
6684
.pdf30
армируют стальной арматурой, которая воспринимает растягивающие напряжения. Совместной работе бетона и стальной арматуры способствует хорошее сцепление между ними и близость коэффициентов температурного расширения; бетон к тому же защищает арматуру от коррозии.
Железобетонные конструкции изготовляют с обычной и предварительно напряженной арматурой. Основная идея предварительного напряжения железобетонных конструкций заключается в том, что при изготовлении бетон искусственно обжимается. Благодаря этому бетон растягивается только тогда, когда будут преодолены созданные обжатием сжимающие напряжения. Если они превосходят растягивающие напряжения от нагрузки, то можно избежать образования трещин в растянутой зоне бетона.
Различают два основных вида железобетонных конструкций с предварительно напряжённой арматурой: конструкции с натяжением арматуры до бетонирования и конструкции с натяжением арматуры после бетонирования. В первом случае арматуру предварительно растягивают и концы её закрепляют. После затвердевания бетонной смеси концы арматуры освобождают (отрезают) и арматура, стремясь вернуться в первоначальное состояние, обжимает бетон. В конструкциях с натяжением арматуры после бетонирования, арматура, подлежащая натяжению, располагается в каналах, образованных в бетоне специальными пустотообразователями, и после натяжения анкеруется на концах, а каналы заполняются раствором.
Железобетонные конструкции подразделяют на сборные и монолитные. Сборные железобетонные конструкции монтируют на строительной площадке из отдельных элементов, изготовленных на заводах и полигонах. Монолитные железобетонные конструкции бетонируют на месте строительства.
Армирование железобетонных конструкций осуществляют отдельными стержнями, сетками, пространственными каркасами, проволокой. Наиболее употребительные виды арматурных сталей и их основные характеристики приведены в главе 10 первого раздела настоящего учебного пособия..
Бетонные смеси приготовляют в специальных бетоносмесительных установках - гравитационных или с принудительным смешиванием. Затем происходит процесс формования и уплотнения бетонной смеси. Основным способом уплотнения бетонных смесей является вибрирование. После этого отформованное изделие должно затвердеть и набрать определённую прочность. Различают естественное и искусственное твердение бетона. Искусственное твердение - это так называемая температурно-влажностная обработка (прогрев изделий при атмосферном давлении в паровоздушной среде с температурой 8085° С или выдерживание в среде насыщенного пара при 100° С), применяемая в заводских условиях.
Из сборного железобетона изготовляют все части здания: фундаменты, стены подвалов, наружные и внутренние стены, элементы каркаса и покрытий, междуэтажные перекрытия, лестницы и др.
Производство железобетонных и бетонных сборных конструкций может быть организовано двумя принципиально отличными способами: поточным в перемещаемых формах или на перемещаемых поддонах и стендовым в стационарных (неперемещаемых) формах.
При поточном способе все технологические операции (очистка и смазка форм, армирование, формование, твердение, распалубка) выполняются на специализированных постах, которые оборудованы стационарными машинами
31
и установками, образующими поточную технологическую линию. Формы с изделиями последовательно перемещаются по технологической линии от поста к посту.
При стендовом способе производства в отличие от поточного и конвейерного, сборные конструкции изготовляют в стационарных формах. Изделия в процессе их изготовления и до затвердевания бетона остаются на месте, в то время как технологическое оборудование для выполнения отдельных операций последовательно перемещается от одной формы к другой.
6.РАСТВОРЫ
6.1.Общие сведения и классификация
Строительный раствор - это искусственный каменный материал, полученный в результате затвердевания растворной смеси, состоящей из вяжущего вещества, воды, мелкого заполнителя и добавок, улучшающих свойства смеси и растворов. Крупный заполнитель отсутствует, так как раствор применяют в виде тонких слоев (шов каменной кладки, штукатурка и т.п.).
Строительные растворы разделяют в зависимости от вида вяжущего вещества, величины плотности и назначения.
По виду вяжущего различают растворы простые: цементные, известковые, гипсовые и сложные: цементно-известковые, цементно-глиняные, известковогипсовые и др.
По плотности различают: тяжелые растворы плотностью 1500кг/м3 и более, изготовляемые обычно на кварцевом песке, и легкие растворы плотностью менее 1500 кг/м3, изготовляемые на пористом мелком заполнителе и с порообразующими добавками.
По назначению строительные растворы различают: на кладочные - для каменной кладки и монтажа крупнокаменных и крупноблочных стен; облицовочные - для устройства облицовок; штукатурные - для оштукатуривания поверхностей зданий и сооружений; специальные - декоративные, гидроизоляционные, тампонажные и др.
6.2. Свойства растворной смеси и раствора
Подвижность растворных смесей характеризуется глубиной погружения металлического конуса стандартного прибора. Подвижность назначают в зависимости от вида раствора и отсасывающей способности основания.
Водоудерживающая способность - это свойство растворной смеси сохранять воду при укладке на пористое основание, что необходимо для сохранения подвижности смеси, предотвращения расслоения и хорошего сцепления раствора с пористым основанием.
Прочность при сжатии определяют испытанием образцов-кубиков с длиной ребра 7,07 см в возрасте, установленном в стандарте или технических условиях на данный вид раствора. Строительные растворы по прочности в 28-суточном возрасте при сжатии делят на марки: 4, 10, 25, 50, 75, 100, 150, 200,
300.
Морозостойкость раствора характеризуется числом циклов попе-
32
ременного замораживания и оттаивания, которое выдерживают насыщенные водой стандартные образцы-кубики размером 7,07x7,07x7,07см. Строительные растворы для каменной кладки наружных стен и наружной штукатурки имеют марки по морозостойкости: F10, F15, F25, F35, F50, F75, F100, F150, F200.
6.3. Виды строительных растворов
Кладочные растворы применяются для каменной кладки наружных стен зданий. Изготавливаются главным образом цементные и сложные растворы на смешанном вяжущем (цементно-известковые и цементно-глиняные) различных марок в зависимости от влажностных условий и требуемой долговечности здания. В кладке перемычек, простенков, карнизов, столбов марка может быть повышена.
Штукатурные растворы. Для наружных каменных и бетонных стен зданий применяют цементно-известковые растворы. Внутреннюю штукатурку стен и покрытий здания при относительной влажности воздуха помещений до 60% выполняют из известковых, гипсовых, известково-гипсовых и цементноизвестковых растворов.
Декоративные растворы предназначены для отделочных слоев стеновых панелей и блоков, наружной и внутренней отделки зданий. Эти растворы изготовляют на белом, цветном и обычном портландцементах; для цветных штукатурок внутри зданий применяют также строительный гипс и известь.
Гидроизоляционные растворы применяются для гидроизоляционных слоев и штукатурок и изготовляют, применяя портландцемент, расширяющиеся цементы, сульфатостойкий портландцемент.
Инъекционные цементные растворы применяют для заполнения каналов в предварительно напряженных конструкциях и уплотнения бетона.
Сухие строительные смеси - это композиции заводского изготовления на основе минеральных вяжущих веществ, включающие заполнители и добавки. В отдельных случаях в качестве вяжущего могут быть использованы водорастворимые или водоэмульгируемые полимеры. На место производства строительных работ сухие смеси доставляются в расфасованном виде, причем для их использования по назначению достаточно только добавить необходимое количество воды.
Сухие смеси по сравнению с товарными смесями имеют ряд преимуществ: сокращение количества технологических операций для перевода сухих смесей в рабочее состояние; повышение качества строительных работ благодаря заводскому приготовлению смесей; сокращение транспортных расходов; сокращение отходов растворов; повышение производительности труда.
В настоящее время сухие смеси применяют в качестве кладочных, отделочных и штукатурных растворов, шпатлевок, плиточных клеев, составов для наливных полов, ремонтных составов.
Технология производства сухих смесей складывается из следующих технологических операций: поступающий с карьера песок подвергается тепловой
33
обработке в сушильных агрегатах, где его влажность доводят до 0,5%, затем производят рассев на ситах до нужных фракций (как правило, применяется песок с крупностью зёрен 0,16 - 1,25мм). Просеянный песок после дозирования направляется в смеситель принудительного действия. В этот же смеситель загружают и другие компоненты в необходимом количестве. Отдозированные материалы перемешивают до получения однородной массы. Полученную смесь затаривают в емкости, необходимые для реализации, и подают на склад готовой продукции. Смеси хранят в сухом месте, а модифицированные полимерами - при температуре не выше 40° С.
7. ИСКУССТВЕННЫЕ КАМЕННЫЕ МАТЕРИАЛЫ И ИЗДЕЛИЯ НА ОСНОВЕ НЕОРГАНИЧЕСКИХ ВЯЖУЩИХ ВЕЩЕСТВ
Искусственные каменные материалы и изделия на основе вяжущих веществ получают необходимую прочность в результате затвердевания вяжущих, в отличие от керамических материалов, которые переходят в камневидное состояние только после обжига. Они разделяются на изделия на основе гипса, извести, портландцемента.
7.1. Материалы на основе гипса
Изделия на основе гипсовых вяжущих имеют ряд значительных преимуществ по сравнению с изделиями на основе других вяжущих. Быстрое твердение гипса и высокие его формовочные свойства дают возможность сократить технологический процесс производства гипсовых изделий, повысить оборачиваемость форм и снижают стоимость строительства. При сравнительно малой плотности гипсовые изделия имеют достаточную прочность, низкую теплопроводность и высокую звукоизоляцию; они легко поддаются механической обработке и окрашиваются в различные цвета.
Наряду с перечисленными выше преимуществами изделия на основе гипса имеют и существенный недостаток - низкую водостойкость, при увлажнении значительно снижается прочность гипсовых изделий, а также наблюдается явление ползучести (увеличение пластических деформаций при неизменной нагрузке), поэтому их можно применять только в сухих помещениях или надежно защищать от увлажнения.
По назначению гипсовые и гипсобетонные изделия разделяют на следующие группы: плиты и панели для перегородок; гипсокартонные листы для облицовки стен (гипсовая сухая штукатурка); стеновые камни; теплоизоляционные изделия; архитектурно-декоративные детали (карнизы, потолочные розетки, плафоны, фризы и др.).
34
Плиты для перегородок. Изготовляют такие плиты из гипсового теста (гипсовые) либо из гипсового раствора и бетона с минеральными или органическими заполнителями (гипсобетонные). Производство плит состоит из следующих операций: дозирование сырьевых материалов - гипса, заполнителей, воды и добавок; перемешивания смеси; формования и высушивания плит.
Гипсоволокнистые листы изготовляют из смеси гипса, воды и волокнистых заполнителей (бумажной макулатуры, отходов текстильной промышленности и др.). Гипсоволокнистые листы хорошо пилятся и легко поддаются гвоздимости. Такие изделия выпускают размерами 3000x1200 мм и 2500x600 мм, толщиной 50 мм и плотностью 800-1100 кг/м3.
Гипсокартонные листы представляют собой листовой отделочный материал, состоящий из тонкого слоя затвердевшего гипса, покрытого с обеих сторон картоном и прочно соединенного с ним. Картон выполняет как отделочную роль, так и армирующую, повышая прочность гипсового изделия при изгибе.
Гипсовые обшивочные листы применяют для отделки внутренних поверхностей помещений - стен, потолков и перегородок. Использовать их можно только в помещениях с нормальной относительной влажностью воздуха (до 60%), а в санитарных узлах - лишь при условии надежной защиты от увлажнения. Применение гипсовых листовых отделочных материалов упрощает и ускоряет отделочные работы, поскольку крепление листов к стенам и перегородкам - менее сложный процесс, чем оштукатуривание тех же поверхностей; кроме того, не нужно тратить время на ее сушку.
7.2. Материалы на основе извести (силикатные изделия)
Производство силикатных строительных материалов базируется на гидротермальном синтезе гидросиликатов кальция, который осуществляется в реакторе-автоклаве в среде насыщенного водяного пара давлением 0,8-1,3 МПа и температурой 175-200° С. Силикатные автоклавные материалы - это материалы, приготовленные из сырьевой смеси, содержащей известь (гашёную или молотую негашеную), кварцевый песок и воду, которые образуют в процессе автоклавной обработки гидросиликаты кальция
Са(ОН)2 + SiО2 + mН2О = СаО·SiО2·nН2О.
Автоклав представляет собой горизонтально расположенный стальной цилиндр с герметически закрывающимися с торцов крышками. Диаметр автоклава 2,6-3,6м, длина 21-30м. В нижней части автоклава уложены рельсы, по которым передвигаются загруженные в автоклав вагонетки с изделиями. Схема автоклава для производства силикатных материалов
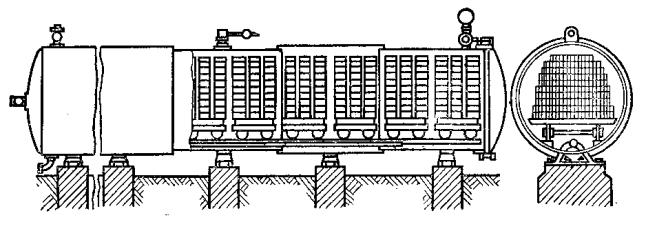
35
представлена на рис. 8.
Рис. 8. Автоклав для производства силикатных изделий
Силикатный кирпич изготовляется из смеси кварцевого песка (92-94%), извести (6-8%) и воды (7-9%) путем прессования под давлением (15-20 МПа) и последующего твердения в автоклаве.
Цвет силикатного может быть любым за счёт введения в состав смеси щелочестойких пигментов. Выпускают кирпич двух видов: одинарный 250x120x65 мм и утолщённый 250x120x88мм. Утолщённый кирпич изготовляют с пустотами, чтобы масса одного кирпича не превышала 4,3 кг. В зависимости от предела прочности при сжатии и изгибе силикатный кирпич имеет марки: 75, 100, 125, 150, 175, 200, 250 и 300.
Силикатный кирпич применяют для несущих стен зданий. Не рекомендуется его применять для цоколей зданий из-за недостаточной водостойкости. Для кладки труб и печей силикатный кирпич не используют, так как при высокой температуре дегидратируется Са(ОН)2, а зерна кварцевого песка при 600° С расширяются и вызывают растрескивание кирпича.
Схема производства силикатного кирпича состоит из следующих основных операций. Комовую известь, поступающую из известеобжигательной печи, дробят и размалывают в тонкий порошок. Гасить известь в смеси с песком можно в силосах в течение 8-9 ч (первый способ) или, что гораздо быстрее и интенсивнее, в специальных гасильных барабанах (второй способ). Прессуют кирпич на прессах под давлением до 15-20 МПа. Применяемые на заводах прессы имеют периодически вращающийся стол с устроенными в нем формами. Спрессованный кирпич-сырец получает высокую плотность, что способствует более полному прохождению реакции между известью и кварцевым песком. Отформованные кирпичи снимают со стола пресса, осторожно укладывают на вагонетки и отправляют в автоклавы для твердения.
Силикатные бетоны могут быть тяжелыми (заполнитель - песок и щебень), лёгкими (заполнители– керамзит, вспученный перлит, аглопорит, и др.). В силикатном бетоне применяют известково-кремнеземистое вяжущее, в состав которого входят воздушная известь и тонкомолотый кварцевый песок. В процессе автоклавизации между всеми компонентами бетона протекают
36
химические взаимодействия. Силикатный бетон применяют для изготовления сборных бетонных и железобетонных конструкций, в том числе предварительно напряженных
Пеносиликат - это искусственный каменный материал ячеистой структуры, который получается в результате затвердевания пластичной известково-песчаной смеси, смешанной с технической пеной. Материал, полученный смешиванием того же раствора с газообразователем (алюминиевой пудрой, пергидролем и др.), называют газосиликатом.
Из теплоизоляционного пеносиликата и газосиликата изготовляют плиты, полуцилиндры и короба - для ограждения теплопроводов и другие теплоизоляционные изделия.
7.3. Материалы на основе цемента
Асбоцемент - искусственный композиционный каменный строительный материал, получаемый в результате затвердевания смеси, состоящей из цемента, асбеста (10-20% от массы цемента) и воды. Такой материал обладает высокой прочностью, огнестойкостью, долговечностью, малыми водонепроницаемостью, теплопроводностью и электропроводностью.
Асбестом называют природный тонковолокнистый минерал, состоящий из водных или безводных силикатов магния, а некоторые разновидности - из силикатов кальция и натрия. 95% мировой добычи асбеста составляет хризотил - асбест (3MgO·2SiО2·2H2O), который и применяется для производства асбестоцементных изделий. Диаметр волокон асбеста 1 мкм, однако при гидромеханической обработке асбестовый камень расщепляется до среднего диаметра волокон 20 мкм. Хризотил-асбест имеет очень высокую прочность при растяжении вдоль волокнистости. Введение гибких волокон в качестве армирующего компонента в цемент (10-20%) позволяет в 3-5 раз увеличить прочность цементного камня при растяжении и изгибе, а также стойкость к ударным воздействиям.
Способы производства асбестоцементных изделий в зависимости от количества воды, которое используется при их изготовлении, подразделяются на: мокрый, полусухой и сухой. Сущность формования изделий для любого способа производства состоит в отфильтровывании воды из асбестоцементной массы до необходимого уплотнения и придания ей заданных формы и размеров на специальной формовочной машине, представленной на рис.9.

37
Рис. 9. Схема формовочной машины для производства асбестоцементных изделий: 1 - металлическая ванна; 2 - желоб подачи асбестоцементной массы; 3 - лента конвейера; 4 – прижимной вал; 5 - слой асбестоцементной массы; 6 – вакуум-коробка;
7 - форматный барабан; 8 - ведущий вал; 9 - натяжной валик; 10 - барабан, обтянутый металлической сеткой
Твердение асбестоцементных изделий, как правило, осуществляется в две стадии: предварительное твердение до набора прочности, обеспечивающей дальнейшее бездефектное внутризаводское транспортирование, и окончательное.
Предварительное твердение изделий, после выдержки при нормальных условиях в течение 6-8 часов, осуществляется в пропарочных камерах при температуре 50-60° С в течение 12-16 часов. Окончательное твердение изделий на песчаном цементе производится в автоклавах при давлении пара 0,8 МПа и температуре 172-174° С в течение 12-16 часов. Основные виды асбестоцементных изделий включают: кровельные, стеновые, декоративные, погонажные трубы и специальные.
8.СТРОИТЕЛЬНЫЕ МАТЕРИАЛЫ ИЗ ДРЕВЕСИНЫ
8.1.Общие сведения, состав, строение и свойства древесины
Древесина является одним из самых распространенных строительных материалов с многовековым опытом применения. Потребность в лесоматериалах удовлетворяется путем комплексной и глубокой переработки древесины. Высокая прочность и упругость древесины сочетаются с малой плотностью, а следовательно, с низкой теплопроводностью. Древесина морозостойка, не растворяется в воде и органических растворителях. Хорошо известна легкость обработки древесины, удобство скрепления деревянных элементов с помощью клея, врубок, гвоздей и пр. Вместе с тем древесина имеет ряд недостатков, ограничивающих область ее применения в строительстве: анизотропию свойств, вследствие волокнистой структуры; пороки структуры;
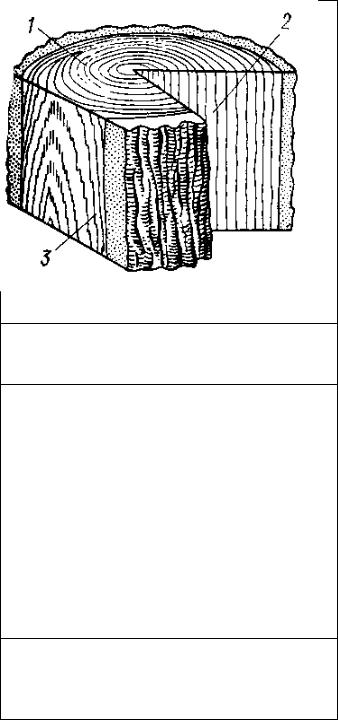
38
гигроскопичность и, как следствие, влажностные деформации; загниваемость и горючесть.
Наряду с такими традиционными материалами, как круглый лес, доски, брусья, шпалы и т.п., все шире применяют клееные деревянные конструкции и разнообразные изделия, получаемые из отходов лесообработки.
Древесные породы подразделяются на две основные группы: хвойные и лиственные. К хвойным породам, широко используемым в строительстве, относят сосну, лиственницу, ель, пихту и кедр. Лиственные породы в строительстве используют значительно реже, чем хвойные. Среди многообразия лиственных пород наибольшее применение в строительстве имеют дуб, ясень, бук, береза, осина.
Растущее дерево состоит из корневой системы, ствола и кроны. Промышленное значение имеет ствол, так как из него получается от 60% до 90% древесины.
Обычно изучают три основных разреза ствола: поперечный (торцовый) (1), радиальный (2), проходящий через ось ствола, и тангенциальный (3), проходящий по хорде вдоль ствола (рис. 10). При рассмотрении поперечного разреза ствола дерева можно различить следующие основные его части: сердцевину, кору, камбий и древесину (рис. 11).
Сердцевина состоит из клеток с тонкими стенками, слабо связанных друг с другом. Эта часть ствола дерева легко загнивает и имеет малую прочность.
Кора защищает дерево от вредных влияний среды и механических
повреждений. Луб проводит питательные вещества от кроны в ствол и корни Под лубяным слоем располагается тонкий кольцевой слой живых клеток -
39
камбий. Ежегодно в вегетативный период камбий откладывает в сторону коры клетки луба и внутрь ствола, в значительно большем объеме - клетки древесины, поэтому древесина ствола (часть ствола от луба до сердцевины) в поперечном разрезе состоит из ряда концентрических, так называемых, годичных колец, располагающихся вокруг сердцевины. В процессе роста дерева стенки клеток древесины внутренней части ствола, примыкающей к сердцевине, постепенно изменяют свой состав и пропитываются у хвойных пород смолой, а у лиственных - дубильными веществами, и она становится более прозрачной, твердой и менее способной к загниванию. Эту часть ствола, состоящую из мертвых клеток, называют у некоторых пород ядром, у других - спелой древесиной.
Истинная плотность древесины изменяется незначительно, так как древесина всех деревьев состоит в основном из одного и того же вещества - целлюлозы. В связи с этим истинную плотность древесины можно принять равной 1,54 г/см3.
Влажность выражают обычно в % по отношению к массе сухой древесины. В древесине различают гигроскопическую влагу, связанную в стенках клеток, и капиллярную влагу, которая свободно заполняет полости клеток и межклеточное пространство.
Усушка, разбухание и коробление. Колебания влажности волокон древесины влекут за собой изменение размеров и формы изделий из древесины. Усушка и разбухание древесины вызывают коробление и растрескивание лесных материалов. Коробление деревянных изделий является следствием разницы в усушке древесины в тангенциальном и радиальном направлениях и неравномерности высыхания. Неравномерность усушки и коробление вызывают появление внутренних напряжений в древесине и растрескивание пиломатериалов.
Текстура - это рисунок древесины, зависящий от сочетания ее видимых элементов: годовых слоев, сердцевинных лучей, сосудов. Цвет и текстура древесины характерны для каждой породы дерева.
Прочность древесины определяют путем испытания малых, чистых (без видимых пороков) образцов древесины. Прочность древесины характеризуется пределами ее прочности при сжатии, растяжении, статическом изгибе, скалывании..
Пороки древесины - возникают в процессе роста дерева и подразделяются на: сучки, трещины, сбежистостъ ствола (уменьшение диаметра круглых лесоматериалов от толстого к тонкому концу), кривизна (искривление продольной оси бревен), грибковые поражения и др.