
КРАСОВСКИЙ_УП
.PDF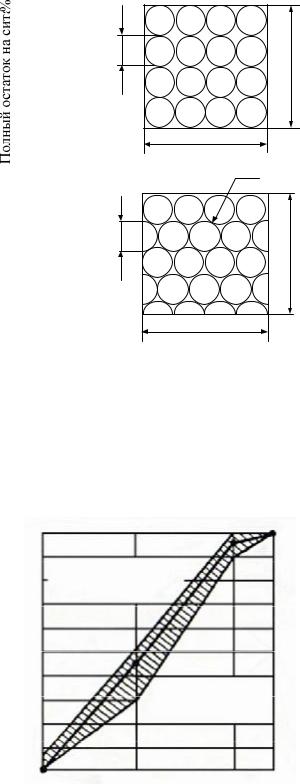
меров (5…10, 10…20, 20…40, 40…70, 70…120). |
|
|||
Зерновой состав называют непрерывным, если в |
|
|||
нем встречаются зерна всех размеров, и преры- |
|
|||
вистым, если отсутствуют зерна какого-либо |
|
|||
промежуточного размера. |
|
|
|
|
Распределение размеров частиц в заполните- |
|
|||
ле очень важно по ряду причин. Чем меньше |
|
|||
число частиц, требуемых для заполнителя данно- |
|
|||
го объема, тем меньше их суммарная поверх- |
|
|||
ность Sуд, которая при рядовом расположении |
|
|||
шаров (рис. 2.1) составит |
|
|
|
|
Sуд = π/d, |
|
|
|
|
т. е. поверхность зерен обратно пропорциональна |
|
|||
диаметру зерна. Поскольку все эти частицы в бе- |
|
|||
тоне должны быть покрыты цементным тестом, |
|
|||
то чем меньше Sуд, тем меньше требуется це- |
|
|||
ментного теста, а следовательно, и цемента. То |
Рис. 2.1. Расположение зерен |
|||
есть, чем крупнее заполнитель, тем экономичнее |
||||
бетон. Максимальная крупность заполнителя, |
заполнителя: а – при рядовой |
|||
ладкеукладке; б – при шахматной ук- |
||||
допускаемая в конструкцию, определяется видом |
||||
конструкции, характером армирования, техноло- |
|
|||
гией приготовления и устанавливается в стандартах или ТУ на определенное |
||||
изделие. Во всяком случае, она должна быть не более ½ d (толщины конструк- |
||||
ции) и ¾ а (размера ячейки арматурного каркаса или сетки). |
||||
Для бетонов гидротехнических |
|
|
|
|
сооружений при соответствующих |
0 |
|
|
|
технико-экономических обоснова- |
10 |
Область мелкого |
||
ниях и непосредственной укладке в |
20 |
|||
бетон допускается применять за- |
щебня (гравия) |
|||
30 |
||||
полнитель размером выше 120 мм. |
|
|
||
40 |
|
|
||
Но цемент расходуется не только |
|
|
||
для покрытия поверхности тестом. |
50 |
|
|
|
Он должен заполнять объемы пус- |
60 |
|
|
|
тот, возникающих между частица- |
70 |
|
Область крупного |
|
ми заполнителя, т. е. экономию це- |
|
щебня (гравия) |
||
80 |
|
|||
мента можно обеспечить правиль- |
|
|
||
90 |
|
|
||
ной градацией частиц: от самого |
|
|
||
крупного до самого мелкого разме- |
100 |
Dнаим |
0,5 (Dнаим+ Dнаиб) Dнаиб 1,25Dнаиб |
|
ра. Поэтому в любом заполнителе |
|
|||
|
|
Размеры отверстий сит |
||
проверяют его зерновой (грануло- |
|
|
||
|
|
|
||
метрический) состав (рис. 2.2). |
Рис. 2.2. График зернового состава щебня |
|||
|
11 |
|
|
PDF created with pdfFactory Pro trial version www.pdffactory.com

Существует много предложений по назначению оптимального зернового состава заполнителя. Одни считают более эффективным непрерывный зерновой состав заполнителя, так как он более экономичен по расходу цемента, другие отдают предпочтение прерывистому, обеспечивающему меньшую пустотность. Следует помнить, что для получения реальных прерывистых смесей необходимо, чтобы размеры соседних фракций отличались примерно в 6 раз, что не всегда возможно на стройке, и такие смеси склонны к расслоению.
Для выбора непрерывного состава заполнителя предлагается целый ряд «идеальных» кривых просеивания, предложенных различными авторами (Фуллер, Боломей, Александрин и др.). Их подбирают из условия, чтобы количество пустот в смеси и суммарная поверхность зерен требовали минимального расхода цемента для получения определенной подвижности и прочности плотного
|
|
|
|
|
|
|
|
|
|
|
|
|
|
бетона. В этом случае получа- |
|
|
|
|
|
|
|
|
|
|
|
|
|
|
|
ются более подвижные смеси |
|
|
|
|
|
|
|
|
|
|
|
|
|
|
|
||
|
|
|
|
|
|
|
|
|
|
|
|
|
|
при одинаковом расходе це- |
|
|
|
|
|
|
|
|
|
|
|
|
|
|
|
мента, менее склонные к рас- |
|
|
|
|
|
|
|
|
|
|
|
|
|
|
|
||
|
|
|
|
|
|
|
|
|
|
|
|
|
|
слаиванию [4]. |
|
|
|
|
|
|
|
|
|
|
|
|
|
|
|
Подбор состава по идеаль- |
|
|
|
|
|
|
|
|
|
|
|
|
|
|
|
||
|
|
|
|
|
|
|
|
|
|
|
|
|
|
ным правилам требует рассева |
|
|
|
|
|
|
|
|
|
|
|
|
|
|
|
щебня и песка на отдельные |
|
|
|
|
|
|
|
|
|
|
|
|
|
|
|
||
|
|
|
|
|
|
|
|
|
|
|
|
|
|
||
|
|
|
|
|
|
|
|
|
|
|
|
|
|
фракции. Часть из них может |
|
|
|
|
|
|
|
|
|
|
|
|
|
|
|
оказаться излишней, часть не- |
|
|
|
|
|
|
|
|
|
|
|
|
|
|
|
достаточной. |
Поэтому на |
|
|
|
|
|
|
|
|
|
|
|
|
|
|
||
|
|
|
|
|
|
|
|
|
|
|
|
|
|
стройках и |
заводах сборного |
|
|
|
|
|
|
|
|
|
|
|
|
|
|
железобетона зерновой состав |
|
Рис. 2.3. Зависимость объема пустот смеси от содер- |
заполнителей подбирают, ис- |
||||||||||||||
жания мелкого и крупного заполнителей |
пользуя реальные пески и ще- |
бень и устанавливая такое соотношение между ними (рис. 2.3), чтобы кривая зернового состава по возможности приближалась к идеальной кривой. Некоторое ухудшение зернового состава в этом случае легко компенсируется незначительным повышением расхода цемента или более эффективным способом уплотнения бетонной смеси. При этом достигается упрощение технологии бетона и снижение его стоимости. Поэтому и в государственных стандартах, и ТУ всегда указывается не один какой-либо рекомендуемый состав, а допускаются колебания в соотношениях отдельных фракций, при которых зерновая смесь еще близка к оптимальной по плотности (табл. 2.1).
Правильный выбор заполнителей и соотношения между песком и щебнем
τ = Vп Vп +Vщ
может быть сделан только с учетом расхода цемента и воды (рис. 2.3).
12
PDF created with pdfFactory Pro trial version www.pdffactory.com
Таблица 2.1
Рекомендуемые составы крупного заполнителя
Наибольшая крупность |
|
Содержание фракций в крупности заполнителя, % |
||||||||
заполнителя, мм |
5... |
10 |
10 |
...20 |
20 |
...40 |
40 |
...70 |
70... |
120 |
20 |
25... |
40 |
60... |
75 |
|
– |
|
– |
|
– |
40 |
15... |
25 |
20... |
35 |
40... |
65 |
|
– |
|
– |
70 |
10... |
20 |
15... |
25 |
20... |
35 |
35... |
55 |
|
– |
120 |
5... |
10 |
10... |
20 |
15... |
25 |
20... |
30 |
20... |
40 |
В бетонах марок 200, 300 при подвижной бетонной смеси наилучшие результаты обеспечивает зерновой состав, близкий к идеальным кривым просеивания. В бетонах высокой прочности с повышенными расходами цемента, в жестких бетонных смесях долю песка уменьшают до τ ≤ 0,33; в высокопластичных, литых смесях, особенно с добавками суперпластификаторов, во избежание расслоения ее наоборот увеличивают до 0,45…0,48.
С зерновым составом вплотную связана пустотность заполнителя, определяемая возможностью его плотной укладки. Пустотность заполнителя определяет расход цемента (чем больше пустот, тем больше цемента требуется для их заполнения). Теоретически объем пустот в заполнителе не зависит от крупности его зерен, но зато на эту характеристику может повлиять порядок укладки зерен (см. рис. 2.1), а значит будет влиять форма зерна (табл. 2.2). В действительности наиболее и наименее плотные укладки маловероятны, а реальна промежуточная система укладки, а значит, и средняя пустотность, определяемая степенью уплотнения.
Таблица 2.2
Пустотность заполнителя в зависимости от формы зерна, %
Форма зерна |
|
Укладка |
|
|
наиболее плотная |
наименее плотная |
средняя |
||
|
||||
Куб |
0 |
87,1 |
43,55 |
|
Октаэдр |
12,2 |
83,9 |
48,05 |
|
Додекаэдр |
14,1 |
60,7 |
37,4 |
|
Икосаэдр |
10,8 |
59,9 |
35,10 |
|
Шар |
26,2 |
47,6 |
36,50 |
С увеличением угловатости, особенно при применении зерен удлиненной формы (игольчатых, лещадных), пустотность увеличивается. Поэтому содержание таких зерен в заполнителе не должно превышать 35 %, а для некоторых видов конструкций – 25 %.
Если заполнитель представлен зернами окатанной формы разной крупности, то пустотность уменьшается с увеличением степени окатанности.
В случаях, когда зерна смешанных фракций близки по размерам, размер мелких фракций может оказаться больше, чем размер пустот между зернами
13
PDF created with pdfFactory Pro trial version www.pdffactory.com
крупной фракции, и тогда произойдет раздвижка зерен (увеличение пустотности смеси). Поэтому в России пока предпочитают работать с одной фракцией щебня (в зависимости от размеров конструкции), заполняя межзерновые пустоты песком и цементным тестом.
Необходимо помнить об уже упомянутой характеристике заполнителя, связанной с его зерновым составом, – удельной поверхности зерен заполнителя.
Чем больше мы берем песка для заполнения пустот в щебне, тем больше суммарная поверхность заполнителей и тем больше расход цементного теста для обеспечения требуемой подвижности, а следовательно, и цемента. В табл. 2.3 приведены данные по изменению расчетной удельной поверхности зерен песка. Значительно возрастает она при крупности зерен песка меньше 1 мм.
Таблица 2.3
Расчетная удельная поверхность отдельных фракций заполнителя
Фракция, мм |
Расчетная удельная поверхность, |
м2/л, абсолютного объема |
|
20...10 |
0,4 |
10...5 |
0,8 |
2,5...5 |
1,6 |
2,5...1,2 |
3,25 |
1,2...0,63 |
6,67 |
0,63...0,31 |
13,33 |
0,31...0,15 |
26,67 |
Менее 0,15 |
80 |
Пылевидные частицы |
160 |
0,05...0,15 |
|
Илистые частицы |
218 |
0,005...0,05 |
|
Глинистые частицы |
2400 |
(меньше 0,005) |
|
Для получения монолитного бетона необходимо, чтобы цементное тесто не только заполнило пустоты между зернами песка, но и раздвинуло зерна с целью создания между ними цементной прослойки, т. е. сформировалась оболочка из цементного теста вокруг каждого зерна заполнителя. Расход цемента на получение подобной оболочки зависит от удельной поверхности заполнителя: возрастает с уменьшением размера зерен.
Добавление к крупному заполнителю мелкого уменьшает их общую пустотность, но одновременно увеличивает их удельную поверхность, поэтому окончательное влияние заполнителя на бетон определяют непосредственным испытанием заполнителя в бетоне.
Для определенных видов изделий рекомендуются конкретные крупности песка (табл. 2.4).
14
PDF created with pdfFactory Pro trial version www.pdffactory.com
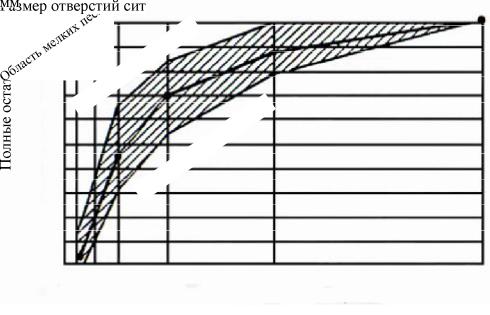
Зерновой состав песка также контролируется с помощью стандартного набора сит и характеризуется графиками просеивания (рис. 2.4) [5].
Рекомендуемые составы песка |
Таблица 2.4 |
||||||
|
|
||||||
|
|
|
|
||||
|
Полные остатки на контрольных ситах, %, |
||||||
Размер отверстий |
|
по массе для бетонов |
|
|
|||
всех видов конст- |
железобетонных и бетонных труб |
||||||
контрольного сита, мм |
|||||||
рукций и изделий, |
напорных, |
безнапорных |
|||||
|
|||||||
|
кроме труб |
низконапорных |
|||||
|
|
|
|||||
2,5 |
0... |
20 |
10 |
...20 |
0... |
20 |
|
1,25 |
5... |
45 |
25... |
45 |
10... |
45 |
|
0,63 |
20... |
70 |
57... |
70 |
50... |
70 |
|
0,31 |
35... |
90 |
70... |
90 |
70... |
90 |
|
0,16 |
90... |
100 |
95... |
100 |
90... |
100 |
|
проходит через сито 0,16 |
10... |
0 |
5... |
0 |
10... |
0 |
|
Модуль крупности |
1,5... |
3,25 |
2,5... |
3,25 |
2,0... |
3,25 |
Рис. 2.4. График зернового состава песка
Для упрощения характеристика крупности песка задается в виде определенного числа – модуля крупности Мкр, определяемого по стандартной методике. По модулю крупности пески различают:
– повышенной крупности |
Мкр = 3…3,5; |
– крупные |
Мкр = 2,5…3; |
– средние |
Мкр = 2…2,5; |
– мелкие |
Мкр = 1,5…2; |
– очень мелкие |
Мкр = 1…1,5. |
|
15 |
PDF created with pdfFactory Pro trial version www.pdffactory.com
Поскольку с уменьшением Мкр увеличивается Sуд, то пески с Мкр = 1,5…2 допускается применять в бетонах прочностью до 200 кг/см2, а также для бетонов подводной зоны конструкций мостов. Пески с Мкр = 2,5 рекомендуются для бетонов прочностью 350 кг/см2 и выше. При технико-экономических обоснованиях государственный стандарт допускает в бетоне классов до В30 использовать пески с Мкр от 1,0 до 1,5.
2.2.3. Прочность заполнителя
Государственный стандарт предъявляет к заполнителям в зависимости от класса бетона и происхождения породы требования по прочности, содержанию в крупном заполнителе зерен слабых пород, по морозостойкости.
Прочность заполнителя, кгс/см2, определяется, как правило, при открытии карьера, путем испытания образцов правильной формы при сжатии, выпиленных из породы. Марка щебня из изверженных пород должна быть не ниже 800, из метаморфических – 600, осадочных – не ниже 300. Как правило, марка щебня должна быть в 1,5…2 раза выше будущей марки бетона.
Впоследующем прочность щебня и гравия контролируется уже с помощью раздавливания в цилиндре и характеризуется дробимостью. Для бетонов классов В30 и выше используется щебень и гравий дробимостью Др 8, для бетонов классов В22,5 и ниже – Др 16.
При определении прочности щебня для путевых работ находят его косвенные характеристики – истираемость и прочность при ударе на копре ПМ.
Но прочность заполнителя определяется не только прочностью горной породы, из которой он получен, но и крупностью зерен. При выветривании или дроблении породы разрушение происходит по более слабым местам структуры
ис уменьшением размера зерен, прочность их как бы повышается. Само выветрелое зерно может служить точкой начала разрушения бетона при внешних воздействиях как наиболее слабое звено его структуры. Поэтому содержание таких зерен в заполнителе ограничивается для бетонов низких классов (В15 и ниже) 15 % по массе, для бетонов высоких классов (В40 и выше) – 5 %.
Вкакой-то степени прочностным показателем щебня является и его морозостойкость. Вследствие этого морозостойкость крупных заполнителей должна быть не ниже нормативной марки бетона по морозостойкости.
Как правило, прочность песка и крупного заполнителя из прочных горных пород выше прочности раствора или цементного камня. Прочность бетона на гранитном щебне выше прочности раствора. Но при применении менее прочного крупного заполнителя прочность бетона при увеличении прочности раствора возрастает только до определенных пределов и дальнейшее увеличение прочности раствора уже не ведет к повышению прочности бетона.
16
PDF created with pdfFactory Pro trial version www.pdffactory.com
2.2.4. Чистота заполнителей
Большое влияние на прочность бетона оказывает чистота заполнителя. Пылевидные и особенно глинистые примеси создают на поверхности зерен заполнителя пленку, препятствующую сцеплению их с цементным камнем. В результате прочность бетона снижается на 30…40 % [6]. Корректировать отрицательное влияние грязного или некачественного заполнителя на свойства бетона можно только путем повышения расхода цемента, что вообще нежелательно.
Еще хуже, когда заполнитель содержит органические примеси. В этом случае процессы твердения и формирования будущих свойств бетона могут стать вообще неуправляемыми.
Вредные примеси в бетоне (в заполнителях, применяемых для производства бетона) могут вызвать:
∙снижение прочности и долговечности бетона (уголь, графит, горючие сланцы, сложные силикаты, цеолит, апатит, нефелин, фосфорит);
∙ухудшение качества поверхности и внутреннюю коррозию бетона (аморфные разновидности диоксида кремния, растворимого в щелочах цемента, хлорит и некоторые цеолиты, сера, сульфиды, сульфаты, магнетит, гидроксид железа);
∙коррозию арматуры в бетоне (галоиды, включающие водорастворимые хлориды, сера, сульфиды и сульфаты).
В связи с этим содержание пылевидных и глинистых частиц в щебне из изверженных и метаморфических пород, щебне из гравия и гравии не должно превышать для бетонов всех классов 1 % по массе, а из осадочных пород для бетонов класса В22,5 и выше – 2 %, а классов В20 и ниже – 3 % по массе.
Аморфные разновидности диоксида кремния (SiО2), растворимого в щелочах цемента (халцедон, опал, кремень и др.), допускаются в количестве не более 50 ммоль/л. Включения серы, сульфидов, кроме пирита (марказит, пирро-
тин и др.) и сульфатов (гипс, ангидрит и др.) в пересчете на SО3, допускаются не более 1,5 % по массе для крупного и 1 % по массе для мелкого заполнителей.
Пирита в пересчете на SО3 возможно не более 4 % по массе.
Слоистые силикаты (гидрослюды, слюды, хлориты и другие, являющиеся породообразующими минералами) ограничиваются 15 % по объему для крупного и 2 % по массе для мелкого заполнителей.
Магнетиты, гидрооксиды железа (гетит и др.), апатит, нефелин, фосфорит, являющиеся породообразующими минералами, каждый в отдельности допустим в объеме до 10 %, а в сумме не более 15 %.
Жесткие требования касаются галоидов (галит, сильвин и др.), включающих водорастворимые хлориды. В пересчете на ион Сl их допускается не более 0,1 % по массе для крупного и 0,15 % по массе для мелкого заполнителей. Свободные волокна асбеста допускаются в количестве не более 0,25 %, а угля – не более 1 % по массе.
17
PDF created with pdfFactory Pro trial version www.pdffactory.com
ГОСТ 26633-91[7] помимо названных устанавливает дополнительные требования к заполнителям для бетонов конструкций различных видов (дорожных и аэродромных покрытий однослойных и двухслойных, бетонов транспортного строительства, гидротехнических и др.).
2.3. Пористые заполнители
Для легких бетонов используют природные заполнители (туф, пемзу, пористые известняки) или полученные искусственным путём (керамзит, шлаковая пемза, аглопорит и перлит).
Марка пористых заполнителей определяется их насыпной массой, кг/м3. Керамзит – гранулы округлой формы с пористой сердцевиной и плотной
спекшейся оболочкой. Получают керамзит быстрым обжигом во вращающихся печах легкоплавких глинистых пород с большим содержанием оксидов железа и органических примесей до их вспучивания.
Керамзит выпускают в виде гравия (5…40 мм) и песка крупностью менее 5 мм. Марки керамзита колеблются от 250 до 600 кг/м3 (зависят от исходных глин), морозостойкость керамзита не менее 15.
Шлаковая пемза – пористый щебень, получаемый вспучиванием жидких металлургических шлаков путем их быстрого охлаждения водой или паром. Этот заполнитель экономически эффективен, а переработка его крайне проста. Марки шлаковой пемзы от 400 до 1000 кг/м3, прочность 0,4…2 МПа.
Аглопорит – пористый заполнитель в виде гравия или щебня, получаемый спеканием сырьевой смеси из глинистых пород и топливных отходов. Марки аглопорита от 400 до 900.
Вспученные перлитовый песок и щебень – пористые зерна светло-серого цвета, получаемые путем быстрого нагрева (1…2 мин) до температуры 1000…1200 °С вулканических горных пород, содержащих небольшое количество (3…5 %) гидратной воды (перлита и др.). При обжиге исходная порода увеличивается в объеме в 5…15 раз, при этом пористость зерен достигает 85…90 %.
Щебень имеет насыпную плотность от 200 до 500 кг/м3, а перлитовый песок – насыпную плотность от 75 до 200 кг/м3.
2.4. Добавки к бетонам
К добавкам относятся вещества, не склонные к самостоятельному твердению, но способные активно участвовать в физико-химических процессах структурообразования смеси или затвердевающего бетона и тем самым усиливать какие-либо их свойства. Добавки делят на 2 группы:
1)химические, вводимые в бетон в небольшом количестве 0,1…2 %;
2)тонкомолотые, вводимые в бетон в количестве 5…20 %.
Применение добавок является одним из наиболее универсальных и доступных способов управления технологией бетона и регулирования его свойств. Ес-
18
PDF created with pdfFactory Pro trial version www.pdffactory.com
ли раньше количество и виды добавок были достаточно ограниченными, то в настоящее время практически любое свойство бетона, любой технический передел смеси можно изменить с помощью одной или группы добавок. Поэтому сегодня уже не обойтись без классификации добавок, способной систематизировать знания в этой области. Вместо использования в качестве добавок отдельных продуктов или модифицированных отходов промышленности в настоящее время используют добавки, специально приготовленные для бетона (суперпластификаторы, органо-минеральные и др.).
Комплекс добавок, улучшающих свойства бетона и облегчающих технологию производства бетонных работ, рассматривается в специальном курсе, опирающемся на глубокое понимание структурных изменений, происходящих в бетоне в течение всего его жизненного цикла. Поэтому в данном пособии в основном рассмотрены только обычные подходы в подборе состава бетона и технологии производства монолитных бетонных работ и производства сборных железобетонных изделий.
2.5. Вода для приготовления бетонной смеси
Для затворения бетонной смеси без ограничений можно использовать питьевую воду, а также любую другую, имеющую показатель ρH не менее 4, т. е. не кислую, способную окрашивать лакмусовую бумагу в красный цвет.
Кроме этого, вода не должна содержать сульфатов более 2700 мг/л (в пересчете на SО4) и всех солей суммарно более 5000 мг/л. Запрещаются к использованию болотные и сточные воды. В сомнительных случаях пригодность воды для приготовления бетонной смеси необходимо проверять путем сравнительных испытаний образцов, изготовленных на данной воде и на обычной водопроводной.
Для приготовления бетонной смеси можно использовать морскую и другие соленые воды, удовлетворяющие названным выше условиям. Кроме этого, к таким сооружениям не должны предъявляться повышенные эстетические требования. Исключением является бетонирование внутренних конструкций жилых и общественных зданий, а также подводных сооружений в жарком и сухом климате, где опасно появление высолов и возможна коррозия арматуры.
Для поливки бетона при уходе за ним в первые 10 суток следует применять ту же воду, что и для приготовления бетона.
Контрольные вопросы
1.Каковы основные принципы выбора вяжущих для бетона?
2.Назовите основные виды гидравлических вяжущих, применяемых при изготовлении бетона.
3.Какова роль заполнителей в бетоне и основные требования к ним?
4.Чем определяются требования к крупному заполнителю по зерновому составу?
19
PDF created with pdfFactory Pro trial version www.pdffactory.com
5.Какое примерное соотношение объемов мелкого и крупного заполнителей рекомендуется в бетонах?
6.Какими свойствами можно охарактеризовать прочностные показатели крупного заполнителя?
7.Каковы требования к зерновому составу мелкого заполнителя и чем они определяются?
8.В связи с чем формулируются требования к заполнителям по чистоте?
9.Какие примеси ограничиваются в заполнителях для бетонов?
10.Какие легкие заполнители вы знаете?
11.С какой целью и какие добавки вводятся в бетоны?
12.Каковы требования к воде для бетона?
3. СТРОИТЕЛЬНЫЕ РАСТВОРЫ
Строительным раствором называют искусственный каменный материал, получаемый в результате рационально подобранной смеси, состоящей из вяжущего вещества, мелкого заполнителя, воды и специальных добавок. До затвердевания эту смесь называют растворной.
Строительные растворы применяют для связывания в монолит кирпичной, каменной кладки, крупных элементов (блоки, панели) при строительстве сборных жилых и промышленных зданий, при декоративной отделке стен и потолков, для устройства полов и стяжек, изготовления тонкостенных конструкций, для выполнения штукатурных, облицовочных и специальных работ.
3.1. Классификация строительных растворов
В соответствии с ГОСТ 28013-98 [8] строительные растворы классифицируют по следующим признакам:
∙основному назначению;
∙применяемому вяжущему;
∙средней плотности.
По основному назначению растворы разделяют: на кладочные (в том числе для монтажных работ) – для каменной кладки стен, фундаментов, столбов, сводов и т. п., а также для монтажа крупных блоков и панелей; штукатурные – для оштукатуривания внутренних конструкций и фасадов зданий; облицовочные – для крепления облицовочных изделий (плитки, плиты, панели и т. п.).
Кроме того, в обширную группу специальных растворов (на которые действие [9] не распространяется) входят жаро-, огне- и химически стойкие, тепло- и гидроизоляционные, тампонажные, декоративные, напрягающие и т. д. – для устройства покрытий в декоративно-отделочных, изоляционных, защитных и других специальных целях.
20
PDF created with pdfFactory Pro trial version www.pdffactory.com