
3016
.pdf
11
Таблица 3. Характеристика и состав органически загрязнённых механических примесей (вторичного шлама) как составной части донных отложений нефтешламовых амбаров.
Наименование показателя |
Единица |
Величина |
|
|
|
измерения |
(усреднённая) |
Внешний вид |
|
|
вязкая тёмная |
|
|
|
смесь |
Плотность |
|
кг/м3 |
1540 |
Содержание минеральной части |
% масс. |
58.0 |
|
Содержание |
воды |
% масс. |
12.8 |
|
|||
Содержание органических, |
% масс. |
26,0 |
|
веществ |
|
|
|
Температура начала текучести |
оC |
50 |
Высокотоксичные сточные воды Уруссинского опытно-хими- ческого завода имеют в своём составе спирты, ароматические углеводороды, органические вещества предельного и непредельного ряда, циклические углеводороды и амины (результаты
анализов |
сточной |
воды |
приведены |
в |
табл.4). |
Таблица 4. Характеристика сточной воды общего смешанного потока (I) и от установки по производству ингибиторов коррозии и парафиноот-
ложений (II).
Наименование |
|
Ед. |
Пробы |
|
показателей |
|
изм. |
I | |
II |
1.Внешний вид |
|
|
бледно |
тёмно- |
|
|
|
жёлтый |
бурый |
2. Плотность |
|
КГ/ M3 |
1020 |
871 |
3. Содержание веществ: |
| |
% |
|
|
-ароматических углеводородов |
|
|
4,31 |
41,1 |
-органических веществ предельного и |
|
6,56 |
|
|
непредельного ряда, циклических угле- |
|
|
|
|
водородов и аминов |
|
|
|
|
-спиртов |
|
|
7,28 |
8,2 |
-смол в кубовом остатке |
|
|
6,97 |
24,0 |
-воды |
|
|
74,78 |
26,5 |
-содержание минеральных веществ |
|
0,1 |
0.1 |
|
4. рН |
|
|
7,0 |
6,0 |

12
Органическая фаза, выделенная из сточных вод, представляет смесь углеводородов различных классов. Из-за отсутствия эффективных и приемлемых способов её утилизацию или обезвреживание на Уруссинском заводе не производят и накапливают
втечении длительного времени в резервуарах.
Бходе выполнения анализов составов сырья и получаемых продуктов применялись следующие методики проведения исследований:
-плотность фракций измерялась по ГОСТ 2070-77;
-коксуемость по ГОСТ 5987-51;
-разделение на фракции проводилось в колонне чёткой ректификации в присутствии ингибитора для снижения полимеризации;
-зольность и содержание мехпримесей устанавливались по ГОСТ 7885-86;
-содержание воды находили титрованием с помощью реактива Фишера, групповой углеводородный состав - хроматографиче-
ским методом; - содержание металлов определяли атомно-абсорбционным ме-
тодом на спектрофотометре Перкен-Эльмер с графитовой кюветой.
Третья глава посвящена материалам по исследованию режимных параметров проведения плазмохимической переработки отходов и разработке технологической модели процесса с использованием теневого метода.
В ходе экспериментов изменение удельной термической нагрузки производилось при неизменной мощности плазмотрона,составляющей 7,8 кВт, и изменяемом расходе сырья на пиролиз, что достигалось соответствующей регулировкой хода поршня дозировочного насоса. Опыты проводились при расходе смеси, подаваемой на пиролиз от минимального значения 4,8 кг/ч до максимального - 9,0 кг/ч. Расход водорода в плазмотрон поддерживали в количестве 3,0 м5 /ч , на распыл сырья - 0,73 м3 /ч. В таблицах приведены усреднённые данные трёх опытов.
Из данных, приведённых в табл.5, можно сделать вывод, что при расходе сырья до 8 кг/ч обеспечивается максимальный выход продуктов реакции (ацетилена до 20,47%, [ΣC3...C4] до 2,43% об.) при минимальном содержании окиси углерода (до 6,31% об.).

|
|
|
|
|
Таблица 5. |
|
Расход сырья, |
|
|
Состав газа, % о |
|
|
|
кг/ч |
|
|
|
|
|
|
|
СН4 |
СО |
! С2H4 |
[ΣC3...C4] |
С2Н2 |
Н2 |
1 |
2 |
3 |
4 |
5 |
D- |
7 |
4,8 |
18,72 |
7,23 |
2,25 |
1,35 |
11,48 |
59.96 |
6,5 |
115,42 |
11,00 |
0,54 |
1,54 |
15,50 |
56,00 |
8,0 |
12.67 |
6,31 | 2,98 | 2,43 |
20,47 |
55,14 |
||
9,0 |
13,05 |
7,37 |
3,95 |
1,95 |
19,24 |
54,44 |
В таблицах 6 - 8 представлены зависимости основных показателей пиролиза донных отложений нефтешлама от удельных затрат энергии на пиролиз, от времени пребывания сырья в реакционной камере и изменения соотношения водорода к сырью.
|
|
|
|
|
|
|
Таблица 6. |
|
|
Зависимость выхода продуктов реакции от удельных затрат |
|||||||
|
|
|
энергии. |
|
|
|
|
|
Удельные |
Степень |
Выход продуктов реакции, % масс. |
||||||
затраты |
превраще- |
|
|
|
|
|
|
|
энергии |
ниясырья, |
|
|
|
|
|
|
|
по пироли- % масс. |
|
|
|
|
|
|
||
зу, |
кВтч/кг |
|
СН4 |
СО |
С2Н4 |
[ΣС3..С4)! С2Н2 H2 |
||
|
0.87 |
1OO |
16,3 |
16,0 |
13,0 |
6,9 |
39,2 |
8.6 |
|
0,98 |
100 |
16,0 |
13,0 |
9,0 |
8,0 |
44.0 |
9,0 |
|
1,20 |
100 |
20,0 |
26,0 |
2.0 |
6,0 |
36.0 |
10,0 |
|
1,63 |
100 |
28,0 |
18,0 |
9,0 |
5,0 |
29,0 |
11.0 |
Из табл. 6 видно, что с увеличением удельных затрат энергии на пиролиз выход C2H2 уменьшается. При увеличении мощности усиливается обуглероживание органических веществ, что вызывает снижение концентрации непредельных углеводородов. Недостаточное значение данного параметра также уменьшает степень газообразования сырья.
В табл. 7 приведена зависимость выхода продуктов реакции от времени пребывания сырья в реакционной камере. Время пребывания сырья в реакционном канале варьировалось за счёт изменения подачи сырья при постоянном объёме реактора ( 0,8 л). С увеличением расхода сырья при постоянном реакцион-
ном объёме время пребывания сырья уменьшается пропорцию-
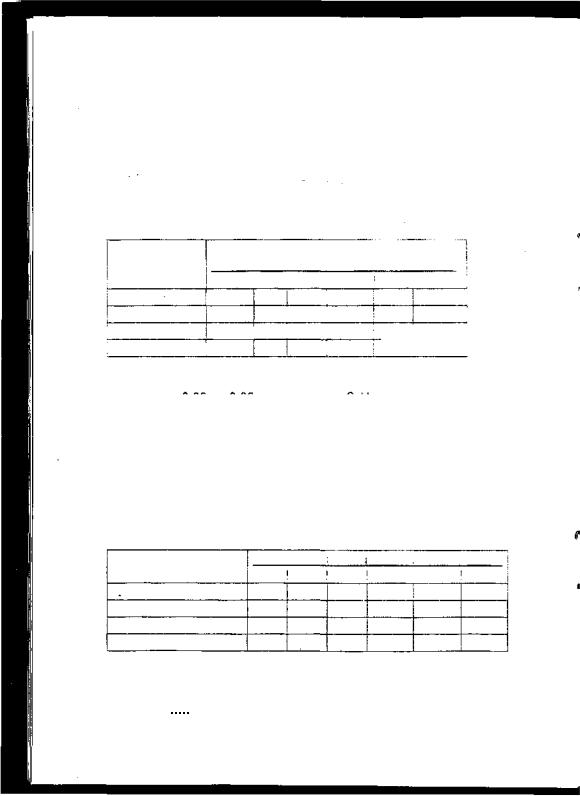
14
нально расходу. Уменьшение времени пребывания способствует увеличению концентрации ацетилена в пирогазе и выходу ацетилена, но при меньших значениях удельных энергозатрат (мощности струи энергоносителя) объем реактора недостаточен для получения более высоких значений концентраций целевых продуктов
|
|
|
|
|
|
Таблица 7. |
|
Зависимость выхода продуктов реакции от времени |
|
||||||
пребывания сырья в реакционной камере. |
|
||||||
Время пребы- |
|
Состав газа, % объемные |
|
|
|||
вания сырья в |
|
|
|
|
|
|
|
реакторе, с |
CH4 |
' СО ' С2Н4 ! |
[ΣC3...C4] C2H2 |
| 112 |
i |
||
0,042 |
12,05 |
8,37 |
3,95 1 |
1,95 |
19,24 |
54,44 |
| |
0,045 |
12,67 |
6,31 2,98 1 2.43 |
20.47 |
55,14 | |
|||
0,050 |
15,42 |
j 11,0 0,54 ! |
1.54 |
15.50 |
56,00 |
i |
|
0,066 | |
18,72 |
7,23 |
2,25 I |
1.35 |
11.48 59.96 |
_|J |
В тaбл. 8 приведена зависимость выхода продуктов реакции от изменения соотношения Н2 к сырью. С увеличением соот-
ношения с o,03 до 0,06 концентрация С2Н2 уменьшается почти в
2 раза, что связано с появлением избыточного Н2 из Н20 и реакцией взаимодействия воды и углерода (Н20 + С -> CO| + H2). При этом следует отметить, что недостаточное количество водорода не позволяет создать необходимую энергоёмкость энергоносителя, чтобы обеспечить требуемую мощность и, следовательно, повышенную концентрацию продуктов реакции.
Таблица 8. Зависимость выхода продуктов реакции от отношения
водорода к сырью.
Соотношение, |
кг/кг |
|
Состав г аза, % об |
|
|
|
|
СН4 |
СО |
С2 Н4 |
[ΣСЗ...С4] ! С2Н2 |
Н2 |
|
0,030 |
12,05 |
8,37 |
3,95 |
1.95 |
19.24 |
54,44 |
0,033 |
12,67 |
6,31 |
2,98 |
2,43 |
20.47 |
55.14 |
0,041 |
15,42 |
11,0 |
0,54 |
1,54 |
15.50 |
56,00 |
0,056 |
18,72 |
7.23 |
2.25 |
1.35 |
11,48 |
59,96 |
Из результатов проведённых исследований видно, что при пиролизе донных отложений нефтешлама в водородной плазме получен пирогаз с высоким содержанием непредельных углеводородов С2 С4; выход ацетилена на органическую часть сырья

|
|
|
|
15 |
|
|
|
|
|
|
увеличивался с уменьшением до определённых пределов удель- |
|
|||||||
|
ных затрат энергии (0,98 кВт*ч/кг), идущей на пиролиз, времени |
|
|||||||
|
пребывания сырья в реакционном канале (0,045 с) и отношения |
|
|||||||
|
водорода к сырью (0,033 кг/кг). |
|
|
|
|
|
|
||
|
Результаты экспериментальных исследований по переработ- |
|
|||||||
|
ке органически загрязнённых сточных вод приведены в табл. 9. |
|
|||||||
|
Результаты исследований по переработке органически |
|
|||||||
|
загрязнённых сточных вод в воздушной плазме. |
|
|
||||||
; Мощность |
состав продуктов сгорания, % вес. |
| |
|||||||
|
плазмотрона. |
|
(без учета |
|
|
Н2О) |
l |
|
|
; |
кВт |
N2 |
: СО2 |
: 02 |
: |
СО |
сажа |
: С:...С:. ! |
|
I |
3.5 |
85,8 |
0,2 | |
14.0 |
OTC. |
OTC. |
отс. |
I |
|
|
8,9 |
86,2 |
0,2 |
|13,6 |
OTC |
OTC. |
OTC. |
|
|
|
10,4 |
86,1 |
0,2 |
|13,7 |
! |
отс. |
OTC. |
отс. |
ι |
Произведено полное окисление загрязняющих веществ и получен водяной конденсат без органических веществ с показателем ХПК < 50 мг/л. Изменение мощности практически не влияет на процент выхода азота, углекислого газа и кислорода. В продуктах сгорания отсутствуют углеводороды, окись углерода и сажа, что показывает на экологическую чистоту применяемого способа
Для выяснения закономерностей превращения сырья в целевые продукты с учётом времени смешения была разработана технологическая модель процесса и использован теневой метод. Результаты исследований показали, что время нагрева углеводородов до необходимой температуры не должно превышать времени реакции, то есть процессы тепло и массообмена должны быть завершены за время меньшее или равное времени реакции. Таким образом, в плазмохимических реакторах должны достигаться высокие скорости смешения. Как видно из рис.2, увеличение интенсивности соударения струй (то есть увеличение газодинамического параметра) способствует более быстрому выравниванию концентрационных полей в смесителе. Более интенсивному смешению способствует также увеличение начального диаметра струй, что объясняется двумя причинами:
1)более крупные струи, соударяясь, сильно турбулизируют поток;
2)невозмущенное ядро струи достигает средней части смесителя и создаются условия смешения в режиме сталкивающихся струй

16
Исходя из полученных данных, можно сделать следующие выводы.
а) процесс смешения потока плазмы с сырьем следует вести в режиме сталкивающихся струй, б) диаметр сопел для подачи сырья не должен быть менее 0,05 диаметра смесителя:
в) дальнобойность струи должна быть по крайней мере не меньше 2/3 диаметра смесителя.
Рис 2. Зависимостьсреднеквадратичныхотклоненийконцентраций от газодинамического параметра
В четвёртой главе исследована возможность применения феноменологических методов термодинамики многокомпонентных стохастических систем к описанию процесса пиролиза высокомолекулярных многокомпонентных смесей в низкотемпературной плазме с целью выбора оптимальных режимных параметров плазмоагрегата, повышения эффективности его работы и получения максимального выхода целевых продуктов, в частности, ацетилена. Расчёты проведены по программе Сибирского энергетического института СО РАН и представлены в виде графиков, имеющих определённые закономерности изменения параметров процесса для равновесных и неравновесных промежуточных состояний термодинамических систем.
Расчёты выполнены при изменении массового соотношения водорода к органической массе (Н2/ОМ) от О до 1, температуры
(T) от 500 до 250OK, содержания воды в нефтешламе от 5 до 25% масс., давление равнялось 0,1 МПа. Уравнение реакции имело следующий вид:
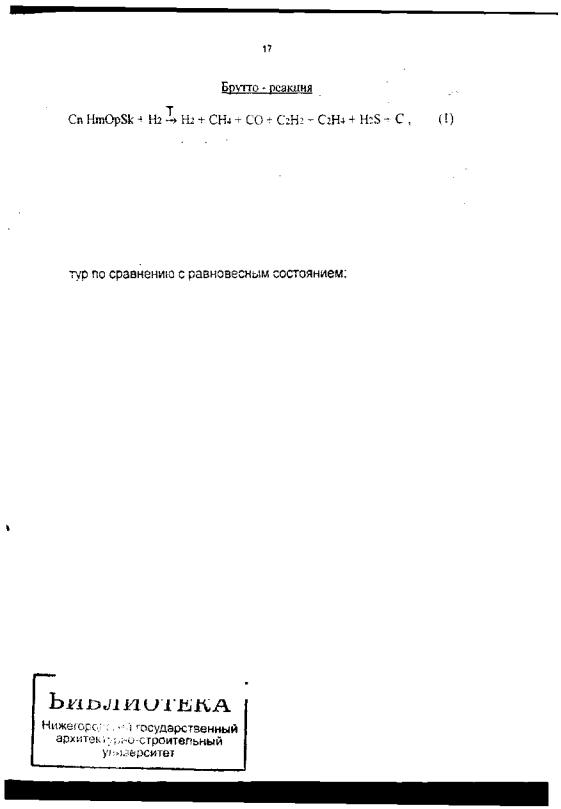
где С - технический углерод
Исходя из общего анализа полученных результатов расчёта, были сделаны следующие выводы -выход С2Н2 растёт с увеличением температуры процесса в рав-
новесных условиях и промежуточном неравновесном состоянии; -в промежуточном неравновесном состоянии при одинаковой температуре процесса выход С2Н2 выше чем при равновесном состоянии, образование С2Н2 сдвинуто в область низких температур по сравнению с равновесным состоянием; -выход С2Н2 растёт с увеличением соотношения Н2/сырьё как при равновесном состоянии, так и при промежуточном неравновесном состоянии; -с повышением температуры процесса увеличивается степень
превращения CН4, наиболее термодинамически устойчивого соединения, образовавшегося из органической части шлама; -степень превращения СН4 с ростом температуры уменьшается, что связано с процессом дегидрирования СН4, при этом растёт выход Н2; -с увеличением Н2/ОМ+МЧ (МЧ-минеральная часть) степень пре-
вращения СН4 растёт; -выход СО увеличивается пропорционально увеличению содержания Н20 в сырье;
-в продуктах реакции отсутствует конденсированный углерод за счёт реакции С + Н20 -> СО + H2;
-значения теплового эффекта реакции практически не зависят от изменения содержания воды в нефтешламе и Н2/ОМ+МЧ эндотермический эффект реакции увеличивается с ростом температуры процесса; -основным продуктом реакции превращения сероорганических со-
единений, содержащихся в нефтешламе является сероводород, в то же самое время сероуглерод, сернистый ангидрид и трёхвалентный оксид серы не образуются, что упрощает схему очистки пирогаза от сероводорода;
сточкизрениянаибольшейэкологическойнейтральностиостат-
капроцесса-наиболееоптимальнойтемпературойпроцессаяв-

18
ляется 1500К, вследствие образования минимума органических соединений в остатке.
Таким образом, получена возможность прогнозирования режимных параметров плазмоагрегата, повышающих эффективность его работы с целью получения максимальных выходов олефинов и наибольшей степени экологической безопасности получаемых соединений.
В пятой главе приводится описание принципиальной технологической схемы процесса переработки донных отложений нефтешламовых амбаров и ее технико-экономическое обоснование.
На опытно-промышленной установке (N=100κBτ) отрабатывались работоспособность аппаратов, оборудования при заданных режимах работы, уточнялись оптимальные значения параметров процесса и по ходу исследований вводились коррективы в
большой круг интересовавших нас вопросов. |
|
На рис. 3 представлена блок-схема технологического |
|
процесса. |
энергия |
Н2
олефины
сырьё
Рис.3. Блок-схема процесса разложения донных отложений
нефтешламового амбара. |
, ., |
1-подготовка газа; 2-подготовка сырья; 3-пиролиз в плазме; 4-вы- деление технического углерода и металлов; 5-выделение сероводорода с последующей переработкой в водород и серу; 6-выде- ление непредельных углеводородов; 7-блок получения электроэнергии.
• Донные отложения нефтешламовых амбаров предварительно разбавляли верхним жидким нефтяным слоем шламонакопителя в массовом соотношении 1: 0,25 и подогревали до температуры 90-950C в блоке подготовки сырья 2. Затем дозировочным насосом подавали в реактор плазмоагрегата 3, где происходило их смешение с плазмообразующим газом Н2, подаваемым из

19
блока подготовки и подачи газа А. В плазмотроне плазмообразующий газ нагревался до среднемассовой температуры 3000400OK. Для регулировки силы тока использовался выпрямитель.
В реакторе в процессе плазмохимического пиролиза получали целевые компоненты в виде смеси парафиновых и непредельных углеводородов, водорода и окиси углерода. Газообразные продукты пиролиза подвергали закалке в специальном закалочном устройстве или теплообменнике плазмоагрегата. Далее пирогаз после выхода из закалочного теплообменника проходил циклон 4 и фильтр 5. После фильтра газ подавался на переработку. Результаты испытаний приведены в табл. 10.
Из данных таблицы видно, что суммарная концентрация олефиновых углеводородов С2Н4 + С2Н2 + Сз + С4 достигает 29%, а водорода 59% об.
Таблица 10. Состав углеводородных газов после плазмохимического
разложения нефтешламов (без Н2О). Состав газа, % об.
СН4 |
! С2Н6 |
С2Н4 |
| С2Н2 |
'[ΣСз. .С4] ! Н2 |
|
|
10,90 |
0,50 |
8,17 | |
19.40 |
|
! 58,94 |
|
11.00 |
0.60 |
8,40 |
| 18,50 |
|
| 59,34 |
| |
10,32 |
0,70 |
8,07 |
[ 19,02 |
|2.35 |
| 59,54 |
| |
В связи с этим возможно несколько направлений использования пиролизных газов:
-суммарно как компонент товарного газового топлива - это самый простой, не требующий дополнительных средств разделения смесей, способ использования газа;
-отдельное выделение олефинов и водорода с использованием их по прямому назначению; однако, из-за отсутствия реальных потребностей на нефтегазовых предприятиях на нефтехимическое сырьё, данное направление малоперспективно;
-выделение только ацетилена для производственных нужд пред-
приятий нефтегазового комплекса.
В продуктах реакции отсутствовали сажа и другие побочные вещества, загрязняющие окружающую среду. Минеральный остаток являлся пористой, хрупкой спёкшейся массой, имеющей цвет красной глины, легко растирался на мельчайшие частицы, не растворялся в воде Экологическая безопасность обеспечивает

20
возможность его использования в качестве добавки к строительным материалам (табл. 11).
Таблица 11. Содержание элементов в твердой фазе вторичного шлама.
1. Бериллий |
0,0001 |
2. Мышьяк |
< 0,001 |
3. Скандий |
0,001 |
4. Свинец |
0,0026 |
5. Олово |
< 0,0001 |
6. Молибден |
0.02 |
7. Ванадий |
0,004 |
8. Кадмий |
< 0,000046 |
8. Кобальт |
< 0,00017 |
10. Никель |
0,00287 |
11. Хром |
< 0,001 |
12. Медь |
0.0056 |
Таким образом, предложена высокопроизводительная, безинерционная, экологически чистая технология переработки отходов донных отложений нефтешламовых амбаров с получением ценных топливных продуктов и неорганического остатка, которые могут быть использованы для внутреннего потребления на самих предприятиях нефтедобычи или реализованы внешним потребителям
Расчёт экономической эффективности плазмохимической переработки проведён по методике, разработанной объединённой комиссией АН СССР и ГКНТ по экономической оценке природных ресурсов и мероприятий по охране окружающей природной среды и Научным Советом АН СССР по экономической эффективности основных фондов, капитальных вложений и новой техники. Из проведённой технико-экономической оценки переработки донных отложений нефтешламовых амбаров следует, что данная технология позволяет получить, кроме экологического, экономический эффект в сумме 54600 тыс. руб. на 100 тыс. т отходов.
Основные выводы
1. Исследована возможность применения термодинамических расчётов к описанию процесса пиролиза высокомолекуляр-