с увеличением добычи нефти ее запасы уменьшатся, и наступит время, когда основа для масел исчезнет. Ко всему прочему смазки на основе нефтекомпонентов имеют кислотную среду, что может приводить к коррозии щитов опалубки, произведенных из стали. Это вынуждает проектировщиков прибегать к добавкам ингибиторов коррозии, что приводит к удорожанию конечной продукции [3]. Вывод напрашивается сам. Необходимо вести разработки альтернативных компонентов для проектирования смазок, причем желательно, чтобы они были восполняемыми и инертными по отношению к материалу палубы и бетону.
ВННГАСУ в результате возобновленных исследований, В.А. Войтовичем, И.Н. Хряпченковой были изучены новые основообразующие компоненты антиадгезионных смазок на основе фузов. Они представляют собой отходы, образующиеся при переработке растительных масел. Запасы фузов достаточно велики, однако, их утилизация одна из современных проблем. Они нетоксичны и экологически безопасны. На их основе были получены смазки по типу обратной эмульсии для применения на фанерных
иметаллических щитах опалубки, которые в результате испытаний показали снижение поверхностной пористости бетона и пластифицирование бетона в пристыковом слое, что снижает трудозатраты на демонтаж опалубки. Данные смазки получили название «антиадгезионные смазки ЭФО» [6].
Следующим примером приведу смазку, разработанную на основе использования жиропеномассы, образующейся в результате очистки сточных вод рыбоперерабатывающих предприятий, и соапстока, являющегося отходом процесса рафинации рыбных жиров. Данный состав был разработан Технологическим факультетом МГТУ, кафедрой пищевых производств [5]. В процессе исследования был получен состав прямой эмульсии. Главной проблемой проектирования этой смазки являлось снижение содержания липидов до 3,5 – 6%, иначе на поверхности будут
оставаться следы жирных пятен, что не допускает СТБ 1707-2006 [1]. Если процентное содержание липидов будет ниже 3%, то тогда будут ухудшаться антиадгезионные свойства эмульсии. Выход был найден путем применения сепарирования, что обеспечивало необходимое содержание липидов. В результате на выходе получался состав, который по качественным характеристикам не уступает традиционной смазке на основе эмульсола ЭКС.
В зарубежной практике наиболее востребованными смазками являются составы компании «ADDINOL». Самая известная смазка на растительном основообразующем компоненте – ADDINOL Ökoplus XTU. Биоразлагаемая смазка на основе нефтекомпонентов – ADDINOL F10. Помимо Европы, данный состав нашел широкое применение и в России, и в странах СНГ. В результате на Украине для снижения стоимости смазочных составов были разработаны аналоги смазки ADDINOL F10, только с применением масел растительного происхождения. Это составы «Биосмол - 1» и «Биосмол - ЭМ». Экономический эффект разработанных смазок на обработку на 1м2 палубы без НДС в ценах на IV квартал 2011 года составлял 1,09 руб/м2 и 0,74 руб/м2 соответственно по отношению к
ADDINOL F10 – 1,79 руб/м2 [9].
Все приведенные составы не требуют специальных условий утилизации, не оказывают вредного воздействия на окружающую среду и организм человека, а качественные характеристики сравнимы с показателями смазок на минеральных маслах, что делает данные составы конкурентно способными на рынке смазочных материалов.
Данные примеры показывают, что выбранное направление является приоритетным в настоящем и будущем времени, но оно не спешит выходить на первостепенные роли. Причиной тому служат несколько факторов, которые необходимо полноценно изучить и найти выход из них. В компании «ADDINOL», в результате исследований, установили, что если проводить параллели по схеме «производство-использование» смазки на растительном основообразующем будут стоять по нагрузке на экологию в одном ряду с составами на основе нефтепродуктов. Такой результат получается за счет сильных воздействий на экосистему в процессе производства составов. Дополнительно установлено, что экологические свойства растительных масел имеют и негативную сторону – они подвержены микробиологическому разложению, поэтому при использовании таких масел в качестве формовочных часто наблюдается возникновение неприятного запаха при долгом складировании масла или преждевременному разложению состава до нанесения на формующую поверхность [10].
Литература
1.СТБ 1707-2006. Смазки для форм и опалубок. Общие технические условия. - Введ. 2007-06-01. – Минск.: Госстандарт, 2007. – 13 с.
2.Хряпченкова, И.Н. Совершенствование технологии железобетонных конструкций на основе применения эффективных антиадгезионных смазок: автореф. дис. … канд. техн. наук: 05.23.08 / И.Н. Хряпченкова; Нижегор. гос. архитектур.-строит. академия. – Н. Новгород, 1995. – 20 с.
3.Гордиюк, Ю.П. Оптимизация свойств смазочных составов с целью повышения качества и эффективности монолитного домостроения: дис. на соискание степ. магистра техники и технологии по направлению 270100 – «Стр-во»: программа 550102 – «Теория и практика орг.-технол. и экон. Решений» / Ю.П. Гордиюк ; науч. рук. программы А.А. Яворский; Нижегор. гос. архит.-строит. ун-т. – Н.Новгород, 2006. – 145, [8] с.: ил. – Библиогр.: с. 133-141.
4.Бублиевский, А.Г. Рынок бетона в 2010 году: итоги и прогнозы на
будущее / А.Г. Бублиевский // Технологии бетонов. – 2011. – №3-4 (56-57).
–С. 8-9.
5.Петров, Б.Ф. Технология антиадгезионной смазки на основе жировых отходов рыбоперерабатывающих предприятий. / Б.Ф. Петров //
Вестник МГТУ. –2010. – № 4 (1),т. 13. – С. 678-680.
6. Симирский, В.В. Разработка отечественных антиадгезионных смазок для опалубок и форм с улучшенными характеристиками на основе возобновляемого сырья / В.В. Симирский, О.Е. Игнашева, Ю.Н. Луговик, Н.А. Вориводская, О.А. Ивашкевич // Труды БГУ. – Минск, 2010. – Вып. 2, Т. 4. – С. 69-80.
7.Стойчев, В. Б. Эффективные антиадгезионные смазки для опалубок монолитного железобетона на основе фузов / В.Б.Стойчев, И.Н.Хряпченкова, В.А. Войтович// Приволжский научный журнал. – 2010.
–№ 3 (15). – С. 112-118.
8.http://www.reprom-sm.ru/razdelitelnye-smazki/
9.http://www. SMAZKI.com.ua
10.http://www.addinol.ru
УДК 624.191.95
Е.А. Мордвина
Основы проектирования и оптимизация выбора гидроизоляции в современном строительстве
Качественная гидроизоляционная защита конструкций является одной из важнейших проблем нового строительства и эксплуатации существующих зданий и сооружений. В настоящее время происходит
стремительное освоение подземного пространства, возрастает количество уникальных по сложности объектов. Так, подземные паркинги, метрополитены, интенсивно эксплуатирующиеся подвалы высотных зданий, сооружения транспортной инфраструктуры зачастую возводятся в различных, в том числе сложных гидрогеологических условиях. Такие сооружения невозможно качественно построить без надежной, грамотно выбранной и запроектированной гидроизоляции, обеспечивающей безотказную работу и надлежащие условия эксплуатации объекта на протяжении всего проектного срока службы.
Для обеспечения эффективного функционирования гидроизоляции необходимо ориентироваться на системный подход к реализации решений по ее созданию. Следует акцентировать внимание на том, что гидроизоляционный материал - это лишь часть гидроизоляционной системы сооружения, состоящей из совокупности элементов, направленных на защиту от внешних факторов, в основном воды, а порой - агрессивных ее составляющих (хлоридов, двуокиси углерода и т.д). Что касается гидроизоляционной системы, то основное ее назначение - препятствовать проникновению влаги в глубь сооружения (подвалы, железнодорожные тоннели), либо наоборот, держать воду внутри него (бассейны, гидротехнические сооружения).
Качество гидроизоляции закладывается, в первую очередь, на стадии проектирования, когда требуется выбрать оптимальный для конкретного случая вариант технического решения. На стадии технического проекта устанавливают назначение гидроизоляции и основные требования к ней. На основании технико-экономического сравнения вариантов и схематической проработки конструкции выбирают тип гидроизоляции, определяют объемы и стоимость работ. На стадии рабочих чертежей уточняют основные положения технического проекта, определяют состав необходимых гидроизоляционных материалов, включая, при необходимости, использование расчетных методов и проведение лабораторных исследований для возможной корректировки рецептуры. Разрабатывают проект гидроизоляции с детализацией узлов, сопряжений и уплотнений деформационных швов, составляют проект производства гидроизоляционных работ.
Проектирование современной гидроизоляции является сложным и ответственным процессом, выполнение которого на практике должно осуществляться высококвалифицированными, опытными специалистами. Еще на начальном этапе проектирования необходимо учитывать следующие ответственные моменты, определяющие выбор материала, а
также технологию производства гидроизоляционных работ: |
|
||
1) Категорию |
ответственности |
возводимого |
сооружения, |
особенности его конструктивного решения, назначение гидроизоляции.
2)Климатические условия района строительства: температуру воздуха и ее экстремальные значения, скорость изменения температуры воздуха, а также требования к гидроизоляционным покрытиям в отношении теплоустойчивости, трещиностойкости, прочности и т. п.
3)Геологические, гидрологические, гидрохимические условия района строительства, которые важны для определения видов и интенсивности внешних воздействий.
4)Производственные условия возведения конкретного сооружения, определяющие возможность и целесообразность применения различных способов выполнения гидроизоляционных работ.
К сожалению, в настоящий момент при выборе гидроизоляции первостепенное значение уделяется стоимости материала, с целью максимальной экономии средств. Стоимость гидроизоляции незначительна, по сравнению с ее ролью в обеспечении надежного функционирования объекта, а ремонт водонепроницаемых покрытий в отдельных случаях в пятьдесять раз выше первоначальной стоимости ее устройства [1]. По этой причине значительно большее внимание при сравнении вариантов требуется уделять ремонтопригодности, экологичности, технологичности гидроизоляционной системы, возможности механизации процессов производства работ и т.д. При выборе гидроизоляционных материалов необходимо учитывать и конкретную фирму - производителя, опыт применения ее продукции на отечественном и зарубежном рынках, отсутствие рекламаций, наличие системного подхода по обеспечению качества, включая наличие технических регламентов на этапы проектирования и производства работ.
Особое влияние при проектировании гидроизоляции новых
объектов и, в первую очередь, в случае проведения ремонтностроительных работ оказывает совместимость гидроизоляционного материала с субстратом и другими материалами. Зачастую заказчики, используя при гидроизоляции конструкций новейшие эффективные, дорогостоящие материалы не получают должного результата по причине отсутствия у применяемых гидроизоляционных материалов адгезии к старым (битуминозным), применявшимся ранее. Например, при ремонте гидроизоляции фундаментов невозможно качественно наклеить ПВХ мембраны или нанести эпоксидную композицию на уже имеющиеся битуминозные материалы. Так же при ремонте старой битуминозной кровли из-за отсутствия адгезии к основанию нецелесообразно использовать мембраны на основе полиофиленов или ПВХ-мембраны, так как в результате по истечении непродолжительного срока вновь потребуется восстановление гидроизоляционного слоя.
Для обеспечения качественного контакта гидроизоляционного материала с основанием при проектировании необходимо иметь знания и уметь практически использовать теоретическую концепцию
совместимости строительных материалов, созданную, научным руководителем программы «Гидрозащита», профессором О.А. Лукинским [2]. Данная концепция подтверждена материалами масштабных экспериментальных исследований, в результате которых были выявлены материалы, обладающие адгезионными свойствами на химическом уровне, т.е. практически родственные. Такую адгезию можно считать абсолютной, как, например, для битума и бутилкаучука. При испытании на отрыв такой контактной пары происходит когезионный разрыв по герметикам, как правило, мастичного типа [3].
Как было отмечено, обязательным при выборе материала гидроизоляции является наличие у фирмы производителя документации, подтверждающей качество предлагаемой продукции (сертификатов, паспортов, технических условий), которые в определенной мере гарантируют надежность материала и, соответственно, его качество и долговечность. Однако, в нормативно-технической документации на гидроизоляционные материалы, как правило, отсутствуют конкретные показатели, характеризующие их долговечность, а другие, физикотехнические характеристики, не всегда гарантируют их надежную работу в течение длительного времени.
Поэтому особое значение приобретает разработка методик, позволяющих научно обоснованно прогнозировать эксплуатационную долговечность гидроизоляционных материалов. Применительно к рулонной гидроизоляции в НИИМосстрой разработана «Методика испытаний рулонных и мастичных кровельных материалов на долговечность», в которой режим ускоренных испытаний был скорректирован на основании данных, полученных при исследовании различных видов современных кровельных материалов. Продолжительность испытаний по данной методике сокращена, практически в два раза, в сравнении с проведением аналогичных исследований, согласно методическим рекомендациям, разработанным совместно тремя институтами ВНИИстройполимер, МНИИИТЭП, ЦНИИПромзданий [4].
Помимо рулонных материалов, в системах гидроизоляции используется значительное количество других вариантных решений, постоянно совершенствующихся и обновляющихся. Так, постепенно завершается переход от применения традиционных битумных материалов к использованию более эффективных битумно-полимерных и полимерных. Среди относительно новых для России систем невозможно оставить без внимания группу гидроизоляционных материалов проникающего действия («Пенетрон», «Лахта», «Пенеплаг», «Кальматрон», «Акватрон», « ПластГидро» и т.д.)[5]. В нашей стране их все шире внедряют в практику строительства, все чаще используют при восстановлении поврежденной, либо вышедшей из строя гидроизоляции