
9847
.pdf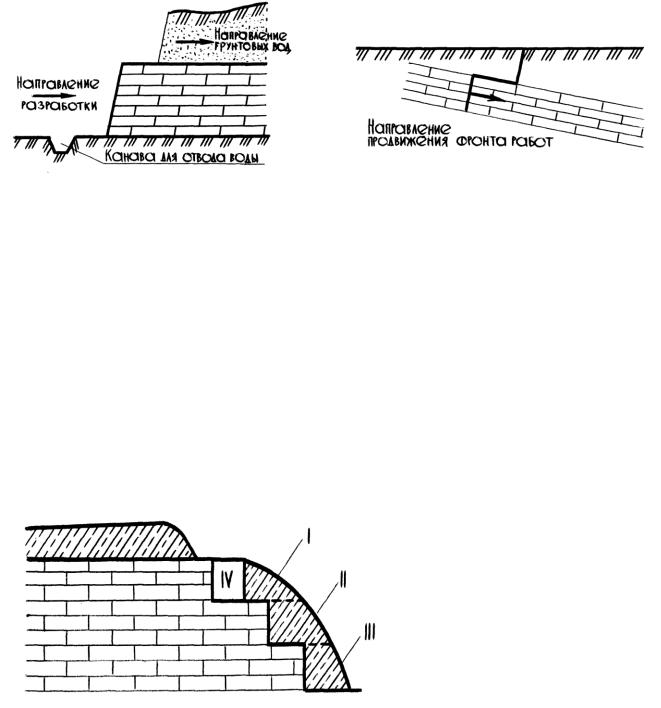
Рис. 3 Влияние направления грунтовых вод |
Рис. 4 Влияние угла падения пород на выбор |
и выбор фронта работ |
направления продвижения фронта работ |
-угол падения пород (фронт работ следует располагать таким образом, чтобы породы разрабатывались вниз по падению для обеспечения устойчивости откосов уступа)
-ориентацию фронта работ (фронт работ временных притрассовых карьеров располагают так, чтобы разработка карьера производилась с юга не север).
Подготовка месторождения к разработке предусматривает следующие виды работ: очистка участка от леса и пней; засечка и формирование уступов; подготовка транспортных берм (проходка транспортной траншеи); создание опережения вскрышного уступа; защита карьера от внешних вод.
Последовательность и состав работ по образованию уступов зависит от рельефа местности: холмистый карьер – обнажение лобовой части; глубинный карьер
– образование разрезных траншей и соединение их с откаточной.
Рис. 5 Последовательность вскрытия холмистого карьера
Обнажение лобовой части обязательно производят сверху вниз (рис. 5).
Вскрышные работы - разработка, транспортировка и разгрузка на отвале вскрышных пород. Основное отличие от обычных земляных работ – организация работ на отвале и необходимость максимально использовать отведенную площадь под отвалы.
Условия размещения отвала: располагают на площади, где последующая разработка ископаемого исключена; плечо транспортировки от забоя до отвала должно быть наименьшим.
Высота породных отвалов определяется характеристиками грунта, способом отвалообразования (экскаваторный, бульдозерный), рельефом местности.
г) проектирование буровзрывных работ. Применяются при разработке скальных пород:
– основное взрывание (отделение скальных пород от общего массива);

–разделка негабарита (доводка крупных кусков взорванной породы до требуемого размера).
Негабаритным считается кусок, линейный размер которого превышает допустимый:
1)по вместимости ковша экскаватора (Е, м3): Lг 0,53Е ;
2)по ширине ленты конвейера (В, мм): L’г = 0,5В+200 мм;
3)по размеру загрузочного отверстия дробилки первой стадии (А, мм):
L”г = (0,78-0,85)А.
При проектировании буровзрывных работ для стадии бурения определяют потребность в сжатом воздухе Qв, мощность и тип компрессоров, буровое оборудование; для стадии производства взрывных работ – число, расположение и масса заряда.
Рис. 6 Схема расположения зарядов при проектировании буровзрывных работ
Н – мощность взрываемого слоя уступа; W – расчетная линия сопротивления (РЛС); q – расчетный удельный расход взрывчатого вещества; lзаб. – длина забойки заряда; lзар. – длина заряда в скважине (шпуре); lп – глубина перебура; а – расстояние между зарядами в ряду; b – расстояние между рядами зарядов
Мощность (величина) заряда:
Q q Кпер. W3 (n) – рыхление, выброс
Q = q V – накладной (для дробления негабарита)
где: q – расчетный удельный расход аммонита № 6 (в зависимости от типа породы варьируется в пределах 0,5-2,5 кг/м3);
Кпер. = 0,85-1,20 – коэффициент перевода к различным взрывчатым веществам;
W = (0,5-0,8)Н - расчетная линия сопротивления по подошве уступа (расстояние от дневной поверхности до заряда), м;
n = r/W – показатель действия взрыва;
r – радиус воронки, м; V – объем камня, м3
При взрывании монолитной прочной породы бурение производят с перебуром на величину (0,10-0,15)W, при залегании слабой породы под разрыхляемым пластом производят недобур на 10-20 см.
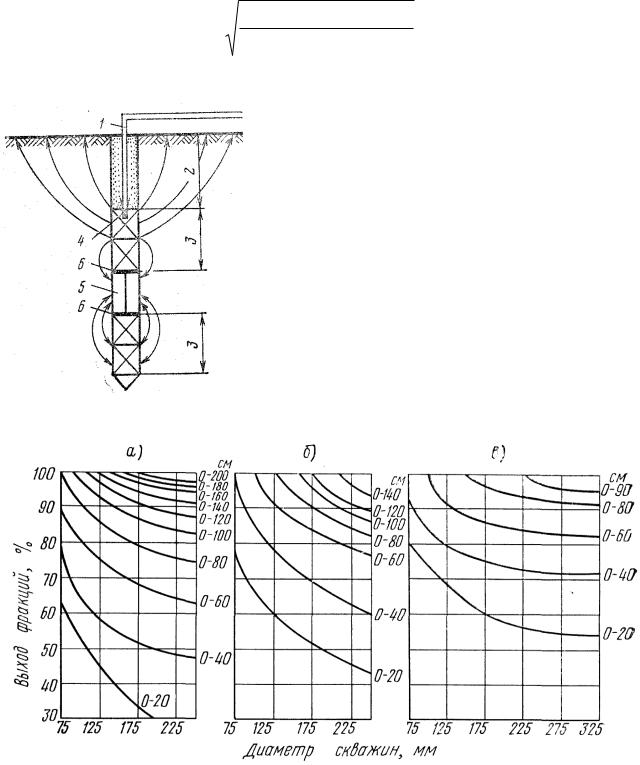
Расстояние между зарядами в ряду а варьируется в зависимости от метода зарядов и способа взрывания (а = (1,0-1,5)W). Расстояние между рядами при многорядном взрывании b = (0,6-1,0)W.
Диаметр скважины:
d |
Q |
, дм |
7.85 (L 0.75W) |
где: - плотность заряжания, кг/дм3; L – глубина скважины, м
Для улучшения качества дробления и получения равномерного дробления пород применяют рассредоточенные заряды в скважинах – создают воздушные промежутки, высота которых кратна высоте запроектированного заряда.
Рис. 7 Типовые характеристики зернового состава взорванной горной массы:
1 – электропровод; 2 – забойка; 3 – заряд ВВ; 4 – электродетонатор; 5 – стойка-распорка; 6 – фанерный кружок.
С помощью диаметра d можно регулировать зерновой состав взорванной породы.
Рис. 8 Типовые характеристики зернового состава взорванной горной массы:
а – крупноблочные породы; б – среднеблочные породы; в – мелкоблочные породы
д) организация работ. Применяемые машины:
– для добычи - экскаватор, скрепер, бульдозер, землесос, гидромонитор;

–для транспортировки – автотранспорт, пульпопровод, ленточный транспортер.
Особенность организации работ при добыче камня (экскаваторная разработ-
ка):
1) фронт работ разделяется не менее чем на два участка, разрабатываемые последовательно (рис. 9);
I участок II участок III участок
разработка породы
экскаватором; разделка негабарита
бурение скважин
Рис. 9 Последовательность работы экскаватора в забое
2)запас взорванной породы для работы экскаватора обеспечивается не менее чем на 2 суток, обуривание – с опережением продвижения экскаватора на 5-6 суток;
3)угол поворота экскаватора при погрузке породы должен быть наимень-
шим;
4)объем кузова автосамосвала должен превышать в 3 раза емкость ковша экскаватора;
5)подача автотранспорта под погрузку должна быть бесперебойной.
е) технология разработки скальных пород.
Схема разработки карьера
1)Подготовка месторождения (расчистка территории, ограждение, осушение, организация поверхностного водоотвода, удаление растительного слоя, устройство подъездных дорог).
2)Вскрышные работы (вскрытие месторождения выполняют наклонными траншеями с опережением на безопасное расстояние от работ по добыче; вскрышные породы вывозят на дорогу, в овраг или отвал в карьере, либо за его пределами).
3)Зачистка месторождения, устройство въездной и разрезной траншеи.
4)Буровые работы.
Выполняют вручную или с помощью станков (бурильных машин).
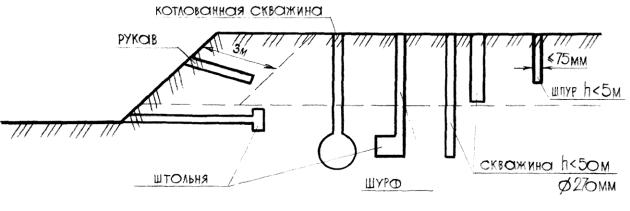
Виды бурения (механическое и термическое):
-вращательное (резка и истирание породы за счет вращения коронки бура);
-ударное (раскалывание и дробление твердой и резка мягкой породы за счет силы удара бура);
-ударно - вращательное ( разрушение каменной породы за счет силы удара с последующим проворачиванием бура в скважине);
-термическое ( разрушение породы в результате теплового расширения за счет нагрева ее до высокой температуры термобуром с реактивной горелкой).
Механизмы:
- перфораторы (ПР) (бурильные молотки) – ручные, колонковые, телескопические
(область применения: бурение шпуров и скважин (d = 35-75 мм, h 10 м));
- станки шнекового бурения (БС, БСН, СВБ, СБР)
(область применения: бурение скважин в нескальных грунтах (d 270 мм, h
<40 м));
-станки шарошечного бурения (БТС, БСВ, СВБК, СБШ)
(область применения: бурение скважин (d < 300 мм, h < 40 м) при разработке нерудных материалов);
- станки ударно-вращательного бурения (СБМК, СБУ, Урал)
(область применения: бурение скважин (d < 300 мм, h < 40 м) при разработке нерудных материалов);
- станки ударно-канатного бурения (БС, УКС)
(область применения: бурение скважин в сильнотрещиноватых грунтах (d <
900 мм , h < 50 м));
- станки термического бурения
(область применения: бурение скважин в твердых горных породах (d 250
мм, h < 20 м)).
Выбор типа механизма зависит от крепости и абразивности разрабатываемой породы (по шкале проф. М. М. Протодьяконова):
-коэффициент крепости до 4 – вращательное (шнековое) бурение;
-коэффициент крепости от 4 до 12 – шарошечное бурение;
-коэффициент крепости от 12 до 20 – огневое бурение;
-в неподдающихся породах – ударно-вращательное бурение.
Виды горных выработок

5) Забивка выработок взрывчатыми материалами. Взрывчатые материалы: взрывчатые вещества ВВ;
средства взрывания.
Взрывчатые вещества подразделяются на три группы:
-метательные (разломка на куски при рыхлении пород; вид воздействия – статическое давление (порох));
-бризантные (дробление горной породы при взрывании (аммониты));
-инициирующие (возбуждение взрыва; высокочувствительны к внешним воздействиям (пламя, удар, трение); применяются при снаряжении капсюлей детонаторов, детонирующих шнуров (гремучая ртуть, азид свинца)).
Хранение ВВ осуществляется в специальных складах (материалы отличаются повышенной гигроскопичностью).
6) Взрывные работы.
Методы взрывных работ определяются характером горной выработки:
-метод накладных зарядов (разломка негабарита);
-метод шпуровых зарядов;
-метод скважинных зарядов;
-метод камерных зарядов;
-метод котлованных зарядов.
Способы взрывания:
-огневой (для одиночных зарядов) – инициация с помощью детонатора и огнепроводного шнура, горящего со скоростью 1 см/с;
-электрический (одновременно несколько зарядов) – инициация с помощью электродетонаторов искрового действия и конденсаторной подрывной машинки;
-детонирующим шнуром (бескапсюльное взрывание) – скорость воздействия 6500 м/с через зажигательную трубку или электродетонатор;
-электроогневой – посредством зажигательной трубки или ОПШ, действующий от электротока.
Управление взрывом: мгновенный; короткозамедленный; контурный; направленный; скважинных зарядов с воздушными прослойками.
Дополнительное рыхление: механическое; накладных зарядов.
7) Погрузочные работы и транспортировка породы.
Зависят от характера разрабатываемого материала (технология – см. выше).
1 – ось передвижения экскаватора; 2 – ось движения автосамосвалов; Rп – радиус поворота экскаватора; I-III – номера экскаваторных заходок.

8) Рекультивация земель – комплексное использование месторождения, решается с учетом спецификации ландшафта и др. факторов.
Цель – приведение земель в состояние, пригодное для использования в интересах сельского, лесного, водного хозяйства, промышленно-гражданского или дорожного строительства.
Горнотехническая рекультивация выполняется по окончании работ (предусматривается проектом): снятие и хранение растительного слоя, планировка отвалов, дренирование и другие мелиоративные мероприятия, отсыпка плодородного слоя. Проводится разработчиками месторождения. Следующий этап – биологическая рекультивация.
3.Предприятия по переработке горной массы
1.Основные рабочие процессы камнедробильных заводов
Переработка горных пород – изменение размера (дробление), сортировка по размерам (грохочение), очистка от примесей пустых пород и глины (грохочение и промывка) и классификация (обогащение).
а) Дробление – получение продуктов крупных размеров в дробилках. Измельчение – получение продуктов мельче 0,5 мм в мельницах (шаровых,
стержневых).
Рис. 10 Виды дробильно-размольного оборудования:
а) щековая дробилка; б) конусная дробилка; в) валковая дробилка; г) молотковая (роторная) дробилка; д) роторная дробилка; е) бегуны; ж) шаровая мельница; з) вибрационная мельница.
1, 2 |
- подвижная и неподвижная щеки, с укрепленными на них дробящими плитами; |
|
3 |
– |
внутренний подвижный конус, 4 – внешний неподвижный конус; 5, 6 – валки; |
7 |
– |
молотки (била), шарнирно или неподвижно закрепленные на роторе, 8 – ротор; |
9 |
– валки бегунов, 10 – чаша дробления (конструктивно выполняется подвижной, либо |
неподвижной); 11 – металлические дробящие шары (стержни), 12 – цилиндрический барабан; 13 – встроенные вибраторы, 14 – пружины корпуса.
Основная характеристика процесса дробления – степень измельчения
iDср. dср.
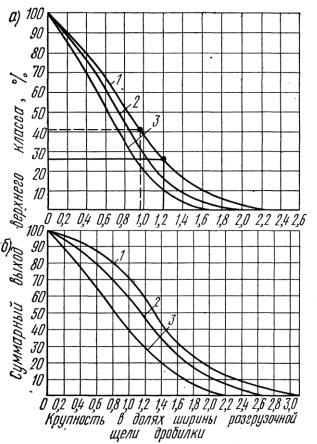
где: Dср. – средний размер камней до дробления; dср. – средний размер раздробленных кусков.
Различают следующие основные виды дробления:
-крупное (D = 1300-300 и d = 300-100 мм);
-среднее (D = 300-100 и d = 100-10 мм);
-мелкое (D = 100-10 и d = 10-5 мм)
Выбор дробильного оборудования зависит от необходимого размера щебня и объема продукции.
Примерный выход щебня по фракциям после дробления в зависимости от ширины разгрузочной щели дробилки можно определить по кривым дробления (см. рис. 11).
Рис. 11 Кривые дробления:
а - щековой дробилкой; б – конусной дробилкой;
1 - для пород прочностью более 150 МПа,
2 - для пород прочностью 80-150 МПа, 3 - для пород прочностью 30-80 МПа
Дробление может быть одно- и многостадийным (в нескольких последова-
тельно расположенных дробилках). |
|
I стадия (крупное дробление) |
– щековые дробилки; |
II стадия (среднее дробление) |
– щековые со сложным качанием щеки или |
конусные дробилки;
III стадия (мелкое дробление) – валковые дробилки в замкнутом цикле с грохотом.
iобщ. = iI + iII + iIII – общая степень дробления где: iI, iII, iIII – частные степени дробления
Циклы дробления:
-открытый – материал проходит через дробилку один раз, в конечном продукте всегда присутствуют куски избыточного размера;
-замкнутый – многократный проход материала через дробилку с возвратом крупных кусков для повторного дробления.
Производительность дробилки (щековой):
Q = Qп kд k kф kкр. , т/час.

где: Qп – паспортная производительность дробилки, т/час.;
kд – поправочный коэффициент на дробимость материала (1,2-0,85 в зависимости от прочности пород);
k - коэффициент, учитывающий насыпную массу дробимого материала (равен отношению насыпной массы дробимого материала ( ) к насыпной массе, соответствующей паспортным данным ( п));
kф – коэффициент, учитывающий форму дробимого материала (1,0-0,85); kкр. – коэффициент, учитывающий крупность дробимого материала (1,0 -
1,23 в зависимости от ширины зева дробилки)
Изменение ширины разгрузочной щели влияет на производительность дробилки (с увеличением ширины производительность повышается, степень измельчения уменьшается, выход мелких фракций снижается).
б) Сортировка – разделение материала по крупности на грохотах (вибрационных, колосниковых, барабанных).
Часть материала, проходящая через просеивающее сито (колосники) – подрешетный продукт (нижний класс, знак «минус»); не прошедшая через сито – надрешетный продукт (верхний класс, знак «плюс»).
а = 1 |
|
|
|
|
Виды грохотов: односитные |
||
|
|
|
|
|
|
двухситные |
|
-(0-40) |
+40 |
|
|
|
|
||
а = 2 |
|
|
|
|
|
|
|
|
|
|
|
|
Число фракций: А = а + 1 , |
||
- (0-5) - (5-40) |
+40 |
|
где: а – число сит |
||||
Основной показатель, характеризующий |
качество сортировки – точность |
||||||
(эффективность) грохочения: |
|
|
|
|
|
|
|
Е 100 |
100(а з) |
|
|
m( ) |
|
||
а(100 з) |
mисх. |
||||||
|
|
где: а – содержание материала крупностью меньше размера отверстия сита в исходном продукте, поступающем на грохочение, %;
з – допустимая засоренность верхнего продукта грохота нижним продуктом, % (при товарном грохочении – 5%);
m(-), mисх. – соответственно масса нижнего и исходного продукта такого же по крупности класса.

Производительность вибрационного грохота:
Q = с q F R l m n o p , м3/час.
где: с – коэффициент использования рабочей поверхности сита (0,7-1,0 в зависимости от вида сита и наличия загрузочных устройств);
F – рабочая площадь сита, м2;
q – удельная производительность 1 м2поверхности сита, м3/час.;
R, l, m, n, o, p – поправочные коэффициенты, учитывающие зерновой состав, эффективность грохочения, форму зерен и состояние материала, вид грохочения.
исходный материал
верхний класс +40 |
|
=0-(18-19)0 |
Удельная производительность при- |
|
нимается для грохота, установлен- |
|
ного под углом 18-190. Изменение |
|
на 30 изменяет на 25% производи- |
нижний класс -40 |
тельность грохочения |
Сортировка может быть:
1)предварительная – удаление фракций, не подлежащих дроблению;
2)классификационная – разделение на фракции;
3)избирательная – отделение материалов с различными физикомеханическими свойствами.
в) Промывка (дешламация)
В зависимости от наличия средне- и трудноразмываемых глин ведется на вибро- и корытных мойках, гидроклассификаторах и обогатительных агрегатах (гидроциклонах, сгустительных воронках), в барабанных мойках как перед дроблением, так и после него.
Схема промывочного виброгрохота
1 |
– лоток для предварительного размыва; |
2 |
– сопла для подачи воды; |
3 |
– брызгала; |
4 |
– виброгрохот; |
5 |
– лоток; 6-пульпопровод. |
Расход воды – 1-8 м3/м3
Подача воды под давлением Р = 200 МПа
Соотношение «твердое-жидкое» - 1:2-1:6
г) Обогащение – комплекс технологических операций по улучшению свойств исходного материала.
Виды обогащения: