
- •СОДЕРЖАНИЕ
- •Системы вентиляции промышленных зданий в сравнении с системами общественных зданий имеют следующие отличительные особенности:
- •1. Большие расходы воздуха;
- •2. Большие скорости движения воздуха в воздуховодах;
- •3. Большие площади поперечных сечений воздуховодов;
- •4. Применяются в основном воздуховоды круглого сечения;
- •7. Проектирование и монтаж систем промышленной вентиляция отличается специфическими требованиями к их конструированию в зависимости от технологических особенностей производственных процессов.
- •8. Высокая концентрация вредных компонентов в удаляемом воздухе требует либо его очистки в специальном оборудовании перед выбросом в атмосферу, либо организации “факельного выброса” для снижения концентрации вредностей в приземном слое атмосферы.
- •Расчёт и подбор устройств для очистки вытяжного воздуха производится по специальным методикам, приведённых в нормативно-справочной документации, для соответствующих видов производств.
- •9. Местные системы вентиляции и кондиционирования воздуха компонуются в системы по технологическим линиям производства, по одновременности действия оборудования, по видам вредных выделений и по оптимальным расходам воздуха.
- •2. ВРЕДНЫЕ ВЫДЕЛЕНИЯ НА ПРОМЫШЛЕННЫХ ПРЕДПРИЯТИЯХ
- •Избыточная теплота.
- •Источниками теплоты в промышленных производствах могут быть:
- •2. сушильные установки; 5. источники искусств. освещения;
- •3. теплота нагретой продукции; 6. эл.двигатели и др.
- •Количество выделяющейся теплоты определяется по результатам составления теплового баланса в каждом из производств по соответствующей методике.
- •Избыточная влага.
- •Источником влаговыделений могут быть:
- •1. ванны и аппараты с горячей водой;
- •2. сушильные установки;
- •3. смоченные поверхности;
- •4. обрабатываемая продукция
- •5. установки, использующие технологический пар и др.
- •5. красильно-отделочные предприятия легкой промышленности;
- •6. предприятия пищевой промышленности;
- •7. коммунальные предприятия и др.
- •Определение количества влаговыделений проводят в зависимости от источника и вида выделяющейся влаги.
- •Вредные газы и пары.
- •Многие промышленные производства сопровождаются выделением вредных (часто ядовитых) газов и паров.
- •Ядами называют вещества, которые попадая в организм человека даже в незначительных количествах приводят к отравлениям и заболеваниям.
- •x2…xn компонентов смеси вредных газов, м3/ч.
- •Так, например, поступают при одновременном выделении паров растворителей совместно с окислами азота.
- •Расчет количества выделяющихся паров и газов в большинстве случаев проводят по эмпирическим зависимостям, определенным для каждого вида вредностей.
- •Среди наиболее характерных и вредных газов и паров следует отметить:
- •Кроме непосредственного влияния на организм человека пары и газы взрывоопасны при определенном процентном соотношении в смеси с воздухом или кислородом.
- •Классификация вытяжных зонтов
- •Зонты-козырьки над загрузочными отверстиями электрических печей
- •9.6. Пылевые вентиляторы для систем аспирации и пневмотранспорта

42
изготавливают с большими углами раскрытия сторон. Такие зонты называют
низкими.
а) |
б) |
Рис. 3.4 Схемы вытяжных зонтов
а– “высокий” зонт; б – “низкий” зонт
Узонтов с углами раскрытия 90° имеется параболический профиль скоростей на срезе. Значение осевой скорости на 65% больше средней скорости
вплоскости среза зонта υо = 1,65 υср. Эффективность подобных зонтов ниже по сравнению с высоким зонтом.
Классификация вытяжных зонтов
Влитературе встречается достаточно много, не имеющих принципиальных отличий, вариантов классификации зонтов. Для отражения основных свойств и отличий подобных местных отсосов условно вытяжные зонты можно классифицировать следующим образом.
1.По конструктивным особенностям:
−обычные или отдельно стоящие (симметричные, несимметричные). Обычные зонты, в свою очередь, могут быть по форме круглыми, квадратными или прямоугольными.
−зонты-козырьки.
Зонты-козырьки, как правило, несимметричны и устанавливаются в комплекте с технологическим оборудованием. Чаще подобные зонты устанавливают над загрузочными отверстиями печей.

43
Рис. 3.5 Варианты исполнения зонтов по форме
Как правило, из-за высокой температуры внутри печи в её объеме создается давление воздуха немного больше, чем в рабочей зоне помещения. Вследствие этого при открывании дверцы отверстия поток нагретого вырывается наружу.
|
Зонты-козырьки устанавливаются |
|||
|
над загрузочными отверстиями печей. |
|||
|
При открывании дверцы проема в |
|||
|
помещение |
поступает |
нагретый |
|
|
воздушный поток из печи. |
|
|
|
|
Задачей зонта-козырька является |
|||
|
максимальная локализация и отвод из |
|||
|
помещения |
теплового |
потока |
из |
|
проема печи. |
|
|
|
|
Рекомендуется |
следующее |
||
|
соотношение |
размеров |
зонта |
и |
Рис. 3.6 К расчету зонтов |
оборудования: |
|
|
-ширина рабочего проема зонта b = B + 400 мм (равномерно по 200 мм с каждой стороны);
-вылет зонта l = 1,2…1,25 H.
2.По принципу действия (способу движения воздуха):

44
−гравитационные;
−с механическим побуждением;
−активизированные (с поддувом).
Рис. 3.7 Вытяжной зонт с поддувом:
1 – зонт; 2 – технологическое оборудование (источник теплоты); 3 – направленный (по всему периметру источника) поток воздуха – поддув.
3.По расположению:
−одиночные;
−групповые.
Основы расчета вытяжных зонтов
Расход воздуха, удаляемого зонтом, в общем случае может быть определен по рекомендуемой скорости на срезе зонта и площади среза зонта:
L = υз · Fз · 3600 (3.17)
Рекомендуемая скорость зависит от токсичности вредных выделений и формы зонта, и изменяется в пределах 0,2÷1,5 м/с.
Зонты над кухонным оборудованием.
Расход воздуха, удаляемого местным отсосом, определяют из расчета улавливания конвективного потока, восходящего над горячей поверхностью кухонного оборудования.
Для зонтов, установленных над варочным оборудованием (см. рис. ниже), обращенным нагретой поверхностью вверх, расход удаляемого воздуха зависит от:
-площадей нагретой поверхности источника Fи и среза зонта Fз;
-от вертикального расстояния от нагретой поверхности до среза зонта H;
-количества теплоты, выделяемой от нагретой поверхности Qк:
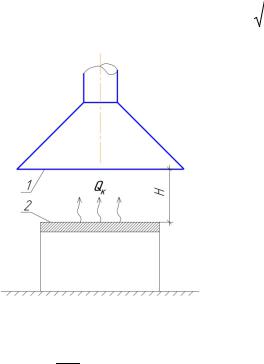
|
|
|
|
|
45 |
|
|
Fз |
|
|
|
||
L =125 |
3 |
H Q |
F 2 |
(3.18) |
||
|
||||||
|
Fи |
|
к |
и |
|
|
|
|
|
|
|
Рис. 3.8 К расчету зонта над варочным оборудованием:
1 – зонт площадью всасывающего
проема Fз;
2 – нагретая поверхность
(источник теплоты) площадью Fи.
Для электрических плит в справочной литературе рекомендовано
соотношение Fз =1,2÷1,5.
Fи
Долю конвективных тепловыделений кухонного оборудования Qк, Вт, определяют по формуле:
Qк = Qт ·Кя ·Кк ·Ко, |
(3.19) |
где Qт - установленная мощность кухонного оборудования, кВт; Кя - доля явных тепловыделений от установочной мощности
кухонного оборудования, Вт/кВт; Кк - доля конвективных тепловыделений от явных тепловыделений
кухонного оборудования. При отсутствии данных для конкретного оборудования допускается принимать Кк = 0,5;
Ко - коэффициент одновременности работы кухонного оборудования.
Зонты-козырьки над загрузочными отверстиями электрических печей
Для электрических печей расход воздуха, удаляемого зонтамикозырьками, определяется по зависимости:
L = |
B L′ |
, |
(3.20) |
|
H |
||||
|
|
|
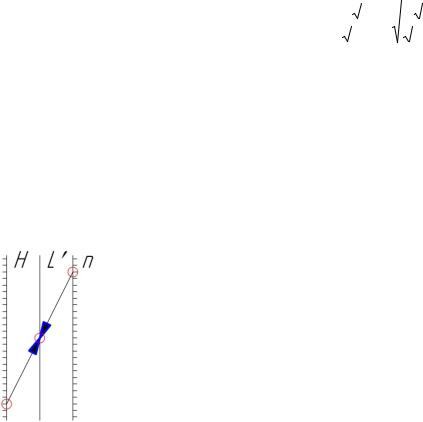
46
то есть расход удаляемого воздуха определяется геометрическими размерами загрузочно-выгружного отверстия В и Н и комплексным показателем L'.
Комплексный показатель L' зависит от высоты и относительной температуры и рассчитывается по выражению:
|
3 |
|
|
|
|
|
|
3 |
|
|
|
|
|
|
|
|||
L′=7700 H 1,5 |
|
n |
|
|
|
|
n |
(n −1), |
(3.21) |
|||||||||
|
|
|
|
|
|
|
|
|
|
|
|
|||||||
3 n +1 |
3 n +1 |
|||||||||||||||||
|
|
|
|
|
|
где n – отношение абсолютной температуры горячих газов в печи к абсолютной температуре воздуха в рабочей зоне:
n = |
Tг |
≈ |
ρв |
(3.22) |
|
ρг |
|||||
|
Тв |
|
|
Температура горячих газов принимается равной температуре в камере
печи.
Значение L' также определяется в справочной литературе по графику-номограмме в зависимости от H и n.
Для зонтов-козырьков со шторками ширина принимается не менее ширины отверстия + 200 мм (с каждого края по 100
мм), т.е. b ≥ B + 200 мм.
4. ВОЗДУШНЫЕ ЗАВЕСЫ
Воздушная завеса – вентиляционное устройство, использующее шиберующее (“schieber” – нем. заслонка) свойство плоской воздушной струи для предотвращения прохода воздуха через открытый проем.
В системах вентиляции применяют воздушные (ВЗ) и воздушно-тепловые завесы (ВТЗ).
Воздушные завесы (ВЗ) − вентиляционные устройства, предназначенные для предотвращения перетекания воздуха через проемы внутренних перегородок смежных помещений производственного здания с различными классами вредных веществ.
Воздушные завесы устанавливают также у проемов и отверстий технологического оборудования для предотвращения выбивания вредных
47
выделений в воздух рабочей зоны.
Воздушно-тепловые завесы (ВТЗ) – вентиляционные устройства,
предназначенные для предотвращения перетекания наружного воздуха через двери, ворота и проемы зданий и сооружений различного назначения. Они исключают проникновение в помещение холодного наружного воздуха и позволяют поддерживать нормируемые параметры микроклимата в помещении в холодный период года.
ВТЗ имеют следующие основные элементы:
1.вентиляционный агрегат;
2.воздухонагреватель;
3.система воздуховодов и каналов;
4.воздухораспределитель - воздуховоды равномерной раздачи или вентиляционная колонка с щелевым выпуском воздуха через направляющие лопатки.
4.1.Классификация воздушно-тепловых завес
Воснове классификации ВЗ положены принцип действия завесы, режим работы, качество и направление приточных струй, место забора воздуха.
ВТЗ классифицируют по следующим признакам:
1.По принципу действия:
- шиберующего типа - применяются чаще в производственных зданиях
ииспользуется главное свойство плоской струи – отсекать холодный наружный воздух.
- смесительного типа – применяются чаще в общественных зданиях и предназначены для смешивания холодного наружного и нагретого в калорифере воздуха для обеспечения требуемых температурных условий вблизи проема.
2.По режиму работы:
-периодического действия - применяются, как правило, в
производственных зданиях и работают в период открывания ворот. Завесы

48
периодического действия конструируются таким образом, чтобы они не оказывали влияние на тепловой и воздушный режим помещений (в балансе не учитываются).
-постоянного действия - используются либо как воздушноотопительные агрегаты, либо как элементы приточных систем вентиляции. Работают постоянно.
Режим работы завесы определяется следующими факторами: а) требованиями к параметрам микроклимата в помещении; б) наличием постоянных рабочих мест в районе завесы;
в) режимом работы общеобменных приточных систем вентиляции.
3.По направлению действия струи:
-“снизу вверх” (с нижней раздачей);
-“с боковой подачей” (одностороннее или двухстороннее)
-“сверху-вниз” ( с верхней раздачей)
Степлотехнической точки зрения наиболее эффективной является завеса по схеме “снизу-вверх”, т.к. в этом случае совпадает направление действия гравитационных и инерционных сил. Данная схема не получила широкого распространения из-за постоянного засорения и разрушения щелевого выпуска
ивоздуховода равномерной раздачи при движении автотранспорта и проходе людей через проем.
Впромышленных зданиях наибольшее распространение получила схема с боковой подачей.
Двухстороннюю боковую раздачу проектируют при ширине проема более 2,5 м, при ширине проема менее 2,5 м проектируют одностороннюю боковую раздачу.
Вобщественных зданиях и административно-бытовых комплексах в основном конструируют воздушно-тепловые завесы по схеме “сверху-вниз” (это связано с планировкой помещений).
4. По температуре подаваемого воздуха и месту воздухозабора на завесу:
- с внутренним воздухозабором и подогревом воздуха
49
tз > tв, tв = tр.з. (tв = tв.з.).
Используется в помещениях при наличии постоянных рабочих мест в районе завесы, где недопустимо значительное понижение температуры.
- с внутренним воздухозабором без подогрева
tз = tв, tв = tр.з. (tв = tв.з.).
Используется в помещениях с явными теплоизбытками и отсутствием постоянных рабочих мест в районе завесы. Допускается некоторое снижение температуры в районе завесы.
- с наружным воздухозабором и подогревом воздуха tз > tн.
Используется, если завеса является системой приточной вентиляции.
- с наружным воздухозабором без подогрева tз = tн.
Используется в сухих помещениях с явными тепловыделениями и избыточным давлением (доминирующим дисбалансом общеобменных приточных систем вентиляции над вытяжными системами). За счет внутреннего избыточного давления весь воздух воздушно-тепловой завесы выдавливается через открытый проем наружу.
Согласно СНиП 41-01-2003 «Отопление, вентиляция и кондиционирование» воздушные и воздушно-тепловые завесы следует предусматривать в следующих случаях:
1.У постоянно открытых проемов в наружных стенах помещений, а также у ворот и проемов в наружных стенах, не имеющих тамбуров и открывающихся более пяти раз или не менее чем на 40 мин в смену в районах с расчетной температурой наружного воздуха минус 15 °С и ниже (параметры Б);
2.У наружных дверей вестибюлей общественных и административнобытовых зданий в зависимости от расчетной температуры наружного воздуха (параметры Б) и числа людей, проходящих через двери в течение
50
1 ч при температуре, °С: |
|
|
|
минус 15 - минус 25 |
- |
400 чел. и более; |
|
минус 26 – минус 40 |
- 250 |
чел. и более; |
|
ниже минус 40 |
- |
100 |
чел. и более. |
3.При обосновании – у наружных дверей зданий, если к вестибюлю примыкают помещения без тамбура, оборудованные системами кондиционирования либо имеются специальные технологические требования.
4.У наружных дверей, ворот и проемов помещений с мокрым режимом;
5.При обосновании – у проемов во внутренних стенах и перегородках производственных помещений для предотвращения перетекания воздуха из одного помещения в другое; Температуру воздуха, подаваемого воздушно-тепловыми завесами,
следует принимать не выше 50 °С у наружных дверей и не выше 70 °С у наружных ворот и проемов.
Согласно положений СНиП 41-01-2003 расчетную температуру смеси
воздуха, поступающего в помещение через наружные двери, ворота и проемы, следует принимать, °С, не менее:
12 – для производственных помещений при легкой работе и работе средней тяжести и для вестибюлей общественных и административно-бытовых зданий;
5 – для производственных помещений при тяжелой работе и отсутствии постоянных рабочих мест на расстоянии 6 м и менее – от дверей, ворот и проемов.
Воздушные и воздушно-тепловые завесы у наружных проемов, ворот и дверей следует рассчитывать с учетом ветрового давления.
Расход воздуха следует определять, принимая температуру наружного воздуха и скорость ветра при параметрах Б, но не более 5 м/с. Если скорость ветра при параметрах Б меньше, чем при параметрах А, то воздухонагреватели следует проверять на параметры А.
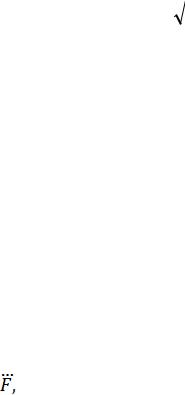
51
Скорость выпуска воздуха из щелей или отверстий воздушных и воздушно-тепловых завес следует принимать, м/с, не более:
8 – у наружных дверей;
25 – у ворот и технологических проемов.
Рекомендуемая скорость в воздуховодах и каналах завесы должна составлять 70% от скорости воздуха на выходе из щели всасывания: υв = 0,7υз.
4.2.Расчёт воздушно-тепловых завес
(на примере ВТЗ шиберующего типа периодического действия)
1. Определяется массовый расход воздуха воздушно-тепловой завесы:
Gз = 5100 qз µпр Fпр |
∆Р ρсм |
, |
|
(4.23) |
||||
где qз– относительный расход воздушной завесы или характеристика |
||||||||
воздушно-тепловой завесы, |
|
|
|
|
|
|||
|
qз = |
G |
|
|
|
|
(4.24) |
|
|
з |
|
|
|
|
|
||
|
G |
|
|
|
|
|||
|
|
пр |
|
|
|
|
|
|
Gпр – количество приточного воздуха, поступившего в помещение |
||||||||
Через проем при работе завесы; |
|
|
||||||
Значение qз |
определяется технико-экономическим расчетом. |
|||||||
Рекомендуется принимать qз = 0,6…0,7. |
|
|
||||||
μпр – коэффициент расхода проема; |
|
|
|
|
|
|||
Принимается |
по справочной |
литературе |
в |
зависимости от |
||||
относительной площади |
относительного |
расхода qз |
и |
способа подачи |
||||
воздуха. |
|
|
|
|
|
|
|
|
Относительный расход рекомендуется принимать равным в
пределах 20…30.
Fпр – площадь проема, закрываемого воздушно-тепловой завесой, м2,
Fпр = Нпр · Впр;
∆Р − расчетный перепад давлений воздуха на уровне проема

|
52 |
снаружи и внутри здания, Па; |
|
∆Р = ∆Рр +kυ ∆Рυ , |
(4.25) |
∆Рр − располагаемое давление в проеме, Па; |
|
∆РР = g h (ρн −ρв), |
(4.26) |
h – расчетная высота, т.е высота от центра проема до уровня |
|
нулевых давлений; |
|
ρн, ρв – плотности воздуха при температурах наружного и внутреннего воздуха соответственно, кг/м3;
kυ − коэффициент, характеризующий поправку на ветровое давление и учитывающий степень герметичности зданий. Определяется по справочной литературе (см.ниже);
∆Рυ – избыточное давление на уровне проема, Па
∆Рυ = сυ |
υ2 |
ρн ; |
(4.27) |
υ |
|||
|
2 |
|
|
сυ – расчетный аэродинамический коэффициент; в расчетах для зданий принимают сv = + 0,8;
υυ – расчетная скорость ветра, м/с, по параметрам Б для холодного периода года.
Значение kυ принимается из справочной литературы в зависимости от конструкции зданий.
Высота h принимается по вертикали от центра проема до нулевой зоны, которая совпадает с верхним краем проема.
а)
Рис. 4.1 К расчету воздушнотепловых завес
а - для зданий без аэрационных проемов и
фонарей (kυ = 0,2) |
(4.28) |
h = 0,5Нпр |
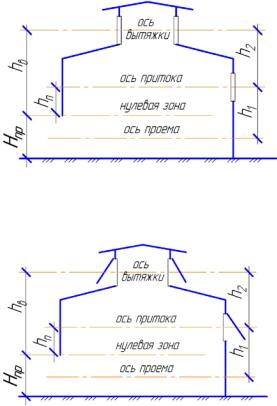
|
|
|
|
|
|
|
53 |
|
б) |
б - для зданий с аэрационными проемами |
|||||||
|
закрытыми в холодный период года |
|||||||
|
(kυ = 0,5) |
|
|
|
h2 |
|
|
|
|
h = h1 |
+ |
|
|
|
(4.29) |
||
|
|
|
2 |
|
||||
|
|
|
lп |
|
|
|
|
|
|
|
|
|
|
|
+1 |
||
|
|
2l |
|
|||||
|
|
|
|
|
|
|||
|
|
|
|
в |
|
|
в)
в- для зданий с аэрационными проемами открытыми в холодный период года
(kυ = 0,8) |
|
|
|
|
|
h2 |
|
|
|
|
h = h1 |
+ |
|
|
|
|
|
|
|
(4.30) |
|
|
µп |
|
Fп |
|
2 |
|
||||
|
|
|
|
|
|
|||||
|
|
|
|
|
|
+1 |
||||
|
F |
|
||||||||
|
|
|
µ |
в |
|
|
||||
|
|
|
|
|
в |
|
|
|
|
где h1, h2 – вертикальные расстояния от центра проема до центра приточных фрамуг и между центрами приточной и вытяжной фрамуг соответственно, м;
hп, hв – соответственно вертикальные расстояния от центра приточных фрамуг до нулевой зоны и от центра вытяжных фрамуг до нулевой зоны, м;
h – расчетная высота, м;
Усредненные значения h для одноэтажных производственных зданий приведены в справочнике проектировщика.
Н – высота проема, м;
lп – горизонтальная длина приточной фрамуги (в плане), м; lв – горизонтальная длина вытяжной фрамуги (в плане), м;
μп, μв – соответственно коэффициенты расхода приточных и вытяжных аэрационных фрамуг;
Fп, Fв – площади соответственно приточных и вытяжных фрамуг, м2.

|
|
|
|
|
54 |
2. Определяется температура воздуха воздушно-тепловой завесы: |
|
||||
|
tсм −tн |
|
|||
tЗ = |
q (1− |
|
) |
+tн , |
(4.31) |
Q |
где tн – расчетная температура наружного воздуха в холодный период по параметрам Б, °С;
Q – относительные потери теплоты завесы, характеризует долю теплоты, теряемую с воздухом, уходящим через открытый проём
наружу, относительно общей тепловой мощности ВТЗ, т.е. |
|
|||||
|
|
= |
Qт/пот |
, |
(4.32) |
|
Q |
||||||
|
|
|||||
|
|
|
Qз |
|
Определяется по справочнику проектировщика в зависимости от
Q= f (qз; F ).
3.Рассчитывается тепловая мощность воздушно-тепловой завесы:
Qз = 0,278 · Gз · св · (tз – tо), |
(4.33) |
где tо – начальная температура воздуха, забираемого для завесы; Определяется в зависимости от местоположения всасывающего отверстия вентилятора:
tо = tр.з.; tо = tв.з.; tо = tсм; tо = tн |
|
||||
4. Определяется ширина щелевого выпуска завесы: |
|
||||
bщ = |
|
Fпр |
, |
(4.34) |
|
|
|
|
|||
|
|
|
|||
|
2 F Hщ |
|
Нщ = Нпроема
Коэффициент 2 применяется для двухсторонних воздушно-тепловых
завес.
5. Вычисляется скорость воздуха, м/с, на выходе из щели завесы по зависимости
υз = |
Gз |
|
|
, |
(4.35) |
2 3600 F |
ρ |
|
|||
|
щ |
|
з |
|
Fщ = bщ · Нщ,
|
|
55 |
|
|
υз ≤ υдоп |
(4.36) |
|
6. Если неравенство (25) не выполняется, то пересчитывают ширину |
|||
щелевого выпуска при υз = υдоп |
|
|
|
b = |
Gз |
(4.37) |
|
2 3600 Нщ υдоп ρз |
|||
щ |
|
7. Так как при открывании проемов, дверей или ворот температура в районе завесы понижается, то необходимо определять дополнительно количество теплоты завесы, которое расходуется на восстановление температуры от tсм до tр.з.
Q |
= |
0,278 Gв с |
(t |
р.з. |
−t |
см |
) |
τ |
(4.38) |
|
|||||||||
доп |
|
в |
|
60 |
|
||||
|
|
qз |
|
|
|
|
|
Из зависимости (4.38) рассчитывают время работы завесы после закрытия проема τ.
5. АВАРИЙНАЯ ВЕНТИЛЯЦИЯ
Системами аварийной вентиляции (АВ) оборудуются промышленные здания, в которых возможен внезапный (залповый) выброс вредных веществ в количествах, создающих опасные для жизни или взрывоопасные концентрации.
Системы представляют собой совокупность элементов и устройств вытяжной вентиляции, работающих только в аварийных ситуациях. Если по технологии производства в помещении возможно выделение взрывоопасных газов и паров, в нем устанавливают автоматические газоанализаторы, которые при достижении опасных концентраций до значений в 20 % от нижнего предела взрываемости включают системы АВ. При этом общеообменные приточновытяжные системы выключаются. В некоторых случаях функции аварийной вентиляции могут выполняться “штатными” системами и устройствами:
1. Если категория и группа взрывоопасной смеси соответствуют техническим условиям на основные (“штатные”) местные и общеообменные систем, то их допускается использовать в качестве аварийных.
56
2.Производительность основных систем должна быть не меньше требуемого аварийного воздухообмена.
3.Если основные системы планируют использовать как аварийные, то они должны быть оборудованы резервным вентилятором.
4.Если выделяющиеся газы и пары легче воздуха, то в одноэтажных зданиях с аэрационными фонарями и шахтами аварийная вентиляция может быть решена приточной системой, вытесняющей вредности через эти проемы.
Если производительность основных систем недостаточна, то возможны
два варианта устройства систем АВ:
1.Основные системы оборудуются резервными вентиляторами и дополнительно устраивается отдельная система АВ с недостающей производительностью.
Lдоп.ав = Lав – Σ Lосн , |
(5.1) |
где Lдоп.ав – производительность дополнительной системы АВ, м3/ч; Lав – расчетный аварийный воздухообмен, м3/ч;
Σ Lосн – суммарная производительность основных (“штатных”) систем вентиляции, м3/ч;
2. Основные системы остаются без изменения (один вентилятор на систему). Производительность дополнительной Системы АВ определяется по формуле
Lдоп.ав = Lав – Σ Lосн + Lосн.макс., |
(5.2) |
где Lосн.макс – наибольшая производительность одной из основных систем, м3/ч.
Особенности устройства аварийной вентиляции
взданиях различных категорий:
1.Для помещений категорий А и Б оборудование АВ должно быть во взрывобезопасном исполнении либо для этих целей применяют эжекторные установки.
2.Системы АВ зданий всех категорий должны быть механическими.

57
3. Если необходимый аварийный воздухообмен будет обеспечен в теплый период при параметрах Б наружного воздуха, в зданиях В, Г, Д допускается аварийная вентиляция с естественным побуждением.
Согласно требованиям норм для компенсации удаляемого воздуха не требуется дополнительных приточных установок.
Исходными данными для расчета АВ являются:
1.Количество выделяющихся при залповом выбросе вредностей;
2.Производительность существующей (основной) системы вентиляции. Расчетные зависимости принято рассматривать для двух основных
вариантов.
Вариант 1: Изменение концентрации вредных веществ в помещении при неработающей (отсутствующей) вентиляции (основные системы отключены).
Исходные данные:
1.Концентрация вредных веществ в помещении в начальный момент времени равна Co, мг/м3;
2.Источник вредных выделений действует с интенсивностью Mвр,
мг/ч.
Балансовое уравнение по вредным выделениям в любой момент времени τ имеет вид
Mвр dτ - Vпом dC = 0. |
(5.3) |
Для определения концентрации вредностей в любой момент времени |
|
балансовое уравнение необходимо проинтегрировать в интервале |
времени |
от 0 до τ: |
|
|
(5.4) |
После интегрирования получим выражение для определения текущей |
|
концентрации вещества в любой момент времени: |
|
C = Co + (Mвр / Vпом ) τ, |
(5.5) |
где Co – начальная концентрация вещества в помещении, мг/м3; |
|

58
Mвр – интенсивность вредных выделений, мг/ч; Vпом – объем помещения, м3;
τ – продолжительность процесса, ч.
Зависимость (5.5) позволяет оценить необходимость устройства вентиляции в помещениях большого объема при небольшом количестве выделяющихся вредностей. Графическая интерпретация этого процесса приведена на рисунке.
Рис. 5.1 Изменение во времени концентрации вредных веществ в помещении при отсутствии вентиляции:
1 – ПДК достигается за рабочую смену;
2 – ПДК достигается по окончании рабочей смены.
Графическая зависимость позволяет сделать следующие выводы:
1.если концентрация вредных веществ достигает значения ПДК за время τ ≤ 1 (линия 1), то в этом случае вентиляция обязательна в течение всей смены;
2.если концентрация вредных веществ достигает значения ПДК в течение рабочей смены (1<τ<8), то в этом случае система вентиляции включается через некоторое время после начала смены, а затем периодически включается через определенное время для предотвращения повышений концентраций выше значений ПДК (линия 2);
3.если в течение рабочего дня значение концентрации вредных веществ не превышает ПДК, допускается не устраивать систему вентиляции
59
для данного помещения (линия 3). В этом случае достаточно неорганизованного воздухообмена.
Вариант 2 : Изменение концентрации вредных веществ в помещении при обеспечении заданного воздухообмена (основные системы работают).
Исходные данные:
1.Концентрация вредных веществ в помещении в начальный момент времени равна Co, мг/м3;
2.Источник вредных выделений действует с интенсивностью Mвр,
мг/ч.
3.Система общеобменной вентиляции включается с началом поступления вредных выделений.
При рассмотрении данного варианта принимают следующие допущения:
1.в помещении рассматриваются изотермические условия (температура воздуха по всему объему постоянна);
2.вредности от действующего источника распределяются по помещению равномерно.
Тогда в любой момент времени будем иметь следующие соотношения:
1.С = Сух (Сух - концентрация вредного вещества в уходящем воздухе);
2.Lпр = Lух;
3.ρпр = ρух .
Балансовое уравнение по выделяющимся вредностям можно представить в виде:
Mвр dτ + Lпр Спр dτ – Lух Сух dτ – Vпом dС = 0 |
(5.6) |
где Mвр dτ – количество вредных веществ, поступивших в помещение за время τ (аварийный выброс);
LпрCпр dτ – количество вредных веществ, поступивших в помещение за время τ с приточным воздухом;
LухCухdτ – количество вредных веществ, удаляемых из помещения за время τ вытяжными общеобменными системами.
60
После интегрирования балансового уравнения получим выражение:
|
|
|
|
Mвр |
|
|
|
|
|
|
||
|
|
|
+С |
пр |
−С |
|
|
|||||
|
|
|
|
|
||||||||
V |
τ = −ln |
|
М |
|
|
|
|
|
|
(5.7) |
||
|
|
|
|
|
|
|
|
|||||
Lух |
|
|
|
Lух |
|
|
|
|
|
|||
nом |
|
|
|
|
вр |
+С |
пр |
−С |
|
|
||
|
|
|
|
|
|
|||||||
|
|
|
|
Lух |
0 |
|
|
|||||
|
|
|
|
|
|
|
|
|
Отсюда можно выразить продолжительность изменения концентрации в заданных пределах:
|
|
|
|
|
|
|
|
|
|
|
|
|
|
|
|
|
|
|
|
|
Mвр |
|
+C |
|
|
−C |
|
|
|
||
|
V |
|
|
|
|
|
|
|
|||||||
|
|
|
|
Lух |
|
|
пр |
|
0 |
|
(5.8) |
||||
τ = |
пом |
ln |
|
|
|
|
|
|
|
|
|
|
|||
L |
ух |
|
M |
вр |
|
|
|
|
|
|
|
||||
|
|
|
|
|
+C |
пр |
−C |
|
|
||||||
|
|
|
|
|
|
|
|||||||||
|
|
|
|
|
Lух |
|
|
|
|
|
|
|
|||
|
|
|
|
|
|
|
|
|
|
|
|
|
В соответствии с понятием кратности воздухообмена, выразим кратность аварийного воздухообмена:
|
|
|
|
n |
= |
Lух |
|
|
|
|
|
|
|
|
|
|
||||||
|
|
|
|
|
|
|
|
|
|
|
|
|
|
|
|
|||||||
|
|
|
|
|
ав |
|
|
|
Vnом |
|
|
|
|
|
|
|
|
(5.9) |
||||
|
|
|
|
|
|
|
|
|
|
|
|
|
|
|
|
|
||||||
Тогда из выражения для τ можно получить формулу для определения |
||||||||||||||||||||||
кратности аварийного воздухообмена: |
|
|
|
|
|
|
|
|
|
|
|
|
|
|
|
|
|
|
|
|||
|
|
|
|
|
|
|
|
|
|
|
|
|
|
|
|
|
|
|
|
|||
|
|
|
|
|
|
|
Mвр |
|
+C |
пр |
|
−C |
0 |
|
|
|
||||||
|
|
|
|
|
|
|
|
|
|
|
||||||||||||
1 |
|
|
|
Lух |
|
|
|
|
|
|||||||||||||
|
|
|
|
|
|
|
|
|
|
(5.10) |
||||||||||||
|
nав = |
|
ln |
|
|
|
|
|
|
|
|
|
|
|
|
|
|
|
|
|||
τ |
|
Mвр |
|
|
|
|
|
|
|
|
|
|||||||||||
|
|
|
|
|
|
|
+C |
пр |
−C |
|
|
|
||||||||||
|
|
|
|
|
|
|
|
|
||||||||||||||
|
|
|
|
|
|
|
Lух |
|
|
|
|
|
|
|||||||||
|
|
|
|
|
|
|
|
|
|
|
|
|
|
|
||||||||
Если необходимо определить изменение концентрации, то применяют |
||||||||||||||||||||||
выражение: |
|
|
|
|
|
|
|
|
|
|
|
|
|
|
|
|
|
|
|
|||
|
Mвр |
|
|
|
|
|
|
|
|
|
|
|
|
|
−n |
τ |
|
|||||
С = |
+Спр − |
Mвр |
|
+Cпр −C0 |
e |
|
ав |
|
(5.11) |
|||||||||||||
|
|
|
|
|||||||||||||||||||
|
Lух |
|
|
|
|
|
|
|
|
|
|
|
|
|
|
|
|
|
||||
|
Lух |
|
|
|
|
|
|
|
|
|
|
|
|
|
Варианты графической интерпретации этой зависимости приведены на рисунке 5.2.
По графику (б) можно определить время эвакуации людей, то есть время, в течение которого концентрация не будет превышать ПДК, и находящиеся в помещении люди могут принять меры для защиты от отравления.
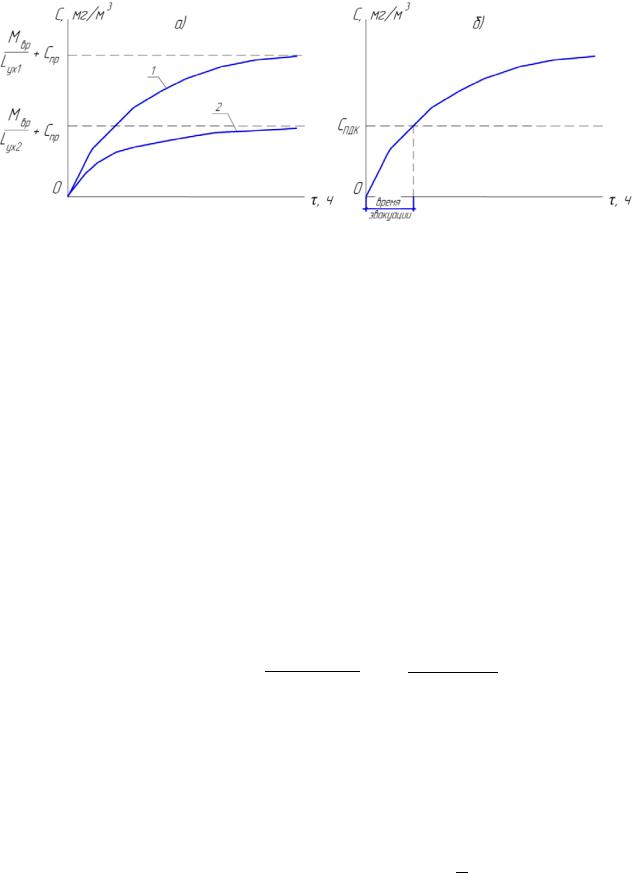
61
Рис. 5.2 Изменение во времени концентрации вредных веществ в помещении при наличии вентиляции
а) при начальной концентрации |
б) при наступлении аварийного |
|
Со = 0: |
|
режима (время эвакуации |
1 – при воздухообмене Lух1 |
; |
рассчитывают по ф-ле (5.8)). |
2 – при воздухообмене Lух2 |
; |
|
Lух1 > Lух2 |
|
|
Более сложную задачу представляет определение воздухообмена, создаваемого аварийной вентиляцией при известных значениях τ, Со и Mвр .
Решение уравнения (5) относительно Lух невозможно из-за большого числа переменных. В инженерной практике для определения производительности аварийной вентиляции предложено (инж. А.Ф. Маурер) использовать систему относительных выражений: относительно концентрации, времени и расхода.
с = |
C −Cпр |
|
|
|
τ Mвр |
|
|
|
|
|
|
|
Mвр |
|
|
|
||||||||
; τ = |
|
|
; L = |
|
|
|
|
(5.12) |
||||||||||||||||
C |
0 |
−C |
пр |
V |
(C |
о |
−C |
пр |
) |
L |
yx |
(C |
о |
−C |
пр |
) |
||||||||
|
|
|
|
|
|
nом |
|
|
|
|
|
|
|
|
|
|
|
На основе зависимостей (5.12) составлена номограмма для определения требуемых расходов Lух (рис.5.3).
Из первых 2-х зависимостей системы определяют относительную концентрацию и относительное время. Потом по графику находят значение относительного расхода.
Найденное значение относительного расхода L подставляют в 3 выражение системы (10) и решают его относительно Lух.

62
Рис. 5.3 Номограмма для расчета воздухообмена
аварийной вентиляции
Размещение приемных отверстий систем аварийной вентиляции:
1.В рабочей зоне: при поступлении вредностей с удельным весом больше, чем удельный вес воздуха рабочей зоны.
1.1.Если для АВ используются местные вытяжные системы, то
удаление
выбросов осуществляется через местные отсосы;
1.2.Отверстия систем АВ размещают на уровне до 0,3 м от уровня
пола.
2.В верхней зоне: при поступлении вредностей с удельным весом меньшим, чем удельный вес воздуха рабочей зоны.
2.1.Не ниже 0,4 м от плоскости потолка или покрытия до верха отверстий
–при удалении взрывоопасных смесей газов, паров и аэрозолей (кроме смеси воздуха с водородом).
2.2.При выделении смеси воздуха с водородом:
-В зданиях высотой до 4 м - не ниже 0,1 м от плоскости потолка или покрытия до верха отверстий;
-В зданиях высотой более 4 м – не ниже 0,025 высоты помещения (но не более 0,4 м) от плоскости потолка или покрытия до верха отверстий.
Организация выбросов за пределы здания
1.Срез шахты или низ отверстий для удаления загрязненного воздуха,
63
удаляемого АВ располагают на уровне не менее 3 м от уровня земли.
2.Не ближе 10 м по горизонтали, и выше 6 м (если горизонтальное расстояние меньше 10 м) по вертикали от воздухоприемных отверстий приточной вентиляции.
3.Не ближе 10 м от источников возможного воспламенения – при удалении взрывоопасных паров и газов.
4.Не допускается организовывать выбросы в места постоянного пребывания (прохода) людей и непроветриваемые зоны (зоны аэродинамической тени).
6.ВЕНТИЛЯЦИОННОЕ ОБОРУДОВАНИЕ
ОКРАСОЧНЫХ ЦЕХОВ
Окраска деталей применяется в различных производствах для защиты изделий от коррозии, а также для придания им определенного декоративного вида. С этой целью применяют окрасочные материалы различного состава и свойств: масляные (на основе олифы); на основе растворителей; битумные; нитроцеллюлозные и др.
Процесс окраски изделий включает следующие основные операции: 1. подготовка под окраску – механическая обработка для удаления окалины, пыли, жировых пятен и др.; 2. грунтование – покрытие специальным составом для улучшения связующих свойств краски;
3.шпатлевание и шлифовка – нанесение шпатлевок и мастик для окончательного выравнивания поверхности;
4.окраска;
5. сушка.
Наиболее распространены следующие способы окраски:
1. пневмораспыление; 2. струйный облив; 3. окрашивание кистями или валиками; 4. окунание; 5. электроосаждение.
64
Сушку осуществляют либо естественным путем – в помещении цеха или в специальных сушильных установках различных принципов действия (конвекционные, индукционные, терморадиационные и др.).
Среди основных вредностей окрасочных цехов - пары растворителей и разбавителей, окрасочная пыль, как в жидком, так и в твердом состоянии.
При расчете вентиляции метеорологические условия в окрасочных цехах должны принимаются как для помещений с незначительными тепловыделениями и категорией работ средней тяжести.
По взрыво-пожароопасности в окрасочных цехах встречаются помещения категорий А, Б, В, Г и Д.
Наиболее распространенными видами местных отсосов в окрасочных цехах являются вытяжные вентиляционные камеры.
Конструкция вытяжных вентиляционных камер зависит от способа окрашивания изделия или от способа нанесения на его поверхность различных составов.
Вытяжные вентиляционные камеры
Вытяжные вентиляционные камеры – полуоткрытые местные отсосы,
оборудованные вытяжной вентиляцией, внутри корпуса которых проходят технологические процессы с выделением вредных или токсичных компонентов.
В настоящее время выпускаемые вытяжные венткамеры оборудуются гидрофильтрами, через которые проходит воздух перед выпуском за пределы камеры.
Классификация вытяжных венткамер производится по конструкции гидрофильтров:
1. Вытяжная вентиляционная камера с лабиринтовым гидрофильтром
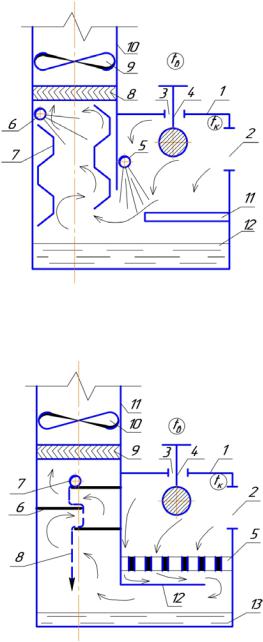
65
Рис. 6.1 Схема вытяжной камеры с
лабиринтовым гидрофильтром
1 – корпус камеры; 2 – рабочий проем; 3–технологический проем; 4–окрашиваемое изделие; 5 – форсунки водяного экрана; 6 – форсунки гидрофильтр; 7 –
лабиринтовый |
гидрофильтр; |
8 |
– |
|
каплеуловитель; 9 – вытяжной вентилятор |
|
|||
(устанавливается |
в теплом помещении); 10– |
|||
вытяжная шахта; 11– трап; |
12 – водяной |
|||
отстойник. |
|
|
|
|
2. Вытяжная вентиляционная камера с каскадным гидрофильтром и переливом
Рис. 6.2 Схема вытяжной камеры с
каскадным гидрофильтром
1 |
– корпус камеры; |
2 – рабочий проем; |
3–технологический проем; |
||
4–окраши-ваемое изделие; |
||
5 |
– перфорированный трап; 6 – каскад |
гидрофильтра;7 – перфорированная труба;
8– водяной экран – перелив;
9– каплеуловитель; 10 – вентилятор
(устанавливается в теплом помещении); 11 – вытяжная шахта; 12 – экран; 13 - водяной отстойник.
Отличительными конструктивными особенностями камеры являются:
1. ка скадная конструкция гидрофильтра 6 с перфорированной трубой 7 для
подачи |
воды на верхний каскад; |
2. |
перфор |
ированный трап 5 с экраном 12, для обеспечения равномерного всасывания по всей площади трапа и исключения образование застойных зон в камере.
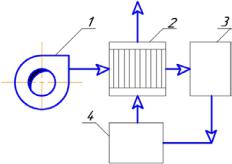
66
Подача воды осуществляется на верхний каскад сосредоточенно или через перфорацию. Переливные каскады создают сплошной экран воды на каждом уровне, что позволяет повысить степень очистки удаляемого воздуха.
Степень очистки газо-воздушной смеси зависит от скорости движения
воздуха в сечении гидрофильтра. |
|
|
|
||
Оптимальной |
считают |
скорость |
воздуха в |
гидрофильтрах |
|
в пределах 5…6 м/с. |
|
|
|
|
|
При этом степень очистки воздуха от лакокрасочного аэрозоля составляет |
|||||
90…95 %, от паров растворителя – 30…35 %. |
|
|
|||
Степень очистки воздуха от окрасочной пыли можно определить по |
|||||
формуле: |
|
|
|
|
|
|
|
|
к = 65 + 5·v, |
(6.1) |
|
где v – скорость воздуха в |
сечении гидрофильтра, м/с. |
|
|||
|
|
|
|
||
Аэродинамическое сопротивление гидрофильтра, Па, определяют по |
|||||
формуле: |
|
|
|
|
|
|
|
|
P = 16· v2, |
(6.2) |
|
где v – скорость воздуха в сечении гидрофильтра, м/с. |
|
||||
Низкая степень |
очистки |
от паров |
растворителей |
в гидрофильтрах |
приводит к загрязнению окружающего воздуха. Для обеспечения безопасных концентраций в приземном слое атмосферы воздух, содержащий пары растворителей после гидрофильтров либо подвергают дополнительной очистке в фильтрах другого типа, либо устраивают “факельный выброс”.
Одним из способов дополнительной очистки является окисление паров растворителей методом каталитического дожигания.
Рис. 6.3 Схема каталитического дожигания паров растворителей:
1– вентилятор; 2 – теплообменник; 3 - нагреватель; 4 – аппарат каталитического дожигания
67
Воздух на доочистку вентилятором 1 направляется в межтрубное пространство теплообменника 2, где нагревается до 300…350 оС за счет теплоты очищенного воздуха, проходящего по трубкам теплообменника 2. В электро - или газовом нагревателе 3 воздух нагревается до температуры 350…450 оС и направляется в контактный аппарат каталитического дожигания 4. В аппарате 4 происходит окисление паров растворителя с образованием углекислого газа и паров воды. Очищенный воздух поступает для охлаждения в теплообменник 2 и выбрасывается в атмосферу. Степень очистки достигает
99 %.
При выборе расчетных параметров воздуха рабочей зоны в окрасочных цехах принимают категорию работ средней тяжести II-а
по проектированию отопления и вентиляции окрасочных цехов и участков”).
Расчет производительности вытяжки из вентиляционных камер зависит от времени нахождения человека внутри камеры. В настоящее время существует два способа расчёта производительности вытяжной вентиляции из вытяжных вентиляционных камер
Способ 1: Расчёт производительности вытяжных вентиляционных камер
при кратковременном пребывании человека в камере. |
|
|
Расчет производительности, м3/ч, |
вытяжной системы вентиляции |
|
производится по зависимости: |
|
|
Lух = υдоп · Fпр · 3600 |
(6.3) |
|
Значение допустимой скорости в |
рабочем проеме камеры |
υдоп |
принимается в зависимости от способа окрашивания изделия и от токсичности образующихся компонентов (табл. 6.1).
Способ 2: Расчет производительности вытяжных вентиляционных камер
при постоянном пребывании человека в камере.
Расчет производится по количеству образующихся вредных выделений Gвр и предельно допустимым концентрациям соответствующих компонентов:
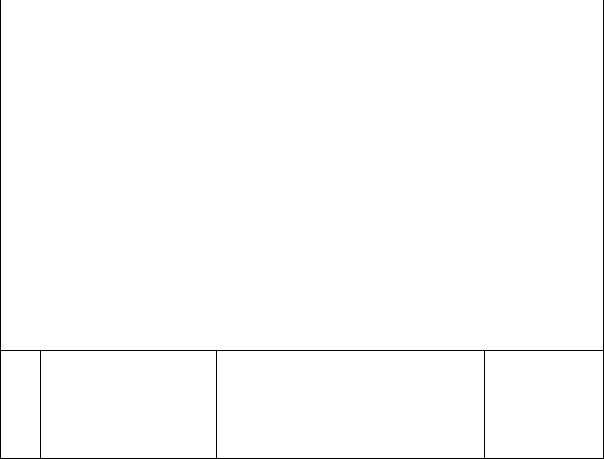
|
|
|
|
|
|
|
|
68 |
|
|
G |
10 6 |
|
|
|
||
Gух = |
|
вр |
|
|
|
|
, |
(6.4) |
|
сПДК |
|
|
с |
|
|||
|
|
|
|
− |
в |
|
|
|
|
|
ρк |
|
ρв |
|
|
|
|
|
|
|
|
|
|
|
Таблица 6.1
Допустимая скорость движения воздуха в рабочем проеме окрасочной камеры
|
|
|
|
№ |
Способ |
Применяемые материалы |
Расчетная |
средняя |
|||
п/п |
окрашивания |
|
скорость, м/с |
|
|
|
|
|
|
Ручное окрашивание |
|
1. |
Электростатическое |
Различные |
0,4..0,5 |
|
распыление |
|
|
|
|
|
|
2. |
Кисть, окунание, |
Не содержащие ароматических |
0,5 |
|
облив |
углеводородов |
|
|
|
||
|
|
Содержащие ароматические |
1,0 |
|
|
углеводороды |
|
|
|
|
|
3. |
Пневматическое |
Не содержащие соединений |
|
|
распыление |
свинца и ароматических |
1,0 |
|
|
углеводородов |
|
|
|
Эпоксидные, полиуретановые, |
1,7 |
|
|
акрилатные |
|
|
|
|
|
|
|
Автоматизированные методы |
|
1.Окунание, облив в Различные
стационарной |
|
0,4…0,5 |
|
установке |
|
|
|
2. Безвоздушное |
Содержащие соединения |
0,5 |
|
распыление |
свинца |
||
|
где Gвр – количество вредных выделений, образующихся в камере по каждому компоненту, кг/ч;
спдк, св – ПДК и концентрация данного компонента в рабочей зоне; ρк, ρв – плотности воздуха в камере и в рабочей зоне, кг/м3.
Расчет по зависимости (6.4) производится по каждому компоненту вредных выделений с учетом суммации их действия на организм человека. За
расчетное значение принимается большее из полученных значений.

69
Чтобы человек не получил профессиональных заболеваний концентрация вредных компонентов в камере не должна превышать предельно допустимой концентрации (ПДК).
Рис. 6.4 Схема вентиляции камеры окраски
в электростатическом поле
1 – корпус камеры; 2 - транспортные про емы; 3 – воздухоприемные короба; 4 – вытяжной вентилятор; 5 – фильтр.
Схема вентиляции автоматических камер электростатической окраски
показана на рисунке 6.4. В подобных камерах вентиляция может быть как вытяжной, так и приточно-вытяжной в зависимости от технологии окраски и требований, предъявляемых к качеству продукции.
Скорость воздуха в транспортных проемах должна составлять 0,4…0,5 м/с. Это исключает возможность “вырывания” загрязненного воздуха смежное помещение. Одновременно необходимо контролировать, чтобы концентрация паров растворителей в удаляемом воздухе не превышала 20 % нижнего предела взрываемости.
При наличии приточной вентиляции воздух подают в верхнюю зону камеры так, чтобы в зоне краскораспылителей подвижность воздуха не превышала 0,5 м/с.
Окрашивание электроосаждением осуществляется в специальных ваннах.
Удаление воздуха осуществляется через бортовые отсосы из расчета 50 м3/ч на 1 м3 емкости ванны.
Приточный воздух подается в верхнюю зону в объеме 75 % от объема вытяжного воздуха, т.е. Lп = 0,75 Lух.
70
Основные положения, используемые при конструировании систем вентиляции окрасочных цехов
В состав окрасочных цехов могут входить помещения категорий А, Б, В. При конструировании систем вентиляции следует учитывать требования действующих норм по обеспечению взрывопожаробезопасности.
Вытяжные системы:
1.Согласно требованиям АЗ-202 устройство аварийной вентиляции не требуется. Аварийная вентиляция проектируется в соответствии с техническим заданием.
2.Для контроля концентрации взрывоопасных веществ необходимо устанавливать сигнализаторы с настройкой на концентрацию 20 % от нижнего предела взрываемости. Сигнализаторы блокируются с вентиляционным оборудованием.
3.При кратности воздухообмена помещений окраски менее 5 ч-1 необходимо дополнительно предусматривать общеообменную вытяжку из подкровельного пространства с кратностью n = 1 ч -1 (0,4м от плоскости потолка).
Для помещений высотой более 6 м количество воздуха, удаляемого из верхней зоны определяют из расчета 6 м3/ч на 1 м2 площади пола.
4.Кратность воздухообмена в помещениях приготовления красок и лабораториях должна быть не менее 10 ч-1 .
Недостающий (дополнительный) воздухообмен обеспечивают за счет вытяжки из нижней зоны помещения.
5.Вытяжные вентиляторы должны конструироваться во взрывозащищенном исполнении. Для бесперебойной работы рекомендуется установка резервного вентилятора.
6.Удаление воздуха общеобменными местными системами должно осуществляться из верхней и нижней зон в соотношении 50/50.
7.Перед удалением воздуха из окрасочных цехов необходимо производить его очистку.
71
Приточные системы:
1.Приточный воздух следует подавать выше рабочей зоны так, чтобы скорость подаваемого воздуха вблизи открытых проемов местных отсосов не превышала 75 % от скорости всасывания в проеме.
2.Если в помещения категорий А и Б имеются выходы помещений других категорий, то они оборудуются тамбур-шлюзами. В тамбур-шлюзы подается воздух в размере не менее 250 м3/ч от самостоятельной приточной системы вентиляции с резервным вентилятором.
3.Приточные общеобменные системы должны обеспечивать воздухораспределение, исключающее пересечение траектории приточных струй с факелом вредных выделений.
Применение рециркуляции воздуха в окрасочных цехах не допускается.
7.СИСТЕМЫ ВЕНТИЛЯЦИИ СВАРОЧНЫХ ЦЕХОВ
7.1. Общие сведения о технологии сварки
При использовании сварки в производственных процессах осуществляют следующие основные операции:
1. Разметка деталей и узлов; 2. Резка; 3. Сборка деталей и узлов; 4. Предварительная (прихватка) и окончательная сварка
Сварочные процессы, включающие в себя сварку, резку и наплавку металлов, широко используются во многих отраслях промышленности при сборке различных изделий и конструкций.
Сборочно-сварочные цеха, как правило, характеризуются
незначительными тепловыделениями — до 23 Вт/м3. Выполняемые в них работы соответствуют категории работ средней тяжести.
Сварочные процессы могут выполняться вручную или в автоматическом (полуавтоматическом) режиме.
Наиболее распространены следующие сварочные технологии:
1.электродуговая сварка и наплавка электродами;
2.автоматическая электродуговая сварка под флюсом и в
72
среде защитных газов; Флюс – органическая присадка, предотвращающая разбрызгивание
расплавленного металла, исключающая контакт сварного шва с кислородом воздуха и снижающая ультрафиолетовую радиацию на рабочем месте.
В качестве защитной газовой среды применяют углекислый газ и инертные газы (аргон). При таком способе сварочная дуга защищена газовой оболочкой, не вступающей в контакт с расплавленным металлом и вытесняющей воздух из зоны сварки.
3. Электросварка и наплавка порошковой проволокой; Порошковая проволока представляет собой непрерывный электрод
трубчатой конструкции с порошкообразным наполнителем — сердечником. Назначение наполнителей подобно назначению электродных покрытий —
защита расплавленного металла от вредного воздействия воздуха. Порошковые проволоки используются для сварки без дополнительной
защиты зоны сварки, а также для сварки в защитных газах, под флюсом. 4. Электрошлаковая сварка;
Особенность способа – расплавленный металл в зоне сварки защищен “шлаковой ванной”.
Способ предназначен для соединения металлов и сплавов большой толщины. Технология данного способа возможна при толщине металла не менее 16 мм.
5. Электронно-лучевая сварка; Сущность процесса состоит в использовании кинетической энергии
потока электронов, движущихся с высокими скоростями в вакууме. Осуществляют с помощью электронной пушки.
6. Электрическая контактная сварка (точечная и стыковая); Сварка осуществляется за счет кратковременного плотного (под
давлением) соединения свариваемых деталей.
7. Плазменная обработка (сварка, резка, наплавление);
73
Способ высокотемпературной (по сравнению с температурой обычной дуги) обработки в среде ионизированного газа (плазмы) с помощью неплавящегося вольфрамового электрода.
8. Газовая обработка (сварка и резка).
Место проведения сварочных работ называется сварочным постом или постом сварщика.
Сварка мелких изделий производится на стационарных постах – на сварочных столах. Изготовление крупногабаритных изделий выполняется на специальных стендах.
Сварочные процессы сопровождаются выделением сварочного аэрозоля, содержащего мелкодисперсную твердую фазу и газы.
Сварочный аэрозоль может содержать:
1.Окислы металлов (железа, марганца, никеля, хрома, алюминия, меди и других веществ);
2.Оксид и диоксид углерода, оксиды азота, оксид и диоксид углерода, озон;
3.Газообразные фтористые соединения.
Интенсивность выделений зависит от:
1.технологии процесса;
2.марки и состава сварочных материалов (определяющее значение);
3.свариваемого металла.
При отсутствии правильно организованной вентиляции концентрация вредных веществ в зоне дыхания работающих может значительно превышать допустимую. Следствием этого является достаточно высокий по сравнению с другими профессиями уровень профессиональных заболеваний сварщиков: болезнь органов дыхания (пневмокониоз), отравление марганцем, парами других металлов и сварочными газами. Образующийся при электросварке аэрозоль обладает мелкой дисперсностью, низкой скоростью витания (<0,1 м/с) и, как следствие, высокой летучестью. Поэтому частицы аэрозоля легко следуют за воздушными потоками аналогично газам.
74
В сборочно-сварочных цехах применяют приточно-вытяжную общеообменную и местную, естественную и механическую вентиляцию.
Количество вредностей, удаляемых местной вытяжной вентиляцией определяют в зависимости от расхода сварочного материала (проволоки, электродов и т.д.) и принимают в размере 90 % - для вытяжных шкафов и 75 %
- от иных отсосов.
Оставшееся количество вредностей (соответственно 10 % и 25 %)
необходимо ассимилировать за счет общеобменной вентиляции.
7.2. Местная вытяжная вентиляция сварочных цехов
Типы местных отсосов для различных технологических операций и рекомендуемые расходы удаляемого воздуха приведены в справочной литературе (АЗ-499 Рекомендации по проектированию отопления и вентиляции заготовительных и сборочно-сварочных цехов).
Многообразие способов сварки, типов и размеров изготавливаемых изделий является причиной большого количества конструкций местных вытяжных устройств.
По принципу действия их делят на группы:
1.всасывающие панели;
2.подъемно-поворотные самофиксирующиеся вытяжные устройства;
3.переносные воздухоприемники с держателями;
4.местные отсосы, встроенные в сварочное оборудование;
5.местные отсосы, встроенные в оснастку рабочих мест автоматизированных и механизированных линий.
Всасывающие панели
1. Вертикальные панели В качестве примера рассмотрим одностороннюю всасывающую панель –
боковой местный отсос открытого типа. Подобные панели применяют на стационарных постах, где более полное укрытие невозможно.
Расчетные словия размещения панели:

75
1. b = от 0 до B; |
2. А = 1,2 а; |
3. Нижняя кромка всасывающего отверстия должна находится на уровне
верх источника выделения вредностей.
Рис. 7.1 Вертикальная всасывающая панель:
1 - всасывающая панель;
2 – источник вредных выделений.
.
Расход воздуха, удаляемый вертикальными панелями всасывания, зависит:
1. от конструкции панели и ее расположения;
2.геометрических размеров сварочного поста;
3.тепловой мощности конвективного потока от электрической дуги.
|
L |
ух |
= С |
пан |
3 |
Q (В+Н)5 |
, |
(7.1) |
|
|
|
|
к |
|
|||
где Спан |
– коэффициент, характеризующий конструкцию и размещение |
|||||||
|
вертикальной панели всасывания (по справочной литературе); |
|||||||
Qк – поток конвективной теплоты от электрической дуги, Вт |
|
|||||||
|
Qк = kсв · Pэл, |
(7.2) |
||||||
kсв |
– коэффициент, характеризующий условия проведения |
|
||||||
|
сварочных работ; |
|
|
|
|
|
|
kсв = 0,1 – при сварке под слоем флюса;
kсв = 0,25 – при обычной электродуговой сварке; kсв=0,3 – при сварке в среде углекислого газа.
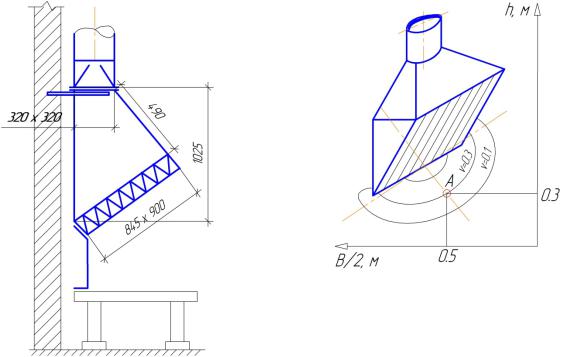
|
76 |
Pэл – мощность эл.тока, Вт: |
|
Pэл = I · U |
(7.3) |
При сварке применяют ток I ≤ 50 А; при резке - |
I > 50 А. |
В сборочно-сварочных цехах выполняются различные виды сварочных работ, поэтому разработана универсальная зависимость для расчета количества воздуха, удаляемого от сварочного поста:
Lух = kυ св · Lо, |
(7.4) |
где Lо – нормативный расход, приведенный в справочной литературе для конкретных видов сварочных работ;
kυ св – коэффициент запаса по скорости, учитывающий особенности проведения сварочного процесса (принимается из справочной литературы).
2. Наклонные панели (панели Чернобережского)
Среди наиболее распространенных видов местных отсосов - наклонные всасывающие панели. Они предназначены для постоянных рабочих мест для сварки небольших деталей.
Рис. 7.3 К расчету панели Чернобережского
В/2 – полуширина сварочного Рис. 7.2 Панель Чернобережского поста;
h – высота свариваемого изделия;
77
Расход удаляемого панелями воздуха определяется пропорционально пересчетом.
Например, при необходимости обеспечения нормального качества и условий сварки у точки сварки скорость должна быть 0,6 м/с (υо=0,6 м/с) при высоте свариваемого изделия h = 0,3 м и полуширине сварочного поста В/2 = 0,5 м (рис. 7.3). Требуется определить расход Lух.
Если определенное значение скорости по полям υп по вышеприведенным данным при нормируемом расходе (значение в точке А) υА = 0,3 м/с, то за расчетный расход удаляемого воздуха принимают значение Lух, определенное при υо = 0,6 м/с.
Также необходимый расход удаляемого воздуха может быть определен по
формуле |
|
Lух = 0,23 Fпан · vж.с.·3600, |
(7.5) |
где Fпан – габаритная площадь всасывающей панели, м2; |
|
vж.с – скорость воздуха в живом сечении, м/с; |
|
Для вредных паров и газов без пыли принимают vж.с = 2,0…3,5; то же с примесями горячей дисперсной пыли vж.с = 3,5…4,0.
Экспериментально установлено, что наиболее эффективно подобные панели работают при обеспечении удельных расходов:
-при установке вблизи стены Lуд = 3300 м3/ч на 1 м2 габаритной площади панели;
-при установке на удалении Lуд = 5000…7000 м3/(ч· м2).
Упостов резки металла удаление воздуха осуществляется через нижнюю зону стола сварщика с нижним подрешеточным пространством. Расход удаляемого воздуха определяется через удельный расход и площадь горизонтальной поверхности стола резки, выполненной в виде решетки:
Lух = kυ св · Lуд · Fст |
(7.6) |
где Lуд – удельный расход, м3/(м2·ч), значения которого
приведены в литературе в зависимости от особенностей условий

78
резки;
kυ св – коэффициент, корректирующий особенности резки на данном рабочем месте.
Для постов полуавтоматической и автоматической сварки расход удаляемого воздуха зависит от силы тока:
Lух = k1св 3 |
|
, |
(7.7) |
I |
где k1св – коэффициент, характеризующий условия сварки и конструкцию местного отсоса, принимается из справочной литературы.
Для щелевого отсоса k1св = 12; для отсоса-воронки k1св = 16.
Если в справочной литературе отсутствуют данные по объемам удаляемого воздуха для конкретных операций и типов отсосов, то расчет проводят по значению рекомендуемой скорости всасывания.
|
|
|
Таблица 7.1 |
|
Рекомендуемые значения скорости всасывания в проеме местных отсосов |
||
|
|
|
|
№ |
|
Технологическая операция |
Рекомендуемая скорость |
п/п |
|
воздуха, м/с |
|
|
|
||
|
|
Местные отсосы различных типов, кроме шкафов |
|
1. |
|
Ручная сварка |
0,5 |
|
|
|
|
2. |
|
Сварка в углекислом газе |
0,5 |
|
|
|
|
3. |
|
Сварка в инертных газах |
0,3 |
|
|
|
|
4. |
|
Газовая резка титановых сплавов |
1,0 |
|
|
|
|
|
|
Рабочие проемы вытяжных |
шкафов |
1. |
|
Сварка с применением электродов |
0,6 |
|
|
|
|
Современные местные отсосы на гибких воздуховодах
(подъемно-поворотные самофиксирующиеся
ипереносные вытяжные устройства)
Внастоящее время широкое применение получают системы из гибких воздуховодов, закреплённые на растяжках (подъемно-поворотные
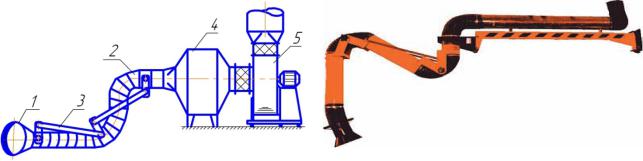
79
самофиксирующиеся вытяжные устройства). Они были разработаны шведской фирмой Plimyth и выпускаются совместным российско-шведским предприятием SovPlym (“Совплим”).
Отечественной промышленностью выпускаются аналогичные системы типа «Лиана» (рис. 7.4):
1 – диффузор (Ø 200÷315 мм); 2 – гибкий воздуховод с металлическими вставками на растяжках 3 (Ø 160÷180 мм); 4 –
электростатический фильтр;
5 – вентилятор высокого давления. Производительность вентилятора зависит от вида сварочных работ:
- при пайке L = 75÷400 м3/ч; - для сварочных работ L=400÷800
м3/ч.
Оптимальным считается расход L = 600÷800 м3/ч.
Рис. 7.4. Местные отсосы от сварочного оборудования
а– “Лиана”; б - “SovPlym”
1– диффузор (Ø 200÷315 мм); 2 – гибкий воздуховод (Ø 160÷180 мм) с металлическимивставками на растяжках 3;
4 – электростатический фильтр; 5 – вентилятор высокого давления.
Преимущества отсосов на гибких воздуховодах:
1.Являются наиболее универсальными и могут быть использованы при любых видах сварки как в нестационарных, так и в стационарных условиях;
2.Использование телескопических устройств и шарниров позволяет легко перемещать и устанавливать воздухоприемник в нужном положении;
3.Большой радиус обслуживания (до 8 м от места крепления устройства);
80
4.Максимальное приближение воздухоприемника к источнику выделения вредностей, что позволяет улавливать до 85% выделяющихся вредностей;
5.Удержание на фильтрах и фильтрующих устройствах (ФВУ) не менее 96% вредных веществ;
Применение местных отсосов в реальных условиях сварочных цехов бывает ограничено и даже невозможно по следующим причинам:
1) систематические изменения номенклатуры свариваемых изделий;
2) сварка крупногабаритных изделий;
3) отсутствие фиксированных мест сварки;
4) необходимость выполнения погрузочно-транспортных операций. Обеспечение требуемых условий воздушной среды в этих случаях
достигается общеобменной вентиляцией.
Из вышесказанного можно сделать следующие выводы об особенностях вентиляции промышленных зданий, где применяются сварочные технологии:
1.Воздушный режим на подобных производственных участках рассчитывается исходя из вида и конкретных условий проведения сварочных технологий, т.е. если на одном сварочном посту протекают различные операции сварочных работ, то необходимо устраивать систему вентиляции, позволяющую регулировать расход удаляемого воздуха при проведении определенного типа сварки.
2.В реальных условиях каждый сварочный пост имеет вытяжную местную систему, рассчитанную по доминирующей вредности данной технологической операции. Часть сварочного аэрозоля не улавливается местными отсосами и попадает в объем помещения. В результате в помещении постоянно накапливаются вредные вещества, которые необходимо дополнительно разбавлять до концентрации, не превышающей ПДК.
В приложениях (Л) СНиП 41-01-2003 и (17) СНиП 2.04.05-91* приведены расчетные формулы для определения количества приточного воздуха, необходимого для разбавления вредных веществ и компенсации вытяжки по доминирующим видам вредных веществ (наизусть):
|
|
|
81 |
Lпр = Lм.о. + |
mp оп − Lм.о. (ср.з. −спр) |
, |
(7.8) |
|
|||
|
сух −спр |
|
|
где mр.оп – количество вредных веществ (сварочного аэрозоля), |
|
||
попадающее в помещение, мг/ч. |
|
||
m р оп = (0,01÷0,25) m ро, |
(7.9) |
||
mро – количество вредного вещества, образующееся при сварочных |
|||
работах; |
|
Lм.о. – производительность местной вытяжной системы, м3/ч;
ср.з. – концентрация вредного вещества в рабочей зоне помещения, мг/м3; при отсутствии данных принимают ср.з = спдк;
спр – концентрация этих вредных веществ в приточном воздухе; при отсутствии данных принимают спр = 0,3 · спдк;
суд – концентрация вредных веществ в удаляемом воздухе; при отсутствии данных суд = ср.з..
Количество общеобменной вытяжки при этих условиях будет определяться как разность массового расхода приточного воздуха за вычетом массового расхода воздуха, удаляемого местными вытяжными системами.
Gух = Gпр – Gм.о. |
(7.10) |
7.3. Очистка удаляемого воздуха
Установки для очистки воздуха от сварочных газов можно разделить на 2
типа:
1.Передвижные установки для обслуживания одного или двух нестационарных постов с использование поворотной консоли, позволяющей эффективно удалять загрязненный воздух при сварке деталей сложной формы.
2.Стационарные установки для обслуживания стационарно
оборудованных |
постов. |
Все оборудование оснащено системой контроля загрязненности фильтров. Для очистки воздуха от сварочных аэрозолей наиболее эффективна
двухступенчатая система очистки:
82
-на первой ступени происходит очистка от аэрозолей;
-на второй ступени происходит очистка от газовой составляющей. В качестве первой ступени могут использоваться:
1. Электростатический фильтр позволяющий улавливать частицы
размером до 0,01 мкм и эффективностью 99%.
2. Картриджный фильтр из полиэстра, позволяющий улавливать частицы размером 0,1 мкм с эффективностью 99,9 %.
Отличием электростатического фильтра от картриджного является эксплуатационная характеристика - электростатический фильтр служит практически вечно, но требует тщательного еженедельного технического обслуживания – очистки фильтра, а картриджный фильтр очищается автоматически, путем импульсной продувки фильтра сжатым воздухом, но, как правило, срок службы картриджного фильтра не превышает 8000 часов.
На второй ступени используется фильтр из активированного угля. Наличие двухступенчатой очистки позволяет возвращать очищенный
воздух обратно в рабочее помещение, что обеспечивает значительную экономию тепловой энергии для поддержания температурного режима в помещении цеха.
Электростатические фильтры.
Вкачестве одного из вариантов современных очистных устройств компанией “Консар” (Россия) предлагаются электростатические фильтры
“ФВУ”.
Установки серии «ФВУ» предназначены для удаления и очистки воздуха от сварочного аэрозоля и газов. Выпускаются как в передвижном, так и в стационарном (для обслуживания нескольких постов) вариантах.
Вустановках использован принцип осаждения аэрозолей на электростатическом фильтре, что позволяет достигать высокой степени очистки воздуха и возвращать его в рабочее помещение.
Вустановках использована трехступенчатая система очистки загрязненного воздуха:
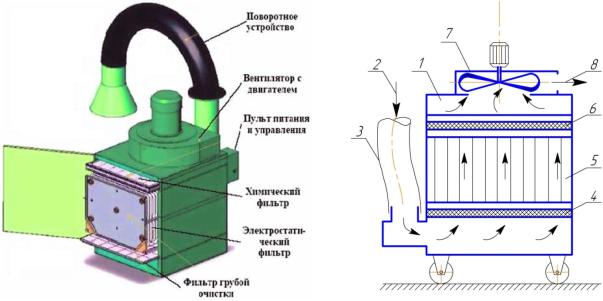
83
1 -я ступень – фильтр грубой очистки;
2-я ступень – электростатический фильтр;
3–я ступень – химический фильтр.
Химический фильтр производит очистку воздуха от газов CO, NOx,HF,
О3.
Установка состоит (рис. 7.5) из воздуховода (3), закрепленного на поворотном узле, вентилятора (7), фильтра грубой очистки (4), электростатического фильтра (5) и химического фильтра (6), выполненных в едином корпусе. Воздуховод (3) закреплен на шарнирно-поворотном механизме и вращается вокруг своей оси на 360°, что позволяет зафиксировать воздухоприемную воронку в любом пространственном положении обслуживаемой зоны. Радиус действия поворотного устройства 2,5 м.
Установки оборудованы автоматической системой контроля запыленности электростата с подачей светового сигнала.
Рис. 7.5. Элекстростатический фильтр ФВУ
Таблица 7.2
Технические характеристики фильтров ФВУ
|
|
|
|
84 |
|
|
|
|
|
|
|
№ |
Характеристики |
ФВУ-1200 |
ФВУ-2400 |
ФВУ-3500 |
|
п/п |
(передв.) |
(стац.) |
(стац.) |
||
|
|||||
1. |
Производительность, м3/ч |
1200 |
2400 |
3500 |
|
|
|
|
|
|
|
2. |
Степень очистки газообразной фазы, |
90 |
90 |
85 |
|
|
%, не менее |
|
|
|
|
3. |
Степень очистки твердой фазы, %, |
97 |
97 |
95 |
|
|
не менее |
|
|
|
|
4. |
Количество обслуживаемых постов |
1 |
2 |
4 |
|
|
|
|
|
|
Среди “картриджных” фильтров компанией “Консар” предлагается, например, установка серии “JETCLEAN” итальянского производства (“Coral”).
Установки (см. рис. ниже) предназначены для удаления и очистки воздуха от сварочных дымов, газов, паров, аэрозолей, растворителей, сухих пылей и т.д.
Достоинства:
1.Высокая степень очистки, позволяющая возвращать очищенный воздух в помещение;
2.Возможность многократной промывки фильтрующих картриджей;
3.Простота устройства и эксплуатации;
4.Низкий уровень шума.
Принцип работы .
В установках серии «JETCLEAN» применена двухступенчатая система очистки воздуха от сварочных газов.
Сначала сварочные дымы и газы и проходят через металлический лабиринтный фильтр, находящийся в камере предварительной очистки (4), расположенной сбоку. При этом крупные частицы осаждаются на специальный поддон. Металлический лабиринтный фильтр также выполняет роль искрогасителя. Далее воздух проходит через картриджные фильтры, которые являются второй ступенью очистки и выбрасывается в помещение.

85
Рис. 7.6 Передвижная установка для очистки воздуха “Jetclean”:
1 – корпус фильтра; 2 – вход загрязненного воздуха; 3 – поворотный патрубок от приемного устройства; 4 – лабиринтный фильтр грубой очистки;
5 - фильтрующий элемент-картриджи из полиэстера; 6 – вентилятор; 7 – выход очищенного воздуха.
Таблица 7.3
Технические характеристики фильтров “Jetclean”:
№ |
Характеристики |
1 HP |
1.5 |
3 HP |
|
п/п |
HP |
||||
|
|
|
|||
1. |
Производительность,м3/ч: с одним входом 150 мм |
1100 |
1400 |
1600 |
|
|
с двумя входами 150 мм |
|
|
|
|
|
--- |
--- |
2400 |
||
|
|
|
|
|
|
2. |
Степень очистки, % |
99,9 |
99,9 |
99,9 |
|
3. |
Количество картриджей |
1 |
2 |
2 |
7.4. Основы проектирования вентиляции сварочных цехов
Основные положения, используемые при конструировании систем вентиляции сборочно-сварочных цехов:
86
-При расчете вентиляции метеорологические условия в сборочносварочных цехах должны принимаются как для помещений с незначительными тепловыделениями и категорией работ средней тяжести.
-Для сварочных цехов оптимальным является сочетание местной вытяжной и общеобменной приточно-вытяжной механической вентиляции.
Вытяжные системы
1.При одновременном использовании сварочных материалов различного состава и с различным содержанием вредных выделений необходимый воздухообмен следует определять по вредности, преобладающей в объеме сварочного аэрозоля.
2.Предпочтительнее местные вытяжные системы конструировать из мобильных систем на гибких воздуховодах.
3.Применение рециркуляции воздуха в сварочных цехах должно быть обосновано.
4.Высокая эффективность современных очистных устройств позволяет использовать вытяжной воздух для частичной рециркуляцией. В этом случае в помещении обязательно конструируют общеобменную вытяжную систему с кратностью не менее 1 ч-1.
5.Системы местной вытяжной вентиляции компонуют в
зависимости от:
-видов образующихся вредных веществ;
-объемно-планировочных решений помещения;
-от расположения сварочных постов и оборудования;
-режима работы сварочного оборудования.
6. Общеобменную вентиляцию устраивают, как правило, по следующей схеме:
-естественная вытяжка из верхней зоны;
-механический приток в верхнюю или рабочую зону в зависимости от выполняемых операций (по АЗ-499).

87
7.Если сварочный цех имеет смежные проемы с цехами иного назначения вытяжка должна быть механической, независимо от наличия фонарей.
8.При газопламенной обработке металлов с применением сжиженных газов местные вытяжные устройства должны быть выполнены во взрывозащищенном исполнении.
Приточные системы
9.Воздухораспределение организуют в зависимости от расположения сварочных постов и технологии выполняемых операций.
10.Приточные струи не должны оказывать влияние на вытяжной факел местных отсосов.
Системы вентиляции, как показывает практика, должны иметь резервы увеличения мощности в связи с перспективами увеличения выпуска продукции
ивозможности минимальной реконструкции в соответствии с изменением номенклатуры выпускаемой продукции.
8.ВЕНТИЛЯЦИЯ МЕХАНИЧЕСКИХ ЦЕХОВ
Вмеханосборочных цехах осуществляются различные виды механической
обработки металлических изделий.
Основным оборудованием являются токарные, фрезерные, сверлильные,
заточные, шлифовальные и др. станки.
Основными вредностями являются избыточная теплота, влага и пыль. При работе станков с применением для охлаждения резцов минеральных масел и эмульсий источником загрязнения являются пары этих жидкостей (смазочно-
охлаждающие жидкости).
8.1.Местная вытяжная вентиляция механических цехов
Взаточных, полировальных и шлифовальных отделениях обязательно устанавливают местные вытяжные установки для удаления пыли от работающих станков, если они не имеют встроенных пылеулавливающих и

88
пылеочистных устройств. В зависимости от технологического процесса и конструкции станков последние оборудуются местными отсосами различных конструкций.
Основными видами местных отсосов этих цехов являются кожухи-
воздухоприемники. Кожухи-воздухоприемники
Кожухи-воздухоприемники – открытые местные отсосы, удаляющие воздух с примесями абразивной пыли от шлифовального, полировального, обдирочного и заточного оборудования.
Количество воздуха, удаляемого местными отсосами, определяется физико-химическими свойствами частиц отходов.
Факел местного отсоса должен полностью улавливать частицы отходов и удалять их за пределы оборудования.
Так как кожухи-воздухоприёмники помимо укрытия режущего элемента защищает человека от травм, то их часто называют защитно-обеспыливающими кожухами.
Рис. 8.1 Кожух-укрытие для шлифовальных,
полировальных и обдирочных станков
1 - отводящий патрубок;
2 – кожух-воздухоприемник;
3 – режущий инструмент;
4 – обрабатываемое изделие.
Аэродинамические характеристики кожухов для шлифовального,
полировального и обдирочного оборудования: υвх = 14÷18 м/с; ξ = 1,5. Аэродинамические характеристики кожухов для заточного оборудования:
υвх = 17÷21 м/с; ξ = 3,0.
Аэродинамические характеристики кожухов приведены в справочной литературе в зависимости от физико-химических свойств отходов и конструкции местного отсоса.
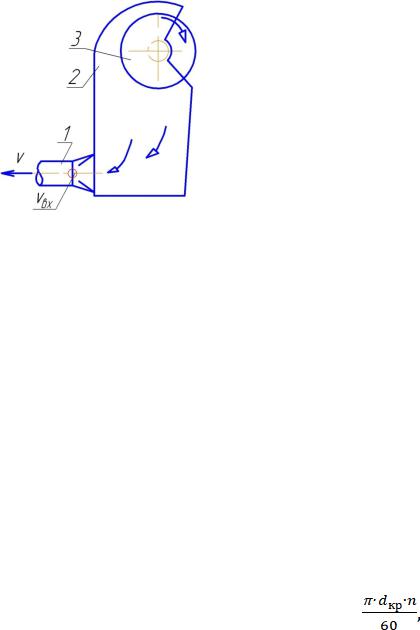
89
Рис. 8.2 Кожух-укрытие для заточного станка:
1 – отводящий патрубок;
2 – кожух-воздухоприемник;
3 – абразивный круг.
υвх – скорость в ответвлении местной системы в характерной точке (ось присоединения патрубка местного отсоса).
Для станков с любыми кругами расход удаляемого воздуха определяется по выражению:
L = υвх · F · 3600, |
(8.1) |
где F – площадь поперечного сечения присоединенного патрубка. Скорость воздуха в воздухоприемном отверстии может быть определена в
зависимости от направления движения загрязненного воздуха:
-при направлении непосредственно в отверстие кожуха υвх = 0,25 υо.с.;
-параллельно плоскости всасывания кожуха υвх = (0,3…0,4) υо.с.,
где υо.с. – максимальная окружная скорость вращения круга, м/с.
|
|
υо.с. = |
|
|
(8.2) |
где dкр – диаметр круга, мм; n – частота вращения круга, об/мин. |
|
||||
Для |
заточных, |
шлифовальных |
и |
полировальных |
станков |
ориентировочные значения |
расходов L, м3/ч, |
определяют в зависимости от |
диаметра кругов табл. 8.1).
Часто у технологического оборудования механосборочных цехов пылезащитные кожухи имеют форму воронки. Такие кожухивоздухоприёмники называются кожухами-воронками.

90
Таблица 8.1
Ориентировочная производительность по воздуху местных отсосов от заточных станков
Для абразивных кругов |
Для полировальных кругов |
||
L, м3/ч |
d, мм |
L, м3/ч |
Материал круга |
|
|
|
|
2 d |
≤ 250 мм |
6 d |
матерчатый |
|
|
|
|
1,8 d |
250÷600 |
4 d |
войлочный |
|
|
|
|
1,6 d |
> 600 мм |
|
|
|
|
|
|
Рис. 8.3 Кожух-воронка:
1 – отводящий патрубок;
2 – кожух-воронка;
3 – режущий инструмент;
4 – обрабатываемая деталь.
Расход воздуха, удаляемого от кожухов-воронок, рассчитывается на максимальную производительность технологического оборудования.
Расход зависит от скорости воздуха на входе в воронку υк, скорости воздуха на выходе из нее υн и расстояния от воронки до места образования отходов l:
L = 3600· υн· l2· |
, |
(8.3) |
где kк – коэффициент, характеризирующий конструкцию (форму) воронки: для воронок круглой формы kк = 7,7; прямоугольной
kк = 9,1.
Данные приводятся в справочной литературе в зависимости от технологического оборудования, физико-химических свойств примесей и расположения воронки.
91
8.2. Основы проектирования вентиляции механических цехов
Основные положения при проектировании систем вентиляции
Вытяжные системы:
1. Системы вентиляции компонуются по видам отходов и в зависимости от объемно-планировочных решений помещения.
2.Местные вытяжные системы, удаляющие от станков сухую пыль и аэрозоль со смазочноохлаждающими жидкостями, должны быть раздельными.
3.Местные отсосы от станков мокрой шлифовки должны быть снабжены каплеуловителями (сепараторами).
4.Воздуховоды местных вытяжных систем, удаляющих пары смазочноохлаждающих жидкостей, должны иметь дренажные устройства.
5.Воздуховоды, в которых транспортируются пары масел, должны
выполняться с учетом требований пожароопасности. 6. Местные вытяжные системы, удаляющие от станков пары масел, сухую или влажную пыль, должны оборудоваться установками для очистки воздуха
перед выбросом в атмосферу.
7. При установке вентилятора местной вытяжной системы перед циклоном (сепаратором) необходимо использовать пылевые вентагрегаты.
8. Если фильтр или сепаратор расположены перед вентилятором, то устанавливают вентилятор обычного исполнения, но среднего или высокого давления.
Приточные системы:
9.Воздухораспределение должно быть таким, чтобы приточные струи не оказывали влияние на всасывающий факел местных отсосов.
10. Подача приточного воздуха допускается сосредоточенными турбулентными струями.
92
9.ВЕНТИЛЯЦИЯ ДЕРЕВООБРАБАТЫВАЮЩИХ ЦЕХОВ
9.1.Общие сведения о технологии деревообработки
Вдеревообрабатывающих цехах (ДОЦ) осуществляют различные виды обработки древесины и сборку готовых деталей и изделий.
ДОЦ состоят из следующих основных производств:
1.раскроечно-строгальное; 2. станочное 3. столярно-сборочное;
4.малярное и сушильное отделения;
5.клее- и краскоприготовительный участки. Технологические операции в основных производственных
подразделениях осуществляются на следующих станках и оборудовании:
1.Станки для распиловки: круглопильные и ленточные;
2.Станки для первичной обработки: строгальный, фуговальный, рейсмусовый;
3.Станки для специальной обработки: сверлильный, фрезерный, шипорезный, прирезной и др.;
4.Станки для финишной обработки: шлифовальный и др.
5.Стенды для склеивания деталей;
6.Оборудование для сушки и декоративного покрытия готовых изделий.
Основные вредности ДОЦ:
1. |
опилки, стружка и древесная пыль; 2. избыт. теплота и влага |
- в суш. |
отделении; |
|
|
3. |
пары клея, р-лей красок и лаков; 4. нажд. и металл. пыль - |
в отделении |
заточки.
Метеорологические условия в деревообрабатывающих цехах принимают как для помещений с незначительными избытками явной теплоты и категорией работ средней тяжести.
Вытяжные системы в ДОЦ представлены в основном системами аспирации и пневмотранспорта.
93
9.2. Системы аспирации и пневмотранспорта
Система пневмотранспорта – механическая система вентиляции, транспортирующая измельченный кусковой материал в смеси с воздухом.
Система аспирации – механическая система вентиляции, транспортирующая мелкодисперсные пыль, дым или капельные аэрозоли веществ в смеси с воздухом (с концентрацией < 50 г/кг воздуха).
Системы аспирации и пневмотранспорта нашли широкое применение в сельскохозяйственной, пищевой, мукомольной, сахарной, деревообрабатывающей и цементной промышленности.
Системы аспирации и пневмотранспорта предназначены не только для удаления отходов, они также являются технологическими системами для перемещения материалов и полуфабрикатов между различными помещениями цеха.
В ДОЦ станки оборудованы пылезащитными кожухами, выполняющими функции местных отсосов и защищающие человека от режущих элементов.
Применяются местные отсосы как отдельные элементы вытяжных систем различного вида (укрытия, воронки ит.п.), так и отсосы, встроенные в корпус технологического оборудования
Методика подбора местных отсосов в ДОЦ аналогична расчету и подбору отсосов в механосборочных цехах.
Из-за многообразия технологического оборудования по обработке древесины существует большое количество различных типов местных отсосов систем аспирации и пневмотранспорта в ДОЦ. Типовые конструкции местных отсосов деревообрабатывающих станков промышленного изготовления приведены в типовой серии 4.904-3 «Местные отсосы и укрытия к технологическому оборудованию деревообрабатывающей промышленности».
В серии приведены схемы размещения местных отсосов у наиболее часто встречающихся типов станков, даны схемы присоединения отсосов и их аэродинамические характеристики. Часть сведений из данной серии приведены

94
в справочнике проектировщика под редакций Павлова Н.Н. Шиллера Ю.И. (часть 3):
|
|
|
|
|
Таблица 9.1 |
|
Основные характеристики местных отсосов от станков |
||||||
|
|
|
|
|
|
|
|
Миним.объем |
Коэффициент |
Потери |
Минимальная |
Расположение |
|
Наименование |
отсасыва- |
гидравлического |
скорость в |
|||
станка |
емого воздуха |
сопротивления |
давления |
воздуховодах, |
и схема |
|
при Lmin, Па |
воздуховодов |
|||||
|
Lmin, м3/ч |
ζ |
vmin, м/с |
|||
Станок |
|
|
|
|
|
|
фрезерный |
1350 |
0,8 |
39,1 |
18 |
См. рис. 9.1 |
|
Ф-4 |
|
|
|
|
|
Рис. 9.1 Схема размещения местного отсоса от станка
Классификация систем аспирации и пневмотранспорта
Существуют различные варианты классификации систем, отличающиеся в основном выбором в качестве классификационных тех, или иных конструктивных признаков, и, поэтому, не имеют принципиальных отличий.
1.По назначению:
-Внутрицеховые системы, являются разветвленными с большим количеством местных сопротивлений.
-Межцеховые системы - линейные системы с небольшим количеством местных сопротивлений.
2.По способу циркуляции:
-Прямоточные – загрязненный воздух после очистки выбрасывается в атмосферу.
95
- Рециркуляционные – очищенный вытяжной воздух частично или полностью возвращается в производственное помещение.
3. По характеру связи с технологическим оборудованием:
- Централизованные - системы, к которым подключено несколько видов оборудования с независимым включением и выключением, т.е. одновременность их работы не является обязательной. Централизованные системы могут быть выполнены как системы с переменной производительностью.
-Автономные - системы, обслуживающие один или несколько видов технологического оборудования, включаемых и выключаемых одновременно. В таких системах по условиям технологии всегда требуется отбирать одинаковый объем воздуха, т.е. автономные системы не могут быть системами с переменной производительностью.
4. По гидравлическому режиму:
-Системы с постоянной производительностью.
-Системы с переменной производительностью.
5.По давлению:
-системы низкого давления, ∆Рпод < 5 кПа;
-системы среднего давления, 5 ≤ ∆Рпод ≤ 20 кПа;
-системы высокого давления, ∆Рпод > 20 кПа.
9.3.Теоретические основы расчета систем
аспирации и пневмотранспорта
При рассмотрении вопросов, связанных с расчетом и конструированием систем аспирации и пневмотранспорта часто встречаются такие основополагающие для данных расчетов понятия, как скорость витания,
скорость трогания, относительная скорость и транспортирующая скорость.
Скорость витания
Понятие скорости витания используется при расчете вертикальных участков систем аспирации и пневмотранспорта.

96
Если частицу твердого вещества массой m отпустить, то под действием силы тяжести P она начинает падать с ускорением свободного падения g.
Воздух будет оказывать сопротивление R
движению частицы, и постепенно движение частицы станет равномерным (υ = const, g = 0). В вязкой среде скорость её падения не может возрастать бесконечно. В некоторый момент времени её значение достигает некоторого наибольшего значения vs, которое сохраняется на протяжении последующего времени падения.
Если частицу разместить в восходящем потоке в
вертикальном канале, то при определенной скорости сила сопротивления среды R станет равна силе тяжести частицы P. В этом случае скорость движения частицы относительно стенок канала будет равна нулю, то есть частица будет находиться во взвешенном состоянии (витать).
Скорость восходящего потока vs, при которой частица не будет иметь вертикального перемещения, равна постоянной
скорости падения частицы в неподвижном воздухе. Такая скорость называется скоростью витания частицы, т.е. по сути это скорость восходящего потока в канале.
На частицу, двигающуюся вниз в восходящем потоке воздуха действуют две силы: сила тяжести P = mg, направленная вниз и сила сопротивления воздуха R = k· , направленная вверх.
R = k· – сопротивление вязкой среды при средних скоростях пропорционально квадрату скорости; k – коэффициент пропорциональности.
При достижении состояния “витания” будет справедливо равенство
P = R, или mg = k·,

|
|
97 |
откуда |
= |
(9.1) |
Сопротивление, которое оказывает воздух движущемуся телу выражается следующей зависимостью:
R = c·F· ·ρв , |
(9.2) |
где с – коэффициент, зависящий от режима течения жидкости.
с = f (Re);
F – площадь проекции движущейся частицы на плоскость, перпендикулярную вектору скорости, м2.
Иногда эту характеристику называют “парусностью” частицы
ρв - плотность воздуха, кг/м3. |
|
|
|
|
Учитывая, что R = ks · υs2, можно выразить значение ks: |
|
|||
ks = c F |
ρв |
, |
(9.3) |
|
2 |
||||
|
|
|
тогда, подставив выражение (9.3) в ( 9.1), формула для определения скорости витания примет вид:
|
|
|
|
|
|
υs = |
2mg |
(9.4) |
|||
c F ρв |
|||||
|
|
|
|
По данным экспериментальных исследований, проведенных Л.С.Клячко для мелкодисперсных фракций опытный коэффициент с может быть определен по зависимостям:
- при значениях числа Рейнольдса, не превышающих Re = 2000
с |
= |
24 |
+ |
|
4 |
|
(9.5) |
|
Re |
|
|
|
|||||
Re |
||||||||
|
|
|
|
|
|
- при значениях Re < 1
(9.6)
Эмпирические зависимости для определения скорости витания древесных отходов были получены в лесотехнической академии им. С.М. Кирова:

|
|
|
|
|
|
|
|
|
98 |
|
|
|
|
|
|
|
|
|
|
υs =0,14 |
|
ρ м |
|
|
, |
(9.7) |
|||
|
0,02 + |
a |
ρ |
|
|||||
|
|
|
|
в |
|
||||
|
|
|
|
h |
|
|
где а – коэффициент, характеризующий форму частиц в поперечном сечении: для квадрата а = 1,1; для окружности а = 1; для прямоугольника а = 0,9.
h – высота (толщина) частицы, мм;
ρм, ρв – соответственно плотность материала и воздуха, кг/м3.
Для обеспечения надежной работы системы скорости потока воздуха υв на вертикальных участках должны быть больше скорости витания υs.
Скорость трогания
Рассмотрим силы, действующие на частицу, лежащую на внутренней поверхности горизонтального канала, по которому движется воздух со скоростью v:
P – сила тяжести;
R – сила давления потока воздуха; F – сила реакции опоры;
Fтр – сила трения.
На стороне частицы в которую направлен вектор скорости v создается некоторое избыточное давление. При определенной скорости воздушного потока она сдвинется с места и начнет движение в направлении движения воздуха.
Минимальная скорость, при которой частица начинает движение,
называется скоростью трогания.
При |
определенной |
скорости |
|
потока (большей, чем скорость трогания) |
|||
подъемная |
сила |
на |
нижней |
гране |
частицы |
может превысить |
|
значение силы тяжести P. В этом случае |
|||
частица оторвется |
от поверхности и |
начнет перемещаться в потоке воздуха.
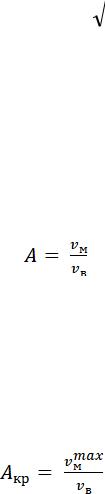
99
В некоторой точке траектории силы, действующие на частицу снизу и сверху будут равны и под действием силы тяжести она начнет опускаться вниз до касания со стенкой канала. Траектория движения частицы на горизонтальном участке в потоке воздуха имеет форму циклоиды. С увеличением скорости движения частицы будет изменяться продолжительность циклов “подъем-падение”.
Для древесных отходов предложено (Л.С. Клячко) использовать следующую зависимость для определения скорости трогания:
υт =1,3 3 |
|
|
ρм |
(9.8) |
Относительная скорость
Твердая частица в воздушном потоке движется всегда со скоростью меньшей, чем скорость воздуха.
Для расчета систем аспирации и пневмотранспорта пользуются понятием относительной скорости движения материала, которая представляет собой отношение скорости материала vм к скорости воздушного потока vв:
(9.9)
В начале движения (трогания) относительная скорость равна 0. Т.к. скорость воздуха всегда выше скорости материала, то А всегда меньше 1 (А<1).
На определенном участке траектории частица имеет максимальную скорость υмmax, называемую критической. Относительная скорость при этом значении называется относительной критической скоростью.
(9.10)
Критическая скорость в горизонтальных участках воздуховодов зависит
от:
1. |
Формы и размера частиц; |
2. |
Концентрации частиц в воздушной |
|
смеси; |
3. |
Плотности воздуха. |
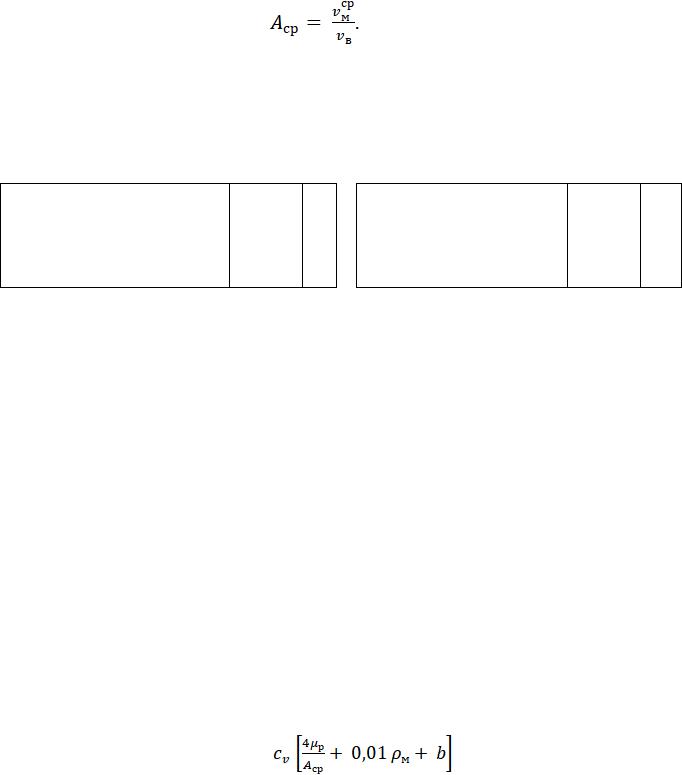
100
Иногда в расчетах используется понятие средней относительной скорости Аср
(9.11)
В справочной литературе (см. табл.) приводятся рекомендуемые значения средних относительных скоростей для различных видов твердых примесей.
Таблица 9.2 Рекомендуемая средняя относительная скорость твердых примесей
Транспортируемый материал |
Аср при |
b |
|
Транспортируемый |
Аср при |
b |
|
μ ≤ 2 |
|
|
материал |
μ ≤ 2 |
|
Опилки мелкие |
0,9 |
7 |
|
Щепа длиной до 35 мм |
0,7 |
11 |
|
|
|
|
|
|
|
Стружка мелкая |
0,85 |
9 |
|
То же, более 40 мм |
0,6 |
13 |
μ = – массовая расходная концентрация древесно-воздушной смеси;
b – опытный коэффициент, характеризующий вид перемещаемого материала.
Для обеспечения устойчивого перемещения материалов системами аспирации и пневмотранспорта скорости на различных участках системы должны быть больше скоростей витания, трогания. Такие скорости называются
транспортирующими.
Транспортирующая скорость
Транспортирующая скорость – это скорость воздушного потока, при которой обеспечивается надежная работа системы по перемещению материалов без образования “пробок”.
Транспортирующая скорость на горизонтальном участке определяется по зависимости, предложенной ЛТА им. Кирова :
vтр. гор. = · |
, |
(9.12) |
где Сv – коэффициент, характеризующий изменение скорости воздушного потока в местном сопротивлении.
Сv = 1,1…1,15 – для внутрицеховых систем с большим числом
101
|
отводов; |
Сv = 1,05…1,10 – для межцеховых систем протяженностью до 30 м; |
|
Сv = 1,0 |
– для межцеховых систем протяженностью более 30 м. |
ρм – плотность перемещаемого материала, кг/м3. μр и b – см. выше.
Формула справедлива для измельченных древесных отходов при значении μ ≤ 2.
Результаты экспериментальных исследований ряда авторов показывают, что для полидисперсной смеси (стружки, опилки …) транспортирующая скорость в горизонтальных участках должна находиться в пределах
vтр. гор = (1,5…2,0) vs.
В вертикальных участках систем аспирации ипневмотранспорта скорость должна быть выше, т.к. движение с той же скоростью, что и в горизонтальных участках приводит под действием силы тяжести частиц к постепенному росту концентрации смеси. Увеличение концентрации может привести к засору вертикальных участков, чему способствуют и фасонные части (отводы), устанавливаемые при переходе к вертикальным участкам.
Для предотвращения засоров в вертикальных участках, скорость в них увеличивают по сравнению с горизонтальными на величину скорости витания, т.е.
υтр.верт = υтр.гор. + υs. |
(9.13) |
На разных участках системы скорости могут быть различны, поэтому для обеспечения надежности работы системы используют различные приемы.
Метод 1
При конструировании систем аспирации и пневмотранспорта на горизонтальном участке перед отводом на вертикальный (за 5…6 диаметров) изменяют диаметр в меньшую сторону, так чтобы увеличить скорость потока на вертикальном участке.

102
Метод 2
Является наиболее распространенным способом.
Система конструируется и рассчитывается таким образом, чтобы на каждом из участков выполнялось условие
(9.14)
В вышеприведенной таблице с характеристиками местных отсосов от деревообрабатывающего оборудования дана минимальная скорость, которая является минимальной транспортирующей скоростью υmin.
9.4. Определение потерь давления в системе при подъёме материала
При подъеме материала на высоту h должна быть затрачена работа, значение которой может быть определено по формуле
Lв · ∆Рпод = Gм · h · g, (9.15)
где Lв – объемный расход воздуха, м3/ч;
∆Рпод – потери давления при подъеме материала, Па; Gм – массовый расход материала, кг/ч.
Выразив объемный расход воздуха через массовый, получим
Gв Рпод =Gм h g .
ρ в
Тогда потери давления на подъем материала равны
Р |
= |
Gм h ρв g , |
|
под |
|
G |
123 |
|
|
{ в |
γв |
|
|
µ р |
|
(9.16)
(9.17)
∆Рпод = μр · h · γв |
(9.18) |
Потери давления при подъеме материала на отметку h зависят от массовой концентрации материала, от высоты подъема и удельного веса транспортирующего воздуха.
Расчет потерь давления в воздуховодах, по которым перемещается смесь древесных отходов и воздуха Δpсм проводят как для обычного (”чистого”)
103
воздуха Δp с использованием поправочных коэффициентов на транспорт материала (уравнение И.Гастерштадта):
Δpсм = Δp (1 + k·μ), (9.19)
где k – опытный коэффициент сопротивления древесно-воздушной смеси, определяемый по справочной литературе в зависимости от состава смеси и диаметра воздуховода.
9.5. Особенности конструирования систем аспирации и пневмотранспорта
1.Так как пылевые вентиляторы имеют высокий уровень звукового давления (высокие характеристики по шуму), то их размещают снаружи здания.
2.Древесные отходы относятся к горючим веществам, поэтому между циклоном и стеной здания необходимо предусматривать противопожарный разрыв не менее 10 м.
3.Системы конструируются с пылевым вентилятором, если через них проходит смесь воздуха и древесных отходов, т.е. циклон или сепаратор находится после вентилятора по ходу движения воздуха. Если циклон или сепаратор размещаются до вентилятора по ходу движения воздуха, то применяют вентилятор обычного исполнения, но среднего или высокого давления.
4.Воздуховоды систем конструируются по временной нормали для
проектирования АЗ -187 (“Временная нормаль на металлические воздуховоды круглого сечения для систем аспирации”):
-применяются воздуховоды только круглого сечения;
-используется сталь с толщиной δ = 1 мм и более;
-воздуховоды соединяются на фланцах, они являются сварными и относятся к классу плотных;
-радиус изгиба отводов должен составлять 2D, полуотводы имеют угол поворота 30°, 45° и 60° с радиусом загиба 2D;
-тройники и крестовины имеют углы врезки под 30° или 45°.