
2681
.pdf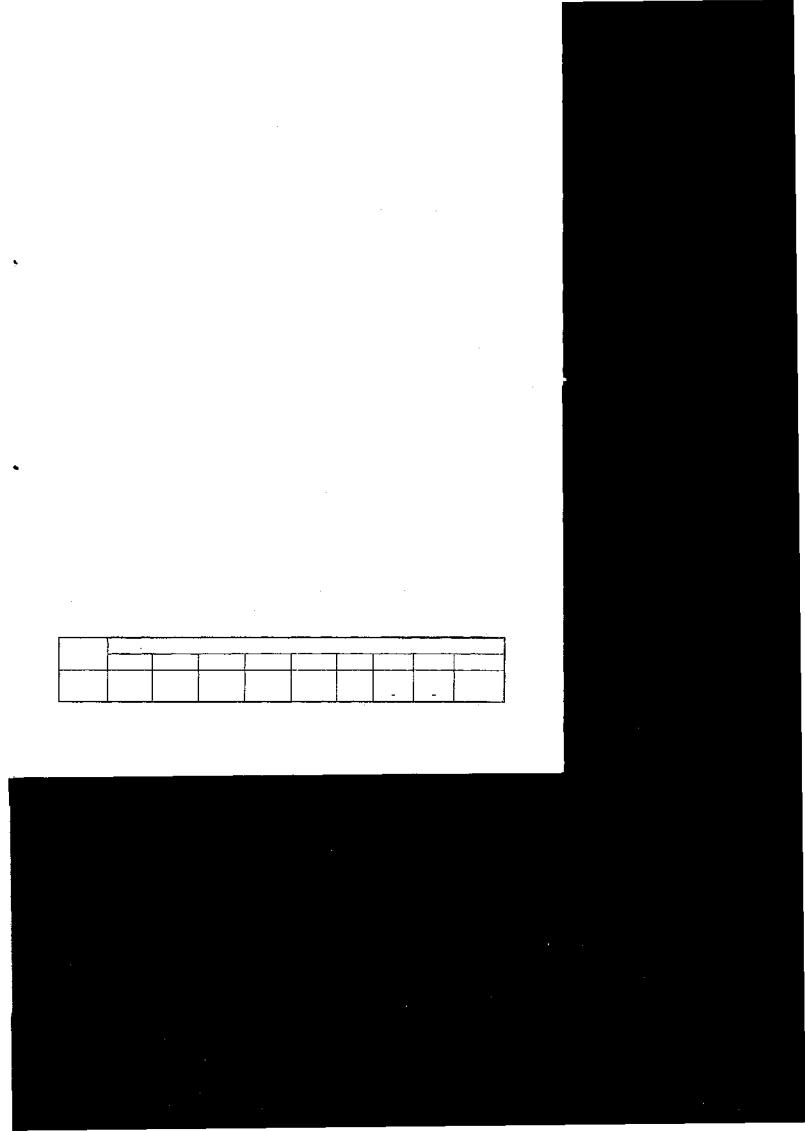
19
сжатии - от 1,4 до 2,2 МПа, водопоглощеиие - от 2,1 до 2,6 %.
Разработанные составы и режимы термической обработки шихты были положены в основу технического задания на проектирование производства пеностекла мощностью 4 тыс. м3, строительство которого на территории завода "Орбита" было начато в 1999 году. Монтаж всей технологической линии производства пеностекла фирма-подрядчик планирует завершить в
начале 2002 г.
Экологическая чистота строящегося производства и предложенной технологии подтверждены санитарно-эпидемиологическим заключением, выданным ЦГСЭН г. Н. Новгорода (№ 52.98.13.000.Т.000016.07.01 от 27.07.2001 г.) и независимой экологической экспертизой, проведенной Городским комитетом по охране окружающей среды и природных ресурсов г.
Н. Новгорода.
Раздел 4.5 посвящен разработке технологии переработки шлаков и отработанных формовочных песков в керамическую плитку. На основе анализа данных по стабильности химического (табл. 3) и гранулометрического
состава во времени в качестве объектов утилизации были выбраны гранулированные ваграночные шлаки ОАО "ГАЗ" и формовочные пески АО "Нижегородский машиностроительный завод".
Показано, что важную роль, определяющую качество изделий и процент брака, играют правильный подбор влажности массы, величины давления и длительности его воздействия при прессовании. Шлак и формовочная земля
являются малопластичными материалами, и отформованные при давлении от
Т а б л и ц а 3 .
|
|
Химический состав ваграночных шлаков. |
|
|
|||||
Номер |
|
|
|
Содержаниеокислов,% |
|
|
|
||
пробы |
SiO2 |
СаО |
MgO |
Fe2O3 |
А120з |
SO3 |
Н2О п.п.п. |
2 |
|
I |
42,54 |
26,60 |
6,00 |
8,08 |
11,37 |
0,56 |
0,14 |
4,62 |
99,76 |
2 |
52,70 |
23,80 |
4,04 |
5,85 |
12,50 |
0,56 |
|
|
99,46 |

20
10 до 40 МПа образцы не выдерживают даже малых нагрузок. В этой связи был проведен поиск связующих, способных обеспечить требуемую прочность прессованных изделий. Были использованы жидкое стекло, цементы, поливиниловый спирт, лигнины, карбоксиметилцеллюлоза (КМЦ) и др.
Установлено, что наиболее технологичной и дешевой является КМЦ
достаточно умеренной концентрации - не более 20 г/л, которая обеспечивает сохранность вяжущих свойств до 7 суток и достаточную для внутрицеховой транспортировки механическую прочность. Были проведены исследования по определению и оптимизации режимов сушки и обжига отформованных изделий.
Показано, что керамическая плитка, изготовленная из шлаков и формовочных песков, имеет высокое водопоглощение - около 15%, при этом
необходим поиск условий, способных обеспечить требуемое качество.
При прессовании керамических масс при производстве плитки в качестве
пластификатора |
и связующего |
обычно используется увлаженная до 10 % |
|||||||
|
|
|
|
|
глина. Этим путем решили пойти и |
||||
|
|
1-1 |
мин |
|
мы. В своих опытах мы |
||||
|
|
|
|
|
|||||
|
|
|
|
|
использовали составы: шлак (Ш) + |
||||
|
|
|
|
|
глина |
(Гл) |
(афонинская или |
||
|
|
|
|
|
мызинская) и формовочные пески |
||||
|
|
|
|
|
(ФП) + глина (афонинская или |
||||
|
|
|
|
|
мызинская), |
где |
изменение |
||
|
|
|
|
|
содержания шлаков (ФП) менялось |
||||
О |
20 |
40 |
60 80 |
100 |
от 100 до 0 %, а глин от 0 до 100 |
||||
|
|
|
|
||||||
|
|
|
гл (аф), % |
%, соответственно. |
|
||||
Рис. 6. Зависимость водопоглощения |
После сушки отформованные |
||||||||
образцов от состава шихты "Ш : Гл |
|||||||||
|
|
|
|
||||||
(аф)" (1-3, t=1050°C) и "ФП : Гл(аф)" |
изделия |
направляли |
на отжиг, |
||||||
(4, t=1100°C) при различных времени |
время |
и температуру |
которого |
||||||
спекания и температурах. |
|
||||||||
|
|
|
|
|

21
подбирали опытным путем, в зависимости от состава шихты и качественных
показателей готового изделия (водопоглощение и прочность). |
|
|
|
||||||
|
|
4 -1025°С |
В |
системе |
"ваграночный |
||||
|
|
|
|
|
|
|
|
||
|
|
|
шлак |
- |
глина |
(аф)" |
|||
|
|
|
наименьшие |
значения |
|||||
|
|
|
водопоглощения (W), |
при |
|||||
|
|
|
температуре |
1050 |
°С |
и |
|||
|
|
|
времени обжига от 1 до 30 |
||||||
|
|
|
мин, |
|
наблюдаются |
|
при |
||
|
|
|
содержании шлака в шихте в |
||||||
|
|
|
количествах от 80 до 50 % |
||||||
10 |
20 |
30 р, МПа 40 |
[рис. |
6 (кривые 1,2,3)]. С |
|||||
Рис. 7. Зависимость прочности на сжа- |
|||||||||
|
|
|
|
|
|
||||
тие (1,2) и прочности на изгиб (3,4) от |
ростом |
содержания |
глины |
||||||
давления прессования и температуры |
(более |
50%) |
наблюдается |
||||||
обжига (состав массы - Ш: Гл(аф) = 70: |
|||||||||
резкое возрастание W. При |
|||||||||
30). |
|
|
содержании шлаков выше 80 % качество прессования, пластичность и
текучесть массы ухудшаются, что и приводит к росту водопоглощения. На этом основании в качестве оптимального был выбран состав "шлак: глина" - 70 : 30, и все дальнейшие исследования проведены с этим составом. Были определены оптимальные значения тонкости помола - от 100 до 250 м2/кг. При больших значениях резко возрастает время помола и наблюдается незначительное улучшения качества плитки. Уменьшение тонины помола до значений менее 100 м2/кг приводит к увеличению водопоглощения за счет роста доли и размеров воздушных пустот. Зависимости водопоглощения и прочности при сжатии и изгибе от температуры спекания и давления прессования носят закономерный характер: при увеличении давления прессования от 10 до 40 МПа и температуры обжига от 1025 до 1050 °С водопоглощение падает с 10 до 2 %, а прочность при сжатии и изгибе
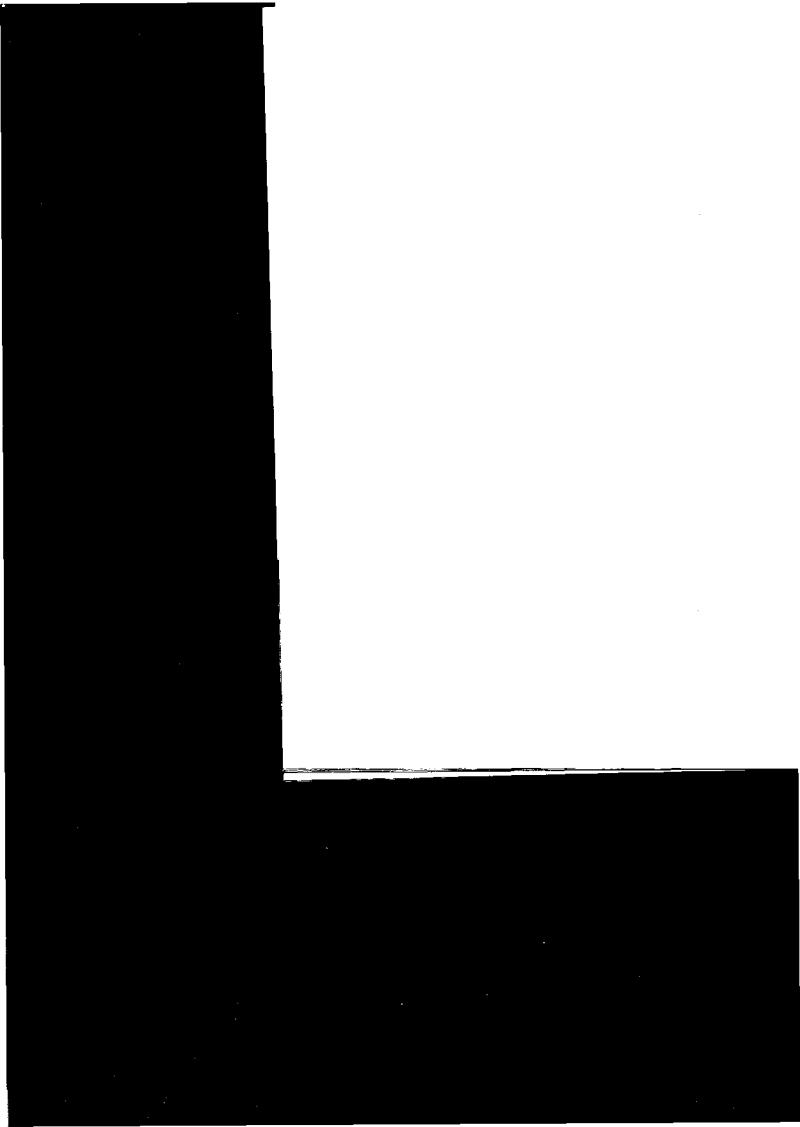
22
возрастает (см. рис. 7) со 100 до 220 МПа и от 30 до 45 МПа (1050°С) соответственно. Это связано с тем, что при увеличении давления и температуры спекания воздушные зазоры между частицами уменьшаются за счет более плотной упаковки.
Добавление молотого стекла в шихту в количестве более 3 % снижает водопоглощение до 1,5 % при всех соотношениях "шлак - глина" в шихте. Температуры спекания при этом понижаются на 20 - 30 °С.
Известно, что керамическая масса начинает спекаться при более низких температурах, чем те, при которых достигается максимальная плотность изделия. По мере роста температуры увеличивается доля жидкой фазы и уменьшается ее вязкость, развивается сдвигающее действие капиллярных сил и происходит заполнение пор жидкостью, что и приводит к уплотнению материала. Температуру обжига, при которой достигается максимальная плотность, принято называть температурой спекания (Тш). Такой материал не имеет открытой пористости, но сохраняет, в значительной части, закрытую пористость. Чтобы добиться дальнейшего уплотнения материала, прибегают к временной выдержке при конечной температуре обжига.
Исследования временных зависимостей прочности от времени спекания при температуре от 1025 до 1075 °С показали, что при получасовой выдержке прочность при сжатии и прочность на изгиб достигают максимума (120 и 65 МПа соответственно). Водопоглощение керамики, полученной при различных Тспи времени более 0,5 часа, практически одинаково и далее с ростом времени спекания приближается к нулевому значению. На этом основании было выбрано время спекания (0,5 часа), достаточное для достижения требуемого ГОСТом водопоглощения половой и фасадной плиток.
Температура, при которой возможен вынос керамики из печи на воздух без потери прочностных и других характеристик, и скорость ее охлаждения являются важными параметрами. От их величины зависят длина и
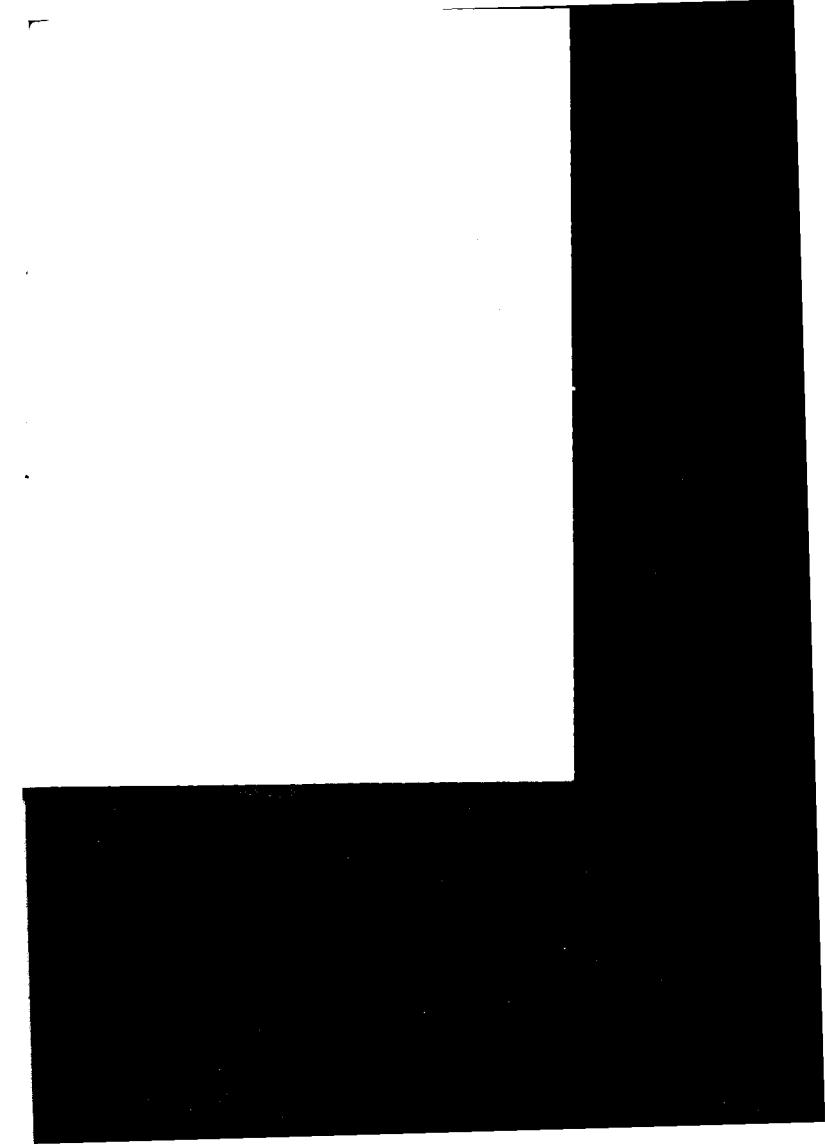
23
производительность линии, а также энергопотребление. Установлено, что разработанный нами керамический материал выдерживает скорости охлаждения до 7 0С/мин в интервале от температуры спекания до 750 0С. При температурах ниже 750 °С плитку можно вынимать из печи без потери ее прочностных свойств.
Рекомендованные режимы: состав шихты "шлак : глина (аф)" - 70 : 30; тонкость помола - от 200 до 250 м2/кг; давление прессования - 25 МПа; скорость нагрева шихты - 15 °С/мин; время спекания - от 0,5 часа, интервал спекания для облицовочной плитки - от 1025 до 1050, а для половой - 1050 - 1075 °С (из-за более жестких требований к величине водопоглощения). При этих режимах плитка имеет следующие параметры качества: водопоглощение - менее 3 %, прочность при сжатии и изгибе -100 и 50 МПа соответственно.
Закономерности, полученные при исследовании керамических масс "ваграночный шлак - мызинская глина", оказались схожими, но прочность изделий - значительно ниже. Это связано с тем, что мызинская глина более тощая и при одних и тех же давлениях прессования получаемое изделие более пористое и хуже спекается. По этой причине дальнейшие эксперименты с мызинской глиной нами были прекращены.
Подобный описанному выше цикл работ был проведен и с отработанной формовочной землей АО "Машзавод". Было установлено, что оптимальные условия помола, смешения, прессования и сушки смесей "формовочные пески - глина" не отличаются от тех, которые были найдены для ваграночных шлаков. Показано, что для смесей "песок - глина" водопоглощение уменьшается с ростом содержания глины [рис. 6 (кривая 4)]. Наименьшие значения водопоглощения - в 2-3 % наблюдаются при содержании песков не более 50 % по массе.
Уменьшать количество песков в шихте, с точки зрения их переработки, невыгодно, и поэтому рабочий состав смеси "песок - глина" был принят
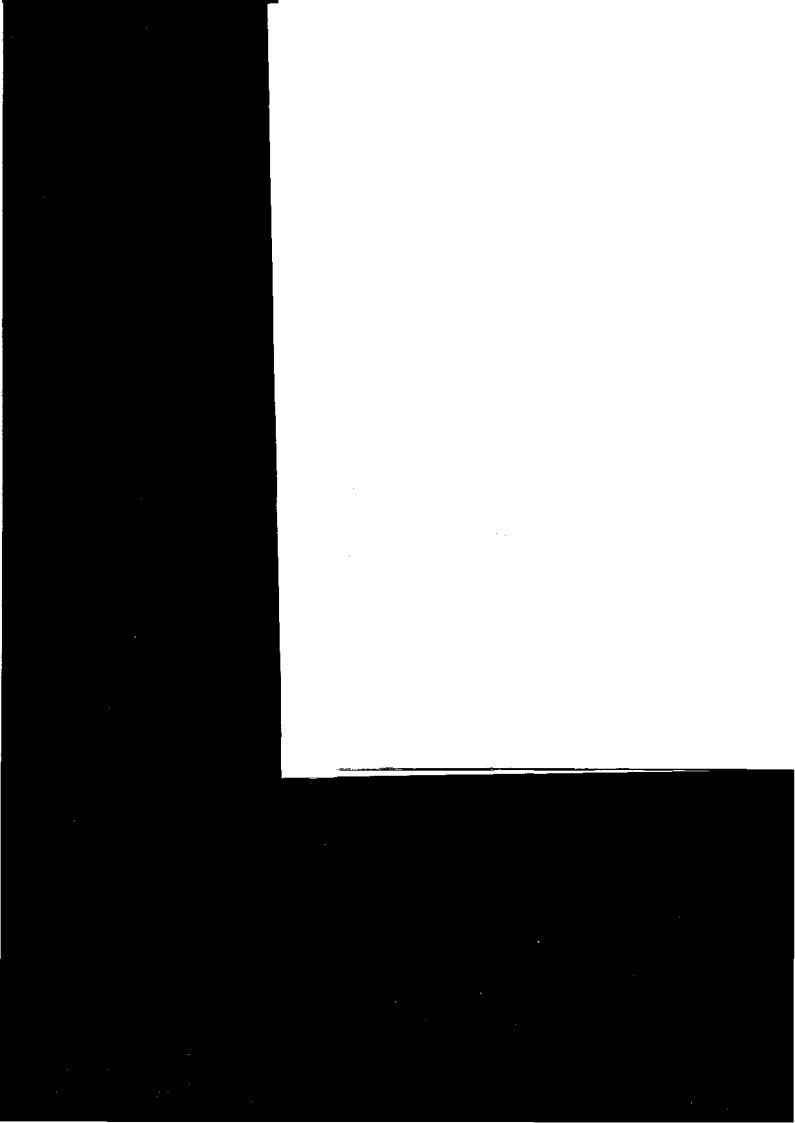
24
равным 50 : 50 %. Для этой массы были определены интервал и время спекания: 1100 ± 15 °С и 0,5 часа соответственно.
Отметим, что плитка, изготовленная из формовочных песков, имеет красивый внешний вид и, в зависимости от состава шихты и режимов термообработки, меняет цвет от светло-бежевого до темно-фиолетового. Водопоглощение плитки находится на уровне 2-3%, а прочность при сжатии около 80 МПа.
Апробация разработанных технологических режимов получения керамической плитки из шлаков и песков была проведена в керамическом производстве завода "Орбита". Спекание проводили в 20 - метровой газовой туннельной печи.
Просушенные плитки (150 шт.) разбили на 3 партии и в вертикальном положении размещали на вагонетках на керамических подставках и в капселях с засыпкой и без нее. Были проведены 3 садки в печь, что позволило оценить качество изделий и процент брака. Установлено, что брак при открытом способе садки составляет от 30 до 35 %, в капселях с засыпкой - от 20 до 25 %. Основной причиной брака являлись коробление, оплавление ребер или недожог. Анализ причин брака показал, что туннельные печи не могут держать столь узкий интервал температур спекания. Измерения температуры в печи по длине, высоте и ширине рабочей зоны во времени с помощью передвижной термопары показали, что колебания температуры превышают допустимые пределы более чем в 2 раза. Очевидно, что для реализации технологий переработки шлаков и отработанных песков в керамические изделия требуются коренная модернизация печей и замена газового обогрева на электрический. Пробный обжиг в камерной электрической 500 - литровой печи в условиях равномерного обогрева позволил устранить указанные выше виды брака керамики.
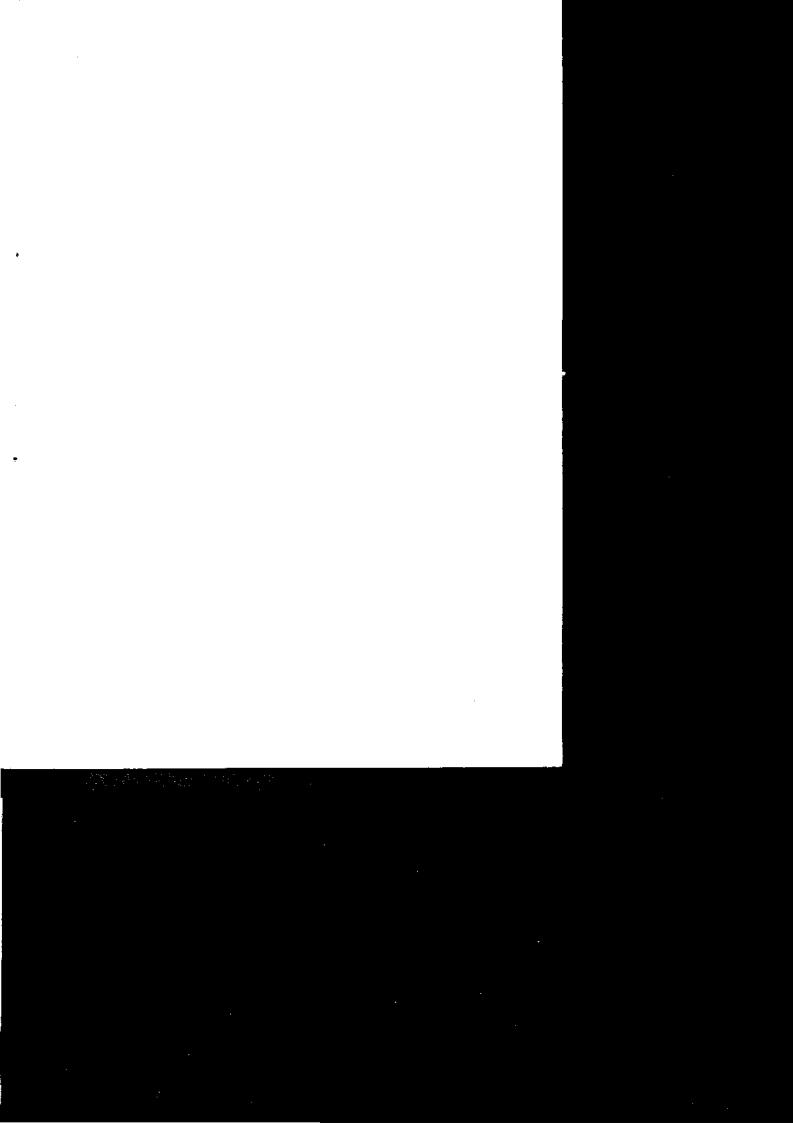
25
3.ОСНОВНЫЕ ВЫВОДЫ
3.1.Впервые разработана экологически безопасная, ресурсосберегающая технология получения высококачественного блочного пеностекла из боя стекла, новизна которой подтверждена патентом и свидетельством на полезную модель, а экологическая безопасность - независимой экспертизой и санитарно-эпидемиологическим заключением.
3.2.На основе проведенных исследований и промышленных апробаций
ООО"Экран" было разработано техническое задание на проектирование производства пеностекла из стеклобоя, первая очередь которого пущена в эксплуатацию на заводе АО "Орбита" (г. Н. Новгород) в 2000 году, а пуск всей технологической линии ООО "Экран" планирует провести в конце 2-го квартала 2002 года.
3.3.Использование в качестве сырья бытового и промышленного стеклобоя позволяет на каждом кубическом метре произведенного пеностекла плотностью 200 кг/м3 экономить 140 кг высококачественных песков, 3 кг глинозема и 50 кг соды, а замена специально сваренных стекол на стадии шихтоподготовки - до 12 МДж/кг стеклянной массы.
3.4.Найденные технические решения по конструкции форм обеспечивают возможность их автоматического раскрытия при высоких температурах и делают ненужными операцию механической обработки блоков пеностекла и подогрева печей отжига.
3.5.Применение качественного пеностекла, полученного по низкотемпературной технологии, позволит потеснить доминирующие на рынке выделяющие токсичные вещества и пожароопасные материалы типа вспененных органических масс и пылящих минеральных ват,
3.6.Предложенная технология экономит энергоресурсы, продлевает сроки службы основного оборудования и оснастки, позволяет полностью замкнуть производство и возвращать брак и улавливаемую стеклянную пыль, т.к. низкие температуры вспенивания предотвращают кристаллизацию стекла

3.7. Экспериментально обоснованы и оптимизированы составы рабочих масс и режимы технологического процесса переработки ваграночных шлаков и отработанных формовочных песков.
Публикации по теме диссертации
1. Гимик В.В, Наумов В.И., Сучков В.П. Теплоизоляционные и изоляционно-декоративные материалы на основе пеностекла// Тр. научно-технической конференции "Строительный комплекс-98", г. Н. Новгород, ННГАСУ, 1999 г..- Н. Новгород, 1999.- Т. 5.- С. 45 - 47.
2.Гимик В.В., Наумов В.И., Сучков В.П. Строительные материалы из отходов промышленных производств// Тр. научно-технической конференции "Строительный комплекс-98", г. Н. Новгород, ННГАСУ, 1999 г..- Н. Новгород, 1999.- Т. 5.- С. 43 - 45.
3.Наумов В.И., Гимик В.В., Сучков В.П. и др. Переработка стеклобоя и ваграночных шлаков ОАО "ГАЗ" в промышленные и строительные материалы и изделия// Тр. региональной конференции "Экологические проблемы промышленности и транспорта", г. Н. Новгород, 1999 г..- Н.Новгород, 1999.- С. 61 - 62.
4.Наумов В.И., Ахлестин Е.С., Гимик В.В. и др. Энергосберегающая технология получения теплоизоляционного пеностекла// Тр. научнотехнической конференции "Архитектура и строительство - 2000", г. Н. Новгород, ННГАСУ, 2001г..-Н. Новгород, 2001.- Т. 5.- С. 36 - 37.
5.Патент 2149146 РФ, МКИ С 03 С 11/00. Шихта для получения пеностекла/ Наумов В.И., Гимик В.В., Ахлестин Е.С., Головин Е.П., Сучков В.П. 98123286/03; Заявл. 12.12.98; Опубл. 20.05.00, Бюл. №14.- Зс.
6.Полезная модель 15574 РФ, МКИ С 03 С 11/00. Форма для производства пеностекла/ Ахлестин Е.С., Наумов В.И., Головин Е.П., Гимик В.В., Сучков В.П 2000108166/20; Заявл. 03.04.00; Опубл. 27.10.00, Бюл № ЗО.-Зс.
Подписано в печать 19.03.02. Формат 60x84 '/16. Бумага офсетная. Печать офсетная. Уч.-шд. л. 1,0. Тираж 100 экз. Заказ 214.
Нижегородский государственный технический университет. Типография НГТУ. 603600, Нижний Новгород, ул. Минина, 24.