
6954
.pdf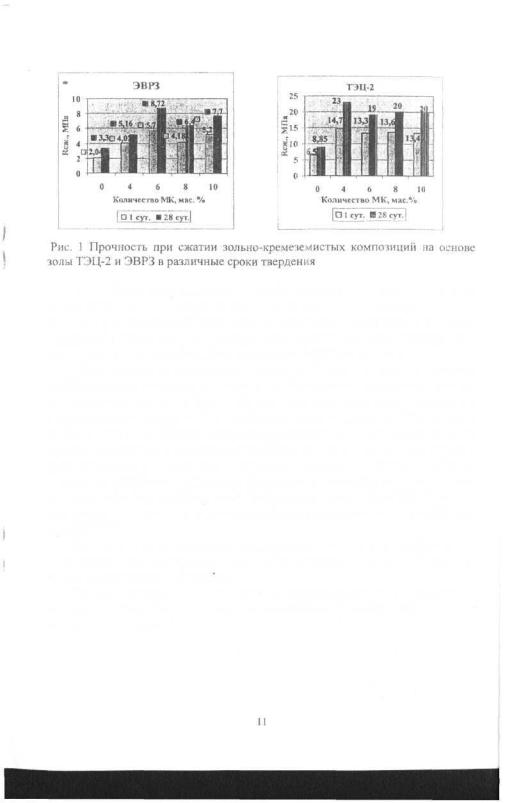
Из таблиц и диаграмм видно, что добавка микрокремнезема в количестве от 4 до 10 % от массы золы увеличивает прочность зольного камня, способствует своевременной гидратации зольно-кремнеземистой композиции. На основании полученных результатов можно сделать вывод о возможности применения зольных композиций для получения бесцементных вяжущих.
Полученные результаты подтверждаются данными рентгенофазового и дифферециально - термического анализов. Добавка микрокремнезема в составе зольного теста способствует образованию дополнительного количества гидросиликатов, которые обеспечивают повышение прочности. Проведенные исследования показали, что наилучшие результаты по срокам схватывания и прочности показали составы на основе высококальциевой золы-унос Красноярской ТЭЦ-2 с добавкой микрокремнезема в количестве 4 %. Композиции на основе золы ЭВРЗ имеют удовлетворительные прочностные показатели, однако отличаются короткими сроками схватывания, поэтому дальнейшие исследования проводились с использованием композиции на основе золы Красноярской ТЭЦ-2.
Для увеличения прочности зольно-кремнеиемистых композиций в их состав были введены минерализованные стоки в количестве от 1 до 4 % от массы сухих компонентов композиции.
Влияние минерализованных стоков на нормальную густоту зольного теста, сроки схватывания, равномерность изменения объема и прочность показано в табл. 6. и на рис. 2
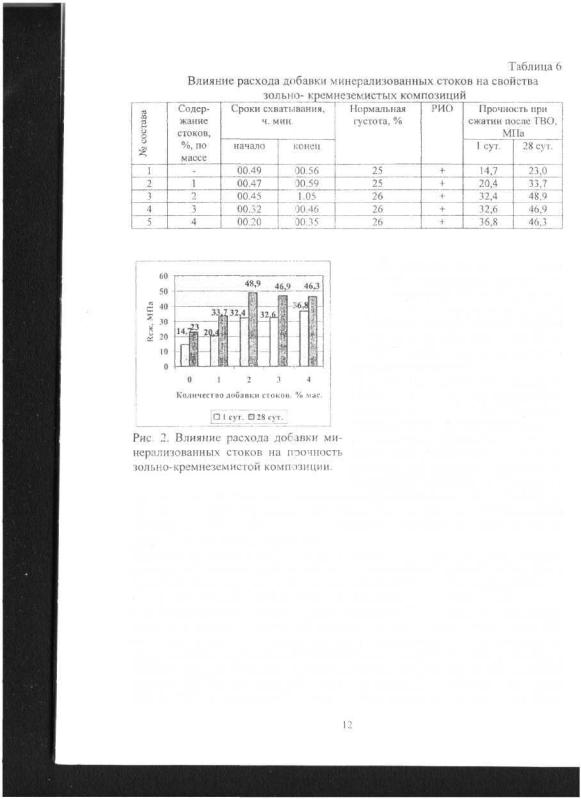
Результаты исследований показали, что оптимальным является состав, содержащий 2 % солевых стоков от массы сухих компонентов, который обеспечивает получение композиции с прочностью при сжатии в 28 суток 48,9 МПа, сопоставимой с прочностью цементного вяжущего.
Исследования процессов структурообразования зольно-кремнеземистых композиций с добавкой минерализованных стоков, проведенные методами рентгенографического и диффе- ренциально-термического анализов показали, что хлориды, содержащиеся в минерализованных стоках, вступают
в реакции обмена или присоединения с минералами золы - унос, увеличивая при этом степень гидратации силикатных фаз, что способствует появлению новообразований в виде гидрохлоралюминатов кальция и высокоосновных гидросиликатов кальция - гиролит Результатом является то, что в твердеющей системе ускоряются процессы гид-
ратации в начальные сроки сразу после изготовления изделий, обеспечивая при этом раннее структурообразование композиции, а также ускоренный набор прочности материала и ликвидацию негативного влияния на СаОсв.
Основными продуктами гидратации силикатной фазы зольного камня в нормальных условиях являются тоберморитовый гель и гидрооксид кальция. Последний появляется в зольном камне на 14 сутки твердения, что свидетельствует о полном связывании хлор-ионов к этому сроку в гидрохлоралюминаты кальция.Минерализованные стоки увеличивают степень гидратации силикатов кальция. Количество связанной воды, определённой в диапазоне температур 200-500°С (дегидратация тоберморитового геля, гидроалюминатов и гидрохло-
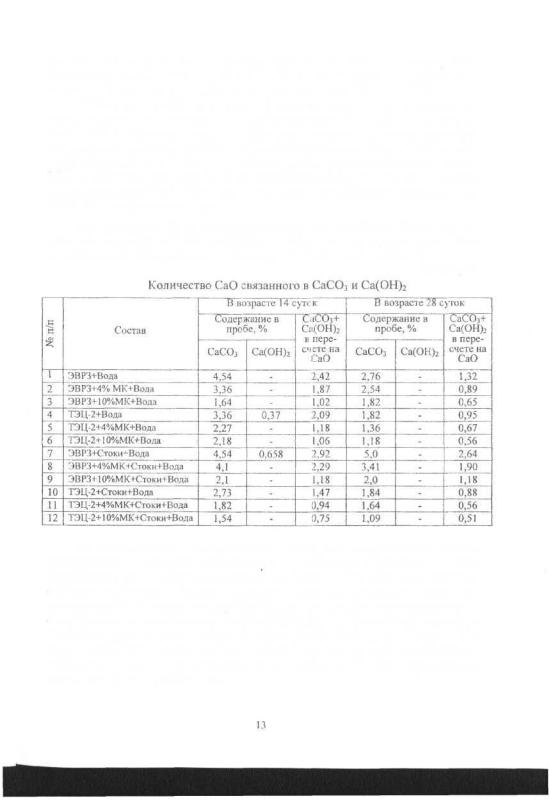
ралюминатов кальция) на 14 сутки твердения для зольного камня, затворённого водой, составило 9,4 %, а промстоками 10,4 %. К 28 суткам твердения количество связанной воды увеличивается соответственно до 11,2 и 12,0 %.
Добавки-хлориды участвуют в образовании гидрохлоралюминатов, которые впоследствие в сочетании с гидросиликатами составляют основу первичного кристаллического каркаса, обрастание которого высокодисперсными тоберморитоподобными фазами повышает его плотность по сравнению с образцами без добавки. Температурные интервалы образования пиков кривых ДТА показывают, что при 115-150°С и 710-760 °С происходит двуступенчатая дегидратация 2СаО.3SiO2.2Н20 - гиролита, который кристаллизуется при 730-770°С с образованием a-CS.
Анализ кривых ТГ позволил провести расчет количества СаО содержащегося в соединениях СаСО3 и Са(ОН)2 в зависимости от содержания количества МК и сроков твердения. Результаты расчетов показаны в табл. 7.
Таблица 7
Из таблицы видно, что образование Са(ОН)2 при введении добавки микрокремнезема и минерализованных стоков уменьшается практически в два раза. Это говорит о том, что комплексное введение добавки МК и стоков способствует вступлению Са(ОН)2 в реакцию с микрокремнеземом образуя при этом прочный гидросиликат - гиролит. Количество непрореагировавшего СаО, содержащегося в соединениях СаСОз и Ca(OH)2, с увеличением расхода добавки микрокремнезема от 4 до 10 % возрастает не значительно. Следовательно, введение 10 % микрокремнезема не целесообразно т.к. практически 6 % не вступает в химическую реакцию и не способствует образованию дополнительного количества гидросиликатов.
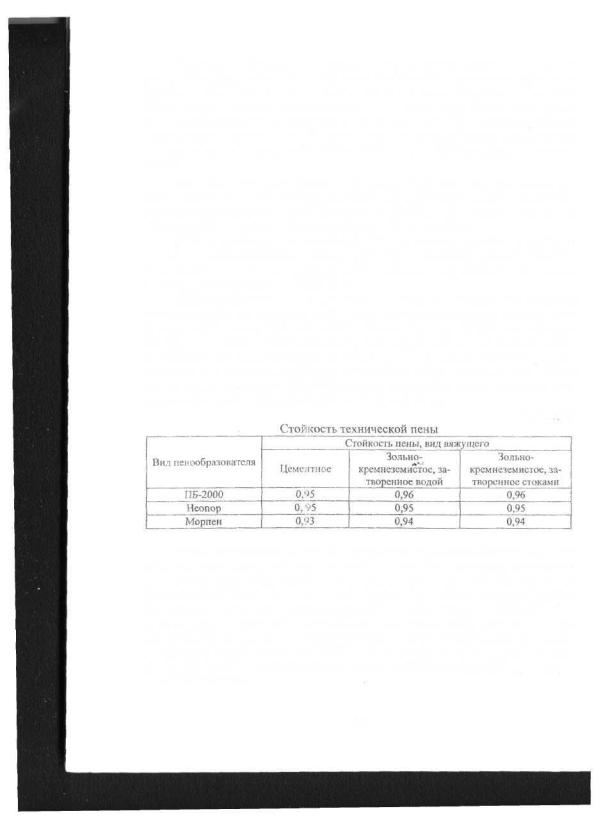
Результаты физико-химических исследований полученных составов показали, что минерализованные стоки интенсифицируют процесс твердения вяжущего в начальные сроки и в более позднем возрасте. Присутствие солейэлектролитов увеличивает степень гидратации силикатной фазы зольнокремнеземистой композиции, приводит к появлению новообразований, представленных гидрохлоралюминатами и высокоосновными гидросиликатами кальция что способствует формированию более плотной и прочной структуры зольного камня.
На основании проведенных исследований установлено, что оптимальным является состав зольно-кремнеземистой композиции, включающей 96% высококальциевой золы - унос Красноярской ТЭЦ-2, 4% микрокремнезема и 2 % минерализованных стоков от массы сухой композиции.
В четвертой главе при ведены результаты исследований по разработке составовтеплоизоляционногоиконструкционно-теплоизоляционногопенобе- тона на основе зольнокремнеземистой композиции и изучению свойств пенобетона марок по плотности D400 и D900,.
При разработке составов пенобетона было изучено влияние компонентов бесцементной композиции на стойкость технической пены, полученной на основе различных пенообразователей. Результаты, представленные в табл. 8 показали, что стойкость пены в вольно-кремнеземистом тесте с солевыми стоками и без них не ниже, чем в цементном тесте. Самым экономичным и результативным по показателю стойкости пены в бетонной смеси из использованных является пенокондентрат ПБ-2000, поэтому дальнейшие исследования проводились с использованием этого вида пенообразователя.
Таблица 8
Одним из технологических факторов, влияющих на плотность пенобетона является пластичность пенобетонной смеси, обеспечивающая максимальную степень поризации при введении в нее технической пены. Для определения оптимальной пластичности зольнокремнеземистого теста проведены исследования со смесями, имеющими различное водо-твердое отношение. Результаты проведенных исследований показали, что для получения пенобетона заданной плотности пластичность смеси на основе зольно-кремеиеземистой композиции должна составлять 25-26 см по расплыву на вискозиметре Суттарда, что обеспечивает максимальную стойкость технической пены и требуемую степень поризации.
14
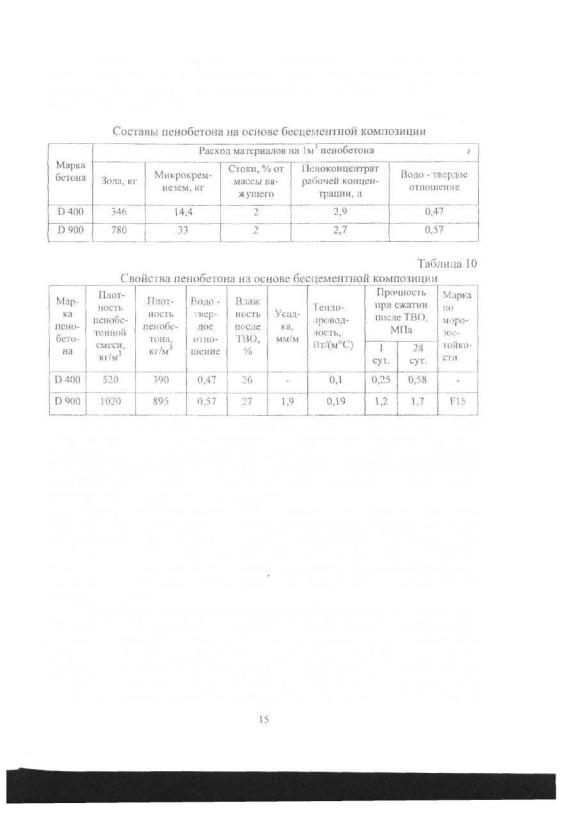
Разработанные составы теплоизоляционного и конструкционнотеплоизоляционного пенобетона неавтоклавного твердения на основе бесцементных зольно-кремнеземистых композиций представлены в табл. 9, а свойства бетонов - в табл. 10.
Таблица 9
Теплоизоляционный пенобетон марки D 400, изготовленный на основе бесцементной зольнокремнеземистой композиции по основным свойствам соответствует требованиям, регламентируемым ГОСТ 25485-89. Таким образом, подтверждено теоретическое 'предположение о возможности получения теплоизоляционного пенобетона неавтоклавного твердения на основе бесцементного зольно-кремнеземистого вяжущего.
Однако пенобетон марки D 900 на основе бесцементной композиции имеет недостаточную прочность как в начальные сроки твердения после тепловлажностной обработки, так и спустя 28 суток, поэтому была рассмотрена возможность повышения прочностных показателей конструкционнотеплоизоляционного пенобетона за счет введения в состав композиции дополнительного количества портландцемента, т.е. был разработан состав малоцементного вяжущего.
Оптимальное количество добавки цемента было рассчитано методом математического планирования эксперимента с использованием матрицы планирования 3-х факторного эксперимента на двух уровнях варьирования. Целью реализации эксперимента были 5 параметров оптимизации: Y1 - плотность пенобетонной смеси, кг/м3; У2-плотность пенобетона, кг/и3; Y3- влажность пенобетона после тепловлажностной обработки, %; Y4- прочность при сжатии на 1 сутки после тепловлажностной обработки, МПа;, Y5 - прочность при сжатии на
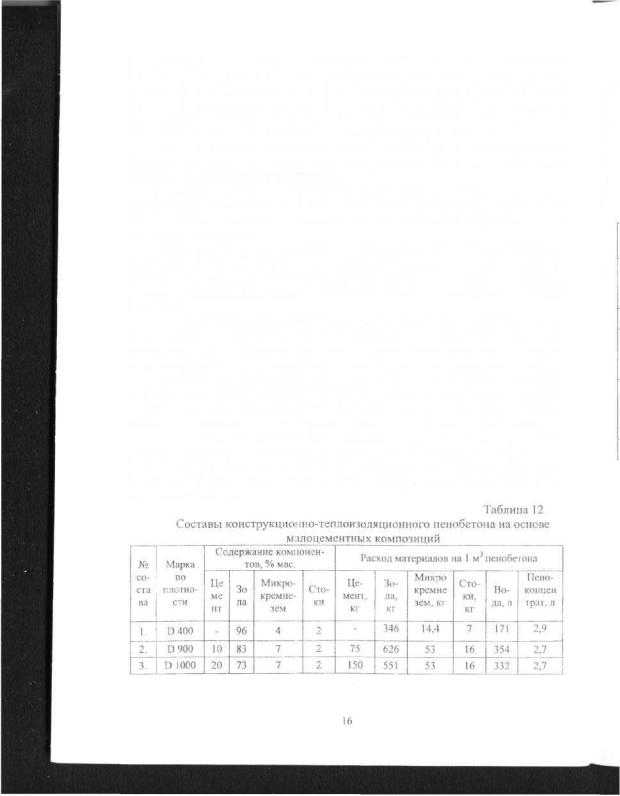
28 сутки нормального твердения после тепловлажностной обработки, МПа. В качестве независимых переменных выбраны следующие факторы: Х| - расход цемента (масс., %) в диапазоне от 10 до 20, интервал варьирования составил 5 %; Х2 -- расход микрокремнезема (масс.., %) в диапазоне от 4 до 8, интервал варьирования 2%; Х3 - расход минерализованных стоков (мас., % сверх 100 % основной смеси) в диапазоне от 2 до 4, интервал варьирования 1%.
По полученным результатам были составлены уравнения регрессии, с помощью которых определены сочетания факторов, обеспечивающие заданные показатели выходных параметров.
Результаты расчетов адекватности полученных моделей плотности и прочности пенобетона после тепловлажностной обработки и спустя 28 суток после ТБО, показали, что фактические значения выходных параметров соответствуют расчетным.
Проверки гипотезы адекватности полученных моделей проводились с помощью критерия Фишера, а. также критерия Кохрена путем определения однородности дисперсии. Расчетные значения критериев Кохрена и Фишера меньше табличных значений, что свидетельствует об адекватности уравнений регрессии.
Установленная математическая зависимость между заданными свойствами пенобетона и расходом составляющих материалов позволила получить математические зависимости для поиска и назначения оптимального состава теплоизоляционно — конструкционного пенобетона неавтоклавного твердения.
Решение уравнений регрессии с учетом верхнего и нижнего пределов варьирования цемента, а также проведенные опытные исследования позволили определить оптимальные расходы компонентов для получения конструкцион- но-теплоизоляционного пенобетона на основе малоцементной композиции.
Было установлено, что добавка цемента в количестве 10 и 20 % от общей массы композиции дает возможность получить пенобетон марок D 900 и
D 1000 с прочностью при сжатии от 5,0 до 6,0 МПа. Составы конструкционнотеплоизоляционного пенобетона на основе малоцементных: композиций представлены в табл. 12.

К конструкционно-теплоизоляционному пенобетону, в отличие от теплоизоляциощюго предъявляются более высокие требования по физикомеханическим и эксплуатационным свойствам. Основным фактором, определяющим физико-технические и эксплуатационные свойства пенобетона, являются параметры его перового пространства. От него, кроме теплофизических свойств, зависят прочность, усадка, морозостойкость. Параметры пористости пенобетона на основе бесцементных: и малоцементных композиций изучены в сравнении с пенобетонами, полученными на основе традиционного портландцементного вяжущего и представлены в табл. 13.
Таблица13
Результаты исследования поровой структуры показали, что размер и характер пор пенобетона на основе бесцементных и малоцементных зольнокремнеземистых композиций практически идентичен показателям пористости пенобетонов на основе традиционных составов на портландцементном вяжущем.
Физико-механические свойства разработанных составов пенобетона на основе бесцементных и малоцементных зольно-кремнеземистых композиций, изучены на соответствие требованиям ГОСТ и представлены в табл. 14.
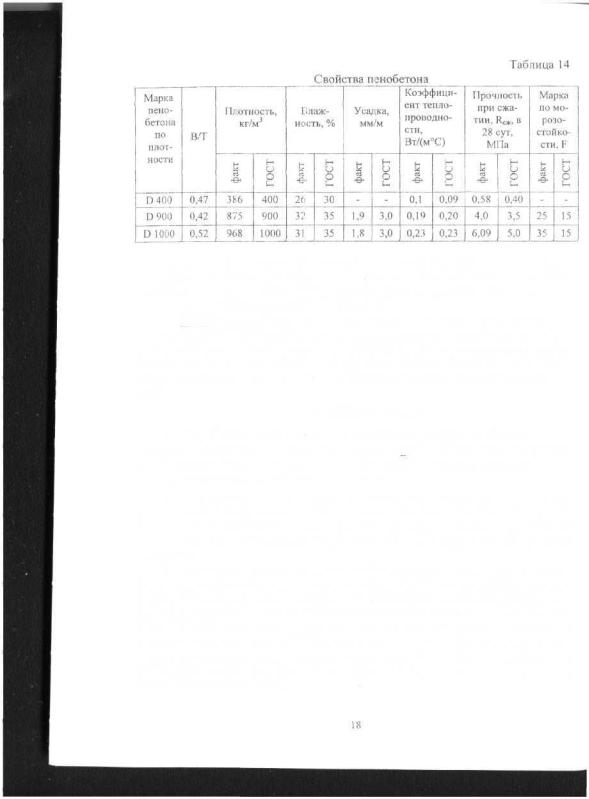
Результаты исследований показали, что разработанные составы теплоизоляционного и конструкционно-теплоизоляционного пенобетона полностью соответствуют требованиям ГОСТ, предъявляемым для пенобетонов неавтоклашгогс твердения марок D400, D 900 и D 1000.
Пятая глава содержит описание технологического процесса получения пенобетона и изделий из него на примере выпуска мелкоштучных стеновых пенобетонных блоков, а также результаты производственных испытаний и технико-экономическое обоснование производства пенобетона неавтоклавного твердения на основе разработанных бесцементных и малоцементных композиций,
ОБЩИЕ ВЫВОДЫ
1. Разработаны теоретические положения твердения и обоснована возможность получения бесцементных композиций, обладающих вяжущими свойствами на основе высококальциевой золы-унос, микрокремнезема и солевых стоков металлургического производства.
2.Теоретически обоснована и практически подтверждена возможность использования бесцементной зольно-кремнеземистой композиции для получения пенобетонов неавтоклавного твердения, что открывает новые возможности для утилизации отходов теплоэнергетической и металлургической промышленности.
3.Определен оптимальный состав бесцементной композиции, обладающей вяжущими свойствами, которая состоит из 96 % высококальциевой золыунос и 4 % микрокремнезема Для повышения прочности композиции и ускорения ее твердения в состав дополнительно вводятся солевые стоки в количестве 2 % от массы сухих компонентов, что позволяет получить бесцементное вяжущее с прочностью 48,9 МПа. в возрасте 28 суток нормального хранения. Сроки схватывания разработанной композиции соответствуют требованиям ГОСТ на цементное вяжущее и составляют: 55 минут - начало схватывания; 2 часа - конец схватывания.
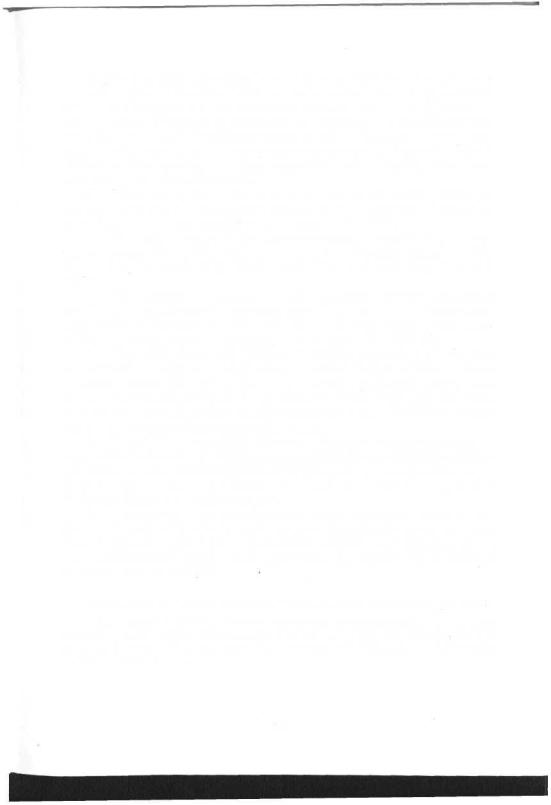
4. Результатами физико-химических исследований структурообразования при твердении бесцементной композиции установлено, что продуктами взаимодействия трех; видов техногенных отходов являются новообразования в виде высокоосновных гидросиликатов и гидрохлоралюминатов кальция, обеспечивающие формирование плотной и прочной структуры зольного камня. Хлориды, содержащиеся в минерализованных стоках, вступают в редакции обмена или присоединения с минералами золы - унос, увеличивая при этом степень гидратации силикатных фаз.
5.Установлено, что стойкость технической пены на основе различных
пенообразователей в зольно-кремнеземистом тесте с солевыми стоками и без них не ниже, чем в цементном тесте и составляет 0,93.. .0,96.
6. На основе бесцементной композиции впервые разработаны составы теплоизоляционного пенобетона неавтоклавного твердения марки D 400, имеющий прочность в 28 суток 0,58 МПа, что соответствует требованиям ГОСТ.
7. Для повышения прочности конструкционно-теплоизоляционного пенобетона предложено дополнительно вводить в композицию портландцемент в количестве 10...20 %. Прочность пенобетона, полученного на основе малоцементных композиций, повышается до 5,0...6,0 МПа.
8. Определены основные физико-технические показатели пенобетонов неавтоклавного твердения, полученных на основе бесцементных и малоцементных композиций: морозостойкость, усадочные деформации, теплопроводность, показатели пористости. Установлено, что пенобетоны разработанных составов по основным свойствам: не уступают цементным бетонам и соответствуют требованиям нормативных документов.
9. Разработана технология производства пенобетона неавтоклавного твердения на основе бесцементных и малоцементных композиций и изделий из них на базе стандартного оборудования и проведено производственное опробование при выпуске мелкоштучных стеновых блоков в условиях ОАО»Стройиндустрия» г. Красноярска.
10. Определена технико-экономическая эффективность производства пенобетона и изделий из него на основе разработанных композиций. Экономический эффект от применения разработанных составов композиций при изготовлении изделий из пенобетона по сравнению с традиционными цементными составами составляет 25,5%.
Основные положения диссертации опубликованы в следующих работах:
1. Шевченко, В.А. Выбор состава золо-цементной композиции для безобжигового зольного гравия /В.А. Шевченко, II.А. Артемьева, Н.А. Медведева // Проблемы архитекту-
ры и строительства XIX региональная научно-техническая конференция. - Красноярск: КрасГАСА,2001.С.92-94.
19
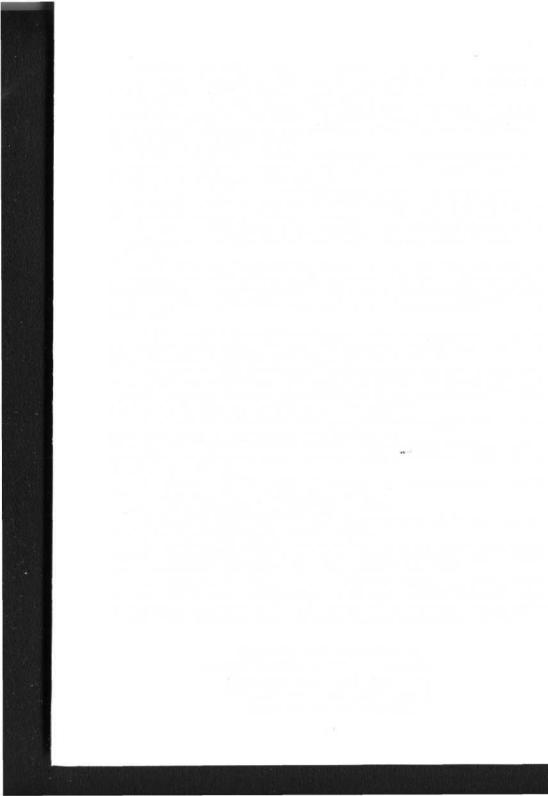
3. Шевченко, В.А. Применение микрокремнезема в малоцементных вяжущих на основе высококальциевых зол / В.А. Шевченко, Н.А. Артемьева // Ученые - юбилею вуза: Сб. науч. тр. / Под ред. И.С. Инжутова. - Красноярск:. КрасГАСА, 2002. С. 49 - 55.
4. Шевченко, В.А. Пенобетон неавтоклавного твердения для мелкоштучных стеновых блоков / В.А. Шевченко, Н.А. Артемьева, и др. // Вестник Красноярской государственной архитектурно-строительной академии: Сб.. науч. тр. Вып. 5 / Под ред. В.Д. Наделяева. - Красноярск: КрасГАСА, 2002. С.65-69.
5. Шевченко, В.А. Прим:енение солевых растворов - отхода металлургической промышленности в технологии ячеистых бетонов /' В.А. Шевченко, Н.А. Артемьева, И.В. Ильчак и др. //Газета «Строитель», №12,2002. С. 2.
6. Шевченко, В.А. Бетоны с добавкой солевых степсов - отхода металлургического производства / В.А. Шевченко, Н.А. Артемьева, И.В. Ильчак и др. // Сб. тр. науч.- практ. конференции «Бетон и железобетон в третьем тысячелетии», Ростов-на-Дону, 2002. С. .
7.Артемьева, Н.А. Влияние минерализованных стоков на свойства зольного теста и камня /Н.А. Артемьева // Труды НГАСУ. Т.6, № 2 (23). - Новосибирск: НГАСУ, 2003.
С.129133.
8.Шевченко, В.А. Применение жидких отходов металлургической промышленности в технологии бетонов / В.А. Шевченко, Н.А, Артемьева, Д.В. Филин // Проблемы и пер-
спективы энергообеспечения города: Материалы IV Всероссийской научно-практической конференции / Под ред. В.М. Журавлева, В.А., Кулагина. - Красноярск: ИПЦ КГТУ, 2003.
С.213-218.
9.Шевченко, В.А. Влияние минерализованных стоков и микрокремнезема на свойства зольного теста и камня / В.А. Шевченко,, Н..А. Артемьева. // Вестник КрасГАСА: Сб. науч. тр. Вып. 6 / Иод ред. В.Д. Наделяева. - Красноярск, 2003. С. 261 - 267.
10.Артемьева, Н.А. Пенобетон неавтоклавного твердения на основе бесцементных
композиций // Сборник материалов Межрегиональной научнотехнической конференции студентов, аспирантов и молодых ученых «Молодежь Сибиринауке России»/ Сост. В.В. Сувейзда; КРО НС «Интеграция». - Красноярск, 2004. С.222 - 226.
11. Шевченко, В.А. Технология пенобетонанеавтоклавного твердения с жидкими отходами металлургической промышленности / В.А. Шевченко, Н.А. Артемьева // Труды НГАСУ: Материалы международной научно-технической конфе-
ренции «Ресурсы, технологии, рынок строительных материалов XXI века», Новосибирск: НГАСУ, 2003. С. 133138.
12.Патент РФ № 2233817, МКИ С 04 В 38/10. Сырьевая смесь для приготовления пенобетона' Шевченко В.А., Кучин Н.М., Ильчак И.В., Артемьева Н.А., Филин Д.В. Опубл. БИ. 27.02.2005. № 22.
13.Патент РФ № 2247094, МКИ С 04 В 28/08, Бетонная смесь / Шевченко В.А., Артемьева Н.А., Рубайло И.С. Опубл. БИ. 2.7.02.2005. № 6.
14.Артемьева, Н.А. Пенобетон на основе бесцементных и малоцементных компози-
ций /' Н.А. Артемьева // Тезисы докладов 62-й научно-технической конференции посвященной 75-летию НГАСУ (СИБСТРИН) - Новосибирск: НГАСУ, 2005. С. 51-52.
15. Артемьева, Н.А. Возможность получения: пенобетона неавтоклавного твердения на основе отходов техногенного производства / Н.А. Артемъева/Молодые ученые - про мышленности, науке., технологиям и профессиональному образованию: проблемы и новые решения: Сб. науч. докладов V Международной конференции. - М.: МГИУ, 2005 С.31-37.
Подписано в печать 14.10.2005 г. Формат бумаги 60 х 84 1/16 . Усл. печ. л. 1,2
Отпечатано на ризографе КрасГАСА. 660041, Красноярск, пр. Свободный, 82 Тираж 100 экз. Заказ №399_
20