
10534
.pdf60
эффективной добавкой-активатором является пыль электрофильтров вращающихся печей. Исследовано влияние этой добавки на свойства гранул, полученных прессованием под давлением от 5 до 50 МПа.
Определена водопотребность формовочных смесей в зависимости от расхода добавки-активатора и максимального давления при прессовании. Влажность попутного продукта на фильтре в условиях ВАЗ изменяется в пределах от 17,2 до 29,5 %. При прессовании гранул из фосфополугидрата с высокой влажностью или при более высоком удельном давлении необходимо понизить относительное содержание воды в формовочной смеси (В/Т). Это достигается введением сухой добавки-активатора. С целью определения водопотребности формовочных смесей при различном давлении прессования расход добавки-активатора варьировали от 3 до 30 % массы сухого фосфополугидрата. Результаты определения водопотребности формовочных смесей приведены в таблице 3.10.
Таблица 3.10 – Зависимость водопотребности формовочных смесей от давления прессования и расхода добавки-активатора
Расход |
Водопотребность смеси, %, при давлении прессования, МПа |
||||||
добавки, |
|
|
|
|
|
|
|
5 |
10 |
20 |
30 |
40 |
50 |
||
% |
|||||||
|
|
|
|
|
|
||
|
|
|
|
|
|
|
|
0 |
30,0 |
27,0 |
19,0 |
16,0 |
12,0 |
10,0 |
|
|
|
|
|
|
|
|
|
3 |
30,0 |
28,0 |
19,0 |
17,0 |
13,0 |
10,0 |
|
|
|
|
|
|
|
|
|
5 |
30,5 |
28,0 |
20,0 |
17,0 |
13,5 |
10,5 |
|
|
|
|
|
|
|
|
|
10 |
31,0 |
28,5 |
21,0 |
17,5 |
14,0 |
11,0 |
|
|
|
|
|
|
|
|
|
15 |
31,5 |
29,0 |
21,5 |
18,0 |
15,0 |
11,5 |
|
|
|
|
|
|
|
|
|
20 |
32,0 |
29,5 |
22,0 |
18,5 |
15,5 |
11,5 |
|
|
|
|
|
|
|
|
|
25 |
32,5 |
29,5 |
22,5 |
19,0 |
16,0 |
12,0 |
|
|
|
|
|
|
|
|
|
30 |
33,0 |
30,0 |
23,0 |
20,0 |
16,5 |
12,5 |
|
|
|
|
|
|
|
|

61
Из таблицы 3.10 следует, что введением добавок-активаторов можно регулировать водопотребность в пределах, не превышающих 2,5− 4,5 % при расходе добавки от 0 до 30 %. Это позволяет при изготовлении гранул прессованием жестких смесей использовать фосфополугидрат, имеющий высокую влажность на фильтре.
Из таблицы 3.10 следует также, что расход высокодисперсной добавки необходимо назначать в зависимости от влажности попутного продукта и давления при прессовании. На основании результатов определения водопотребности формовочных смесей были приготовлены образцы высотой и диаметром 25 мм. При изготовлении образцов давление прессования изменялось в пределах от 10 до 40 МПа. Сразу после прессования гранул (в возрасте 3 мин) определена их прочность при сжатии. Результаты испытания образцов приведены на рисунке 3.13.
Рисунок 3.13 — Зависимость прочности гранул после прессования от расхода добавки и давления прессования при В/Т, соответствующем водоотделению смеси.
Давление при прессовании, МПа:
1 – 10; 2 – 20; 3 – 30; 4 – 40.

62
Из рисунка 3.13 следует, что гранулы с пределом прочности при сжатии более 1 МПа после прессования можно получить при расходе добавки равном 5 % и давлении при прессовании более 10 МПа.
Влияние механохимической активации на свойства гранул
Результаты определения скорости гидратации фосфополугидрата и смеси и прочности образцов от продолжительности механохимической активации смеси на бегунах представлены на рисунке 3.14 и в таблице 3.11. При механохимической активации использована проба влажного фосфополугидрата, отобранного с карусельного фильтра ВАЗ, влажность —
20,9 %.
Рисунок 3.14 — Влияние механохимической активации на скорость гидратации фосфополугидрата и влажность формовочной смеси:
1 – содержание химически связанной воды, % от массы твердых веществ; 2 – влажность смеси, %
Увеличение продолжительности обработки ФПГ на бегунах приводит к ускорению процессов гидратации полуводного сульфата кальция и, как следствие, снижению влажности смеси.
Ранее было отмечено, что после 5 мин обработки на бегунах пластичность смеси резко повышается. Это может быть связано с изменением зернового состава попутного продукта и формы зерен сульфатов кальция за
63
счет разрушения последних, а также удалением газовой фазы из обрабатываемой смеси.
Изменение пластичности может быть также обусловлено процессами гидратации, образованием центров кристаллизации дигидрата, что проводит к изменению зернового состава и удельной поверхности твердых фаз.
Для определения влияния продолжительности обработки на бегунах при введении активатора были приготовлены смеси, состоящие из ФПГ с влажностью 20,9 % и пыли электрофильтров цементных мельниц ВАЗ. Расход пыли принят равным 3 % массы сухого ФПГ. Давление при прессовании изменялось. Результаты испытаний образцов после прессования приведены в таблице 3.11.
Таблица 3.11 - Зависимость прочности гранул от продолжительности механохимической активации и максимального давления при прессовании
Давление |
Прочность гранул, МПа при времени обработки на |
||||||||
|
|
|
бегунах, мин |
|
|
|
|||
прессования, МПа |
|
|
|
|
|
|
|||
|
|
|
|
|
|
|
|
||
1 |
3 |
5 |
7 |
10 |
15 |
20 |
30 |
||
|
|||||||||
|
|
|
|
|
|
|
|
|
|
5 |
0,5 |
0,8 |
1,2 |
1,1 |
1,1 |
1,0 |
0,9 |
0,8 |
|
|
|
|
|
|
|
|
|
|
|
10 |
1,0 |
1,1 |
1,5 |
2,3 |
2,2 |
2,0 |
1,9 |
1,7 |
|
|
|
|
|
|
|
|
|
|
|
20 |
2,1 |
2,8 |
3,1 |
3,7 |
4,2 |
4,0 |
3,6 |
2,6 |
|
|
|
|
|
|
|
|
|
|
|
30 |
2,6 |
3,0 |
3,9 |
4,1 |
4,6 |
4,9 |
4,2 |
3,6 |
|
|
|
|
|
|
|
|
|
|
Из таблицы 3.11 следует, что введение цементной пыли в качестве активатора, обработка смеси на бегунах, с последующим прессованием, позволяют получить окускованный продукт с пределом прочности при сжатии от 1 до 4 МПа, пригодный для погрузки и транспортировки (более 1 МПа).
При введении активатора в сочетании с обработкой на бегунах процессы гидратации активированного фосфополугидрата заканчиваются через 5− 7 ч после обработки. Поэтому следует предусмотреть хранение гранул на складе перед их отгрузкой на цементные заводы. В этих условиях скорость
64
превращения полуводного сульфата кальция в дигидрат и скорость процессов твердения будут зависеть от условий хранения гранул, т. е. от температуры и относительной влажности воздуха. Поэтому исследовано влияние относительной влажности среды на скорость гидратации фосфополугидрата. С этой целью гранулы, полученные прессованием при давлении 10 МПа, хранились в эксикаторах над водными растворами серной кислоты различной концентрации и дистиллированной водой, т. е. в атмосфере с относительной влажностью — 40 %, 60 %, 100 %. Через определенные промежутки времени в течение 10 сут определяли скорость гидратации фосфополугидрата установлено, что с понижением относительной влажности среды скорость гидратации попутного продукта замедляется. На основании полученных данных было рекомендовано при хранении гранул на складе поддерживать относительную влажность воздуха не менее 60 %. В производственных условиях возможно хранение гранул на открытых площадках и их увлажнение дождевой водой. В связи с этим образцы хранились как на воздухе, так и в воде при температуре 20 ° С. Через 12 месяцев хранения в воде прочность образцов понизилась на 10− 15 % по сравнению с первоначальной. При хранении на воздухе прочность гранул практически не изменялась.
На основании результатов лабораторных исследований проведено гранулирование фосфополугидрата методом прессования жестких смесей на Павловском заводе силикатных строительных материалов.
Грануляция фосфополугидрата на Павловском заводе силикатных строительных материалов
Для проведения исследований был отобран фосфополугидрат с карусельного фильтра ВАЗ в количестве 1,0− 1,2 т. Влажность пробы составила 28,5 %. Фосфополугидрат доставлен на Павловский завод силикатных строительных материалов (ССМ) в закрытых полиэтиленовых мешках. Формовочную смесь, состоящую из влажного ФПГ и пыли электрофильтров,
65
взятой в количестве 3 % массы сухого фосфополугидрата, обрабатывали на бегунах в течение 10 мин. Прессование проведено на прессе СМ-481, используемом для получения силикатного кирпича. Давление при прессовании составило 20 МПа. При прессовании получены образцы размером
250×120×65 мм (кирпич).
Испытания образцов проведено по методике, стандартной для
силикатного кирпича. |
|
||
Техническая характеристика образцов приведена ниже: |
|
||
а) |
прочность при сжатии, МПа: |
|
|
|
1) |
через 5 мин после прессования .................................... |
0,6− 0,7; |
|
2) |
после 24 ч хранения на воздухе ................................... |
12,0−16,0. |
б) содержание химически связанной воды, %: |
|
||
|
1) |
через 5 мин после прессования .................................... |
10,2 |
|
2) |
после 24 ч хранения на воздухе ................................... |
17,5 |
в) |
влажность образцов, %: |
|
|
|
после 24 ч хранения на воздухе ........................................ |
8,5 |
Прочность при сжатии в раннем возрасте (через 5 мин после прессования образцов) превышает прочность силикатного кирпича-сырца в 1,5− 2 раза.
Влажность образцов через 24 часа хранения на воздухе составила 8,5 %, что позволяет исключить их сушку. Слеживания при хранении гранул на воздухе в течение 24 ч не наблюдалось.
Исследования, проведенные в лабораторных и опытно-промышленных условиях, показали, что предложенная технология может быть использована для производства из ФПГ как гранул, так и стеновых камней и блоков. Технологическая схема производства приведена на рисунке 3.15.
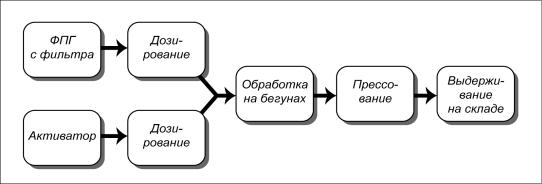
66
Рисунок 3.15 — Технологическая схема прессования ФПГ
3.4.2 Производство гранул методом пластического формования
Преимуществом метода пластического формования (на ленточном прессе) является более высокая производительность и надежность формовочного оборудования. Испытания показали, что для эффективной работы ленточного пресса необходимо, чтобы масса перед формованием имела пластическую прочность, равную приблизительно 0,07 МПа.
Влияние влажности формовочной смеси на её пластическую прочность
Определена зависимость пластической прочности формовочных смесей, состоящих из сухого фосфополугидрата ВАЗ, от В/Т. Расход воды изменяли с таким расчетом, чтобы получить смеси с влажностью 10, 20, 30, 40 и 50 %. Определение пластической прочности проведено с использованием конического пластометра МГУ. Результаты исследований приведены в таблице 3.12.
Таблица 3.12 Влияние влажности смеси на ее пластическую прочность
Влажность, % |
10 |
20 |
30 |
40 |
50 |
|
|
|
|
|
|
Пластическая |
|
|
|
|
|
прочность, |
0,013 |
0,015 |
0,016 |
0,020 |
0,010 |
МПа |
|
|
|
|
|
|
|
|
|
|
|
67
С повышением влажности смеси её пластическая прочность сначала растет, а затем начинает снижаться. Рост пластической прочности связан с адсорбцией воды и слипанием зерен твердых фаз (жидкостное прилипание, по Б. В. Дерягину). После достижения оптимума появляется свободная вода, что приводит к снижению пластической прочности смеси. Из таблицы 3.12 также следует, что пластическая прочность исследованных смесей при изменении их влажности от 10 до 30 % (т. е. в пределах, характерных для фосфополугидрата ВАЗ) значительно ниже, чем у промышленных керамических масс.
В лабораторных и опытно-промышленных условиях при формовании смесей с влажностью от 10 до 40 % после прохождения мундштука пресса масса рассыпалась (т. е. не обладала необходимой связностью). С повышением влажности (более 40 %) формовочная смесь становилась текучей.
Как было отмечено ранее, недостаточная связность и низкая пластическая прочность формовочных смесей обусловлена особенностями зернового состава попутного продукта ВАЗ, который является сравнительно грубодисперсным относительно монофракционным продуктом. Следовательно, формование гранул из фосфополугидрата ВАЗ невозможно без предварительной подготовки.
Известно, что при постоянном В/Т с увеличением дисперсности системы пластическая прочность формовочных смесей растет. С целью повышения пластической прочности и связности формовочных смесей нами вводилась добавка — пыль электрофильтров. Расход добавки изменяли в пределах от 5− 30 % от массы сухого фосфополугидрата. Ранее было установлено, что без механохимической активации введение добавки менее 5 % нецелесообразно. При изготовлении и испытании проб значения В/Т приняты равными 0,1; 0,2; 0,3; 0,4.
Исследования показали, что для получения формовочной массы с пластической прочностью 0,07 МПа необходимо ввести добавку-активатор в количестве 15− 17 % от массы сухого фосфополугидрата. Максимальная
68
пластическая прочность достигается при расходе добавки — 20 – 28 %. При этом формовочная смесь имеет достаточную связность. Водоотделения при испытании не наблюдалось. Содержание химически связанной воды через одни сутки хранения формовочной массы над водой повысилось от 6,6 до 10,5– 13,0 % в зависимости от значения В/Т смеси. Как было отмечено ранее, повышение содержания в гранулах добавки-активатора нежелательно в связи с уменьшением содержания в них сульфата кальция. С целью снижения расхода добавки-активатора при формовании гранул на ленточном прессе намиопределено влияние механохимической активации фосфополугидрата на пластическую прочность формовочной смеси.
Влияние механохимической активации на пластическую прочность формовочных смесей
Формовочную смесь, состоящую из сухого фосфополугидрата ВАЗ, пыли электрофильтров вращающихся печей и воды, обрабатывали на бегунах в течение 15 мин, т. к. при более длительной обработке начинается образование крупных агрегатов. Расход воды затворения был принят равным 20 % массы сухих твердых компонентов, что соответствует среднему значению влажности остатка на фильтре в условиях ВАЗ. Расход добавки-активатора был принят равным 3 % массы сухого попутного продукта. В процессе обработки, через определенные промежутки времени, были отобраны пробы и определена пластическая прочность формовочной смеси. В дальнейшем кювету со смесью хранили в эксикаторе над водой при температуре 20 ° С в течение 2 ч с целью определения изменения пластической прочности при хранении. Результаты испытаний приведены в таблице 3.13.
69
Таблица 3.13 - Влияние механохимической активации на пластическую прочность формовочных смесей
Продолжительность |
Пластическая прочность активированных смесей, |
|||||
|
МПа, после хранения, мин |
|
||||
активации, мин |
|
|
||||
|
|
|
|
|
||
0 |
30 |
60 |
90 |
120 |
||
|
||||||
|
|
|
|
|
|
|
0 |
0,015 |
0,016 |
0,019 |
0,022 |
0,025 |
|
|
|
|
|
|
|
|
3 |
0,032 |
0,040 |
0,051 |
0,065 |
0,072 |
|
|
|
|
|
|
|
|
5 |
0,050 |
0,068 |
0,075 |
0,096 |
0,134 |
|
|
|
|
|
|
|
|
7 |
0,060 |
0,380 |
2,0 |
– |
– |
|
|
|
|
|
|
|
Из таблицы 3.13 следует, что пластическая прочность формовочных смесей растет с увеличением продолжительности механохимической активации и хранения пробы. Варьируя время обработки смеси на бегунах, а также продолжительность последующего хранения, можно регулировать реологические свойства формовочной смеси и получить смеси, пригодные для формования на ленточном прессе. Например, пластическая прочность формовочной массы, равная 0,070–0,075 МПа, достигается через 8– 9 мин обработки смеси на бегунах, или после 5 мин обработки с последующим хранением смеси в течение 40– 50 мин. Это позволяет при производстве гранул методом пластического формования определить оптимальную продолжительность обработки на бегунах и последующего хранения с учетом минимальных затрат энергии.
Вусловиях ЛЗКИ выпущена опытная партия гранул из фосфополугидрата на ленточном прессе, предназначенном для формования керамзита-сырца.
Взаводских условиях получены гранулы со следующей характеристикой: а) пластическая прочность смеси, МПа:
1)перед формованием — 0,06;
2)через 2 мин после формования — 0,07;
б) прочность при сжатии (через 24 ч после формования), МПа — 10;