
6684
.pdf
20
схватывания не нормируется). Для гипсовых вяжущих стандартом установлено
12 марок по прочности: Г-2, Г-3, Г-4, Г-5, Г-6, Г-7, Г-10, Г-13, Г-16, Г-19, Г-22,
Г-25.
Высокообжиговые гипсовые вяжущие вещества производят путем обжига гипсового камня при высоких температурах (600-900° С), поэтому они состоят преимущественно из ангидрида CaSO4, который частично подвергается термической диссоциации с образованием СаО. Небольшое количество оксида кальция в составе вяжущего играет роль активизатора взаимодействия вяжущего с водой. Высокообжиговый гипс (в отличие от строительного гипса) медленно схватывается и твердеет, но его водостойкость и прочность при сжатии выше.
При твердении строительного гипса происходит химическая реакция присоединения воды и образования двуводного сульфата кальция:
CaSO4·0,5H2O+1,5H2O = CaSO4·2H2O. |
|
|||||
Подробнее |
о |
|
методах |
|
||
определения |
свойств |
гипсового |
|
|||
вяжущего см. главу 2 второго раздела |
|
|||||
настоящего пособия. |
|
|
|
|||
Воздушная |
известь |
- |
продукт |
|
||
умеренного |
обжига |
кальциево- |
|
|||
магниевых |
карбонатных |
|
горных |
|
||
пород: мела, известняка, доломи- |
|
|||||
тизированного известняка, доломита. |
|
|||||
Основной составляющей |
известняка |
|
||||
является карбонат кальция (СаСО3). |
|
|||||
Обжигают известняк при температуре |
|
|||||
900-1200° С |
до |
возможно |
более |
|
||
полного удаления СО2 по реакции: |
|
|||||
СаСО3 = СаО + СО2 ↑. |
|
|
||||
Продукт обжига содержит, кроме |
|
|||||
СаО (основной составной части), |
|
|||||
также и некоторое количество оксида |
|
|||||
магния, образовавшегося в результате |
Рис. 4. Шахтная печь: 1 - шахта печи; |
|||||
термической |
диссоциации |
карбоната |
||||
2 - загрузочный механизм; 3 - зона |
||||||
магния, частично содержащегося в |
подогрева; 4 - зона обжига; 5- зона |
|||||
сырье: |
|
|
|
|
охлаждения; |
|
MgCO3 = MgO + СО2↑. |
6 - гребень; 7 - разгрузочный механизм |
|||||
Чем выше содержание основных |
|
оксидов (СаО + MgO) в извести, тем пластичнее известковое тесто и тем выше
21
ее сорт. Обжиг известняка чаще всего производят в шахтных печах (рис. 4), в которые известняк поступает в виде кусков размером 8-20 см. При обжиге известняка удаляется углекислый газ, составляющий 44% от массы СаСОз, поэтому комовая негашеная известь получается в виде пористых кусков, активно взаимодействующих с водой при гашении.
Гашение воздушной извести заключается в гидратации оксида кальция при действии воды на комовую негашеную известь:
СаО + Н2О = Са(ОН)2.
Гашение сопровождается разогревом массы вследствие выделения значительного количества тепла - 950 кДж/кг. В процессе гашения куски негашеной извести самопроизвольно диспергируются, распадаясь на тонкие частицы Са(ОН)2. Высокая удельная поверхность частиц Са(ОН)2 обуславливает большую водоудерживающую способность и пластичность известкового теста.
Гашение комовой извести в тесто на заводах производят в специализированных известегасильных машинах. В зависимости от количества воды, добавляемой к комовой извести, можно получить известковое тесто или гидратную известь (пушонку). Гашение извести в пушонку осуществляют в гидраторах непрерывного действия, в которых выделяющееся тепло и водяные пары используются для превращения комовой извести в тончайший порошок с насыпной плотностью 400-450 кг/м3. При гашении в пушонку известь увеличивается в объеме в 2-3,5 раза; в большей степени "распушивается" высокоактивная известь с высоким содержанием СаО.
На воздухе известковый раствор постепенно отвердевает под влиянием двух одновременно протекающих процессов: высыхание раствора, сближение кристаллов Са(ОН)2 и их срастание; карбонизация извести под действием углекислого газа, который в небольшом количестве содержится в воздухе:
Са(ОН)2 + СО2 = СаСОз + Н2О.
Молотую негашеную известь получают путем тонкого размола комовой извести без предварительного гашения. Строительные растворы и бетоны, приготовленные на молотой негашеной извести, быстро схватываются и отвердевают вследствие гидратационного твердения негашеной извести. При правильно подобранном водоизвестковом отношении (0,9-1,5) кристаллы гидроксида кальция, получившиеся при гидратации оксида кальция непосредственно в материале (СаО·Н2О), срастаются между собой и быстро образуют прочный кристаллический сросток.
4.3.Гидравлические вяжущие вещества
Кгидравлическим вяжущим принадлежат гидравлическая известь, романцемент, портландцемент и его разновидности. Свойства указанных вяжущих веществ зависят от гидравлического модуля и температуры обжига сырья. Гидравлический модуль m выражает содержание основного оксида СаО
22
по отношению к суммарному количеству оксидов:
m = |
|
%CaO |
(11) |
|
%SiO2 |
+ % AI 2 O 3 +%Fe2 O3 |
|||
|
|
Для каждого вяжущего вещества характерен свой гидравлический модуль. У гидравлической извести m=1,7-9; у романцемента m<1,7, у портландцемента
m=1,9-2,4.
Гидравлическую известь получают из мергелистых известняков, содержащих 6-20% глины путём обжига в шахтных печах при температуре 9001100° С не допуская при этом спекания. Полученную известь размалывают и применяют в виде порошка либо гасят в пушонку. Гидравлическая известь начинает твердеть на воздухе (первые 7 сут.) и продолжает твердеть и увеличивать свою прочность в воде. Предел прочности при сжатии после 28 суток комбинированного хранения образцов из раствора из извести и песка 1:3 по массе (7 суток во влажном воздухе и 21 сутки в воде) составляет 2-5 МПа. Гидравлическую известь применяют для изготовления строительных растворов, бетонов низких марок и бетонных камней.
Романцемент - гидравлическое вяжущее вещество, получаемое тонким помолом обожженных не до спекания (900° С) известняковых или магнезиальных мергелей, содержащих более 20% глины. Образующиеся при обжиге низкоосновные силикаты и алюминаты кальция придают романцементу свойство твердеть и сохранять прочность в воде. Романцемент выпускают трех марок: М25, М50 и Ml00. Он применяется для изготовления строительных растворов, бетонов, бетонных камней.
Портландцементом называют гидравлическое вяжущее вещество, в составе которого преобладают силикаты кальция (70-80%). В среднем на 1 т цемента расходуется около 1,5 т минерального сырья. Портландцемент - продукт тонкого измельчения клинкера с добавкой гипса (3-5%). Клинкер представляет собой зернистый материал ("горошек"), полученный обжигом до спекания (при 1450° С) сырьевой смеси, состоящей в основном из углекислого кальция (известняки различного вида) и алюмосиликатов (глины, мергеля, доменного шлака и др.). Небольшая добавка гипсового камня регулирует сроки схватывания портландцемента.
Производство портландцемента включает в себя: добычу в карьере и доставку на завод сырьевых материалов - известняка и глины; приготовление сырьевой смеси; обжиг сырьевой смеси до спекания - получение клинкера; помол клинкера с добавкой гипса - получение портландцемента.
Приготовление сырьевой массы состоит в тонком измельчении и смешении взятых в установленном соотношении компонентов, что обеспечивает полноту прохождения химических реакций между ними и однородность клинкера. Приготовление сырьевой смеси осуществляется сухим, мокрым или комбинированным способами.
Сухой способ заключается в измельчении и смешении сухих (или предварительно высушенных) сырьевых материалов, поэтому сырьевая смесь получается в виде минерального порошка, называемого сырьевой мукой.
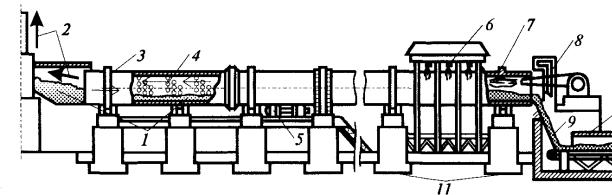
23
Тонкое совместное измельчение известняка и глины осуществляют в трубных (шаровых) мельницах, в которых совмещаются помол и сушка сырьевых материалов до остаточной влажности 1-2%. Сырьевую муку направляют в силосы, в них корректируется состав сырья и создается запас, необходимый для бесперебойной работы печей. Данный способ менее энергоёмкий.
Мокрый способ приготовления сырьевой смеси применяют, если сырье имеет значительную влажность (мел, глины). Тонкое измельчение и смешение исходных материалов осуществляется в водной среде, поэтому сырьевая смесь получается в виде жидко-текучей массы - шлама с большим содержанием воды (35-45%). Из трубных мельниц, где производится совместное измельчение известняка и глины, известково-глиняный шлам перекачивают насосами в вертикальные или горизонтальные резервуары (шламбассейны), в них корректируют и усредняют химический состав шлама.
Обжиг сырьевой смеси как при сухом, так и при мокром способе производства осуществляется в основном во вращающихся печах (рис. 5).
Рис. 5. Схема вращающейся печи: 1 - сырьевая шихта; 2 - горячие газы; 3 - вращающаяся печь; 4 - цепные завесы, улучшающие теплообмен; 5 - привод; 6 - водяное
охлаждение зоны спекания печи; 7 - факел; 8 – форсунка для подачи топлива; 9 - клинкер; 10 - холодильник; 11 - опоры
Вращающаяся печь представляет собой длинный, расположенный слегка наклонно цилиндр (барабан), сваренный из листовой стали с огнеупорной футеровкой внутри. Длина печей 95 - 230 м, диаметр 5 -7 м.
Вращающиеся печи работают по принципу противотока. Сырье в виде порошка (сухой способ) или в виде шлама (мокрый способ) подается автоматическим питателем в печь со стороны ее верхнего (холодного) конца, а со стороны нижнего (горячего) конца вдувается топливо (природный газ, мазут, воздушно-угольная смесь), сгорающее в виде факела на протяжении 20-30 м длины печи. Горячие газы поступают навстречу сырью. Сырье занимает только часть печи по поперечному сечению, и при ее вращении со скоростью 1- 2об/мин медленно движется к нижнему разгрузочному концу. Цементный клинкер выходит из вращающейся печи в виде мелких камнеподобных зеренгранул («горошка»), интенсивно охлаждается с 1000° С до 100-200° С, после чего выдерживается на складе 1-2 недели.
Помол клинкера в тонкий порошок производится преимущественно в

24
трубных (шаровых) мельницах. Трубная мельница представляет собой стальной барабан длиной до 16м и диаметром до 4м, облицованный внутри стальными броневыми плитами и разделенный дырчатыми перегородками на 2-4 камеры. Материал в трубных мельницах измельчается под действием загруженных в барабан мелющих тел - стальных шаров (в камерах грубого помола) и цилиндров (в камерах тонкого помола). При вращении мельницы мелющие тела поднимаются на некоторую высоту и падают, дробя и истирая зерна материала.
Готовый портландцемент - очень тонкий порошок темно-серого или зеленовато-серого цвета; по выходе из мельницы он имеет высокую температуру (80-120° С) и направляется пневматическим транспортом для хранения в силосы, которые обычно выполняются в виде железобетонных банок диаметром 8-15 м и высотой 25-30 м, где выдерживается до его охлаждения и гашения остатков свободного оксида кальция.
Качество клинкера определяет все свойства портландцемента, добавки же, вводимые в цемент, лишь регулируют его свойства. Качество клинкера зависит от его химического и минерального состава, тщательности подбора сырьевой смеси, условий проведения ее обжига и режима охлаждения получившегося клинкера.
Химический состав клинкера выражают содержанием оксидов (% по массе). Главными являются: СаО - 63-66%, SiO2 - 21-24%, Аl2О3 - 4-8% и Fe2O3
- 2-4%. Основными минералами клинкера являются: алит (3CaO·SiO2 или C3S); белит (2CaO·SiO2 или C2S), трехкальциевый алюминат (3CaO·Al2O3 или С3А) и четырехкальциевый алюмоферрит (4CaO· Al2O3·Fe2O3 или C4AF).
Цементное тесто, приготовленное |
|
||||||
путем смешивания цемента с водой, |
|
||||||
имеет три периода твердения. Вначале, |
|
||||||
в течение 1-3 ч после затворения |
|
||||||
цемента водой, оно пластично и легко |
|
||||||
формуется. |
|
Потом |
наступает |
|
|||
схватывание, заканчивающееся |
через |
|
|||||
5-10 ч после затворения; в это время |
|
||||||
цементное |
|
тесто |
загустевает, |
|
|||
утрачивая подвижность, но его |
|
||||||
механическая прочность еще невелика. |
|
||||||
Переход |
|
загустевшего |
цементного |
|
|||
теста в твердое состояние означает |
|
||||||
конец |
схватывания |
и |
начало |
|
|||
твердения, |
|
которое |
характерно |
|
|||
заметным |
|
возрастанием |
прочности. |
Рис. 6. Нарастание прочности минералов |
|||
Твердение |
цементного |
камня при |
|||||
благоприятных |
условиях |
длится |
клинкера портландцемента: |
||||
1 - C3S; 2 - C4AF; 3 - C2S; 4 - С3А. |
|||||||
годами - вплоть до полной гидратации |
|||||||
|
25
цемента.
Скорость набора прочности различными минералами цементного камня различна (рис. 6).
Портландцемент разделяют на марки по прочности 300, 400, 500, 550, 600. Подробнее технические характеристики портландцемента и методы их определения приведены в главе 1 второго раздела настоящего пособия.
При производстве тех или иных строительных работ необходимы цементы со специальными свойствами. Для получения портландцемента с заданными специальными свойствами используют следующие основные пути: регулирование минерального состава и структуры цементного клинкера, введение минеральных и органических добавок и регулирование тонкости помола и зернового состава цемента. К специальным видам цементов относятся: быстротвердеющий портландцемент (БТЦ); особобыстротвердеющий высокопрочный портландцемент (ОБТЦ); сверхбыстротвердеющий цемент (СБТЦ); сульфатостойкий портландцемент; цементные вяжущие низкой водопотребности (ВНВ); пуццолановый портландцемент (ПЦ); шлакопортландцемент (ШПЦ); белый и цветные портландцементы; тампонажный портландцемент; расширяющиеся и безусадочные цементы и др.
5.БЕТОНЫ И ЖЕЛЕЗОБЕТОНЫ
5.1.Общие сведения и классификация
Бетон на неорганических вяжущих веществах представляет собой композиционный материал, получаемый в результате формования и твердения рационально подобранной бетонной смеси, состоящей из вяжущего вещества, воды, заполнителей и специальных добавок. Состав бетонной смеси должен обеспечить бетону к определенному сроку заданные свойства (прочность, морозостойкость, водонепроницаемость и др.).
Технико-экономическими преимуществами бетона и железобетона являются: низкий уровень затрат на изготовление конструкций; возможность применения в сборных и монолитных конструкциях различного вида и назначения; механизация и автоматизация приготовления бетона и производства конструкций. Бетон долговечен и огнестоек, его плотность, прочность и другие характеристики можно изменять в широких пределах и получать материал с заданными свойствами. Недостатком бетона, как любого каменного материала, является низкая прочность на растяжение, которая в 1015 раз ниже прочности на сжатие. По виду вяжущего бетоны разделяют на: цементные (наиболее распространенные), силикатные (известковокремнеземистые), гипсовые, смешанные (цементно-известковые, известково-
26
шлаковые и т.п.), специальные - применяемые при наличии особых требований (жаростойкости, химической стойкости и др.).
По виду заполнителя различают бетоны на: плотных, пористых, специальных заполнителях, удовлетворяющих специальным требованиям (защиты от излучений, жаростойкости, химической стойкости и т.п.). В правильно подобранной бетонной смеси расход цемента составляет 8-15%, а заполнителей - 80-85% (по массе).
5.2. Свойства бетонной смеси и бетона
Бетонной смесью называют рационально составленную и тщательно перемешанную смесь компонентов бетона до начала процессов схватывания и твердения. По своему строению бетонная смесь представляет единое физическое тело, в котором частицы вяжущего, вода и зерна заполнителя связаны внутренними силами взаимодействия. Независимо от вида бетона бетонная смесь должна удовлетворять двум главным требованиям: обладать хорошей удобоукладываемостью, соответствующей применяемому способу уплотнения, и сохранять при транспортировании и укладке однородность, достигнутую при приготовлении.
Удобоукладываемость (удобоформуемость) - способность заполнять форму при данном способе уплотнения, сохраняя свою однородность. Для оценки удобоукладываемости используют два показателя: подвижность бетонной смеси, являющуюся характеристикой структурной прочности смеси и жесткость (Ж), являющуюся показателем динамической вязкости бетонной смеси.
Подвижность бетонной смеси характеризуется измеряемой осадкой конуса (ОК), отформованного из бетонной смеси, подлежащей испытанию. Если осадка конуса равна нулю, то удобоукладываемость бетонной смеси характеризуется жесткостью.
Жесткость бетонной смеси характеризуется временем вибрирования (с), необходимым для выравнивания и уплотнения предварительно отформованного конуса бетонной смеси в приборе для определения жесткости.
Связность бетонной смеси обуславливает однородность строения и свойств бетона. Очень важно сохранить однородность бетонной смеси при перевозке, укладке в форму и уплотнении.
Проектная марка бетона по прочности на сжатие это сопротивление осевому сжатию эталонных образцов-кубов. Контролируют её путем испытания стандартных бетонных образцов размером 15x15x15см после 28 суток твердения в стандартных условиях (24 ч в формах, покрытых влажной тканью, на воздухе с температурой 20±5° С, затем распалубленные образцы помещают в камеру «нормального твердения», в которой поддерживается относительная влажность воздуха 95±5% и температура 20±5° С). Проектные марки тяжелого бетона по прочности на сжатие: М50, М75, М100, М150, М200, М250, МЗ00,
27
М350, М400, М450, М500, М550, М600, М700, М800, М900, М1000.
Проектная марка бетона по морозостойкости характеризуется числом циклов попеременного замораживания и оттаивания, которое выдерживают образцы в условиях стандартного испытания. Назначается для бетона, подвергающегося многократному воздействию отрицательных температур. Установлены марки по морозостойкости: F50, F75, F100, F150, F200, F300,
F400, F500, F600, F800, F1000.
Проектная марка бетона по водонепроницаемости характеризуется односторонним гидростатическим давлением, при котором образцы бетона не пропускают воду в условиях стандартного испытания. Назначается для бетона, к которому предъявляются требования по плотности и водонепроницаемости. По водонепроницаемости бетон делят на марки W2, W4, W6, W8, W10, W12, W14, W16, W18 и W20, причем марка обозначает давление воды (кгс/см2), при котором образец-цилиндр высотой 15 см не пропускает воду в условиях стандартного испытания.
Класс бетона. Бетон должен быть однородным - это важнейшее техническое требование. Прочность бетонных образцов будет колебаться, отклоняясь от среднего значения в большую и меньшую стороны. На прочности сказываются колебания качества цемента и заполнителей, точность дозирования составляющих, тщательность приготовления бетонной смеси и другие факторы. Чем ближе частные результаты испытания образцов к среднему значению, тем выше однородность бетона. Следовательно, для нормирования прочности необходимо использовать стандартную характеристику, которая гарантировала бы получение бетона заданной прочности с учетом возможных ее колебаний. Такой характеристикой является класс бетона. Класс бетона - это числовая характеристика какого-либо его свойства, принимаемая с гарантированной обеспеченностью 0,95. Это значит, что установленное классом свойство обеспечивается не менее чем в 95 случаях из 100 и лишь в 5-ти случаях можно ожидать его невыполненным. Бетоны подразделяются на классы по прочности на сжатие: В1; В1,5; В2; В2,5; В3,5;
В5; В7,5; В10; В12,5; В15; В20; В25; ВЗ0; В35, В40; В45; В50; В55; В60; В65;
В70; В75; В80. Допускается применение бетонов классов В 22,5 и В27,5.
5.3. Виды бетонов
Тяжелый бетон применяется для изготовления несущих и самонесущих ограждающих конструкций. Требования к нему предъявляются в зависимости от назначения и вида конструкции. Качество бетона определяется качеством и составом его компонентов. Для тяжелого бетона применяют портландцемент и его разновидности, а также глиноземистый цемент и другие вяжущие. Марку цемента назначают в зависимости от проектной марки бетона по прочности при сжатии.
В качестве мелкого заполнителя в тяжелом бетоне применяют природные пески, образовавшиеся в результате естественного разрушения горных пород, а
28
также искусственные, полученные из отсевов дробления твердых горных пород.
В качестве крупного заполнителя для бетона применяют щебень, гравий с размером зерен 5-70 мм. При бетонировании массивных конструкций можно применять щебень крупностью до 150 мм.
Заполнитель должен состоять из зерен разного размера (разных фракций), при этом количество крупных, средних и мелких зерен (т.е. зерновой состав заполнителя) устанавливается на основе проверенных рекомендаций таким образом, чтобы зерна меньшего размера располагались в пустотах между крупными. Чем компактнее расположены зерна заполнителей, тем меньше объем пустот.
Состав бетона рассчитывается на основании специально разработанных методик. Подробнее о расчёте состава тяжёлого бетона, методах его испытания и методах определения его свойств смотри в главе 3 второго раздела настоящего учебного пособия.
Легкие бетоны. Снизить высокую среднюю плотность бетона можно применением пористого заполнителя вместо плотного и поризацией цементирующего слоя. Неорганические пористые заполнители отличаются большим разнообразием, их разделяют на природные и искусственные. Природные пористые заполнители получают путем дробления и рассева горных пород (пемзы, вулканического туфа, известняка-ракушечника и др.). Искусственные пористые заполнители являются продуктами термической обработки минерального сырья (например, керамзитовый гравий, вспученный вермикулит) и разделяются на специально изготовленные и побочные продукты промышленности (топливные шлаки и золы, отвальные металлургические шлаки и др.).
Для поризации цементного камня, являющегося самой тяжелой составной частью легкого бетона, используют небольшие количества пенообразующих или газообразующих веществ. Мелкие и равномерно распределенные поры в цементном камне незначительно понижают прочность, но зато существенно уменьшают плотность и теплопроводность легкого бетона.
Крупнопористый бетон состоит из гравия или щебня крупностью 5-20 мм, вяжущего и воды. За счет исключения песка из состава крупнопористого бетона его плотность уменьшается примерно на 600-700 кг/м3 и составляет 1700-1900 кг/м3. Из крупнопористого бетона возводят монолитные наружные стены зданий, изготовляют крупные стеновые блоки. Крупнопористый бетон на пористом заполнителе используется как теплоизоляционный материал.
Гипсобетон изготовляют на основе строительного гипса, высокопрочного гипса и гипсоцементнопуццоланового вяжущего, обеспечивающего получение водостойких изделий. Для повышения прочности на изгиб и уменьшения хрупкости в состав гипсобетона вводят волокнистые наполнители (древесные волокна, измельченную бумажную массу и т.п.). Гипсобетон широко применяют для изготовления сплошных и пустотелых плит перегородок.
Гидротехнический бетон предназначается для конструкций, находящихся
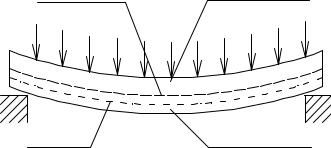
29
в воде или периодически соприкасающихся с водой, поэтому он должен удовлетворять требованиям по прочности, долговечности, водостойкости, водонепроницаемости, морозостойкости, тепловыделению при твердении, усадке и трещиностойкости. В самых суровых условиях работает бетон, расположенный в области переменного уровня воды, многократно замерзая и оттаивая, находясь все время во влажном состоянии.
Дорожный бетон предназначен для оснований и покрытий автомобильных дорог и аэродромов. Покрытие работает на изгиб как плита на упругом основании, поэтому основной прочностной характеристикой бетона является проектная марка на растяжение при изгибе. Бетон дорожных покрытий подвергается совместному действию воды и мороза при одновременном влиянии солей, поэтому он должен иметь необходимую морозостойкость: в суровом климате - не ниже 200; в умеренном - 150; в мягком - 100.
Бетон, упрочненный волокнами Дисперсно-армированный бетон (фибробетон) представляет собой композиционный материал, упрочненный волокнами. В нем невысокая прочность на растяжение и пластичность бетона сочетается с высокомодульным волокном, обладающим высокой прочностью на разрыв. Волокна должны быть стойкими в щелочной среде цементного раствора или бетона. В зависимости от конструкций применяют волокна: минеральные (стеклянные - из бесщелочного стекла, базальтовые, кварцевые и др.), металлические (преимущественно из обычной или нержавеющей стали), синтетические (пропиленовые, капроновые).
5.4. Бетонные и железобетонные изделия и способы их |
|
|
||||||||||
|
производства |
|
|
|
|
|
|
|
|
|
||
Железобетон - это композиционный строительный материал, в котором |
||||||||||||
соединены в единое целое бетон и стальная арматура. Бетон обладает |
||||||||||||
способностью, присущей большинству искусственных и природных каменных |
||||||||||||
материалов: хорошо |
работать |
на |
сжатие, |
но |
плохо |
сопротив-ляться |
||||||
|
зона сжатия |
|
|
растяжению. |
|
|
Так, |
|||||
нейтральная |
|
|
прочность |
|
бето-на |
|||||||
ось |
|
|
|
|
|
|
||||||
|
|
|
|
|
при |
|
растяжении |
|||||
|
|
|
|
|
|
|
||||||
|
|
|
|
|
|
составляет |
|
|
всего |
|||
|
|
|
|
|
|
лишь около 1/10-1/17 |
||||||
|
|
|
|
|
|
его |
прочности |
|
на |
|||
|
|
|
|
|
|
сжатие, |
большинство |
|||||
|
|
|
|
|
|
же |
несущих |
конст- |
||||
арматура |
зона растяжения |
|
|
рукций |
в |
процессе |
||||||
|
|
|
|
|
работы |
испытывают |
||||||
|
|
|
|
|
|
|||||||
|
|
|
|
|
|
напряжение и сжатия |
||||||
Рис. 7. Схема работы железобетонного элемента на изгиб |
и |
растяжения. |
|
Это |
||||||||
|
|
|
|
|
|
наглядно |
видно |
на |
||||
|
|
|
|
|
|
схеме |
|
|
работы |
|||
элемента, представленной на рис. |
7. |
|
|
|
|
|
изгибающего |
|||||
Поэтому растянутую зону конструкций |