
2681
.pdf
Т а б л и ц а 1 .
|
Составы используемых оконных стекол. |
|
|
|||||
Производи |
2 |
|
Компоненты стекла, % |
Р205 |
3 |
|||
тель |
|
2 3 |
СаО |
MgO |
R2O |
|||
"Символ" |
SiO |
Аl2Оз |
Fe 0 |
|
|
|
|
S0 |
71,95 |
1,70 |
0,20 |
6,60 |
4,10 |
14,90 |
0,15 |
0,40 |
|
БСЗ (Бор) |
73,00 |
0,90 |
0,12 |
8,70 |
3,60 |
13,60 |
- |
0,53 |
- около 0,06 Вт/м.К) можно получить и из стеклобоя, используя следующие составы масс и режимы нагрева-охлаждения: стекло - 100 %, кокс - 2-3 % (сверх ста процентов); время нагрева до температуры вспенивания (ок. 830 °С) -. от 60 до 90 мин; время вспенивания - 20 мин; продолжительность отжига - не менее 8 часов. Исследования по отжигу пеностекла показали, что для определения скорости охлаждения можно пользоваться уравнением Даувальтера, согласно которому максимальная скорость охлаждения пеностекла Н, °С/мин, пропорциональна квадрату половинной толщины блока:
Н = К / а2, |
(1 ) |
где К - коэффициент, зависящий от коэффициента термического линейного расширения пеностекла (КТЛР), °С. мм2/мин; а - половинная толщина блока, мм
При использованных в работе толщинах пеностекла качественные блоки можно получить при скоростях охлаждения, не превышающих 1,4°С/мин.
Были найдены и оптимизированы составы суспензий, предназначенных для обмазки металлических форм и предотвращающих прилипание стекла. Найденная обмазка недефицитна, мало подвержена седиментации и легко счищается с поверхности металлических форм.
Показано, что качество пеностекла, как в углеродной, так и в карбонатной технологиях существенно зависит от режимов нагрева шихты до максимальной температуры. Выяснилось, что начальная температура нагрева шихты должна лежать в интервале от 400 до 450 °С, а время нагрева до
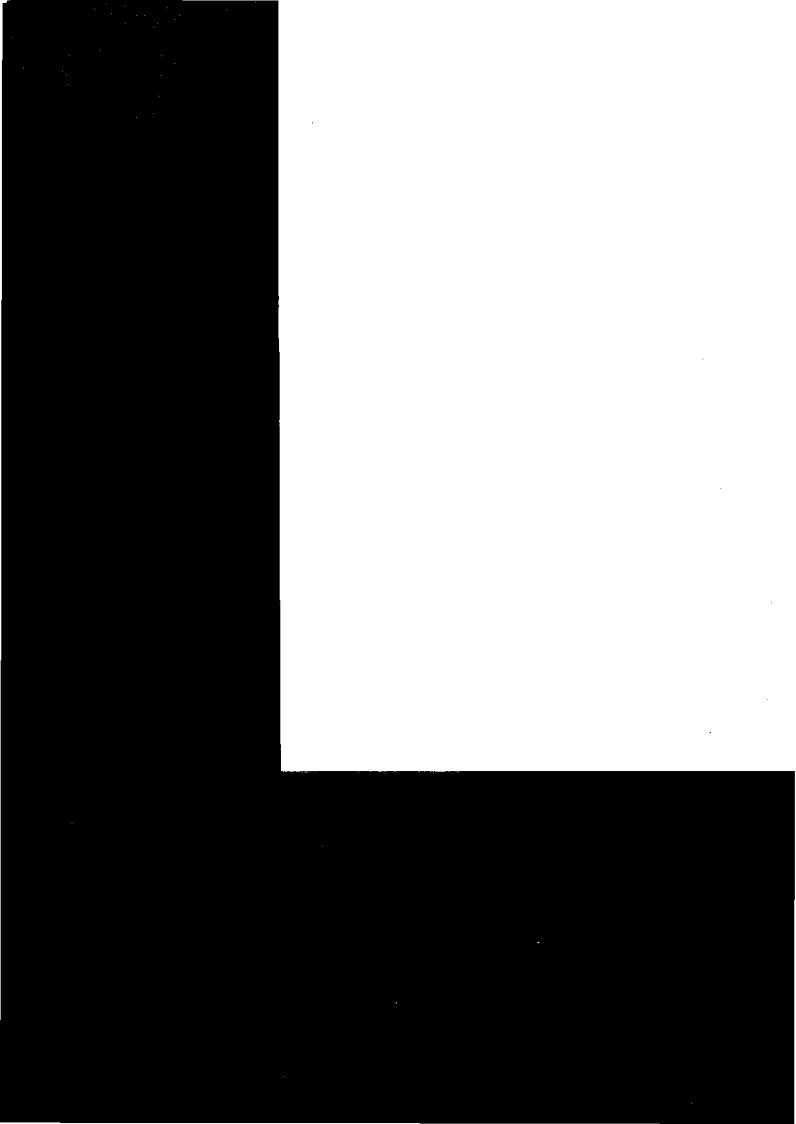
10
температуры вспенивания - от 60 до 90 мин. При большем времени наблюдается преждевременное выгорание газообразователя, а при времени менее 60 мин, вследствие малой теплопроводности шихты, ее середина не успевает прогреваться до состояния расплава. Вследствие меньшей плотности эта масса начинает всплывать, что сопровождается образованием "горба" на верхней поверхности изделия и воздушных пустот внутри блока пеностекла. Этот вывод сделан при использовании индикатора (оксид кобальта), с помощью которого удалось проследить направление потоков расплава и неспекшейся шихты в различные промежутки времени при разных температурах. Снижение скорости нагрева шихты до 3,0 - 5,0 °С/мин позволило устранить этот вид брака в обеих технологиях.
Известно, что в процессе охлаждения пеностекла часто наблюдается усадка со стороны верхней или нижней поверхности блока. Этому явлению в литературе было дано объяснение: при остывании газы в пустотах начинают сжиматься, создавая разрежение в условиях, когда из блока не отведено достаточное количество тепла. За счет тепла, аккумулированного внутри блока, поверхностная корка пеностекла начинает размягчаться, и это создает условия для усадки блока. В производственных условиях использовать сложные режимы охлаждения, компенсирующие эти эффекты, практически невозможно, что увеличивает процент брака.
При использовании углеродной технологии нами предложено добавочно вводить в шихту доломит (0,5 %), который продолжает разлагаться и выделять СO2 в интервале от температуры вспенивания до 620 °С. Углекислый газ способствует поддержанию необходимого давления в газовых пузырьках до образования твердой и прочной корки на поверхности блока.
Раздел 4.2 посвящен разработке технологии получения качественного теплоизоляционного пеностекла с помощью карбонатных газообразователей. Из-за многочисленных неудач в литературе укоренилось мнение, что при этом способе пеностекло получается преимущественно с открытыми порами, что
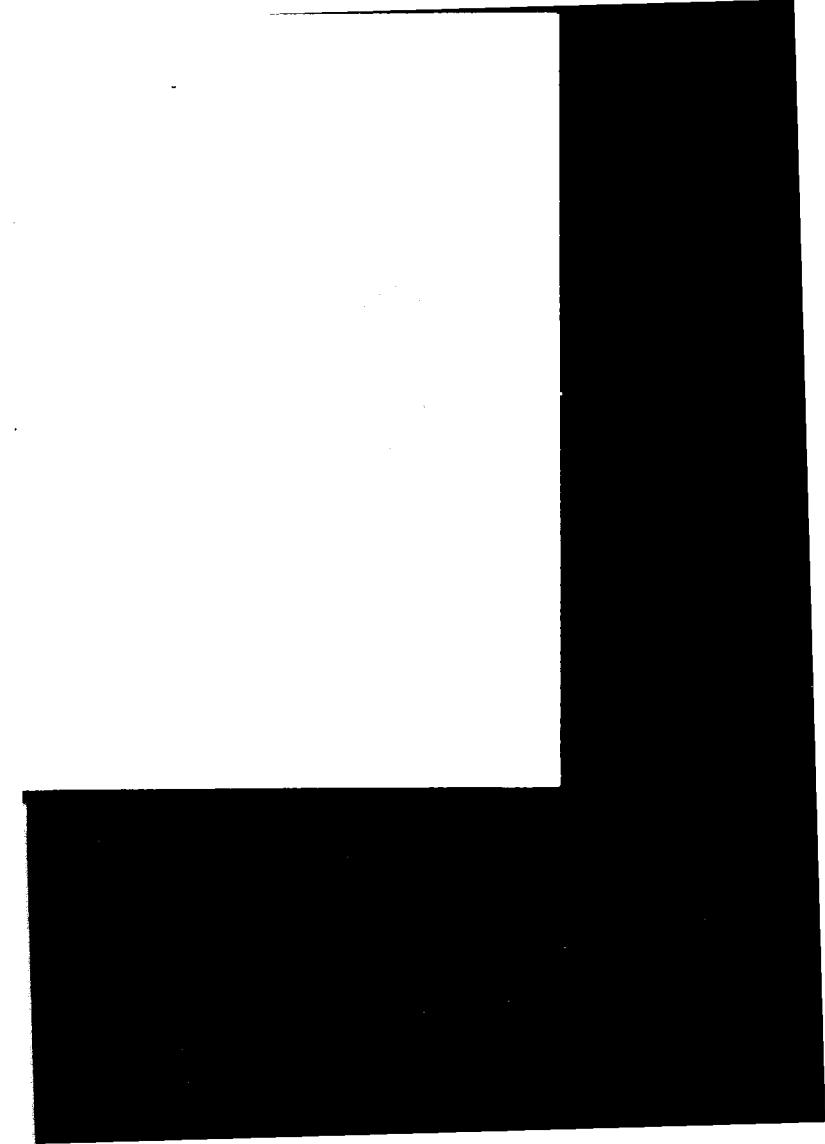
11
является причиной высокого уровня водопоглощения и низкой морозостойкости.
Совместное рассмотрение данных по пеностеклу (Китайгородский И.И., Демидович Б.К., Шилл Ф.), термодинамике поверхностных явлений и теории пен (Gibbs J.W., Русанов А.И., Дерягин Б.В.), позволило предположить, что для получения качественного пеностекла, помимо высокого давления газа и требуемой вязкости расплава (менее 8.10 6 пз), поверхностное натяжение (σ)
на границе расплав - газ должно быть менее 0,5 Н/м. Практика стекловарения показала, что при температурах более 700 °С за счет адсорбции компонентов расплава столь низких значений а достичь нельзя.
Нами показано, что требуемые значения а можно получить, если в шихту вводить лиофобные вещества, которые при температуре вспенивания остаются в твердом состоянии и хорошо приклеиваются к расплаву. Лиофобность предотвращает переход этих веществ в объем расплава, что и обеспечивает низкие значения σ. Нами предположено, что прочное приклеивание к поверхности расплава должны иметь вещества, содержащие в сравнимых количествах с боем стекла оксид кремния (SiO2) и оксид алюминия (А12Оз). Это могут быть полевые шпаты, пегматиты, каолины и глины.
В начале исследований газообразователь (мел или химический реактив СаСОз) вводили в количестве 2 % от массы порошка стекла, изготовленного из стеклобоя (тонкость помола более 250 м2/кг). Вспенивание проводили при температурах от 720 до 780 °С; нагрев шихты - аналогично описанному выше.
Показано, что добавление полевого шпата (ПШ) к шихте [рис. 1 (кривая 1)] в количествах от 2 до 6 % снижает водопоглощение пеностекла в 2 - 2,5 раза. Как и предполагалось, ПШ проявляет поверхностную активность при температурах вспенивания и уменьшает объемное водопоглощение до 15 %, что для теплоизоляционного пеностекла явно недостаточно.
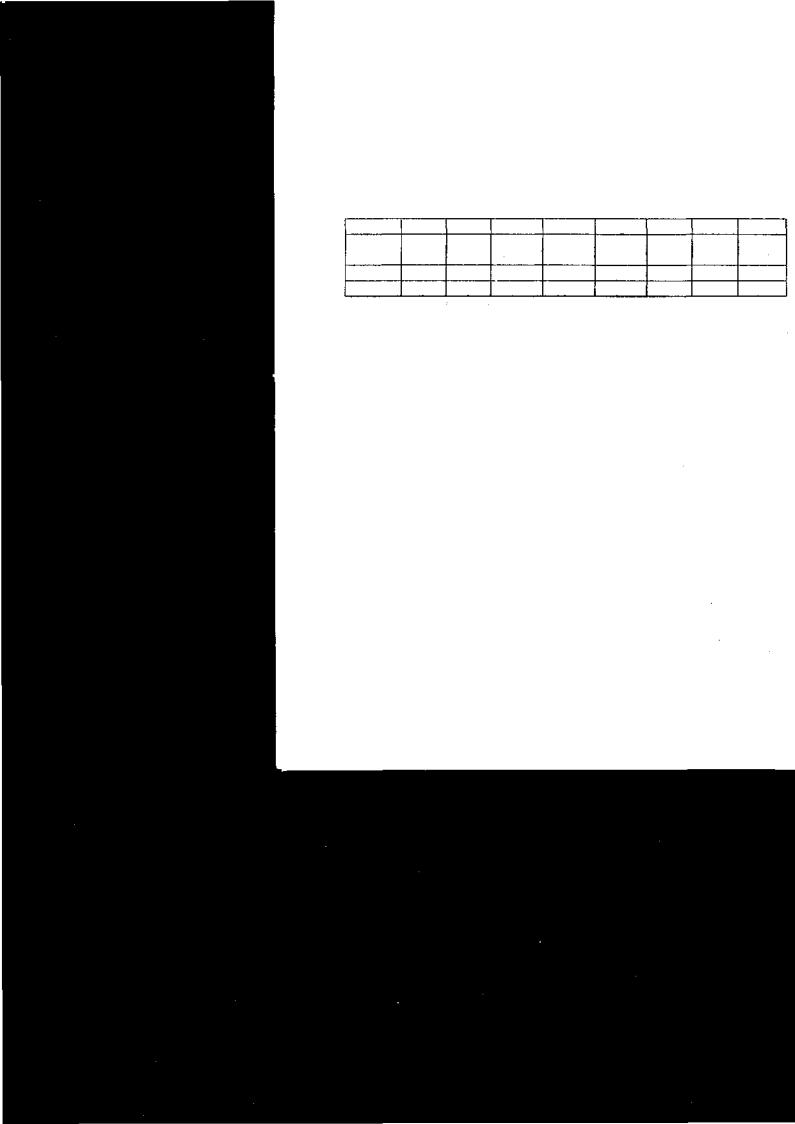
12
Дальнейшие исследования были посвящены поиску добавки,
позволяющей усилить эффект использования ПШ. Были использованы глины (мстерская, мызинская и афонинская), содержание глинозема и кремнезема в которых различается (см. табл.2).
Т а б л и ц а 2.
Химические составы глин мстерского (мст), афонинского (аф) и |
|
||||||||
|
|
мызинского месторождений, масс.%. |
|
|
|||||
карьер |
SiO2 |
А1203 |
Fe203 |
СаО |
MgO |
R2O Ti02 |
S03 |
||
мст№ |
80,74 |
9,64 |
3,06 |
0,97 |
0,85 |
1,64 |
0,64 |
0,08 |
|
2 |
|
|
|
|
|
|
|
|
|
аф № 1 |
77,28 |
10,56 |
1,92 |
1,54 |
1,98 |
1,52 |
— |
0,22 |
|
Мыза |
73,50 |
9,00 |
6,60 |
5,70 |
0,30 |
1,80 |
0,25 |
||
— |
|||||||||
|
|
|
|
|
|
|
|
Дериватографические измерения показали, что температуры плавления этих глин выше 850 °С. Глины лиофобны и прочно приклеиваются к поверхности расплава стекла, что подтверждено исследованиями соответствующих шлифов.
Лучшие результаты получены при использовании мстерской и афонинской глин. На рис. 1 (кривая 2) показано, что мстерская глина снижает водопоглощение пеностекла до приемлемых значений - 4-8 %, но при этом наблюдается возрастание максимальной температуры вспенивания.
Мы хотели сохранить в составе шихты ПШ, присутствие которого положительно сказывается на помоле шихты. К тому же, в производстве стекла и керамики в большинстве случаев срабатывает правило аддитивности, и положительные эффекты, полученные при использовании глин и ПШ,

|
|
|
|
13 |
|
|
|
|
|
|
|
|
|
|
могут |
суммироваться. |
|||
|
|
|
|
|
Для |
проверки |
|||
|
|
|
|
|
этого предположения в |
||||
|
|
|
|
|
шихту |
были введены |
|||
|
|
|
|
|
ПШ (2 %) и мстерская |
||||
|
|
|
|
|
глина (0, 2, 4 и 6 %). |
||||
|
|
|
|
|
Было установлено, |
что |
|||
|
|
|
|
|
добавление |
глины |
в |
||
|
|
|
|
|
шихту, |
|
содержащую |
||
0 |
2 |
4 |
6 |
8 |
ПШ, |
|
увеличивает |
||
|
|
|
|
добавка, % |
|
||||
|
|
|
|
|
максимальную |
||||
Рис. 1. Зависимость водопоглощения пеностекла |
|
||||||||
от содержания в шихте: |
|
|
|
|
температуру |
||||
|
|
|
|
|
|
|
|||
1- полевого |
шпата; 2 |
- мстерской |
глины; 3 - |
вспенивания на 40 °С и |
|||||
мызинской глины; 4 - афонинской глины. |
|||||||||
|
|
|
|
||||||
|
|
|
|
|
на 15 |
- 20 % снижает |
прочность на сжатие. Водопоглощение при этом меняется мало. По этой причине дальнейшие эксперименты по совместному действию добавок были нами прекращены, а работа была направлена на оптимизацию составов и режимов тепловой обработки шихты с добавлением различных сортов глин.
Наименьшим водопоглощением характеризуется пеностекло, полученное при использовании добавок мызинской и афонинской глин [рис. 1 (кривые 3 и 4)]. Но образцы с добавкой мызинской глины, при испытании на сжатие, показали худшие результаты. Поэтому, при оптимизации составов и температурногорежимаиспользоваласьафонинскаяглина.
В результате обобщения экспериментальных данных предложен оптимальный состав шихты и режимы термообработки, которые нами запатентованы: стекло - 100% + мел - 1,5% + глина - 4% (от веса стекла). Время нагрева шихты - от 60 до 90 мин, температура и время вспенивания - 745 ±10 °С и 20 минут соответственно.
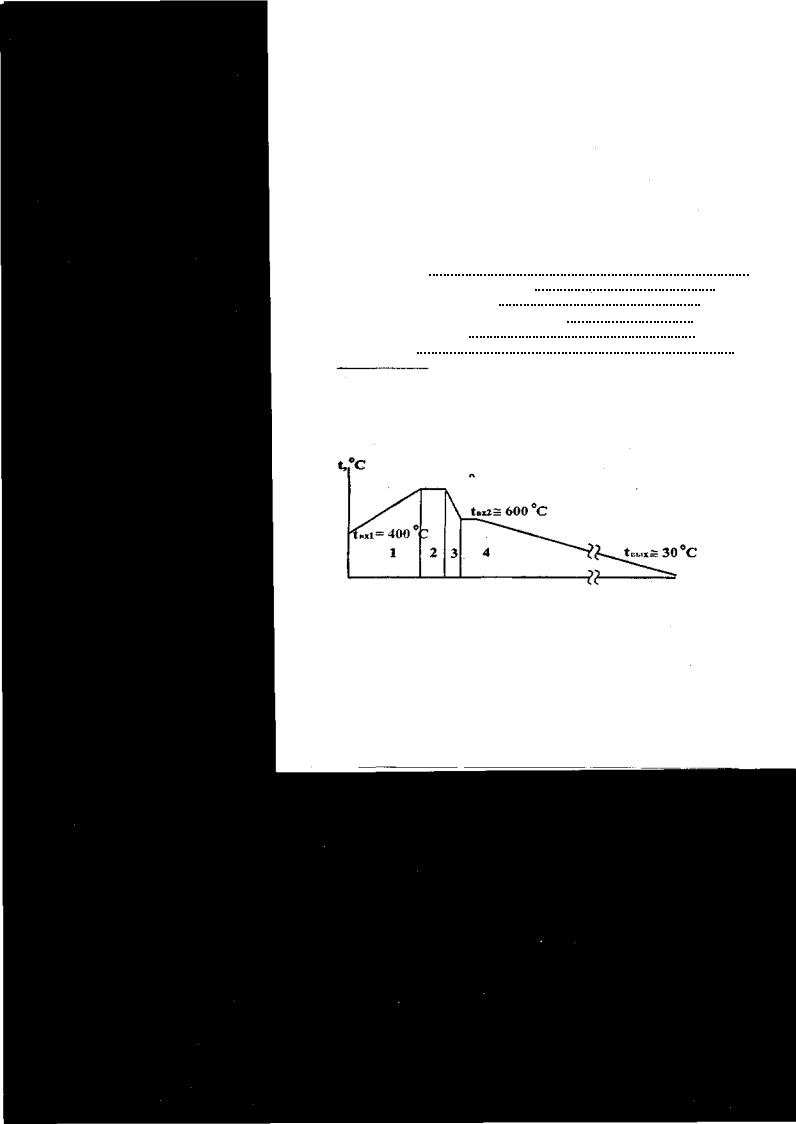
14
Для уменьшения процента брака были проведены исследования,
направленные на поиск оптимальных условий охлаждения между печами
вспенивания и отжига, времени стабилизации и повторного нагрева, отжига и
т.п. В конечном итоге (рис. 2) из боя оконного и тарного стекла, с
использованием карбонатной технологии, нами впервые получено
качественное блочное пеностекло с замкнутыми порами.
Технические характеристики пеностекла, рекомендованной для
промышленного производства плотности, приведены ниже *': |
|
Плотность, кг/м3 |
200 |
Предел прочности при сжатии, МПа |
Более 1,4 |
Объемное водопоглощение,% |
не более 4,0 |
Коэффициент теплопроводности, Вт/(м-К) |
не более 0,06 |
Морозостойкость,циклы |
не менее 100 |
Пористость, % |
90 ±3 |
*' По нашей технологии можно получить пеностекло любой плотности, от 160 кг/м3 и выше. Снижение плотности менее 200 кг/м3 приводит к существенному снижению прочности при незначительном изменении коэффициента теплопроводности. С увеличением плотности более 250 кг/м3, при возрастающем весе, коэффициент теплопроводности увеличивается.
tвсп= 740oС
Рис. 2. Температурная кривая конвейерного производства пеностекла:
1 - зона нагрева; 2 - зона вспенивания; 3 - зона охлаждения; 4 зоны стабилизации и отжига.
Для использования механически необработанных (остеклованных) блоков
пеностекла в строительстве необходимо найти способ крепления его к

15
кирпичной и бетонной стенам. В работе были проведены эксперименты по определению величины адгезии остеклованной поверхности пеностекла к кирпичной и бетонной стенам с помощью цементных растворов, которая оказалась равной от 0,3 до 0,5 МПа. Механически обработанная, неостеклованная поверхность выдерживает нагрузки в 1,5 - 2,0 раза больше. В этих экспериментах, с частотой повторяемости до 40%, наблюдался отрыв образцов по телу цементного раствора. Очевидно, величина когезии цементной связки сравнима с величиной адгезии на границе цементный раствор - пеностекло, что позволяет рекомендовать этот способ крепления пеностекла на поверхности вертикальных бетонных или кирпичных стен.
Раздел 4.3 посвящен созданию декоративно-теплоизоляционного пеностекла - пенодекора. Здания, облицованные пенодекором, позволят экономить тепло и не потребуют повторной окраски в течение всего срока эксплуатации. В процессе разработки пенодекора, в конечном итоге, нами было выбрано 3 приемлемых варианта его изготовления: а) блок пеностекла плотностью от 300 до 350 кг/м3 и прочностью более 4 МПа окрашивают с помощью неорганических пигментов; б) к блоку пеностекла в процессе вспенивания шихты приваривают окрашенные стеклянную или керамическую пластины; в) на поверхность готового блока наносится цветная прочная и водостойкая шпатлевка.
Второй вариант не дал положительных результатов из-за разницы в коэффициентах термического линейного расширения (КТЛР) привариваемых пластин и пеностекла. На стеклянных пластинах, даже в случае использования промежуточных слоев, содержащих газообразователь в меньших количествах, чем основная шихта, наблюдалось образование трещин.
При приваривании керамических пластин по тем же причинам наблюдается разрыв пористого теплоизолирующего слоя.

16
Мы поставили перед собой задачу - разработать рецептуру шпатлевки, которая отвечала бы поставленным требованиям: должна изготавливаться из доступных материалов, хорошо окрашиваться, быть технологичной в изготовлении и нанесении на поверхность. Шпатлевка должна иметь хорошую адгезию, низкую водопроницаемость, высокую прочность и климатическую устойчивость.
Нами разработано более 20 шпатлевок, содержащих обычные и магнезиальные цементы, жидкое стекло и фосфатные связующие. После испытаний на время схватывания, адгезию, водопоглощение, моростостойкость, прочность и способность к окрашиванию было отобрано 4 типа шпатлевок, которые, как мы посчитали, являются перспективными для производства пенодекора. Годичная выдержка таких плит на открытом воздухе показала, что шпатлевки имеют тенденцию к отслаиванию за счет напряжений или каких-либо других причин, накопленных в системе пеноблокпокрытие.
Вконечном итоге мы остановились на первом варианте, который, в сочетании с разработанной нами карбонатной технологией, позволяет при низких температурах получать окрашенные "кирпичи" с прочной, хорошо' остеклованной поверхностью, снижающей водопоглощение пеностекла до 1 - 2%.
Вразделе 4.4 приведены обоснование выбора технологической схемы производства пеностекла (пенодекора), апробация и уточнение разработанных нами технологических режимов на действующем оборудовании керамического производства завода "Орбита". На основе анализа был выбран двухстадийный способ производства пеностекла, в котором процессы вспенивания и отжига разделены (рис 3).
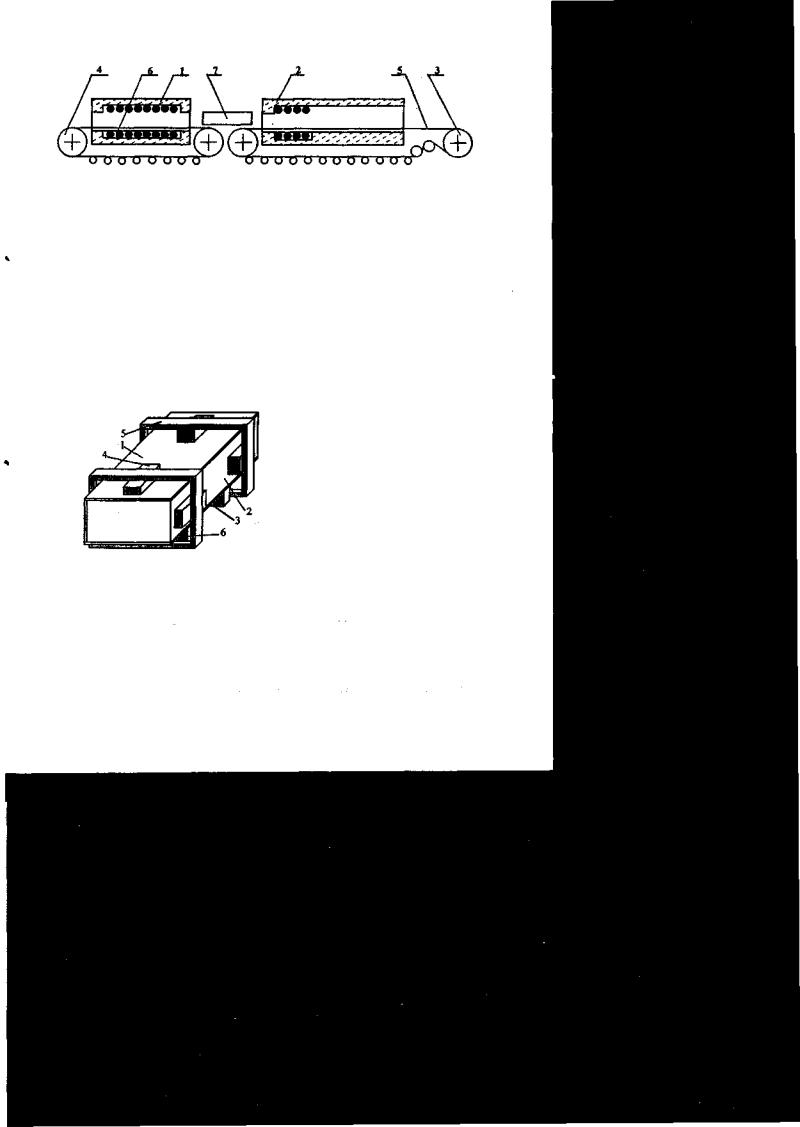
17
Рис. 3. Поперечный разрез печей вспенивания и отжига:
1 -печь вспенивания; 2 - печь отжига; 3 - натяжной барабан; 4 - ведущий барабан; 5 - лента из нержавеющей стали; 6 - нагреватели; 7 - расформовочное устройство.
Двухстадийный способ производства, в совокупности с предложенными
нами мероприятиями по конструкции форм и отжигу изделий, позволили
повысить выход годных изделий на 25 - 30 %. Запатентованная конструкция
металлической формы (рис. 4) сделала ненужными трудоемкие и опасные
операции по ручному раскрытию их при 550-650 °С и механической опиловке
блоков.
Технологическая схема производства пеностекла представлена на рис. 5
|
В |
разделе |
проведены расчет |
||||
|
производительности |
предложенной |
|||||
|
печи |
и |
оценка |
экономической |
|||
|
эффективности |
|
|
производства |
|||
|
пеностекла. |
|
|
|
|
|
|
|
Апробация |
|
предложенной |
||||
|
технологии |
получения |
пеностекла |
||||
Рис. 4. Форма для вспенивания: |
была |
проведена |
в |
10 |
- |
метровой |
|
1 - крышка формы; 2 - Г-образные |
|
|
|
|
|
|
|
стенки; 3 - дно формы; 4 - клинья; |
электрической |
печи конвейерного |
|||||
5 - рамка; 6 - опоры. |
типа |
и 20 - |
метровой |
газовой |
|||
|
туннельной печи. Попытки получить качественное пеностекло в туннельной
печи не увенчались успехом из-за больших градиентов и колебаний
температур в ее рабочей зоне.

18
Эксперименты, проведенные в конвейерной печи, дали положительные результаты и позволили уточнить режимы, предложенные на основе лабораторных исследований: время нагрева шихты - около 90 мин, время вспенивания - 25-30 мин, температура вспенивания - 745 ± 10 °С, время отжига - не менее 8 часов. Опытные образцы имели следующие технические характеристики: средняя плотность - от 200 до 240 кг/м3, прочность при
Стеклянный |
Мел |
Глина |
|
бой |
|||
|
|
||
|
Сушка |
Сушка |
Рис. 5. Технологическая схема производства пеностекла.