
9534
.pdfкачества исходного проката и готовой продукции металлоконструкций, а именно: при оценке качества сварных соединений, определения толщины изделий и элементов конструкций, оценке несплошностей листового проката (наличие пор, шлаковых включений, расслоений) и т.д.
2. СИСТЕМА ТЕХНИЧЕСКОГО КОНТРОЛЯ В СВАРОЧНОМ ПРОИЗВОДСТВЕ
Важнейшей функцией системы организации производства продукции предприятием-изготовителем является ее технический контроль, под которым понимают проверку соответствия объекта контроля установленным техническим требованиям.
Система технического контроля предусматривает организацию на предприятии службы технического контроля, которая, наряду с технологическими службами, должна обеспечивать высокое качество выпускаемой продукции.
Система технического контроля включает следующие основные элементы:
-объект контроля;
-метод и средства контроля;
-исполнители;
-техническая документация.
Под объектом контроля понимают продукцию на той или иной стадии технологического процесса, средства производства и технологические процессы.
Метод контроля – это совокупность определенных принципов и правил выполнения контроля.
К средствам контроля относят контрольно-измерительные приборы, инструменты, аппаратуру, материалы, применяемые при контроле (например, рентгеновская пленка).
Под исполнителями контроля понимают специалистов отдела технического контроля (ОТК) и работников центральной заводской лаборатории (ЦЗЛ), работников лаборатории неразрушающего контроля занимающейся поверкой и ремонтом средств измерения.
При техническом контроле выявляют отклонения объекта контроля от установленных требований нормативно-технической документации (НТД).
Технический контроль проводится в соответствии с технической документацей и организуется по правилам, установленным стандартом предприятия.
Сущность технического контроля определяется выполнением двух следующих функций:
-получение информации о фактическом состоянии объекта контроля, его контролируемых параметрах и показателях качества (эту информацию называют первичной);
-сопоставление первичной информации с установленными требованиями, критериями и нормами (информация об отклонениях фактических параметров и показателей качества от заданных называется вторичной).
Вторичная информация используется для выработки управляющего решения, направленного на объект контроля. При этом решается главная задача управления качеством – сведение к минимуму или полное устранение выявленных отклонений в ходе технологического процесса изготовления продукции.
Помимо отмеченных к другим понятиям, используемым при контроле относятся:
-объем контроля – отношение общего количества проконтролированных объектов к общему количеству изготовленных;
-продолжительность контроля – время, необходимое для его подготовки, проведения и анализа результатов;
-стоимость контроля – материальные затраты на проведение контроля;
-контролируемый параметр – количественная или качественная характеристика объекта контроля;
-достоверность контроля – вероятность соответствия фактических результатов действительным значениям контролируемых признаков.
3.ВИДЫ И СРЕДСТВА ТЕХНИЧЕСКОГО КОНТРОЛЯ
Взависимости от требований к сварным соединениям и категории их ответственности устанавливается определенная система организации контроля продукции на предприятии. В основу этой системы положена классификация видов технического контроля по отдельным признакам.
1. По стадиям технологического процесса контроль разделяют на: а) входной (предварительный); б) операционный (текущий);
в) окончательный (готовой продукции).
К входному контролю предъявляют основной и сварочный материалы (присадочную проволоку, флюсы, газы, электроды), полуфабрикаты и комплектующие. Под термином предварительный контроль понимают не только проверку материала, но и работоспособности сварочного оборудования и квалификации исполнителей работ.
Операционному контролю подвергают технологические процессы по отдельным операциям маршрутной технологии после ее завершения или во время исполнения.
2. По объему контролируемой продукции: а) сплошной; б) выборочный.
Сплошной контроль выполняют для ответственных сварных конструкций. Выборочный – при контроле изделий крупносерийного и массового
производства.
3. По месту проведения контроля: а) стационарный; б) подвижный (скользящий).
Стационарный контроль производится на специально оборудованном контрольном пункте или в специальном помещении (например, рентгеноконтроль выполняют в изолированных боксах).
Подвижный контроль производится непосредственно на рабочем месте (например, ультразвуковой контроль):
4. По характеру контроля: а) инспекционный; б) летучий.
Под инспекционным контролем понимают выборочный контроль продукции специальными лицами (инспекторами) для дополнительной проверки качества проконтролированной продукции.
Летучий контроль выполняется с произвольной периодичностью, носит инспекционный характер и выполняется работниками ОТК. При этом контролируется соблюдение технологических процессов (контроль технологической дисциплины), например, последовательность выполнения швов, соблюдение правил хранения и условий транспортировки изделий на соответствие требованиям технической документации.
При проверке соблюдения технологического процесса особое внимание уделяется рациональной организации рабочих мест, которая предполагает наличие необходимой технологической документации, оснастки, контрольноизмерительных приборов, инструмента и их состояния, соблюдения правил и норм техники безопасности, состояние рабочего места и соответствие его требованиям технологической документации. Такую проверку часто называют контролем производственной дисциплины.
5. По цели контроля: а) приемочный; б) статистический.
Приемочный контроль имеет отбраковочный характер и проводится с целью отделения годной продукции от брака. Статистический контроль используется в крупносерийном и массовом производстве в системе управления качеством продукции.
Статистический контроль является средством профилактического воздействия на ход технологического процесса с целью его корректировки и исключения появления брака.
6. По возможности использования проконтролированной продукции: а) разрушающий; б) неразрушающий.
Разрушающий контроль применяют для получения контролируемых количественных показателей продукции. В некоторых случаях контроль проводят с частичным нарушением целостности материала изделия, т.е. путем испытаний без разрушения изделия.
Неразрушающий контроль не оказывает влияния на целостность продукции
икосвенно характеризует ее качество.
7.По средствам контроля и получения информации: а) визуальный;
б) инструментальный.
Визуальному контролю подвергают 100% изделий.
Инструментальный контроль является более совершенным, т.к. осуществляется с помощью разнообразных технических средств контроля. Технические средства контроля можно разделить на следующие группы.
По характеру измерения контролируемого параметра: а) контрольно-измерительные инструменты и приборы; б) контрольно-сортирующие устройства.
Контрольно-измерительные средства являются основными средствами контроля. Контрольно-сортирующие средства предназначены для сортировки объектов контроля по двум группам: годен, негоден; либо по нескольким группам, исходя, например, из геометрических размеров. По степени воздействия на ход технологического процесса:
а) средства пассивного контроля; б) средства активного контроля.
Средства пассивного контроля относятся к обычным контрольноизмерительным средствам, фиксирующим полученный результат или контрольносортирующим устройствам. Средства активного контроля встраиваются в технологическое оборудование и используются для непосредственного управления технологическими процессами. При достижении предельных значений контролируемых параметров эти устройства автоматически управляют режимом работы оборудования, обеспечивают заданную точность и обладают значительно большей эффективностью предупреждения брака.
По степени автоматизации: а) ручные; б) механизированные;
в) автоматические.
Средства ручного контроля используют там, где применение механизированных и автоматических контрольных устройств затруднено или практически невозможно. Эффективность использования автоматических контролирующих устройств обусловлено возможностью получения документа или протоколирования результатов контроля. При использовании механизированных средств контроля протоколирование результатов контроля осуществляет контролер.
4. ВЫБОР МЕТОДОВ ДЕФЕКТОСКОПИИ СВАРНЫХ СОЕДИНЕНИЙ
Методы дефектоскопии относятся к методам неразрушающего контроля сварных швов. Их используют с целью выявления дефектов – несплошностей.
На практике известно десять видов неразрушающего контроля, разделяющихся на методы в зависимости от способа выявления дефектов.
Основными методами контроля дефектов-несплошностей сварных соединений являются радиографический и радиоскопический, ультразвуковой, магнитопорошковый и магнитографический, капиллярный, вихретоковый, течеисканием, визуальный и визуально-оптический. Каждый из методов имеет
свои особенности и область применения. Основные факторы, определяющие применимость методов, сводятся к следующим:
Физические свойства материала:
Радиационные методы используют для контроля любых конструкционных материалов, магнитные - для ферромагнитных материалов (металлы на основе Fe, Ni, Co), а вихретоковый - для электропроводящих материалов.
Толщина и размеры изделия:
Радиационный и ультразвуковой контроль используют для сварных соединений различной толщины, а вихретоковый и магнитный контроль для малых толщин.
Состояние поверхности:
При ультразвуковом контроле необходимо зачищать контролируемый участок сварного соединения с нанесением контактной смазки. В магнитном контроле необходимо снимать чрезмерное усиление шва. Особенностью капиллярного контроля является особо тщательная подготовка поверхности.
Характеристики дефектов:
При выявлении объёмных дефектов (поры, включения) рационален радиационный контроль, а плоскостных (трещины, непровары) – ультразвуковой, магнитный и вихретоковый контроль.
Дефекты, расположенные в поверхностном слое наиболее надежно выявляются вихретоковым, капиллярным и магнитным контролем, а внутренние дефекты – радиационным и акустическим.
Размеры допустимых дефектов:
Размеры допустимых дефектов определяют технические условия на отбраковку сварных швов и зависят от условий эксплуатации сварных изделий.
Технические характеристики:
Основными техническими характеристиками методов неразрушающего контроля являются чувствительность, разрешающая способность и достоверность.
Чувствительность метода определяется наименьшими размерами выявляемых дефектов, разрешающая способность – наименьшими расстояниями между двумя соседними выявляемыми дефектами; достоверность – вероятностью пропуска дефектов с недопустимыми размерами.
Радиационные методы контроля чувствительны к объемным и плоскостным дефектам, расположенным в направлении просвечивания, ультразвуковые методы
— к любым плоскостным внутренним дефектам, а магнитные и капиллярные методы – к плоским поверхностным дефектам. Эти же методы имеют высокую разрешающую способность и достоверность контроля.
Технико-экономические показатели:
К технико-экономическим показателям контроля относят производительность, возможность механизации и автоматизации, доступность технических средств, возможность документирования результатов, стоимость контроля и др.
Самым непроизводительным является рентгенографический контроль.
Ультразвуковой и вихретоковые методы контроля обладают высокой производительностью, а также возможностью обработки, хранения и регистрации дефектоскопической информации.
Условия выполнения контроля:
При использовании радиационного контроля необходимо тщательно контролировать радиационную обстановку в производственных помещениях и использовать специальные меры защиты. Остальные методы контроля используют при условии выполнения общих требований по технике безопасности и эксплуатации оборудования.
5. ФИЗИЧЕСКИЕ ОСНОВЫ УЛЬТРАЗВУКОВОГО МЕТОДА
5.1. Параметры ультразвуковой волны
Ультразвуковыми колебаниями называются такие механические колебания, частота которых лежит за верхним порогом слышимости человеческого уха. За нижний предел ультразвука принята частота колебаний 15 кГц, а за верхний –
1000 МГц.
Распространение ультразвуковых колебаний в различных веществах зависит от их состава, структуры и свойств на кристаллическом и молекулярном уровнях.
Для случая плоской волны распространение ультразвуковых колебаний описывается формулой
|
a Asin t x / c , |
(5.1) |
где a - |
смещение частицы среды относительно точки покоя, |
м; A - амплитуда |
смещения, м; x - координата рассматриваемой точки, м; 2 f |
- угловая частота, |
|
рад/сек; |
f - частота колебаний, гЦ; c - скорость распространения ультразвуковых |
колебаний, м/сек.
Как видно из выражения (5.1), распространение ультразвуковой волны представляет собой пространственно-временной процесс.
Обычно при исследовании этого процесса рассматривают его параметры либо в определенной точке пространства x0 , либо в определенный момент
времени t0 . В первом случае выражение (5.1) примет следующий вид: |
|
a Asin t 0 . |
(5.2) |
Это выражение описывает синусоидальное колебание частицы среды,
расположенной в точке x0 . Величина 0 x0 / c определяет начальную |
фазу |
колебаний. |
|
Во втором случае из выражения (5.1) получим: |
|
a Asin t0 x / c . |
(5.3) |
Это выражение описывает периодический процесс распространения ультразвуковой волны в направлении координаты x .

Для характеристики волнового процесса вводится понятие длины волны ( ). Длиной волны называется расстояние, которое она проходит за один
период колебаний T ( T 1/ f ).
Виды колебаний. Различают продольные и поперечные колебания ультразвуковой волны. При продольных колебаниях частицы среды совершают колебания в направлении распространения волны, а при поперечных колебаниях частицы среды совершают колебания перпендикулярно направлению распространения волны. В газах и жидкостях могут распространяться лишь продольные ультразвуковые волны, а в твердых телах – как продольные, так и поперечные волны.
Скорость ультразвука. Скорость распространения продольных ультразвуковых волн в большинстве твердых тел находится в пределах 2000…6000м/сек, причем в конструкционных металлах она составляет 4000…6000м/сек, а в пластмассах 2000…3000м/сек.
Скорости распространения поперечных сt и продольных сl |
волн различны, |
но между собой взаимосвязаны. Их отношение зависит от |
коэффициента |
Пуассона : |
|
|
|
|
|||
|
|
|
|
|
|
|
|
|
ct |
|
1 2 |
. |
(5.4) |
||
|
|
|
|||||
|
cl |
2 2 |
|
||||
Так как в конструкционных строительных материалах коэффициент |
|||||||
Пуассона имеет значения, близкие к 0,3 , то скорость поперечных |
волн |
||||||
примерно в 2 раза меньше скорости продольных волн. |
|
Амплитуда, давление, интенсивность. Основными параметрами,
характеризующими ультразвуковые колебания, являются амплитуда, давление и интенсивность. Эти параметры зависят от мощности излучателя ультразвуковых
колебаний и среды, в которой они происходят. |
|
|
Амплитуда давления P и амплитуда смещения частиц |
среды A |
|
функционально взаимосвязаны: |
|
|
P 0,1A c Н / м2 |
, |
(5.5) |
где - плотность материала среды (кг/м3). Остальные параметры в (5.5) имеют следующие размерности: с - м/сек, - 1/с и А - м.
Интенсивностью ультразвука I называется величина звуковой энергии, проходящая в единицу времени через единичную площадку, расположенную перпендикулярно к направлению распространения волны. Интенсивность обычно измеряется в вт/см2. Однако на практике часто используется логарифмическая величина - уровень силы звука, измеряемый в децибелах (дБ). Эта величина представляет собой удесятеренный логарифм отношения заданной интенсивности ультразвука к пороговому значению, которое принимается равным I 10 16 вт / см2 , что соответствует нижнему порогу слышимости для звуковых колебаний.
Между интенсивностью ультразвуковых колебаний I , амплитудой А и
давлением P существуют следующие зависимости: |
|
|||||
I |
1 |
c A 2 |
; |
(5.6) |
||
2 |
||||||
|
|
|
|
|
||
|
|
P |
|
|
||
I |
|
. |
|
(5.7) |
||
200 c |
|
Акустическое сопротивление среды. Из выражений (5.6) и (5.7) следует,
что интенсивность ультразвуковых колебаний I зависит от произведения плотности среды на скорость распространения ультразвука с в ней. Это произведение называется акустическим или волновым сопротивлением среды.
Величины акустического сопротивления некоторых веществ для продольных сl и поперечных волн сt приведены в табл. 5.1.
Т а б л и ц а 5.1
Величины акустических сопротивлений продольных и поперечных ультразвуковых волн в различных веществах, кгм-2с-110-6
с |
Воздух |
Вода |
Трансформ. масло |
Сталь |
Алюминий |
Латунь |
Медь |
Фарфор |
Орг. стекло |
Полистирол |
|
||||||||||
|
|
|
|
|
|
|
|
|
|
|
сl |
0,00043 |
1,5 |
1,28 |
45,6 |
16,8 |
35,9 |
41,8 |
12,9 |
3,21 |
2,49 |
|
|
|
|
|
|
|
|
|
|
|
сt |
--- |
--- |
--- |
25,2 |
8,32 |
17,2 |
20,1 |
7,52 |
1,35 |
1,19 |
|
|
|
|
|
|
|
|
|
|
|
5.2. Излучение и прием ультразвука
Ультразвуковые колебания могут возбуждаться различными способами, основанными на использовании разнообразных физических явлений. В экспериментальной технике широкое распространение получили следующие типы излучателей ультразвука: механические (аэродинамические и гидродинамические), электродинамические, магнитострикционные, пьезоэлектрические и др. Каждый из указанных типов излучателей имеет свою область применения, зависящую в основном от возможных диапазонов генерации ультразвуковых частот колебаний и передаваемых мощностей.
В ультразвуковых приборах чаще всего для излучения и приема колебаний применяются пьезоэлементы из кварца, из керамик титанита бария и других синтетических пьезокристаллических материалов.
Возможность применения таких элементов для излучения и приема ультразвука основана на пьезокристаллическом эффекте. При сжатии и растяжении некоторых кристаллов в определенных направлениях на их поверхностях возникают электрические заряды. Это явление в физике называют
пьезоэлектрическим эффектом. Возможен и обратный эффект. Если приложить к поверхностям этих кристаллов электрическое напряжение, то кристалл соответственно растянется или сожмется. Таким образом, в пьезокристаллах механические колебания преобразуются в переменное электрическое напряжение (прямой пьезоэффект), а переменное электрическое напряжение преобразуется в механические колебания (обратный пьезоэффект). Прямой пьезоэффект используется в приемниках ультразвуковых колебаний, а обратный – в излучателях.
5.3. Принцип работы приборов ультразвукового контроля
При падении ультразвуковой волны на границу раздела двух сред, обладающих разными акустическими сопротивлениями, часть энергии проходит во вторую среду, а часть отражается обратно. При этом процесс отражения и преломления ультразвуковой волны осуществляется по тем же законам, что и свет, и в первую очередь зависит от угла падения волны (угла между направлением распространения волны и нормалью к поверхности раздела сред).
Этим явлением обусловливается возможность решения задач по поиску дефектов в виде трещин и инородных включений как при оценке качества сварных соединений, так и при определении сплошности материала, определении толщины контролируемых элементов конструкций и сооружений и т.д.
Рассмотрим работу источника ультразвуковых колебаний, установленного на поверхность исследуемого элемента 1 конструкции (рис. 5.1).
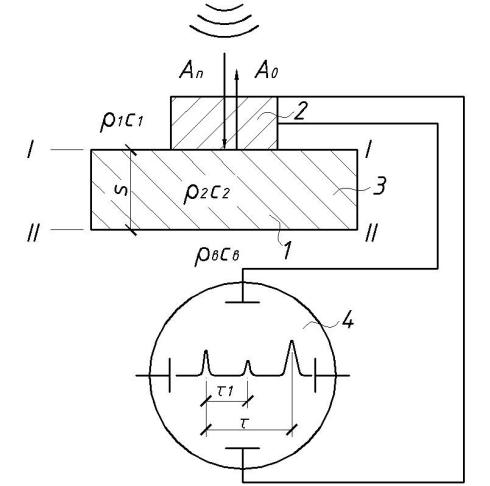
Рис. 5.1. Физический принцип работы ультразвукового дефектоскопа
Генерируемые кварцевой пластинкой 2 механические колебания распространяются по излучателю и достигают границы раздела двух сред I-I (материал излучателя – материал конструкции).
На границе раздела происходит отражение и преломление акустических волн. При этом отраженная волна имеет амплитуду:
|
А А |
|
1с1 |
2с2 |
, |
(5.8) |
|
|
|
|
|||||
|
0 |
п |
|
1с1 |
2с2 |
|
|
|
|
|
|
|
|
||
где 1с1 |
и 2с2 - акустическое сопротивление первой и второй сред. |
|
В соответствии с приведенным выше уравнением, если акустические сопротивления значительно отличаются друг от друга, то происходит почти полное отражение ультразвуковой волны, и колебания во вторую среду не проникают. Это предопределяет необходимость согласования акустических сопротивлений излучателя и материала, обеспечивающего введение в
исследуемую среду колебаний определенной амплитуды.
Прошедшая ультразвуковая волна распространяется в исследуемой среде со скоростью с2 и достигает нижней границы II-II исследуемого материала. Если третьей средой является воздух, который имеет акустическое сопротивлениев св 2с2 , то происходит практически полное отражение; волна возвращается по