
11012
.pdf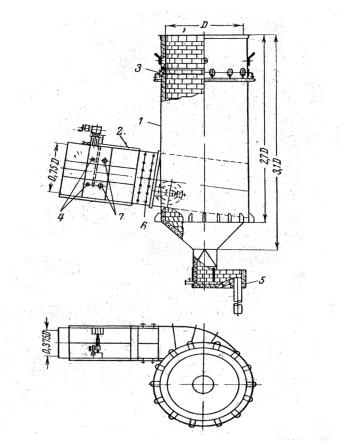
Температура очищенных газов должна лежать в пределах от 120оС до 200оС. Применение мокрых золоуловителей не рекомендуется, если предполагается использовать золу для нужд народного хозяйства. Наибольшее распространение получили центробежные скрубберы ВТИ (рис.2.34).
Дымовые газы подаются в скруббер через тангенциально расположенный входной патрубок. Улавливание золы из дымовых газов происходит на водяной пленке, движущейся по цилиндрической поверхности скруббера, футерованной керамической плиткой. Водяная пленка создается оросительными соплами, тангенциально расположенными к поверхности скруббера.
Рис.2.34. Центробежный скруббер ВТИ: 1 – корпус; 2 – входной патрубок; 3 – оросительные сопла; 4 – смывные сопла; 5 – гидрозатвор; 6 – прутковая решетка; 7 – оросительные форсунки прутковой решетки
Для смыва отложений золы во входном патрубке предусмотрены специальные поворотные сопла.
Насадочные скрубберы
Насадочные скрубберы представляют собой емкости (колонны), содержащие насадочные элементы разной формы: простые кольцакольца Рашига, кольца с перегородками - кольца Лессинга и Палля, седла Берля и "Инталокс", спиральные розетки Теллера и др. Оптимальная область применения насадочных колонн - совместная очистка газовых выбросов от газообразных загрязнителей и дисперсных жидких или твердых растворимых частиц.
41

Такие колонны малопригодны для обработки газов, содержащих обычные, даже неслипающиеся пыли и непригодны для слипающихся и схватывающихся вследствие забивания каналов в насадке.
Рис.2.35. Пенный скруббер
Как и в полых скрубберах, подвод жидкости может быть организован навстречу или поперек потока.
Пенные скрубберы представляют собой колонны с перфорированными перегородками, называемыми тарелками (рис.2.35, а). Для очистки газов чаще всего используются провальные щелевые и дырчатые тарелки (рис.2.35, б, в). Диаметр отверстий дырчатых тарелок принимают в пределах 3...8 мм, а относительное свободное сечение (отношение площади отверстий к площади тарелки) f fr - 0,15...0,25.
Экозащитное оборудование для очистки от газообразных загрязнителей
Дожигательные устройства
Кафедрой Теплогазоснабжения ННГАСУ c 1972 г. проводятся исследования метода дожигания горючих токсичных веществ, в том числе в производственно– отопительных котельных [8]. Разработан ряд конструкций дожигательных устройств, отличающихся по принципу установки: стационарные дожигательные устройства (ДУ), подвесные ширмовые – ДШУ, кассетно– блочные КДУ.
Простейшее стационарное дожигательное устройство представлено на рис. 2.36 и рис. 2.37. Оно представляет собой два ряда раскалённых огнеупоров с камерой смешения
42
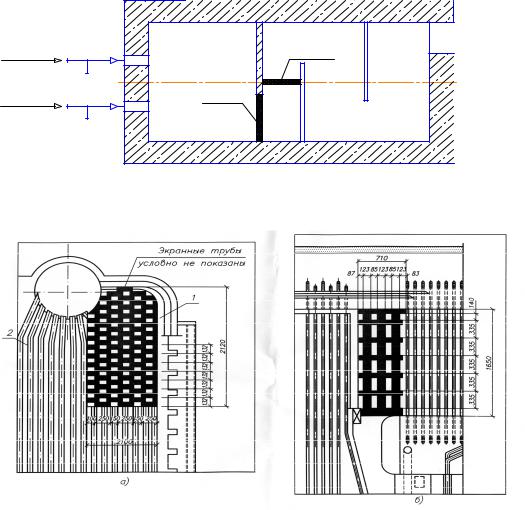
между ними (см. рис. 2.36).
Дожигательное устройство позволяет осуществить контакт раскалённых поверхностей с топочными газами и обеспечивает высокую степень турбулизации потока продуктов сгорания топлива. За счёт гомогенизации продуктов неполного сгорания с избыточным воздухом в зоне раскалённых огнеупоров происходит интенсивное выгорание монооксида углерода, сажи, бенз(а)пирена.
топливо |
II ряд |
|
воздух |
топливо |
I ряд |
|
|
|
воздух |
|
Рис. 2.36. Установка дожигательного устройства в плане котла |
Рис.2.37. Разрезы котла с установкой дожигательного устройства
Установка дожигательного устройства на выходе из топочной камеры позволяет:
–устранить потери теплоты с химическим недожогом q3 ввиду полного обезвреживания компонентов (СО, сажи, БП) продуктов неполного сгорания;
–снизить потери теплоты с уходящими продуктами сгорания q2 ввиду эффективной работы котла с меньшими избытками воздуха в топочной камере;
–снизить плату за загрязнение воздушного бассейна в связи с устранением сажи, оксида углерода, бенз(а)пирена на 99% и более.
Многолетние испытания стационарных дожигательных устройств на внедренных установках показали:
43
–при сжигании природного газа и наличии оксида углерода в продуктах сгорания
впределах (0,05–0,2)% оказалось достаточным дожигательное устройство из двух шамотных решеток с живым сечением (0,4–0,45);
–при сжигании мазута резко увеличивается (на 2 порядка и более) образование сажи и бенз(а)пирена. Это вызывает необходимость увеличения контактирующей поверхности ДУ и снижение его живого сечения до величины 0,3–0,38;
–при установке дожигательных устройств достигается полнота сжигания топлива (газа и мазута) в широком диапазоне тепловых нагрузок и коэффициентов избытка воздуха (значение концентраций СО, сажи бенз(а)пирена не превышают ПДК в атмосферном воздухе);
–достигнута работа котлов, оснащенных дожигательными устройствами, без химического недожога (q3=0 и снижение q2) при малых коэффициентах избытка воздуха (αт = 1,03–1,05 при сжигании природного газа и αт = 1,05–1,08 при сжигании мазута). Работа с такими избытками воздуха без ДУ обуславливала потери тепла от химической неполноты сгорания q3 от 5 до 7%.
В результате снижения коэффициента избытка воздуха в топке:
–повысился КПД котлов и КИТ на (1–3)% в зависимости от паропроизводительности котла и режима работы;
–уменьшился расход топлива: природного газа – в среднем на 2%, высокосернистого мазута – на 3%;
–снизился общий объём выбросов на 20–30% ( в пересчете на 1 т пара).
Кроме того, установка дожигательных устройств способствовала интенсификации теплопередачи в топке за счёт:
–излучения кладки, размещенной в камере догорания, на топочные экраны и первый ряд конвективного пучка;
–увеличения степени заполнения топки и камеры догорания продуктами сгорания (влияние рециркуляционных зон решеток).
К положительным сторонам системы дожигания относится и более устойчивая циркуляция, особенно в трубках первого ряда конвективного пучка (за счёт излучения кладки). Опрокидывание циркуляции не наблюдалось и в периоды работы котла на пониженных нагрузках.
Следует отметить роль ДУ как аккумуляторов тепловой энергии. При повышенных тепловых нагрузках кладка разогревается, а при переходе к минимальной паропроизводительности отдает теплоту газам, имеющим температуру (700–800) º С. Это способствуя полноте дожигания токсичных компонентов и повышая КПД котла и КИТ. Аэродинамическое сопротивление двух решеток не превышает (100-200)Па.
Проведенные автором [8] исследования показали, что при установке ДУ решение задачи защиты воздушного бассейна от канцерогенов и других токсичных веществ сочетается с повышением экономичности котлов, их эффективности и сопровождается экономией топлива. Длительный опыт работы котлов с насадками свидетельствует, что реконструкция не вызывает нарушений работы котла, эксплуатационных затруднений.
Применение дешевого и доступного материала – шамота в температурной зоне 1000ºС эффективна и перспективна, так как шамотные огнеупоры работают устойчиво, прочность кладки достаточна. Отложения золы незначительны; оплавления или ошлако-
44
вания огнеупорных поверхностей дожигательного устройства не наблюдалось.
Для дожигателей, выполненных из других материалов, температура обезвреживания снижается и составляет: для шамотов ША и ШЛА – (780–820)° С, керамзита – (760– 780)° С; хромомагнезита – 710 ° С.
Каталитические реакторы
Каталитические реакторы являются основным оборудованием систем каталитической очистки – одного из наиболее распространенных методов термического обезвреживания выбросов [19-21] . Каталитический реактор это аппарат, в котором размещается специальное вещество для ускорения реакций окисления или восстановления - катализатор.
Кинетику каталитического процесса можно представить в виде следующих элементарных стадий: диффузия исходных веществ к поверхности катализатора, адсорбция, химическая реакция, десорбция и диффузия полученных веществ в свободное газовое пространство.
Преобладание диффузионных процессов вызывает необходимость резкого снижения скорости движения очищаемой смеси через катализатор. Допускаемая с точки зрения эффективной работы линейная скорость обезвреживаемых газов - (0,1 – 1) м/с, т.е на 1-2 порядка ниже, чем в скорость в промышленных газоходах и воздуховодах. Чтобы обеспечить снижение скорости прокачивания очищаемой смеси через катализатор, нужно значительно увеличить поперечное сечение реактора, что приведет к громоздкости установки в целом.
Объем каталитического слоя зависит от основной характеристики катализатора – объемной скорости, ч-1 (объемная скорость означает часовой расход газа, который может быть обезврежен одним м3 катализатора).
Чтобы обеспечить необходимое время пребывания обезвреживаемой смеси в каталитическом реакторе, необходима значительная высота слоя катализатора, что приводит к повышению аэродинамического сопротивления аппарата.
Отсюда следующие перспективные направления развития конструкций каталитических реакторов и катализаторов:
-снижение необходимого объема катализатора за счет повышения эффективности катализатора;
-разработка новых катализаторов с высокой объемной скоростью каталитического процесса;
-снижение аэродинамического сопротивления каталитического реактора в результате его конструктивных изменений.
Динамику конструктивных изменений каталитических реакторов можно представить следующим образом.
45
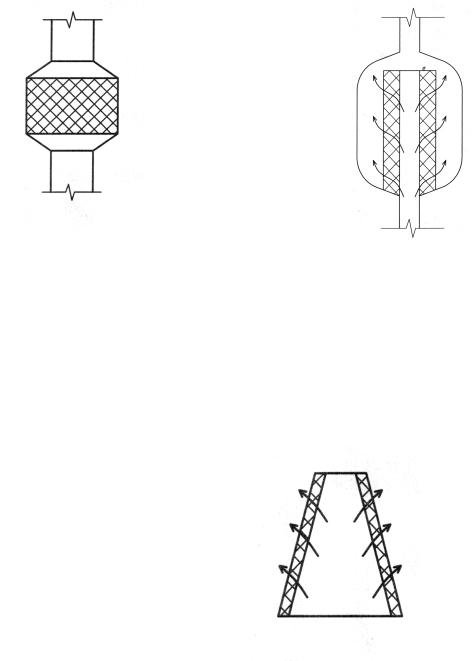
Рис.2.38. Горизонтальный слой |
Рис.2.39. Вертикальный коаксиальный |
катализатора |
слой катализатора |
Замена горизонтального слоя катализатора (см. рис.2.38) на вертикальный с коаксиальным размещением каталитических элементов (см. рис.2.39) значительно снизит толщину слоя и, как следствие, аэродинамическое сопротивление каталитического реактора в целом. Выполнение каталитических элементов с небольшим уклоном к основанию каталитической «корзины» (см. рис. 5.3.) будет способствовать равномерному распределению обезвреживаемой смеси по слою катализатора и повышению эффективности каталитического процесса.
Рис. 2.40. Наклонный слой катализатора
Аппараты для термокаталитической очистки
Если температура обезвреживаемых выбросов ниже, чем эффективная температура каталитического процесса, то необходим предварительный подогрев подаваемой на обезвреживание смеси. Подогрев осуществляется, в основном двумя способами: за счет газогорелочного устройства и путем прокачивания через теплообменникутилизатор.
В зависимости от степени совмещения устройства для нагрева, каталитического реактора и теплоутилизатора системы каталитической очистки разделяются на несовмещенные, полусовмещенные и совмещенные.
На рис.2.41 приведена система термокаталитической очистки. Реактор, теплооб- менник-утилизатор и топочная камера разделены (несовмещенная система). Назначение теплообменника – первичный подогрев обезвреживаемых выбросов за счет теплоты, по-
46
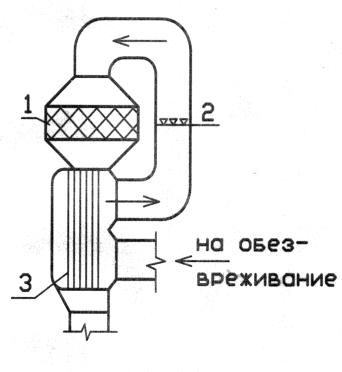
лученной в реакции окисления на катализаторе. Дальнейший подогрев выбросов до эффективной температуры каталитической реакции осуществляется газовой горелкой, размещенной в газоходе между утилизатором и каталитическим реактором.
Рис. 2.41. Несовмещенная система термокаталитической очистки: 1 – катализатор; 2- горелка; 3- теплообменник
На рис.2.42. представлен термокаталитический реактор полусовмещенного типа, разработанный Дзержинским филиалом НИИОГАЗ [8]. Преимущества данной системы очистки в следующем:
-слоевой реактор заменен на коаксиальный;
-топочная камера размещена под каталитической корзиной;
-каталитический реактор и топочная камера объединены в единой обмуровке;
-на входе в каталитический реактор размещено устройство для эффективного перемешивания обезвреживаемых газов с продуктами сгорания.
На рис.2.43 изображен термокаталитический реактор совмещенного типа, разработанный также в Дзержинском филиале НИИОГАЗ [8]. Он отличается от предыдущей
конструкции наличием встроенного теплообменника для нагрева выбросов перед поступлением в топочную камеру. Это наиболее совершенная система каталитической очистки выбросов, содержащих токсичные горючие вещества.
47
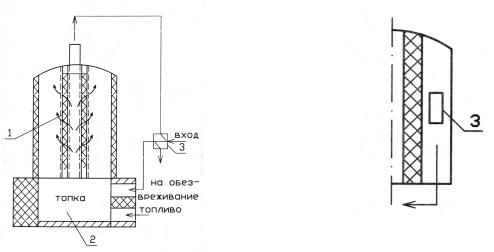
Рис.2.42. Полусовмещенная система: |
|
Рис 2.43. Совмещенная система: |
1. 1 - катализатор; 2- топка; 3- |
теплооб- |
3- теплообменник |
|
||
менник |
|
|
Аппараты для сорбционной очистки
Адсорберы
Адсорбционный метод основан на физических свойствах некоторых твердых тел с ультрамикроскопической структурой выборочно извлекать отдельные компоненты из газовой смеси и удерживать их на своей поверхности [19-21 и др.]. Концентрация вещества, которую может уловить адсорбент, зависит от его количества у поверхности, площади поверхности, физических, химических и электрических свойств адсорбируемого вещества и адсорбента, температурных условий.
По способу организации процесса адсорбции аппараты могут быть разделены на 2 группы: адсорберы периодического и непрерывного действия. Если адсорбент находится в аппарате в неподвижном состоянии, то после достижения определенной (заданной) тени насыщения его необходимо заменить или регенерировать (десорбировать). На время замены или регенерации процесс адсорбции прерывается. В аппаратах с подвижным адсорбентом можно организовать постоянную замену его части в одном адсорбере, не прекращая подачу загрязненных газов.
Однократное использование адсорбентов в аппаратах периодического действия может предусматриваться при необходимости эпизодической обработки или очистки малых количеств загрязненных газов; при низких концентрациях загрязнителей; при очистке газов, содержащих бактериологические, радиоактивные загрязнения или высокие дозы сильнодействующих ядовитых веществ. В таких случаях удобнее всего упаковывать адсорбент в кассеты совместно с фильтрами помещать в контейнеры с присоединительными элементами.
В большинстве случаев очистка технологических газов ведется в адсорберах периодического действия с регенерацией адсорбента. Непрерывность очистки обеспечива-
48

ют при этом компоновкой адсорберов, одновременно задействованных на различных стадиях процесса, в группы от 2 до 4: В группе из 4 адсорберов с активированным углем и десорбции паром стадии процесса организуют следующим образом. В одном аппарате происходит адсорбционная очистка газов, в другом - десорбция, в третьем - осушка, в четвертом - охлаждение адсорбента. Время каждой стадии принимают равным с расчетным временем процесса адсорбции. Если задействованы только 2 аппарата, то в одном из них проводят адсорбцию, а в другом - последовательно остальные три стадии. При этом суммарная продолжительность стадий десорбции, осушки и охлаждения должна быть равна продолжительности адсорбции.
Адсорберы периодического действия могут иметь вертикальное или горизонтальное расположение адсорбента. В вертикальном варианте адсорбент помещается между двумя сетками или перфорированными листами с толщиной слоя не более 100 мм (рис.5.8 а, б). Ввиду невысокой сорбционной емкости тонкие слои адсорбента используют при обработке газов с низкой концентрацией загрязнителя.
Недостатком вертикального расположения адсорбента является неравномерность слоя по высоте, которая образуется при загрузке, а также в процессе эксплуатации из-за неравномерности усадки от истирания, уноса и других причин. При работе адсорбера через зоны с меньшим сопротивлением проходит большее количество отбросных газов, что ухудшает степь очистки. Неравномерность слоя адсорбента возрастает с увеличением сечения аппарата. Поэтому пропускная способность адсорберов с вертикальным слоем адсорбента обычно не превосходит 1... 1,5 м3/с.
Рис.2.44. Адсорберы с неподвижными адсорбентом: а - вертикальный цилиндрический с вертикальным кольцевым слоем адсорбента; б - горизонтальный прямоугольного сечения с вертикальным слоем между гофрированными сетками; в - вертикальный цилиндрический системы ВТР с горизонтальным слоем; г - горизонтальный цилиндрический системы ВТР с горизонтальным слоем адсорбента. Стрелками указаны вход и выход отбросных газов или направление их движения.
Адсорберы с горизонтальным расположением адсорбента имеют значительно большую толщину слоя (до 1 м) и существенно более высокую пропускную способность. Так, вертикальные (рис.5.8,в) и горизонтальные (рис.5.8,г) адсорберы ВТР могут обраба-
49
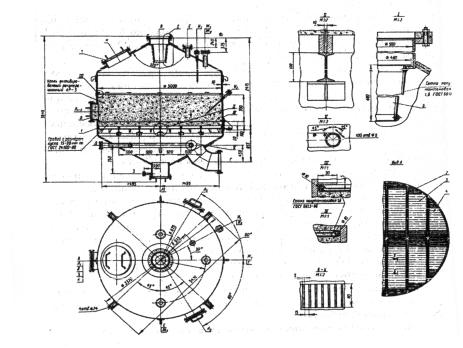
тывать до 8 м3/с и более отбросных газов. Конструкция вертикального адсорбера ВТР диаметром 3000 мм приведена на рис. 5.8,д
Размещая адсорбент в аппарате горизонтально высоким слоем, можно практически устранить влияние неравномерности слоя на степень очистки газов, но при этом возрастает аэродинамическое сопротивление адсорбера.
Кроме того частицы адсорбента в высоком слое интенсивно прогреваются из-за слабого теплоотвода из зоны конденсации, что уменьшает сорбционную емкость адсорбента и нежелательно вследствие возможности возгорания. Если концентрация загрязнителя высока, то может стать необходимым и искусственное охлаждение слоя адсорбента.
Рис.2.45. Вертикальный адсорбер ВТР
Адсорберы непрерывного действия обычно конструируют в виде колонн с провальными или беспровальными тарелками и решетками. В такиx аппаратах организуется противоточное движение адсорбента и обрабатываемых газов.
В колоннах с провальными тарелками адсорбент опускается с верхней ступени на нижнюю через все отверстия тарелки, а с провальными - через специальные переточные штуцера.
Технико-экономические показатели процесса адсорбционной очистки отбросных газов во многом зависят от свойств адсорбентов.
Адсорбент должен иметь высокую сорбционную ёмкость, которая в свою очередь зависит от удельной площади поверхности и физико-химических свойств поверхно-
50