
9117
.pdf
21
1
1
2 |
MAX |
|
|
|
MIN |
MAX MIN
Рис. 2.12. Регулировка подачи смеси с помощью лопастных датчиков: 1 – лопастной датчик; 2 - скребковый конвейер; min, max- уровень смеси
Другим вариантом контроля процесса является применение ультразвуко-
вых или сенсорных датчиков (рис. 2.13). Они отличаются высокой точностью из-
мерений, простотой регулировки заданной толщины (количества) укладываемого
(подаваемого) материала без соприкосновения с ним.
Для исключения прессования смеси при её транспортировке в шнековую камеру ленточным питателям придается дополнительный наклон назад. Скорость ленты регулируется плавно в интервале 0 - 24 м/мин. Дальнейшее распределение смеси по ширине укладки ведется при помощи двух независимых винтовых кон-
вейеров или шнеков. Каждая секция имеет свою навивку спирали - левую и пра-
вую соответственно. Шнек подает смесь на половину ширины укладки от сере-
дины к краям. Привод шнеков цепной или гидравлический.
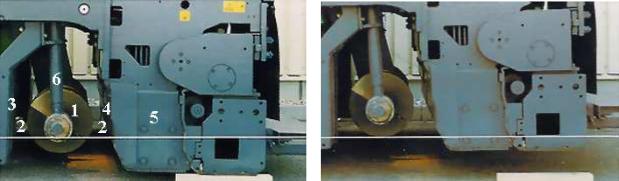
22
Рис. 2.13. Регулировка подачи смеси с помощью ультразвуковых датчиков: 1 – датчик уровня смеси в шнековой камере; 2 – датчик контроля питателей
Валы с размещенными на них лопастями вращаются в подшипниках скольжения, установленных в приводной (центральной) части и кронштейнах на задней стенке рамы асфальтоукладчика. В зависимости от мощности двигателя диаметр шнеков может изменяться от 250 до 480 мм. Лопасти (сегменты) явля-
ются сменными. Высотное положение шнека может плавно регулироваться с по-
мощью гидроцилиндров или вручную в пределах 15 см (рис. 2.14). Гидравличе-
ская регулировка позволяет наклонять шнеки параллельно плоскости подошвы выглаживающей плиты. Большой диаметр распределительных шнеков и опти-
мальная форма лопастей обеспечивают интенсивную подачу смеси при малом вращающем моменте.
Рис. 2.14. Регулировка высоты шнека: 1 – шнек; 2 – шнековая камера; 3 – передний щит; 4 – отражательный щит; 5 – рабочий орган; 6 – кронштейн крепления шнека
Частота вращения валов переменная до 70 об/мин, также регулируемая вручную или автоматически. Конвейеры работают в массе материала, расположенного в шнековой камере. Она образуется четырьмя щитами: передним (задняя часть ра-
мы), задним (отражательным) и двумя боковыми (скользящая опалубка). Днищем камеры служит основание дороги. Ширина шнековой камеры может изменяться в соответствии с шириной полосы укладки. Стандартная длина шнека равна базо-
вой ширине рабочего органа или её минимальному значению, указанному в пас-
порте машины. При укладке смесей на ширину полосы в пределах регулирования с помощью гидравлики (брус системы «Vario»), как правило, распределение ма-
териала ведут без изменения длины шнеков. Однако при укладке с уширенными рабочими органами требуется дополнительное удлинение шнеков. Для этого с
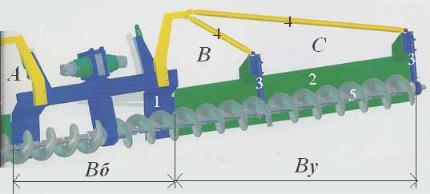
23
помощью специальных несущих балок навешивают добавочные секции с перед-
ним щитом. На этой же оснастке имеются кронштейны, с помощью которых за-
крепляют дополнительные звенья винтового конвейера. Для обеспечения попе-
речной жесткости вновь монтируемой конструкции её дополнительно раскреп-
ляют с помощью металлических тяг в передней части по отношению к асфальто-
укладчику. Крепление балок и тяг осуществляют к раме машины (рис. 2.15).
Для удлинения, как правило, применяют секции стандартных размеров,
имеющиеся в ЗИПе к машине. На рис. 2.16 показаны варианты удлинения шне-
ков на примере асфальтоукладчиков фирмы «Vogele».
На асфальтоукладчики может дополнительно устанавливаться система дымоудаления (рис. 2.17), которая с помощью вентиляторов отсасывает дым и горячие газы из туннеля питателей и шнековой камеры, направляя их в специаль-
ную трубу. Выхлопная труба выведена на верхнюю раму асфальтоукладчика впе-
реди оператора на 1,0 м выше головы и направлена в сторону от него. Такой си-
стемой оборудованы, например, машины американской фирмы «Roadtec». При транспортировке труба складывается. Производительность системы из двух вен-
тиляторов составляет 120 м3/мин.

24
Рис. 2.15. Удлинение шнеков асфальтоукладчика: 1 – привод шнеков; 2 – удлиненный передний щит; 3 – дополнительные кронштейны; 4 – несущие балки; 5 – удлиненный шнек; 6 – тяги; 7 – рама машины; А, В, С – секции; Вб - базовая длина шнека; Ву – удлиненный участок шнека
Рис. 2.16. Варианты удлинения шнеков фирмы «Vogele»
Рис. 2.17. Система дымоудаления асфальтоукладчика: 1 – выхлопная труба
25
2.3. Блок рабочих органов
Рабочие органы асфальтоукладчика выполняют основные функции по укладке смеси, включая уплотнение и выравнивание поверхности покрытия. Блок рабочих органов (рис. 2.18) шарнирно соединен с нижней рамой машины с по-
мощью двух тяговых брусьев или лонжеронов. Возможность вертикального пе-
ремещения лонжеронов относительно переднего нижнего шарнира обеспечивает-
ся нивелировочными гидроцилиндрами. Органы управления цилиндрами распо-
ложены на площадке машиниста и (или) на выносных пультах по бокам рабочих органов. На современных асфальтоукладчиках с помощью нивелировочных ци-
линдров независимо друг от друга можно устанавливать или изменять толщину укладываемого слоя. Ориентиром для установки отметки поверхности покрытия являются масштабные шкалы, работающие синхронно с нивелировочными гид-
роцилиндрами.
Гидроподъемники служат для приведения (поднятия) рабочих органов в транспортное положение. В рабочем положении эти цилиндры не мешают верти-
кальному перемещению концов лонжеронов.
Рабочие органы состоят из выглаживающей плиты и уплотняющего обору-
дования. Выглаживающая плита (рис. 2.19) при ее базовой ширине, как правило,
состоит из двух шарнирно сочлененных между собой металлических каркасов,
поворачивающихся в вертикальной плоскости, а также узлов регулирования по-
перечного профиля (толщины) укладываемого слоя и системы обогрева. Каркас плиты выполнен из листового металла толщиной 16 мм с поперечными ребрами жесткости. Нижняя рабочая грань плиты имеет гладкую поверхность, над кото-
рой устроена камера для прогрева подошвы плиты. В верхней ее части располо-
жен отсек для технологического оборудования (привода уплотняющих органов,
гидросистемы и т.п.).
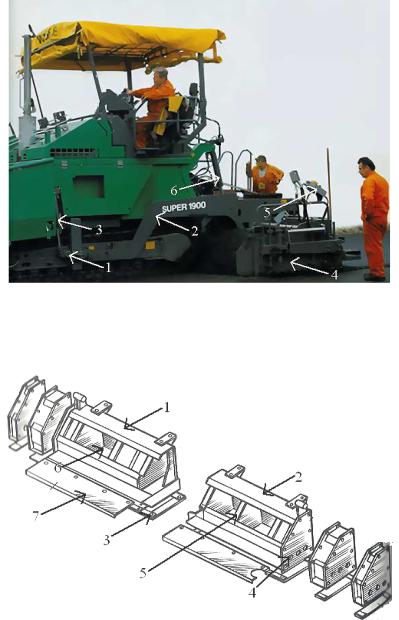
26
Рис. 2.18. Рабочие органы асфальтоукладчика: 1 – шарнир; 2 – лонжерон; 3 - нивелировочный цилиндр; 4 - рабочие органы; 5 - выносной пульт управления (ПУ); 6 – гидроподъемник
Рис. 2.19. Каркас выглаживающей плиты: 1,2 – левая и правая секции каркаса соответственно; 3- подошва плиты; 4 – камера для обогрева плиты; 5 – ребра жесткости; 6 - технологический отсек; 7 – рабочий настил
На старых и некоторых новых моделях асфальтоукладчиков по внешним краям каркасов (рис. 2.20) расположены механические регуляторы толщины.
Они выполнены в виде вантовой стяжки, соединяющей концы тяговых брусьев и выглаживающей плиты. С помощью винтов 2 можно устанавливать расстояние между плитой 4 и брусом 5. При этом происходит изменение толщины укладыва-
емого слоя и соответственно угла наклона всей плоскости плиты по отношению к горизонту, что является грубой настройкой рабочего оборудования. На совре-
менных укладчиках толщину слоя выставляют нивелировочными цилиндрами с

27
визуальным контролем по масштабным шкалам или по выносным пультам
управления.
Рис. 2.20. Механическая регулировка поперечного профиля плиты: I - регулятор толщины; II - регулятор поперечного профиля; 1 – соединительный шарнир; 2 – вантовая стяжка;
3 – винт; 4 – плита; 5 – тяговый брус; а) – горизонтальный профиль; б) – односкатный профиль; в) – двускатный профиль
Регулятор поперечного профиля располагается посередине выглаживаю-
щей плиты, т.е. между секциями. Вращение центральной муфты 3 на винтовой стяжке приводит либо к выравниванию концов левой и правой половин плиты в месте шарнира, либо к их излому. Для придания покрытию горизонтального профиля внешние края плиты с помощью нивелировочных цилиндров (регулято-
ров толщины) располагают на одном уровне. При необходимости получения од-
носкатного профиля один из краев следует опустить ниже другого. Двускатный профиль получается, когда внешние края плиты будут опущены ниже соедини-
тельного шарнира 1. В зависимости от модификации укладчика корректировка поперечного положения плиты может производиться в диапазоне +50 ÷ -40 мм с углом излома -2% ÷ +5 %. Настройка поперечного профиля ведется до начала ра-
бот.
Конструкция рабочего органа асфальтоукладчиков предполагает, что в процессе работы выглаживающая плита, благодаря своему плавающему положе-
нию по отношению к укладываемой смеси, способна самопроизвольно сглажи-

28
вать локальные дефекты профиля поверхности основания. Опорной точкой для нивелирования продольных отклонений плиты является шарнир А (рис. 2.21), находящийся всегда в жестко фиксированном положении по отношению к раме машины.
Рис. 2.21. Схема самопроизвольного устранения неровностей основания
При наезде укладчика на неровность точка В крепления лонжерона к ниве-
лировочному цилиндру поднимется или опустится на высоту Н. В соответствии с правилом рычага (2.1) из-за разности в длине плеч «а» и «b» передний по ходу движения край плиты также изменит своё высотное положение на величину «h».
Так, естественным образом происходит выравнивание вертикальных перемеще-
ний передней части плиты в соотношении примерно 1:5 по сравнению с ампли-
тудой колебаний поверхности основания при наличии неровностей в пределах базовой длины асфальтоукладчика. Устранение дефектов продольного профиля,
выходящих за указанные пределы, требует дополнительного применения автома-
тики нивелирования.
h = H · а /b . |
(2.1) |
При движении асфальтоукладчика передний край основания плиты под действием внешних сил (рис. 2.22) всегда приподнят относительно укладываемо-
го слоя на величину угла атаки, зависящего от рабочей скорости, вида смеси,
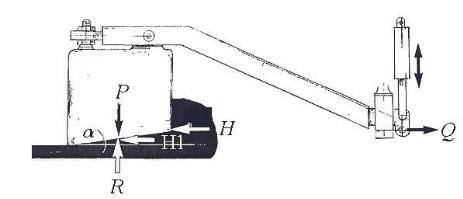
29
температуры укладки и прочих факторов. Практический опыт показывает, что ровность поверхности покрытия обеспечивается при условии, если в процессе укладки все силы находятся в состоянии равновесия, т.е. Q, P, R, H1, H = const.
Причем наиболее вероятным изменениям при укладке подвержено гори-
зонтальное усилие на лобовую часть плиты со стороны смеси, которое зависит от ее количества в шнековой камере.
Рис. 2.22. Схема к определению угла атаки плиты: Q – тяговое усилие; P - вес плиты;
R – реакция на вес плиты (отпор смеси); H1 – сопротивление материала трению; H – лобовое сопротивление смеси; α – угол атаки плиты
До начала работ угол атаки, т.е. угол между плоскостью основания плиты и поверхностью укладываемого слоя, устанавливают с помощью регуляторов толщины или нивелировочных цилиндров (грубая настройка). В процессе работы при нарушении технологического режима подачи смеси в шнековую камеру ав-
томатически меняется соотношение сил, действующих на плиту. При этом плита занимает новое высотное положение: опускается вниз (недостаток смеси) либо поднимается вверх (избыток смеси). Данное явление служит одной из причин возникновения неровностей продольного профиля покрытия, вызывая его иска-
жение. Таким образом, поддержание стабильного давления материала на перед-
нюю часть выглаживающей плиты является главным фактором получения слоя постоянной толщины. Управление настройкой угла атаки в процессе работы сле-
дует производить путем подъема или опускания концов тяговых брусьев с помо-
щью нивелировочных цилиндров, приводя всю систему в первоначальное состо-
яние. Данный вид настройки является более точным по сравнению с регулятором толщины. Он обеспечивает стабильность положения рабочих органов в продоль-
30
ном и поперечном направлениях укладываемого покрытия. Управление концами тяговых брусьев может производиться в ручном или автоматическом режиме, т.е.
с применением автоматики нивелирования.
Система обогрева предназначена для разогрева рабочей поверхности пли-
ты до температуры, соответствующей температуре укладываемой смеси (1200С).
При несоблюдении данного соответствия на поверхности покрытия могут обра-
зоваться дефекты по его ровности или текстуре. Механизм обогрева плиты может работать на жидком, газообразном топливе или с применением электропрогрева.
При работе на дизельном топливе оно поступает из общего бака в рабочую камеру, где смешивается с воздухом и воспламеняется от свечи. Продукты сгора-
ния с помощью вентилятора нагнетаются в лабиринты камеры плиты, нагревая её поверхность. Рабочая камера, как правило, располагается в технологическом от-
секе центральной части плиты.
В качестве газообразного топлива используют газ пропан, хранящийся в съемных баллонах на верхней раме асфальтоукладчика. Сгорание топлива проис-
ходит в 4 газовых горелках, зажигаемых электричеством.
Плиты с электрическим прогревом являются более предпочтительными с точки зрения экологической безопасности из-за отсутствия токсичных испарений и твердого осадка. При этом увеличивается срок службы плиты вследствие устранения неравномерной деформации зеркал ее основания и уменьшения тер-
мического напряжения в рамной конструкции. Источником электроэнергии явля-
ется 3-х фазный генератор постоянного тока с гидроприводом. При таком спосо-
бе зеркало плиты равномерно нагревается по всей плоскости. Нагревательные элементы из нержавеющей стали передают тепло пластинам из алюминия, распо-
ложенным непосредственно на зеркале плиты, что устраняет традиционные «го-
рячие точки», возникающие при работе горелок. Фактическая температура срав-
нивается с заданным значением и регулируется с помощью термореле. Нагрев плиты достигается примерно за 30 минут. Вместе с плитой обогревается и уплот-
няющее оборудование. Электронагрев можно производить во время транспорти-
ровки асфальтоукладчика.