
10694
.pdf131
рациональным является применение замкнутых гнутых профилей из низколегированных сталей, т. к. происходит объединение этих факторов;
2.Снижение веса балок составило примерно 25-42% в зависимости от прочности стали (при обеспечении требований жесткости), колонн – 2035%;
3.При среднестатистических значениях удельного радиуса инерции
инагруженности применение низколегированных сталей эффективно по массе для конструкций промышленных зданий, листовых конструкций, башен, мачт, мостов.
Использование таких сталей для изгибаемых элементов ограничивается условиями II группы предельных состояний. Уменьшение сечения приводит к увеличению прогиба, так как при изменении прочности стали величина еѐ нормального модуля упругости остается постоянной.
Данной тематике посвящен ряд исследований кафедры МК ННГАСУ. Согласно методике А. И. Колесова, Б. С. Поликарпова [3] при
предельном прогибе fu = l/250 оптимальные размеры сечения изгибаемого элемента определяются условиями прочности. При этом эффективно применение сталей повышенной прочности, а относительная высота
сечения балки составляет h ≈ l/15. При fu < l/250 оптимальные размеры сечения определяются условиями жесткости, а прочностные свойства материала используются не полностью.
Следовательно, при выборе стали необходимо учитывать определяющее предельное состояние конструкции и ее элементов. Таким состоянием для балок может также являться местная устойчивость стенок. Согласно исследованиям стенки балок, выполненные из низколегированных сталей, менее устойчивы, чем аналогичные по гибкости стенки, выполненные из малоуглеродистой стали.
Наиболее полное использование преимуществ сталей повышенной и высокой прочности реализовано в методе проектирования бистальных балок. Согласно принятым методикам рациональность применения низколегированной стали определяется величиной нормальных напряжений, действующих в поперечных сечениях. Сталь повышенной прочности применяется только в наиболее напряженных участках поясов балок, а вся стенка и пояса вблизи опор, т. е. участки, испытывающие меньшие нормальные напряжения, выполняются из малоуглеродистой стали.
Рекомендуется при расчетах прочности таких балок руководствоваться одним из двух критериев [4]:
предельных пластических деформаций: пластические деформации допускаются не только в стенке, но и в поясах; вводится ограничение на величину интенсивности пластических деформаций в стенке;
132
предельных напряжений в поясах балки: пластические деформации допускаются лишь в стенке; работа поясов ограничена упругой стадией.
Различные марки сталей могут использоваться и в балках с гибкой стенкой. В отсеках с преимущественным изгибом рационально для стенок и поясов использовать стали одинаковых марок или для поясов применять более прочные стали. В отсеках, преимущественно работающих на сдвиг, стенка оказывается весьма нагруженной, а сечение поясов зачастую определяется условиями устойчивости, когда прочность стали не играет определяющей роли. Поэтому рационально в стенке и поясах использовать сталь одинаковой прочности или в стенках использовать более прочную сталь. Установлено, что оптимальное соотношение расчетных сопротивлений Ryw=(1,3÷1,4) Ryf. Балки с гибкой стенкой рекомендуется проектировать из малоуглеродистых сталей и сталей повышенной прочности, варианты с применением высокопрочных сталей не рекомендуются [4]. Аналогичные требования по применению сталей различной прочности распространяются на методы проектирования балок с гофрированной стенкой и перфорированные балки.
Анализ результатов исследований показывает, что использование сталей повышенной и высокой прочности является возможным путем снижения расхода металла на строительные конструкции. Подобное решение в сочетании с рациональной конструктивной формой и правильно подобранными характеристиками сечений позволяет существенно повысить экономическую эффективность конструкций. В магистерской диссертации влияние прочности стали на несущую способность предполагается рассмотреть на примере рамы с элементами непрерывного переменного сечения.
Значительная экономия стали в таких рамах достижима в первую очередь за счет уменьшения расчетных сечений ригеля. Снижение металлоемкости также возможно при тонкостенной конструкции ригеля. Результаты ВКР(б) показывают, что в рассмотренной раме пролетом 36 м ригель работает преимущественно на изгиб, поэтому основой для исследований служат соответствующие главы норм [4,5].
Методика подбора сечений изгибаемых элементов позволяет установить размеры минимальных по площади сечений шарнирно опертых балок, нагруженных в плоскости стенки и имеющих сварное двутавровое двоякосимметричное сечение с устойчивой и гибкой стенкой, а также определить наиболее эффективное сопротивление стали [5]. Оптимальную высоту изгибаемых элементов можно определить для балки постоянного и переменного сечений, бистальной балки и балки, рассчитываемой с учетом развития ограниченных пластических деформаций [4,5].
В результате анализа нормативных источников отмечено:
1. нормы не содержат рекомендаций по расчету элементов с непрерывным переменным сечением;
133
2.методики расчета бистальных балок и балок с гибкой стенкой не предусматривают их работу в условиях сжатия с изгибом, характерных для ригелей рам;
3.основой существующих методов расчѐта стальных конструкций являются стержневые модели с линейным упругим законом поведения стали, а также модели с линейным упругим поведением и с ограниченным перераспределением пластических деформаций в сечениях элементов конструкций;
4.нормы основаны на методе Эйлера и учитывают момент потери устойчивости только при действии продольных усилий в сжатых, сжатоизогнутых стержнях конструкций.
Действительные условия развития пластических деформаций в конструкциях требуют применения в научных исследованиях расчѐтных моделей с учѐтом нелинейного упругого и пластического поведения стали
–моделей с учѐтом физической нелинейности работы стали. Чтобы наиболее полно и точно выполнять расчѐты, необходимо одновременно учитывать в моделях влияние деформирования конструкции на изменение еѐ напряжѐнного состояния, т. е. рассматривать одновременно физически и геометрически нелинейные модели. Пространственные модели позволяют выполнять расчѐт устойчивости с учѐтом действия пространственно распределѐнных по сечениям стержней рам расчѐтных сочетаний нагрузок. Возможность пространственного моделирования поперечных сечений, узловых соединений, передачи нагрузки на элементы конструкции позволяет учесть в расчѐтах геометрическую нелинейность деформирования не только стержней конструкции, но и их поперечных сечений одновременно.
Рассмотренные вопросы определили цель магистерской диссертационной работы: выполнить численные исследования нелинейной работы стальных рам с непрерывным переменным сечением элементов с учетом влияния конструктивных факторов и различной прочности стали.
Для достижения намеченной цели поставлены следующие задачи:
1.Исследовать работу стальных рам на пространственных пластинчатых конечно-элементных моделях с учѐтом физической нелинейности работы стали и геометрической нелинейности деформирования конструкции под нагрузкой в условиях сложного напряженного состояния.
2.Разработать расчѐтную выборку стальных рам путем варьирования определяющих характеристик конструкций: марок сталей, относительных эксцентриситетов сечений, гибкостей элементов, нагруженности сечений, распределения материала по длине стержней и элементам поперечных сечений и др.
3.Оценить влияние прочности стали на несущую способность и деформативность элементов рам.
134
4.Оценить влияние прочности стали на расход и стоимость материала в рамах.
5.Оценить эффективность полученных конструктивных решений.
6.Разработать рекомендации по применению сталей различной прочности в рамах, рациональным конструктивным решениям рам с элементами непрерывного переменного сечения, выбору оптимальных расчѐтных моделей.
Литература
1.Кузнецов, А.Ф. Строительные конструкции из сталей повышенной и высокой прочности (технология изготовления и монтажа, технико-экономические показатели) / А.Ф. Кузнецов. – М.: Стройиздат,
1975. – 80 с.
2.Металлические конструкции: сб. ст. ЦНИИСК / под ред. В.А. Балдина. – М.: Стройиздат, 1968. – 190 с.
3.Колесов, А.И. Стальная рабочая площадка промздания. Компоновка, конструирование и расчет несущих элементов: учеб. пособие/ А.И. Колесов, Б.С. Поликарпов. – Н. Новгород: ННГАСУ, 1998. – 91 с.
4. Пособие по проектированию стальных |
конструкций |
(к СНиП II-23-81*): утв. Госстроем СССР 15.08.85. – М.: |
ЦИТП Госстроя |
СССР, 1989. – 148 с.
5. СП 16.13330.2011. Стальные конструкции. Актуализированная редакция СНиП II-23-81*: свод правил: утв. Минрегионом России 27.12.10: дата введ. 20.05.11. – М.: Минрегион России, 2011. – 177 с.

135
ТЕПЛОГАЗОСНАБЖЕНИЕ. ОТОПЛЕНИЕ И ВЕНТИЛЯЦИЯ. ВОДОСНАБЖЕНИЕ И ВОДООТВЕДЕНИЕ. ГИДРАВЛИКА.
ГИДРОТЕХНИЧЕСКИЕ СООРУЖЕНИЯ
УДК 621.1
А.И. Автономов
Устройство и принцип работы тепловых труб
Тепловыми трубами названы испарительно-конденсационные устройства для передачи тепла, в которых осуществляется перенос скрытой теплоты парообразования за счет испарения жидкости в зоне подвода тепла и конденсации ее паров в зоне отвода, а замкнутая циркуляция теплоносителя поддерживается действием капиллярных или массовых сил.
Возможны самые различные модификации тепловых труб. В простейшем случае тепловая труба (рис. 1) имеет герметичный корпус, внутренняя поверхность которого устлана слоем капиллярно-пористого материала – фитилем, который насыщен жидкой фазой теплоносителя. Фитилем могут служить различные пористые материалы (сетки, спеченные пористые структуры), канавки на внутренней поверхности корпуса трубы, экраны с перфорациями или какая-либо другая структура, способная осуществлять перенос жидкости из зоны конденсации в зону нагрева за счет действия капиллярных сил. В качестве теплоносителя могут быть использованы любые химически чистые материалы или соединения, имеющие жидкую и паровую фазу при рабочей температуре трубы и, как правило, смачивающие материал фитиля. Используя в качестве теплоносителей жидкий гелий, азот, спирты, фреоны, воду, щелочные металлы и т. п., можно создать тепловые трубы для работы как в областях низких, криогенных, температур, так и в области высоких температур – 2500° С и даже выше.
Рассмотрим работу тепловой трубы простейшего типа в условиях отсутствия массовых сил. Подводимое к трубе тепло передается за счет теплопроводности через корпус трубы и, зачастую, через элементы фитиля к теплоносителю. Испарение смачивающей фитиль жидкости приводит к образованию или увеличению кривизны вогнутых менисков на поверхности жидкости в порах фитиля в зоне нагрева. Под действием сил поверхностного натяжения в вогнутых менисках появляется капиллярное давление Ркап, воздействующее на жидкость и стремящееся уменьшить кривизну менисков. Капиллярное давление в мениске определяется по формуле Лапласа:
Ркап = σ(1/R1+1/ R2), |
(1) |
где Ркап – капиллярное давление; R1 и R2 – главные радиусы кривизны поверхности мениска.
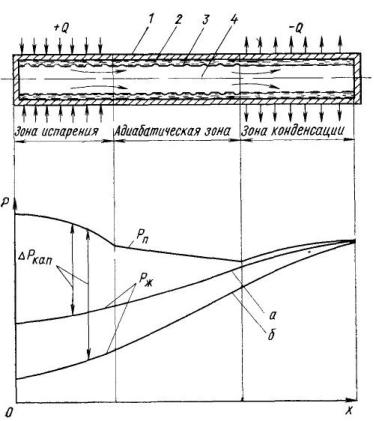
136
Рис. 1. Схема цилиндрической тепловой трубы и качественное распределение давления в паре Рп и жидкости Рж без воздействия массовых сил (а) и в поле сил гравитации, направленных против течения жидкости в фитиле (б): 1 – корпус, 2 – фитиль;
3 – жидкость, 4 – пар
Конденсация жидкости в зоне отвода тепла приводит к затоплению фитиля. Кривизна менисков жидкости внутри фитиля в этой зоне, как правило, ничтожна по сравнению с соответствующей кривизной в зоне нагрева трубы. Различие кривизны менисков и, следовательно, капиллярных давлений в этих двух зонах трубы приводит к появлению перепада этих давлений, который является движущим перепадом давления при перекачке жидкости по фитилю из зоны конденсации в зону испарения. Таким образом, в тепловой трубе для обеспечения замкнутой циркуляции теплоносителя используется «капиллярный насос». Помимо капиллярных сил при работе тепловых труб могут действовать массовые силы – гравитационные, центробежные, электромагнитные и др. Массовые силы способны как улучшать циркуляцию теплоносителя в тепловых трубах, так и затруднять ее.
В работающей трубе при циркуляции теплоносителя имеют место следующие процессы: 1) испарение жидкой фазы теплоносителя в зоне нагрева при подводе тепла от источника; 2) перенос пара в зону с пониженным давлением – зону теплоотвода и конденсации; 3) конденсация пара в зоне теплоотвода; 4) подача жидкости из зоны конденсации в зону испарения под действием капиллярных или массовых сил.
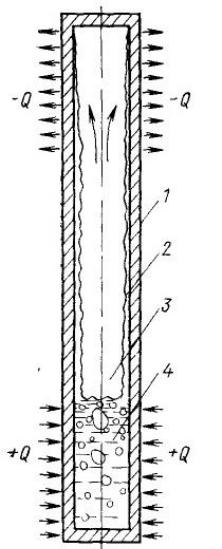
137
Каждый из этих процессов происходит с изменением давления вдоль линии тока циркулирующего теплоносителя. При течении пара по паровому каналу изменение давления происходит как за счет гидравлических потерь, обусловленных трением, так и за счет инерционных эффектов – статическое давление в паре изменяется при вдуве массы пара в поток (испарение) или отводе массы пара (конденсация). Для жидкости, движущейся по фитилю под действием капиллярных сил, давление изменяется главным образом вследствие трения. В зоне испарения и конденсации на границе раздела фаз жидкость
– пар помимо капиллярного давления имеет место перепад давления при фазовом переходе, обусловленный динамическим воздействием испаряющегося или конденсирующегося теплоносителя. В любом сечении стационарно работающей трубы перепад давления между фазами уравновешивается капиллярным давлением:
Рп-Рж+ΔРф‘=Ркап |
(2) |
где Рф‘– перепад давления между паром и жидкостью вследствие фазового перехода.
Рис. 2. Схема испарительного термосифона: 1 – корпус; 2 – плѐнка конденсата; 3 – пар; 4 – объѐм кипящей жидкости
138
Типичное распределение давления в паре и жидкости по длине тепловой трубы показано на рис. 1. Кривизна менисков и капиллярное давление по длине трубы изменяются. Максимальная кривизна имеет место в начале испарительной зоны трубы, а минимальная – в конце зоны конденсации. Кривая а – изменение давления в жидкости при отсутствии воздействия массовых сил, кривая б, данная для сравнения, – распределение давлений в жидкости по длине трубы с учетом влияния гравитации в случае, когда силы тяжести препятствуют циркуляции жидкости. При постоянном значении передаваемой трубой мощности влияние гравитации приводит к тому, что капиллярный насос должен развивать более высокий перепад давления по сравнению с работой трубы
вневесомости.
Вусловиях, когда силы гравитации или иные силы (центробежные, электромагнитные) способны обеспечить перенос жидкости из зоны конденсации в зону нагрева, могут использоваться тепловые трубы, не имеющие капиллярной структуры – бесфитильные тепловые трубы. Конструкция тепловой трубы, не имеющей капиллярной структуры и работающей на использовании гравитационных сил, представлена на рис.2. Такую тепловую трубу принято называть испарительным термосифоном.
Литература 1. Ивановский, М.Н. Физические основы тепловых труб/
М.Н.Ивановский, В.П.Сорокин, И.В. Ягодник. – М., 1978. – С. 9-12.
УДК 662.6
С.П. Барабошкин
Способ контроля горения в топке на основании спектрального анализа в диапазоне длин волн от 0,4 до 1,2 мкм
Условием эффективного (экономичного и устойчивого) процесса сжигания топлива является рациональная организация топочного процесса, включающая оперативный контроль горения топлива и выработку управляющих сигналов для оптимизации процесса. Для контроля горения могут использоваться различные параметры, например температура в определенных зонах, количество подаваемого кислорода, концентрация продуктов сгорания и т.п. Широкое распространение получили способы контроля горения, использующие спектральный анализ пламени, имеющего в составе спектра линии кислорода, газообразных продуктов сгорания, сажи и элементов самой топки.
Для сжигания определенного количества топлива определенного состава необходимо строго определенное количество кислорода. При его
139
недостатке возникает недожог топлива с образованием оксида углерода и молекулярного водорода, оказывающих вредное влияние на окружающую среду. Однако и значительное увеличение количества подаваемого воздуха нецелесообразно, поскольку в этом случае увеличивается выброс в атмосферу избытка нагретого в топке и не участвующего в реакции с топливом воздуха, что ухудшает экономические характеристики топки.
Известен спектральный способ контроля горения, используемый для регулирования подачи топлива и воздуха в горелку. Способ включает прием сигнала от пламени горелки с помощью оптоволоконного датчика, установленного так, что его приемное окно расположено напротив ядра горения. Способ включает также передачу сигнала по световоду на спектрометр и анализ полученного сигнала с целью определения количества воздуха в газообразных продуктах сгорания.
Способ контроля горения по количеству воздуха в топке обеспечивает хорошие результаты в том случае, если состав и количество подаваемого топлива, а также режим работы котла остаются неизменными. Однако обычно характеристики и количество подаваемого топлива, а также режим горения в процессе эксплуатации меняются и наличие расчетного количества воздуха в топке не всегда свидетельствует об оптимальном режиме работы. По количеству находящегося в средней части топки (в области ядра горения, где установлен датчик) воздуха невозможно определить, сгорает ли топливо полностью непосредственно в топке или уже за ее пределами. Поток подаваемой в топку топливновоздушной смеси практически не бывает однородным, что усугубляется взаимодействием потоков топливно-воздушной смеси из разных горелок внутри самой топки: в отдельных участках топки появляются макрозоны с избытком или недостатком воздуха, необходимого для полного сжигания топлива при одинаковой его средней концентрации по топке. Это обычно ведет к выбросам продуктов неполного сгорания топлива в атмосферу.
Таким образом, этот способ не обеспечивает достаточно высокую точность контроля горения.
Более достоверные результаты дает способ, также основанный на спектральном анализе пламени и включающий выделение спектральных линий излучения продуктов сгорания, а именно паров воды и углекислого газа. Основные спектральные линии этих продуктов сгорания лежат в диапазоне длин волн от 1,38 до 6,3 мкм. В результате обработки полученных сигналов на компьютере определяются концентрации указанных продуктов сгорания и изменение этих концентраций, и вырабатывается соответствующий управляющий сигнал.
Поскольку в этом способе контролируются концентрации продуктов сгорания и изменение концентраций этих продуктов, результаты анализа позволяют корректировать режим горения (подачу топлива и кислорода) с большей эффективностью по сравнению со способом, описанным выше.
140
Однако, как и в способе, описанном выше, для анализа используется спектральный диапазон, в котором находятся линии излучения как продуктов неполного сгорания, так и элементов самой топки, создающие такой уровень шумовых сигналов, который делает анализ выбранных линий затруднительным.
Для улучшения параметров контроля горения необходимо исключить влияния спектральных шумов, и тем самым повысить экологические и экономические характеристики топки.
Поставленная задача решается тем, что в способе контроля горения на основе спектрального анализа выбирают диапазон длин волн от 0,4 до 1,2 мкм, измерения производят вне горелочного устройства в верхней части топочной камеры вблизи выхода, и по амплитуде пульсаций излучения сажи судят о режиме горения.
В выбранном диапазоне длин волн присутствуют только сигналы излучения паров воды и сажи, причем сигналы излучения паров воды настолько слабы по сравнению с излучением сажи, что ими можно пренебречь. Поэтому выделение сигнала излучения сажи не представляет трудностей.
Общеизвестно, что в нижней части топочной камеры, вблизи горелок, где процесс горения топлива еще не закончен, количество сажистых частиц и других продуктов неполного сгорания очень велико. Поэтому контролировать процесс горения с целью обеспечения высоких экономических и экологических характеристик целесообразно вблизи выхода из топки в верхней части топочной камеры вне горелочного устройства. Это позволяет анализировать конечные результаты процесса сжигания топлива, которые и определяют экономические и экологические характеристики работы топки. Как показывает практика, при оптимальном режиме горения (достаточном количестве кислорода для данного топлива и данной температуры) частицы сажи в верхней части топочной камеры практически отсутствуют, и появление сигнала излучения сажи свидетельствует о нарушении режима горения, а изменение амплитуды пульсаций свидетельствует об изменении концентрации частиц сажи. Выбор сигнала излучения сажи в качестве контролируемого параметра горения обладает рядом преимуществ. Прежде всего сигнал от частиц сажи, как и от любого твердого тела, весьма мощный. Это очень удобно для измерения, поскольку не требует особенно сложного оборудования или средств обработки сигнала. Диапазон излучения сажи относительно широкий, что позволяет упростить используемое оборудование и методику обработки сигнала. И, самое главное, в выбранном диапазоне практически отсутствуют мешающие сигналы от других продуктов сгорания.
Принципиальная схема системы контроля показана на рисунке 1.